In the fast-paced world of healthcare, precision, cleanliness, and compliance go beyond buzzwords and are a non-negotiable requirement. One of the underlying technologies that makes it possible to produce safe, effective, and scalable medical devices is medical plastic injection molding. Giving form to syringes and catheters, surgical instruments, and diagnostic housings, plastic injection molding is important in powering modern medicine by creating the constituent parts.
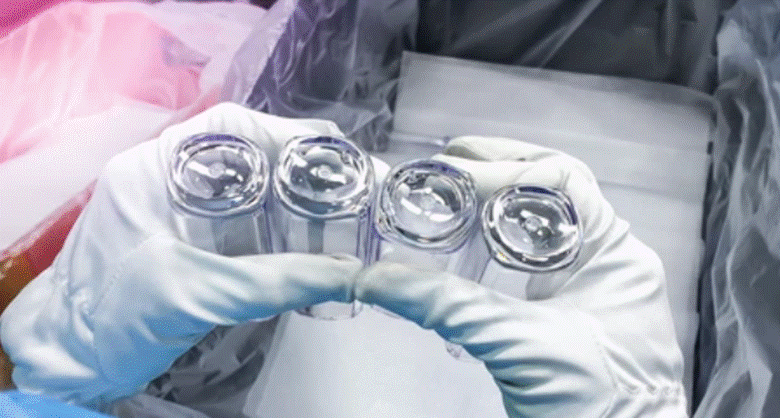
The factor of selecting a trustworthy medical injection mold manufacturer is worth mentioning. The right supplier guarantees your product conforms to strict industry standards, operates with utmost precision, and remains economical in large-scale production runs. This failure may have significant negative impacts, such as product recalls or violations of compliance, or threats to the safety of the patient.
This article provides a list of the top 10 شركات قولبة حقن البلاستيك الطبي from various parts of the world. The consideration criteria of the listed companies are very strict, starting from certifications, innovation, their global presence, and prior performance. Despite the fact that the global nature of the industry involves many regions’ players, we’ve restricted the choice to only two Chinese companies, with Sincere Tech being one of them, and the rest are distributed in the US, Europe, and Israel.
What is Medical plastic injection molding?
It is a niche manufacturing process that is used to produce highly accurate and quality medical and healthcare plastic-aided components. It entails the injection of molten plastic into a specially machined mold and cooling it until it solidifies and takes its final shape.
Key Features:
- Precision and Cleanliness: Medical molding needs to conform to tight tolerances and is taken to clean room environments to avoid contamination.
- Biocompatible Materials: Use medical-grade plastics such as polycarbonate, polypropylene, and PEEK, which are safe for use in or with a human body.
- Regulatory Compliance: Manufacturers need to observe standards such as the ISO 13485, FDA, and CE regulations in order to guarantee safety and efficacy.
- High Volume and Repeatability: Perfect for making large runs of uniform, sterile parts, such as syringes, IV sets, diagnostic housings, Arthroscopes, surgical instruments, and drug-dispensing devices.
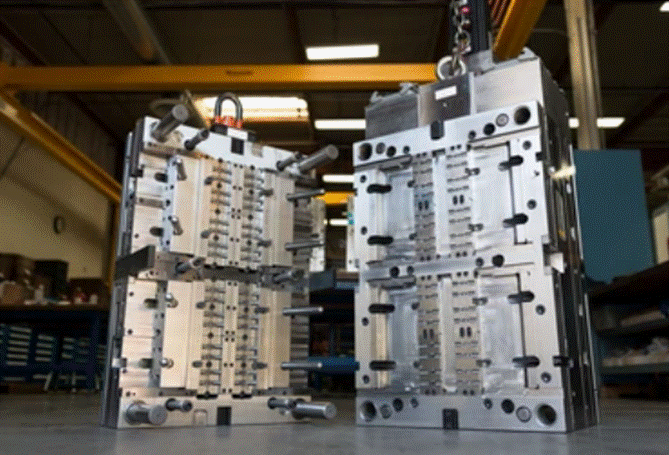
Criteria for Selection
The following criteria help decide which company was the best at medical injection molding,
1. ISO 13485 Certification & Regulatory Compliance
The internationally accepted standard for the quality management systems for the medical device industry is ISO 13485. In addition, companies have to fulfill FDA and CE regulations when they intend to sell their products.
2. Advanced Technology and Cleanroom Capabilities
Companies need to be able to operate in cleanroom environments (ISO Class 7 or better) and make use of the latest injection molding technology (micro molding and multi-shot injection molding) to meet hygiene, contamination, etc. standards.
3. Medical Focus and Industry Track Record
Reliability and expertise in the medical component manufacturing space have a strong history. Companies that have been in the healthcare space for a long time also understand regulation and performance demands better.
4. Large Healthcare Client base and Global Reach
Global companies will have robust quality control, logistics, and regulatory infrastructures to better serve multinational medical OEMs.
5. R&D and Customization Capabilities
Not only do they offer manufacturing, but also engineering support, design for manufacturing (DFM), as well as innovation partnership in bringing new products to life quickly and efficiently.
Top 10 Medical Plastic Injection Molding Companies.
These are some of the world leaders in the medical plastic injection molding industry. Chosen on strict criteria, such as Quality Certifications, Technological advancement, Global presence, and Commitment to innovation, these manufacturers are trusted by top medical device brands across the globe. Here are the top 10:
1. Sincere Tech (China)
Sincere Tech is one of the leading Chinese manufacturers involved in medical plastic injection molding for global clients. Covering clean room molding, rapid prototyping, and mass production, Sincere Tech is a trusted source of high-precision medical parts. They are dedicated to quality by following ISO 13485 standards, advanced tooling, and rigorous validation processes. Moreover, medical OEMs can outsource the entire process, including mold design, fabrication, and even assembly, making it a complete service with various companies.
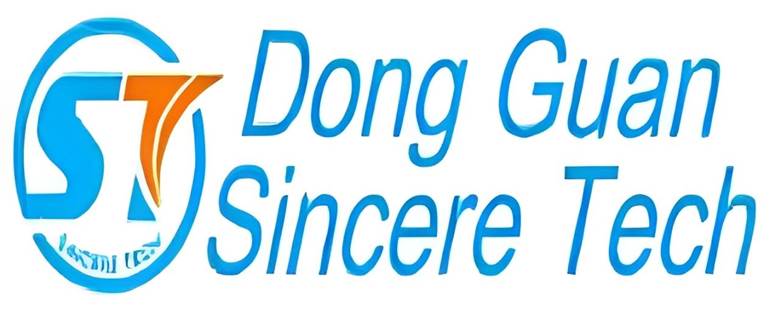
الموقع الإلكتروني: https://www.plasticmold.net/
Company Profile:
For over 15 years, Sincere Tech has specialised in both manufacturing molds and making accurate plastic parts in China. Thanks to its ISO 13485 qualification and high-quality cleanrooms, the company offers important parts for global medical OEMs seeking tight tolerances. This company covers mold design, handles tooling, and carries out secondary processing, all from the same location. Since they can manage product development from the first steps to mass production, they are valuable to healthcare manufacturing.
Industries Served:
Medical devices, automotive, electronics, and packaging.
Why Choose Sincere Tech?
- Our medical-grade precision molding factory meets the strict ISO 13485 standard.
- Provides all services, starting with design, prototyping, and ending with production.
- Ability to mold parts in cleanrooms for no-contamination products.
- Good quality assurance and validation are needed.
- Offering competitive prices to both small and large global clients.
2. Phillips-Medisize (USA)
Phillips Medisize is a Molex company and an industry titan in the field of integrated drug delivery, diagnostic devices, and Medical Electronics. A full-service medical injection molder, they have a global footprint and deep expertise in complex assemblies. They have state-of-the-art cleanroom facilities, which provide design and prototyping services as well as automated high-volume manufacturing services in case you need it. The company is a leading innovator of solutions for connecting digital health and of advanced product tracking.
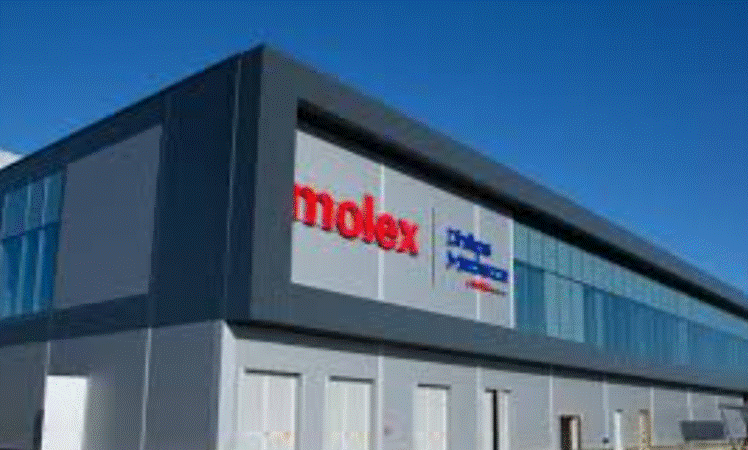
Company Profile:
Operating as a division of Molex, Phillips-Medisize focuses on making drug delivery, diagnostic, and connected health devices worldwide. Being present internationally in the US, Europe, and Asia, the company has cleanrooms from ISO Class 7 up to Class 8. They provide services at every step, taking care of design, development, testing, and full production. Among their clients are some of the world’s leading pharmaceutical and medical device companies.
Industries Served:
Drug delivery, diagnostics, and medical electronics.
Why Choose Phillips-Medisize?
- International operation enhanced by automation and maintained in cleanroom environments.
- Knowledge of connected health and using digital technology.
- A history of successful cooperation with leading MedTech companies.
- All of our operations worldwide comply with ISO 13485 and FDA standards.
- Experienced in handling the needs of major manufacturing projects.
3. Tessy Plastics (USA)
Tessy Plastics has been delivering high-precision plastic injection molding in the medical sector for decades and is notorious for its ISO 13485 certification. They have all the products in-house, from tooling to everything from automation to validation. Completely reliant on the medical field, they produce a wide array of surgical, diagnostic, and wearable medical devices that work closely with clients and partners to guarantee higher reliability, ease of scalability, and compliance with global regulations. They also possess the capabilities to micro mold and insert mold for delicate components.
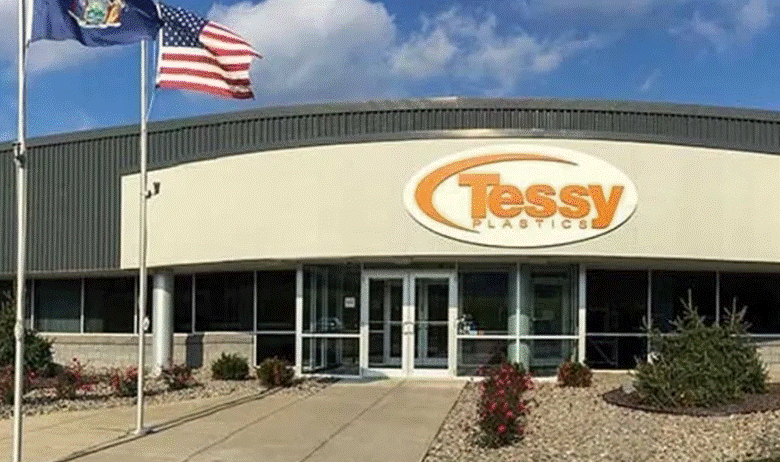
Company Profile:
Since 1976, Tessy Plastics has operated out of New York, USA, as a family business in the precision injection molding field. The medical side of Bosch stresses surgical, diagnostic and wearable devices, all made to strong quality standards. Tessy combines automation, advanced tooling, and assembly processes in its work. The company’s engineering staff cooperates with clients to solve problems in design, regulations, and fast launch.
Industries Served:
Medical, electronics, and consumer goods.
Why Choose Tessy?
- All steps from designing to selling are under one authority.
- Offers micro-molding and insert molding as its top strengths.
- Over 40 years of making medical devices.
- The company has cleanroom ISO Class 7 areas.
- The company is ISO 13485 certified and aims to meet all requirements for medical devices.
4. Gerresheimer (Germany)
Gerresheimer is a global leader in medical and pharmaceutical packaging with an important plastic injection molding division that is capable of manufacturing drug delivery systems, injection molded diagnostic devices, and pre–filled syringes. It maintains multiple cleanroom manufacturing facilities and operates by the highest regulatory standards. On account of their vertical integration of product design to mold fabrication and finally to final assembly, they are the preferred partner of the pharmaceutical companies across the globe.
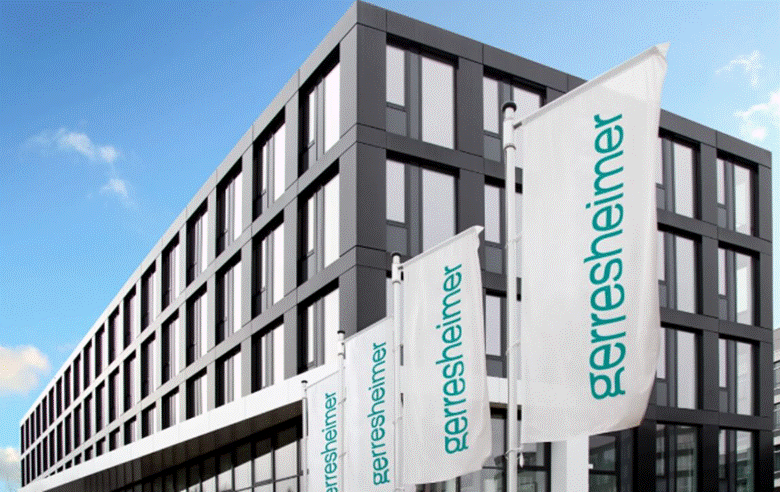
Company Profile:
Medical and pharmaceutical packaging companies widely recognize Gerresheimer and its long track record of injection molding. Global operations for the company include more than 30 sites, giving customers products ranging from insulin pens to inhalers and diagnostics kits. The company is strong because it covers the entire service range, from designing to creating the final packaging. Because of their advanced infrastructure, they can produce large medical devices that comply with many regulations.
Industries Served:
Pharmaceuticals, healthcare, and diagnostics.
Why Choose Gerresheimer?
- Manufacturing solutions that include a whole system.
- There are cleanroom-certified facilities in different locations worldwide.
- Novel developments in both packaging and devices.
- Many leading pharmaceutical organizations rely on us.
- Following all EU and US medical regulations.
5. Nypro Healthcare (Jabil – USA)
Nypro Healthcare is a part of Jabil, and delivers high–volume medical plastic injection molding solutions for high complexity and highly regulated markets. With its automation capabilities and engineering support, Nypro has manufacturing facilities worldwide. They concentrate on sophisticated medical applications like injectable drug delivery, diagnostic systems, and minimally invasive surgical tools. Nypro works with customers on a partnership model, making sure to provide R&D, prototyping, and manufacturing.
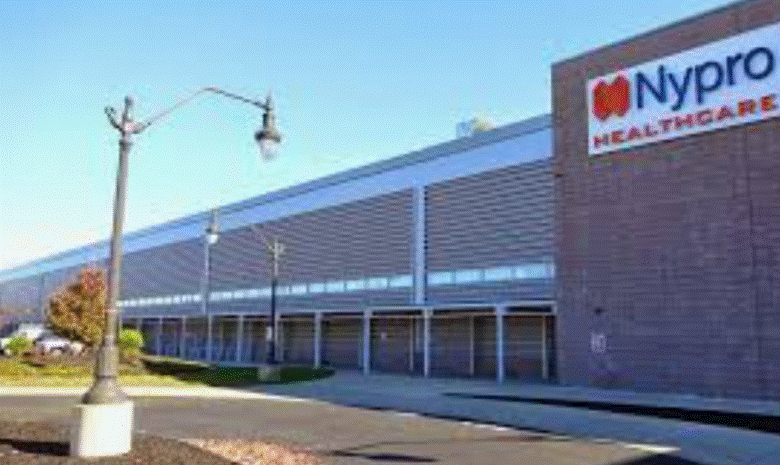
Company Profile:
Nypro, which belongs to Jabil Healthcare, provides complete CDMO services and injection molding for medical devices. Across five world regions, Nypro provides high-volume production for the surgical, diagnostic, and drug-delivery fields. Because of their skill in automation, meeting regulations, and making things smaller, clients can beat out the competition. They also work on engineering at the beginning, pick out important materials , and build prototypes.
Industries Served:
Drug delivery, diagnostics, and surgical systems.
Why Choose Nypro?
- Manufacturing facilities operating in several nations with the ability to grow production.
- Having detailed knowledge of the rules in regulated markets.
- Better automation and assembly bring automakers advantages.
- Early teamwork between R&D and early design.
- Leading provider in the making of high-risk medical devices.
6. Röchling Medical (Germany)
Röchling Medical, a part of the Röchling Group, offers end-to-end injection molding solutions for customers supporting the pharmaceuticals, diagnostics, and medical devices industries. They are globally available in Europe, the USA, and China. The competencies of Röchling include engineering and regulatory compliance, cleanroom molding. Their portfolio encompasses everything from lab-on-chip components to custom surgical device housings, often produced in fully validated Class 7 environments.
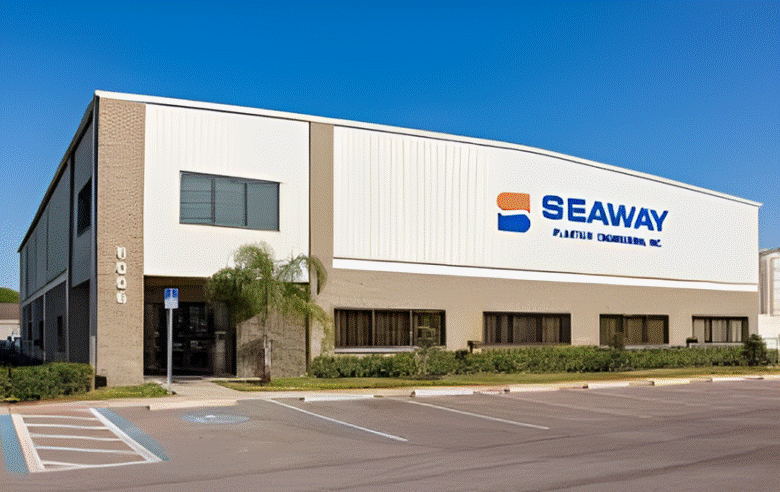
Company Profile:
Röchling Medical operates as part of the Röchling Group, helping pharmaceutical, diagnostic, and MedTech industries around the world. Cleanroom molding, lab-on-chip, and device housing are areas in which they specialize with manufacturing in Germany, the U.S., and China. Röchling has technical assistance, regulatory functions, and full support for product management from start to finish. Manufacturing systems at these facilities support both limited and large production runs.
Industries Served:
Diagnostics, pharma, and surgical instruments.
Why Choose?
- Firms are operating across several countries in Europe, China, and the United States.
- Broad cleanroom manufacturing services are available.
- Having worked in Class 7 and Class 8 molding environments.
- Delivering engineering help for the following regulations.
- We have the skills to develop custom components for medical use.
7. Seaway Plastics Engineering (USA)
Seaway Plastics, specializing in low to mid volume production, is a credible partner for medical OEMs that require fast turnaround and flexible support. Their Services are cleanroom injection molding, in-house tooling, and assembly services. Seaway has particular fame in the orthopedic and surgical devices segment. The company also provides protocols on IQ/OQ/PQ validation, making it clear that their products are highly regulated.
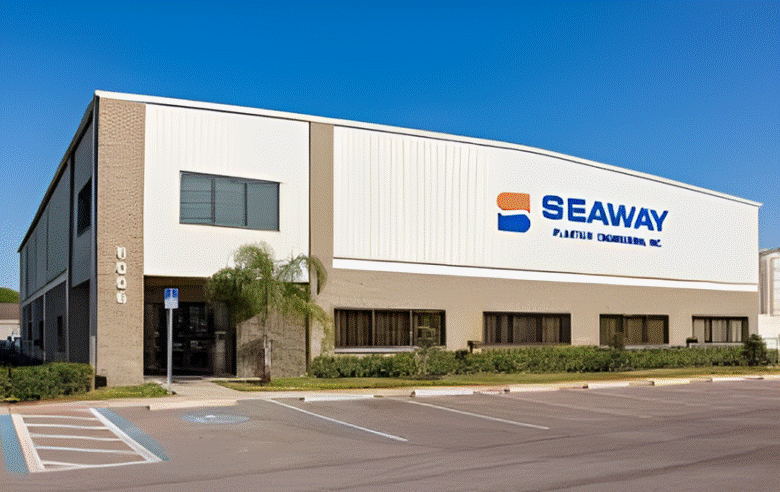
Company Profile:
Seaway Plastics mainly offers low-to-mid volume injection molding to medical device companies. The facilities at ISO Class 7 cleanrooms allow for mold making, as well as validation and assembly of final products. Seaway makes its mark mainly with orthopedic and surgical instrumentation. Due to their quick production times, people go to these companies for both sample and small-scale projects.
Industries Served:
Orthopedics, surgical tools, and diagnostics.
Why Choose?
- Rapid prototyping and low numbers of samples are offered.
- We offer the development and support of our own testing and automated tools.
- You can trust that our facilities are certified by both ISO 13485 and regulated by the FDA.
- Special molding for sensitive components is possible in cleanrooms.
- Offers complete flexibility to the customer.
8. MedPlast (now Viant – USA)
This company is now known as Viant and is a powerhouse in making medical devices. They do contract manufacturing activities, including plastic injection molding, extrusion, assembly, packaging, and sterilization. Their skills in molding go beyond implantable devices, diagnostic kits, and drug-delivery systems. Viant’s emphasis on design for manufacturability (DFM) and intense quality control makes them an ideal provider for high-risk medical applications.
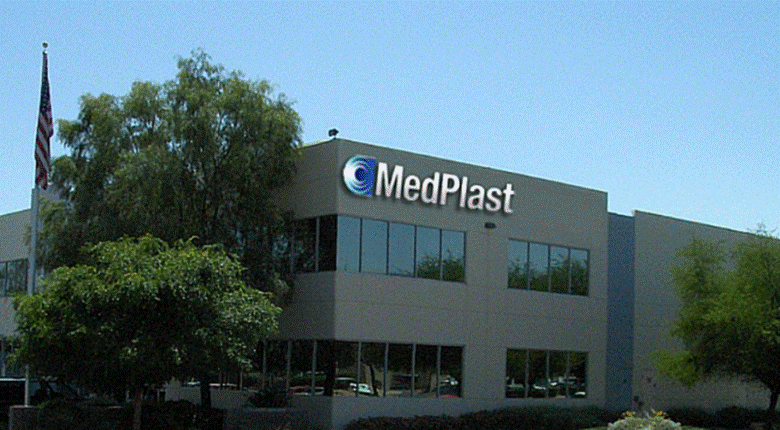
Company Profile:
The company runs under the brand Viant, offering a variety of medical device manufacturing processes, for example, injection molding and sterilization. Their businesses extend to markets for orthopedics, diagnostics and single-use devices. Because of Viant’s DFM skills and inside regulatory resources, the solutions are created to be both safe and scalable. There are more than 25 Vifor Pharma facilities spread around the globe where they apply their regulatory know-how.
Industries Served:
Implantable devices, diagnostics, and surgical systems.
Why Choose ?
- Offering services for design for manufacture, molding and sterilization.
- Proven experience delivering care for medical issues that are hard to treat.
- Designed for the world, produced for the world.
- You can change your order as needed and all products are controlled for quality.
- All our facilities are ISO 13485 and FDA certified.
9. Technoplast (Israel)
Technoplast is an emerging player in the business of precision medical plastic molding, based in Israel. Among the products it offers are product design, rapid prototyping, to mass production with a heavy focus on customized medical components. Among their clients are multi-national medical device manufacturers, and they are known for speed to market because their operations are very agile and they have a strong R&D department. Technoplast is exceptionally strong (cardiology, diagnostics, disposable devices).
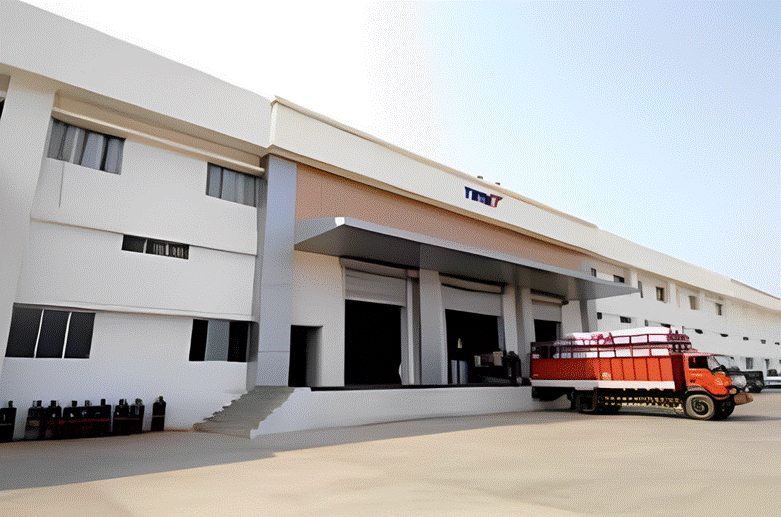
Company Profile:
Technoplast is an Israeli business that supplies advanced plastic molding for use in medical devices. Companies provide help with designing products, prototyping, manufacturing molds, and producing items on a large scale. Technoplast is recognized for being flexible, doing effective R&D, and having experience in making products for cardiology, diagnostics, and single-use disposables. Fast-paced delivery and low manufacturing costs are the top priorities for the company.
Industries Served:
Cardiology, diagnostics, and disposable devices.
Why Choose Technoplast?
- Improved output through agile actions and fast prototyping.
- High precision mold making for detailed medical parts.
- Doing innovative R&D for medical use.
- High rates of getting products to the market.
- ISO 13485 certification is coupled with CE and FDA-compliant products.
10. TK Mold (China)
Having two and the last Chinese companies from this list, TK Mold is known for high precision tooling and injection molding services. They deal in medical-grade moulds and components, exporting products in North America, Europe, and other Asian markets. Their strengths are engineering design and their ability to bring these ideas to life through both the making of molds and small to medium volume production. TK Mold possesses a certified ISO document, adheres to international medical standards. Therefore, they are a good company to outsource production work to.
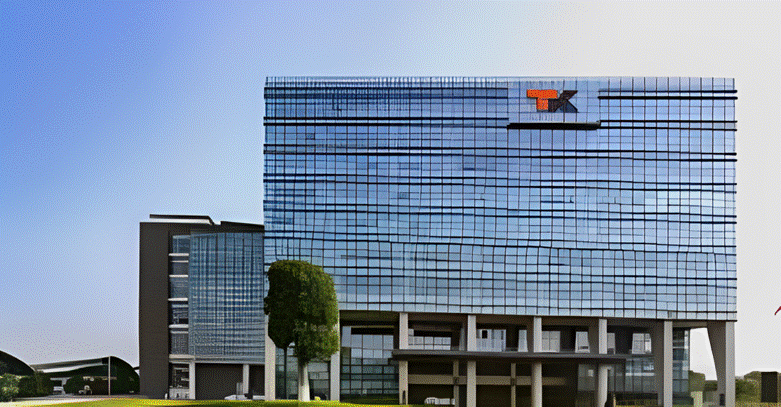
الملف الشخصي للشركة
TK Mold is well known in China for high-quality injection molds and medical device parts. Their clients in North America, Europe, and Asia receive cleanroom molding for Class 7 applications. Mold is supported all the way from its original design through medium-batch fabrication and post-production steps. Because they are ISO 13485 certified and meet international standards, they have earned trust as an offshore partner.
الصناعات المخدومة
Medical, electronics, and automotive.
Why Choose?
- Only a small number of professionally designed molds are used for production.
- Paying particular attention to innovation in engineering.
- ISO-certified and according to medical guidelines.
- Provide expertise to the EU, the USA, and Asia.
- Affordable methods for working with OEMs.
Future Prospects For Medical Plastic Injection Molder Companies.
With the development of the healthcare industry, medical injection molding companies are expected to develop in several essential aspects. Here’s what the future holds:
1. Adoption of Smart Materials
- Companies are putting investment in materials such as antimicrobial, biodegradable, or bioresorbable polymers that provide improved functionality.
- These supplies allow the use of safer and more sustainable single-use medical devices.
2. Expansion into Microfluidics & Miniaturization
- More and more processing firms are forced to create ultra-small and intricate parts for lab-on-a-chip, wearable sensors, and diagnosis devices.
- Micro-molding ability will be needed to remain competitive.
3. Automation & Industry 4.0 Integration
- However, the Advanced automation and real-time data analysis will enable the companies to upgrade their process efficiency, traceability, and quality control.
- The smart factories with connected systems will minimize human error, and productivity will increase.
4. Customization & On-Demand Manufacturing
- There is a rising demand for personalised medical devices, so companies are embracing a flexible, batch production mode.
- Rapid prototyping and additive manufacturing may enhance the traditional molding processes.
5. Sustainability & Environmental Compliance
- World decrees are forcing companies to recycle, reduce waste and energy consumption, and reduce the use of non-recyclable plastics.
- Manufacturers are embracing the green initiatives and practices in the circular economy.
6. Increased Regulatory Scrutiny
- With the advent of new and innovative materials and technology, companies can expect more rigorous validation, traceability, and compliance protocols.
- There will be a need to invest in the red tape expertise for the sake of continued market access.
7. Strategic Partnerships with MedTech Firms
- Companies are establishing tighter collaborations with medical OEMs so as to co-innovate the innovative IP-sensitive solutions.
- It will become a competitive advantage to involve the early-stage design.
الخاتمة
It is important to select the best medical plastic injection molding manufacturer to ensure that your medical device is successful in terms of safety, scaled production, and all compliance. This list is the world’s elite companies, not only in terms of following the technical and regulatory requirements of the medical industry, but they also bring innovative and customer-oriented solutions.
Starting from the giants of the world, such as Phillips-Medisize and Gerresheimer, to the niche companies such as Sincere Tech and Technoplast, every single one of them has certain proven expertise and capabilities in the healthcare field. Whether you are advancing a new diagnostic tool or expanding the output of an established piece of machinery, collaborating with either of these reliable medical injection molding suppliers puts you at the forefront of quality specifications and the competitive race.
Reputable medical injection molding providers guarantee staying ahead in terms of quality benchmarks and competitive play on the market.
الأسئلة الشائعة
1. What is the medical plastic injection molding?
It is a manufacturing process that manufactures high precision plastic parts for medical applications environment with special equipment and materials within high regulatory standards.
2. Why is ISO 13485 certification important for medical molding companies?
It ensures that the company complies with internationally accepted standards of quality management systems of the medical device industry, which is the key to regulatory compliance and product safety.
3. Which materials are usually employed in medical injection molding?
The common materials include medical grade polycarbonate, polypropylene, polyethylene, and thermoplastic elastomers must be biocompatible and sterilizable materials.
4. What is the effect of cleanrooms in medical injection molding?
Cleanrooms are an environment that can be free of contamination, vital in the production of sterile/sensitive medical components by minimizing the chances of particulate contamination.
5. Is it possible for small firms to match the output that big manufacturers produce here?
Yes. Numerous small firms provide niche expertise, agile development, and rapid prototyping services that are indeed good partners for specializing or custom work.