Moulage par injection de plastique renforcé de nylon : avantages, défis et meilleures pratiques
Moulage par injection de plastique renforcé de nylon : avantages, défis et meilleures pratiques
1. Introduction
Le moulage par injection est une pierre angulaire de la fabrication moderne, en particulier pour la création de formes et de composants complexes en grandes quantités. Parmi la myriade de matériaux disponibles pour ce procédé, les plastiques renforcés de nylon se distinguent par leur combinaison unique d'attributs de performance, de polyvalence et de rentabilité. Les fabricants s'efforçant d'obtenir des matériaux légers, durables et performants, le nylon renforcé est devenu de plus en plus important dans diverses industries, de l'automobile à l'aérospatiale en passant par l'électronique.
Le nylon, en particulier sous ses formes renforcées, offre des avantages par rapport aux plastiques standard qui le rendent particulièrement intéressant pour les applications exigeantes. Le nylon renforcé associe les avantages inhérents au nylon, tels que la ténacité, l'élasticité et la résistance à divers produits chimiques, à des propriétés mécaniques améliorées grâce à l'inclusion de matériaux de renforcement tels que des fibres de verre ou de carbone. Cette synergie permet d'obtenir un matériau capable de résister à des contraintes plus importantes, à l'abrasion et aux conditions thermiques sans compromettre l'intégrité structurelle.
Le besoin croissant de composants de haute performance dans des secteurs tels que l'automobile, où la réduction du poids peut conduire à une meilleure efficacité énergétique, a propulsé les plastiques renforcés de nylon sous les feux de la rampe. En outre, l'industrie aérospatiale bénéficie de l'excellent rapport poids/résistance du matériau, ce qui est essentiel dans les applications où chaque gramme compte. Dans le domaine de l'électronique, les propriétés isolantes et la stabilité thermique du nylon renforcé en font un choix privilégié pour les boîtiers et les pièces structurelles.
Cet article se penche sur l'univers du plastique renforcé de nylon, en explorant ses propriétés, ses avantages, ses défis et ses meilleures pratiques en matière de moulage par injection. De la compréhension des différents types de nylon et de leurs renforts à l'examen des applications réelles, nous brosserons un tableau complet des raisons pour lesquelles ce matériau est un choix de premier plan pour les solutions de fabrication modernes.
2. Qu'est-ce que le plastique renforcé de nylon ?
Le nylon, un polymère synthétique, est réputé pour ses propriétés polyvalentes, ce qui en fait un produit de base dans de nombreuses applications. Deux types de nylon sont principalement utilisés dans la fabrication : Le Nylon 6 et le Nylon 66. Le Nylon 6, dérivé du caprolactame, est connu pour sa flexibilité et sa facilité de mise en œuvre, tandis que le Nylon 66, produit à partir d'hexaméthylènediamine et d'acide adipique, se caractérise par une plus grande solidité et une meilleure résistance à la chaleur. Le choix entre ces deux matériaux dépend souvent des exigences spécifiques de l'application, telles que la tolérance à la température ou la charge mécanique.
Le nylon renforcé entre en jeu pour soutenir ces polymères de base. Les principaux types de renforts sont les suivants :
- Nylon renforcé de fibres de verre: Cette variante incorpore des fibres de verre, ce qui améliore la résistance à la traction et à la déformation. Elle est particulièrement utile dans les applications nécessitant une rigidité supérieure.
- Nylon renforcé de fibres de carbone: Les fibres de carbone offrent un rapport poids/résistance exceptionnel, ce qui les rend idéales pour les applications où la légèreté et la résistance sont essentielles.
- Nylon chargé de minéraux: L'ajout de minéraux tels que le talc améliore la stabilité dimensionnelle et les propriétés thermiques tout en réduisant les coûts.
Les plastiques renforcés de nylon se distinguent par leurs propriétés clés. Ils présentent une résistance mécanique et une rigidité élevées, ce qui les rend adaptés aux applications exigeantes. En outre, ces matériaux sont résistants à l'usure et à l'abrasion, ce qui les rend idéaux pour les composants soumis à la friction, tels que les engrenages et les roulements. La résistance aux produits chimiques est une autre propriété remarquable, qui permet d'utiliser le nylon renforcé dans des environnements où l'exposition à des substances agressives est inévitable.
Chaque type de renfort affecte différemment les propriétés du nylon, ce qui permet aux fabricants d'adapter les matériaux à des besoins spécifiques. Par exemple, alors que le nylon renforcé de fibres de verre est excellent pour les applications structurelles, le nylon renforcé de fibres de carbone est plus adapté aux composants aérospatiaux en raison de sa légèreté et de sa grande résistance à la traction.
3. Avantages du moulage par injection avec du plastique renforcé de nylon
Les avantages de l'utilisation du plastique renforcé de nylon dans le moulage par injection sont multiples et remarquables. L'un des principaux avantages est sa résistance mécanique et sa durabilité élevées. Les composants fabriqués à partir de nylon renforcé peuvent résister à de lourdes charges et à des contraintes mécaniques, ce qui les rend idéaux pour des applications critiques dans diverses industries. Des études ont montré que les plastiques renforcés de nylon peuvent avoir une résistance à la traction supérieure à celle de certains métaux, offrant ainsi aux ingénieurs une alternative robuste pour les composants structurels.
Un autre avantage essentiel est l'excellente résistance à la chaleur et aux produits chimiques. Les matériaux en nylon renforcé peuvent fonctionner efficacement dans des environnements où les températures fluctuent et où ils sont exposés à des produits chimiques agressifs sans se dégrader. Cette résistance est particulièrement précieuse dans les secteurs de l'automobile et de l'aérospatiale, où les composants sont souvent soumis à des conditions extrêmes. Par exemple, les capots de moteur fabriqués en nylon renforcé de fibres de verre peuvent supporter des températures élevées sans se déformer ni perdre leur intégrité structurelle.
L'amélioration de la stabilité dimensionnelle est un autre avantage qui distingue le nylon renforcé de ses homologues non renforcés. Les composants fabriqués à partir de nylon renforcé conservent mieux leur forme et leurs dimensions, ce qui améliore la qualité du produit et réduit les déchets dans les processus de fabrication. Cette propriété est particulièrement importante pour les composants de précision dans l'électronique et les appareils médicaux, où les tolérances peuvent être critiques.
La résistance à l'usure est une caractéristique essentielle des plastiques renforcés de nylon, ce qui les rend parfaits pour les applications impliquant des frottements et des pièces mobiles, telles que les engrenages et les roulements. Cet avantage peut se traduire par une durée de vie plus longue des composants, une réduction des coûts de maintenance et une amélioration de l'efficacité globale des machines et des équipements.
En outre, l'utilisation de nylon renforcé peut conduire à une réduction significative du poids par rapport aux métaux traditionnels. Cette réduction est bénéfique dans des secteurs comme l'automobile et l'aérospatiale, où la réduction du poids est directement liée à l'amélioration du rendement énergétique et des performances. Par exemple, le remplacement de composants métalliques par du plastique renforcé de nylon peut réduire le poids total d'un véhicule, ce qui contribue à réduire les émissions et à améliorer la tenue de route.
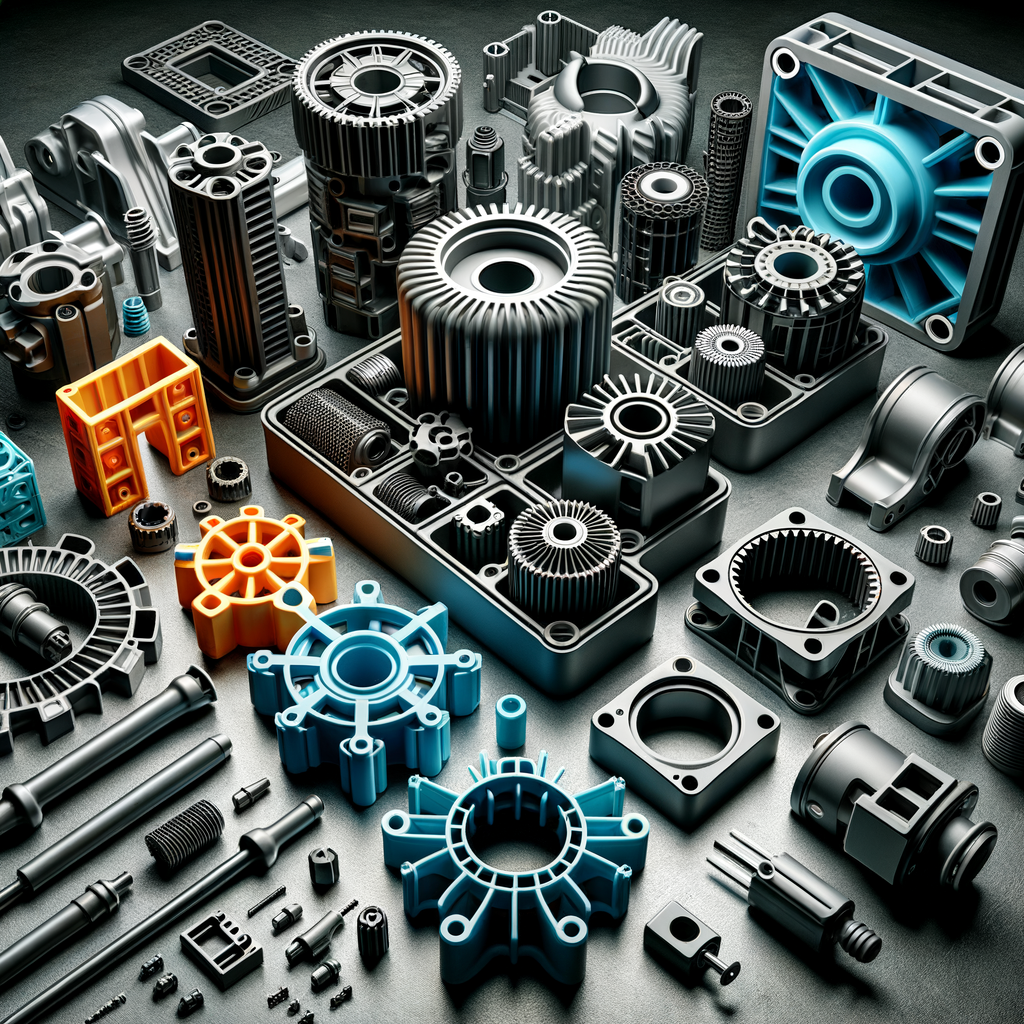
Résumé des avantages :
- Résistance mécanique et durabilité élevées
- Excellente résistance à la chaleur et aux produits chimiques
- Stabilité dimensionnelle améliorée
- Propriétés d'usure et de friction améliorées
- Réduction du poids par rapport aux métaux
Ces avantages font des plastiques renforcés de nylon un choix de premier ordre pour de nombreuses applications, ce qui permet aux fabricants de produire des produits de haute qualité qui répondent aux exigences de leurs industries.
4. Défis et considérations dans le moulage du plastique renforcé de nylon
Bien que les avantages du plastique renforcé de nylon soient convaincants, plusieurs défis doivent être relevés au cours du processus de moulage par injection. L'un des défis les plus importants est celui des températures de moulage élevées nécessaires à la transformation de ces matériaux. Le contrôle de la température est crucial, car une chaleur insuffisante peut entraîner une fusion incomplète et des caractéristiques d'écoulement inadéquates, tandis qu'une chaleur excessive peut dégrader le polymère ou provoquer un retrait excessif et un gauchissement du produit final. Par conséquent, les fabricants doivent soigneusement calibrer leurs procédés afin d'atteindre l'équilibre optimal pour chaque mélange spécifique de nylon renforcé.
L'augmentation de l'usure des moules est un autre problème. L'incorporation de fibres, en particulier de verre et de carbone, peut provoquer une abrasion qui accélère l'usure des moules. Cette usure nécessite une maintenance ou un remplacement plus fréquents, ce qui peut augmenter considérablement les coûts de production. Les fabricants doivent choisir des matériaux et des conceptions de moules appropriés, et éventuellement utiliser des revêtements qui améliorent la résistance à l'usure pour atténuer ce problème.
L'absorption d'humidité est un problème bien connu des matériaux en nylon, et le nylon renforcé ne fait pas exception. La capacité du nylon à absorber l'humidité peut entraîner des modifications des propriétés mécaniques, affectant la résistance et la stabilité dimensionnelle. Par exemple, l'humidité peut provoquer un gonflement et un gauchissement au cours du processus de moulage. Pour atténuer ce problème, les fabricants doivent mettre en œuvre des protocoles de séchage stricts avant le traitement afin de s'assurer que la teneur en humidité du matériau reste faible.
En outre, le gauchissement et le rétrécissement potentiels des pièces moulées peuvent poser des problèmes pour obtenir des tolérances serrées. Ces problèmes peuvent être exacerbés par un refroidissement inégal des pièces moulées, en particulier dans le cas de sections épaisses. Les fabricants doivent optimiser les canaux de refroidissement dans les moules pour assurer un refroidissement uniforme, ce qui peut contribuer à réduire l'incidence du gauchissement et des incohérences dimensionnelles.
Des difficultés de traitement, telles que le maintien d'une distribution uniforme des fibres, peuvent également survenir. Si les fibres sont réparties de manière inégale au cours du processus d'injection, cela peut entraîner des variations dans les propriétés mécaniques de la pièce finie. Ceci est particulièrement critique dans les applications qui requièrent une résistance et une fiabilité élevées. Les fabricants doivent prêter une attention particulière aux paramètres de traitement et envisager des conceptions qui permettent une orientation optimale des fibres.
Résumé des défis :
- Températures de moulage élevées requises
- Augmentation de l'usure des moules en raison de l'abrasivité des fibres
- Problèmes d'absorption d'humidité
- Risque de déformation et de rétraction des pièces moulées
- Difficultés de traitement dans la distribution des fibres
Ces défis obligent les fabricants à adopter une approche globale du processus de moulage, en intégrant les meilleures pratiques pour atténuer les risques et améliorer les performances des plastiques renforcés de nylon.
5. Meilleures pratiques pour le moulage par injection de plastique renforcé de nylon
Pour obtenir de bons résultats lors du moulage de plastiques renforcés de nylon, les fabricants doivent respecter plusieurs bonnes pratiques qui répondent aux défis mentionnés ci-dessus. Tout d'abord, le séchage du matériau est crucial avant le moulage. La teneur en humidité du nylon peut avoir un impact significatif sur la qualité des pièces moulées, entraînant des défauts tels que des bulles ou une mauvaise finition de surface. L'utilisation d'un séchoir déshydratant ou d'un séchoir à air chaud permet de réduire efficacement les niveaux d'humidité. Une bonne règle empirique consiste à sécher le nylon à des températures de l'ordre de 80°C à 90°C pendant plusieurs heures, en fonction de la teneur en humidité initiale du matériau.
L'optimisation de la conception des moules est un autre aspect essentiel du processus de moulage par injection. Des caractéristiques telles qu'une bonne ventilation et des canaux de refroidissement appropriés peuvent faire une différence significative dans le résultat des pièces moulées. L'aération est essentielle pour permettre aux gaz piégés de s'échapper pendant le processus d'injection, ce qui peut contribuer à éviter les défauts. Les canaux de refroidissement doivent être conçus de manière à assurer un refroidissement uniforme de la pièce, ce qui minimise le risque de déformation et de rétrécissement.
En ce qui concerne les paramètres de moulage par injection, il est essentiel de contrôler soigneusement la température, la pression et la vitesse d'injection. La température de fusion des plastiques renforcés de nylon se situe généralement entre 230°C et 260°C, en fonction de la formulation spécifique. Un contrôle adéquat de la vitesse d'injection peut également aider à gérer le flux de matière et à minimiser le risque de rupture des fibres. Des vitesses d'injection élevées peuvent entraîner un cisaillement des fibres, ce qui compromet les propriétés mécaniques du produit final.
Il est également essentiel de réduire au minimum la rupture des fibres au cours du traitement. La longueur et l'orientation des fibres sont des facteurs importants qui influencent les propriétés mécaniques des pièces moulées. Pour éviter d'endommager les fibres, les fabricants peuvent optimiser les paramètres de traitement, assurer une manipulation correcte des matériaux et envisager l'utilisation d'additifs conçus pour améliorer l'intégrité des fibres.
Les considérations relatives au post-traitement méritent également une attention particulière. Des techniques telles que le recuit peuvent améliorer la stabilité dimensionnelle des pièces moulées et soulager les contraintes internes qui peuvent s'être formées pendant le processus d'injection. L'usinage peut s'avérer nécessaire pour les pièces qui nécessitent des tolérances serrées ou des finitions de surface spécifiques. Les fabricants doivent tenir compte des exigences de post-traitement pendant la phase de conception afin de rationaliser les opérations et de s'assurer que le produit final répond aux normes de qualité.
Résumé des meilleures pratiques :
- Exigences en matière de séchage des matériaux avant le moulage
- Optimisation de la conception des moules pour le nylon renforcé
- Paramètres appropriés pour le moulage par injection
- Minimiser la rupture des fibres pendant le traitement
- Considérations sur le post-traitement
L'application de ces bonnes pratiques peut améliorer les performances et la fiabilité des produits fabriqués avec des plastiques renforcés de nylon.
6. Applications du moulage par injection renforcé de nylon
Les applications du moulage par injection de nylon renforcé sont aussi diverses que les industries qui les utilisent. Dans le secteur automobile, le plastique renforcé de nylon est utilisé pour fabriquer des composants tels que des couvercles de moteur, des supports et des engrenages. Ces pièces bénéficient des propriétés de résistance et de légèreté du matériau, ce qui permet d'améliorer le rendement énergétique et les performances. Un exemple notable est l'utilisation du nylon renforcé de fibres de verre dans les applications sous le capot, où la résistance à la chaleur du matériau est essentielle.
L'industrie de l'électronique grand public utilise également beaucoup de plastiques renforcés de nylon. Les boîtiers des smartphones, tablettes et autres appareils nécessitent souvent des matériaux robustes capables de résister à l'usure quotidienne. Les propriétés isolantes du nylon, associées à sa résistance mécanique, en font un choix idéal pour les pièces structurelles qui protègent les composants sensibles tout en offrant un attrait esthétique.
Dans les machines industrielles, les composants tels que les roulements, les rouleaux et les systèmes de convoyage tirent parti de la résistance à l'usure et de la solidité des plastiques renforcés de nylon. Ces applications impliquent souvent des opérations à grande vitesse où les matériaux traditionnels peuvent faiblir sous la contrainte. En utilisant le nylon renforcé, les fabricants peuvent développer des composants plus durables qui réduisent les temps d'arrêt pour maintenance et améliorent l'efficacité opérationnelle.
Le secteur aérospatial, connu pour ses exigences rigoureuses, fait également appel aux plastiques renforcés de nylon. Les avantages de ces matériaux en termes d'économie de poids sont primordiaux, avec des applications allant des composants intérieurs aux éléments structurels. L'utilisation du nylon renforcé de fibres de carbone dans les avions peut entraîner des réductions de poids significatives, améliorant ainsi le rendement énergétique et les performances.
Les applications médicales constituent un autre domaine prometteur pour le moulage par injection de nylon renforcé. En raison des besoins de biocompatibilité et de résistance, les matériaux en nylon renforcé peuvent être utilisés dans une variété de dispositifs, y compris les instruments chirurgicaux et les implants. La capacité de mouler avec précision des géométries complexes permet des conceptions innovantes qui peuvent répondre à des exigences réglementaires strictes.
Résumé des applications :
- Composants automobiles (couvercles de moteur, supports, engrenages)
- Électronique grand public (boîtiers, pièces structurelles)
- Machines industrielles (roulements, rouleaux)
- Applications aérospatiales et médicales
Ces applications illustrent la polyvalence et l'efficacité des plastiques renforcés de nylon, soulignant leur rôle essentiel dans l'amélioration des performances des produits dans de nombreuses industries.
7. Conclusion
En résumé, moulage par injection Le plastique renforcé de nylon présente de nombreux avantages qu'il ne faut pas négliger. Les propriétés uniques du nylon renforcé, notamment sa grande résistance mécanique, son excellente résistance à la chaleur et aux produits chimiques et sa stabilité dimensionnelle améliorée, en font un matériau de choix pour un large éventail d'industries. Malgré les défis associés à la transformation de ces matériaux, tels que les températures de moulage élevées et les problèmes d'absorption de l'humidité, la mise en œuvre de bonnes pratiques peut conduire à des résultats positifs.
Pour l'avenir, on s'attend à ce que des tendances telles que l'importance croissante accordée à la durabilité et le développement de plastiques renforcés de nylon d'origine biologique gagnent du terrain. Les fabricants continueront probablement à explorer des moyens innovants d'optimiser les performances des matériaux renforcés de nylon, afin de s'assurer qu'ils restent compétitifs sur un marché de plus en plus exigeant.
Lors de la sélection du bon type de plastique renforcé de nylon pour des applications spécifiques, il est essentiel de tenir compte de l'environnement opérationnel, des propriétés mécaniques requises et de toute norme réglementaire applicable. En évaluant soigneusement ces facteurs, les fabricants peuvent exploiter tout le potentiel des plastiques renforcés de nylon, ouvrant ainsi la voie à la prochaine génération de composants légers, durables et performants.
Compte tenu de l'évolution de la science des matériaux et de la technologie de fabrication, il ne fait aucun doute que le moulage par injection renforcé de nylon a un bel avenir devant lui. Alors que de plus en plus d'industries reconnaissent les avantages de ce matériau innovant, les possibilités de nouvelles applications et d'amélioration des produits existants sont illimitées. Les fabricants sont encouragés à participer aux discussions, à partager les meilleures pratiques et à explorer les partenariats qui permettront de réaliser de nouvelles avancées dans ce domaine.
Laisser un commentaire
Rejoindre la discussion?N’hésitez pas à contribuer !