Moldeo por inyección con plástico reforzado con nailon: ventajas, retos y mejores prácticas
Moldeo por inyección con plástico reforzado con nailon: ventajas, retos y mejores prácticas
1. Introducción
El moldeo por inyección es una piedra angular de la fabricación moderna, sobre todo para crear formas y componentes complejos en grandes volúmenes. Entre la miríada de materiales disponibles para este proceso, los plásticos reforzados con nailon destacan por su combinación única de atributos de rendimiento, versatilidad y rentabilidad. A medida que los fabricantes se esfuerzan por conseguir materiales ligeros, duraderos y de alto rendimiento, el nailon reforzado ha ido adquiriendo cada vez más importancia en diversas industrias, desde la automoción hasta la aeroespacial y la electrónica.
El nailon, especialmente en sus formas reforzadas, ofrece ventajas sobre los plásticos estándar que lo hacen especialmente atractivo para aplicaciones exigentes. El nailon reforzado combina las ventajas inherentes del nailon, como la dureza, la elasticidad y la resistencia a diversos productos químicos, con propiedades mecánicas mejoradas derivadas de la inclusión de materiales de refuerzo como fibras de vidrio o de carbono. Esta sinergia da como resultado un material que puede soportar mayores tensiones, abrasión y condiciones térmicas sin comprometer la integridad estructural.
La creciente necesidad de componentes de alto rendimiento en sectores como la automoción, donde la reducción de peso puede mejorar la eficiencia del combustible, ha impulsado el uso de plásticos reforzados con nailon. Además, la industria aeroespacial se beneficia de la excelente relación resistencia-peso de este material, fundamental en aplicaciones en las que cada gramo cuenta. En electrónica, las propiedades aislantes y la estabilidad térmica del nailon reforzado lo convierten en la opción preferida para carcasas y piezas estructurales.
Este artículo profundiza en el mundo del plástico reforzado con nailon, explorando sus propiedades, ventajas, retos y mejores prácticas para el moldeo por inyección. Desde la comprensión de los distintos tipos de nailon y sus refuerzos hasta el análisis de las aplicaciones en el mundo real, pintaremos un cuadro completo de por qué este material es una opción líder para las soluciones de fabricación modernas.
2. ¿Qué es el plástico reforzado con nailon?
El nailon, un polímero sintético, es famoso por sus versátiles propiedades, que lo convierten en un elemento básico en diversas aplicaciones. Principalmente, en la fabricación predominan dos tipos de nailon: el nailon 6 y el nailon 66. El Nylon 6, derivado de la caprolactama, es conocido por su flexibilidad y procesabilidad, mientras que el Nylon 66, producido a partir de hexametilendiamina y ácido adípico, es más fuerte y resistente al calor. La elección entre estos dos materiales suele depender de los requisitos específicos de la aplicación, como la tolerancia a la temperatura o la carga mecánica.
El nailon reforzado entra en juego para reforzar estos polímeros de base. Los principales tipos de refuerzos incluyen:
- Nylon reforzado con fibra de vidrio: Esta variante incorpora fibras de vidrio, lo que aumenta la resistencia a la tracción y a la deformación. Es especialmente útil en aplicaciones que requieren una rigidez superior.
- Nylon reforzado con fibra de carbono: Las fibras de carbono ofrecen una excepcional relación resistencia-peso, lo que las hace ideales para aplicaciones en las que tanto el diseño ligero como la resistencia son fundamentales.
- Nylon relleno de minerales: La adición de minerales como el talco mejora la estabilidad dimensional y las propiedades térmicas, al tiempo que reduce los costes.
Las propiedades clave de los plásticos reforzados con nailon son las que realmente los hacen brillar. Presentan una gran resistencia mecánica y rigidez, lo que los hace adecuados para aplicaciones exigentes. Además, estos materiales son resistentes al desgaste y la abrasión, lo que los hace ideales para componentes sujetos a fricción, como engranajes y cojinetes. La resistencia química es otra propiedad destacada, lo que permite emplear el nailon reforzado en entornos en los que la exposición a sustancias agresivas es inevitable.
Cada tipo de refuerzo afectará de forma diferente a las propiedades del nailon, lo que permite a los fabricantes adaptar los materiales a necesidades específicas. Por ejemplo, mientras que el nailon reforzado con fibra de vidrio es excelente para aplicaciones estructurales, el nailon reforzado con fibra de carbono puede ser más adecuado para componentes aeroespaciales por su ligereza y su elevada resistencia a la tracción.
3. Ventajas del moldeo por inyección con plástico reforzado con nailon
Las ventajas de utilizar plástico reforzado con nailon en el moldeo por inyección son múltiples y dignas de mención. Una de las principales ventajas es su gran resistencia mecánica y durabilidad. Los componentes fabricados con nailon reforzado pueden soportar cargas pesadas y tensiones mecánicas, lo que los hace ideales para aplicaciones críticas en diversas industrias. Los estudios han demostrado que los plásticos reforzados con nailon pueden tener una resistencia a la tracción superior a la de algunos metales, lo que proporciona a los ingenieros una alternativa robusta para componentes estructurales.
Otra ventaja fundamental es la excelente resistencia al calor y a los productos químicos. Los materiales de nailon reforzado pueden funcionar eficazmente en entornos con temperaturas fluctuantes y exposición a productos químicos agresivos sin degradarse. Esta resistencia es especialmente valiosa en las industrias automovilística y aeroespacial, donde los componentes se enfrentan a menudo a condiciones extremas. Por ejemplo, las cubiertas de motor fabricadas con nailon reforzado con fibra de vidrio pueden soportar altas temperaturas sin deformarse ni perder integridad estructural.
La mejora de la estabilidad dimensional es otra ventaja que diferencia al nailon reforzado de sus homólogos no reforzados. Los componentes fabricados con nailon reforzado mantienen mejor su forma y dimensiones, lo que mejora la calidad del producto y reduce los residuos en los procesos de fabricación. Esta propiedad es especialmente importante para los componentes de precisión de aparatos electrónicos y médicos, donde las tolerancias pueden ser críticas.
La resistencia al desgaste es una característica esencial de los plásticos reforzados con nailon, lo que los hace perfectos para aplicaciones que implican fricción y piezas móviles, como engranajes y cojinetes. Esta ventaja puede traducirse en una mayor vida útil de los componentes, una reducción de los costes de mantenimiento y una mejora de la eficiencia general de la maquinaria y los equipos.
Además, el uso de nailon reforzado puede reducir considerablemente el peso en comparación con los metales tradicionales. Esta reducción es beneficiosa en industrias como la automovilística y la aeroespacial, donde la disminución del peso está directamente correlacionada con la mejora de la eficiencia del combustible y el rendimiento. Por ejemplo, la sustitución de componentes metálicos por plástico reforzado con nailon puede reducir el peso total de un vehículo, lo que contribuye a reducir las emisiones y a mejorar la maniobrabilidad.
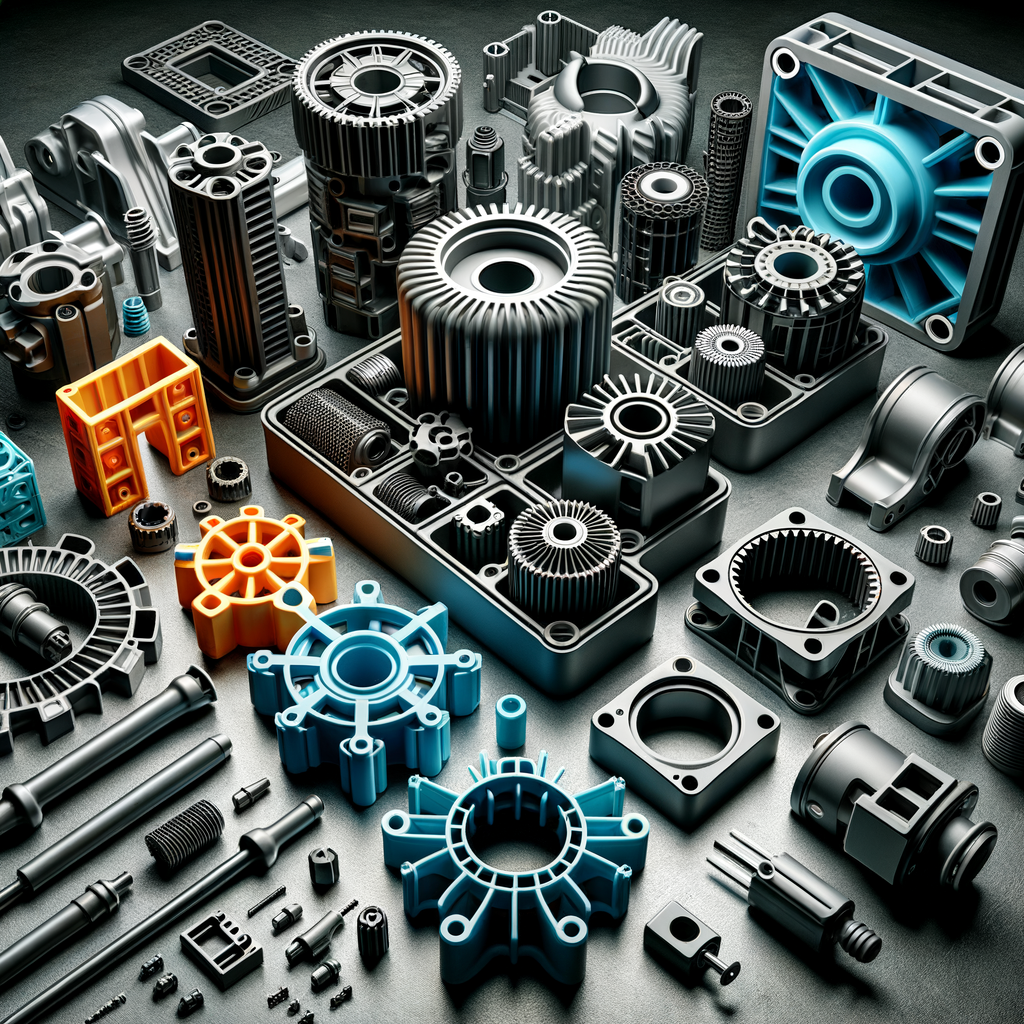
Resumen de ventajas:
- Alta resistencia mecánica y durabilidad
- Excelente resistencia al calor y a los productos químicos
- Estabilidad dimensional mejorada
- Propiedades de desgaste y fricción mejoradas
- Reducción de peso en comparación con los metales
Estas ventajas convierten a los plásticos reforzados con nailon en una elección acertada para numerosas aplicaciones, garantizando que los fabricantes puedan producir productos de alta calidad que satisfagan las demandas de sus industrias.
4. Retos y consideraciones en el moldeo de plástico reforzado con nailon
Aunque las ventajas del plástico reforzado con nailon son convincentes, hay que tener en cuenta varios retos durante el proceso de moldeo por inyección. Uno de los más importantes son las altas temperaturas de moldeo necesarias para procesar estos materiales. El control de la temperatura es crucial, ya que un calor insuficiente puede provocar una fusión incompleta y unas características de fluidez inadecuadas, mientras que un calor excesivo puede degradar el polímero o causar una contracción y deformación excesivas en el producto final. Por lo tanto, los fabricantes deben calibrar cuidadosamente sus procesos para lograr el equilibrio óptimo para cada mezcla específica reforzada con nailon.
Otra preocupación es el mayor desgaste de los moldes. La incorporación de fibras, sobre todo de vidrio y carbono, puede provocar una abrasión que acelere el desgaste de los moldes. Este desgaste requiere un mantenimiento o una sustitución más frecuentes, lo que puede aumentar significativamente los costes de producción. Para mitigar este problema, los fabricantes deben elegir materiales y diseños de moldes adecuados y, en su caso, utilizar revestimientos que mejoren la resistencia al desgaste.
La absorción de humedad es un problema bien conocido en los materiales de nailon, y el nailon reforzado no es una excepción. La capacidad del nailon para absorber la humedad puede provocar cambios en las propiedades mecánicas, afectando a la resistencia y la estabilidad dimensional. Por ejemplo, la humedad puede provocar hinchazón y deformación durante el proceso de moldeo. Para mitigar este problema, los fabricantes deben aplicar estrictos protocolos de secado antes del procesamiento para garantizar que el contenido de humedad del material se mantiene bajo.
Además, la posible deformación y contracción de las piezas moldeadas puede dificultar el logro de tolerancias estrictas. Esto puede verse agravado por el enfriamiento desigual de las piezas moldeadas, sobre todo con secciones gruesas. Los fabricantes deben optimizar los canales de refrigeración de los moldes para garantizar un enfriamiento uniforme, lo que puede ayudar a reducir la incidencia de alabeos e incoherencias dimensionales.
También pueden surgir dificultades de procesamiento, como mantener una distribución uniforme de las fibras. Si las fibras se distribuyen de forma desigual durante el proceso de inyección, pueden producirse variaciones en las propiedades mecánicas de la pieza acabada. Esto es especialmente crítico en aplicaciones que requieren gran resistencia y fiabilidad. Los fabricantes deben prestar mucha atención a los parámetros de procesamiento y considerar diseños que permitan una orientación óptima de las fibras.
Resumen de los retos:
- Se requieren altas temperaturas de moldeo
- Mayor desgaste del molde debido a la abrasividad de la fibra
- Problemas de absorción de humedad
- Posibles alabeos y contracciones en piezas moldeadas
- Dificultades de procesamiento en la distribución de fibra
Estos retos exigen que los fabricantes adopten un enfoque holístico del proceso de moldeo, integrando las mejores prácticas para mitigar los riesgos y mejorar el rendimiento de los plásticos reforzados con nailon.
5. Mejores prácticas para el moldeo por inyección de plástico reforzado con nailon
Para lograr resultados satisfactorios en el moldeo de plásticos reforzados con nailon, los fabricantes deben seguir varias prácticas recomendadas que aborden los retos mencionados anteriormente. En primer lugar, el secado del material es crucial antes del moldeo. El contenido de humedad del nailon puede afectar significativamente a la calidad de las piezas moldeadas, provocando defectos como burbujas o un mal acabado superficial. El uso de un secador desecante o de aire caliente puede reducir eficazmente los niveles de humedad. Una buena regla general es secar el nailon a temperaturas de entre 80 °C y 90 °C durante varias horas, en función del contenido inicial de humedad del material.
Optimizar el diseño del molde es otro aspecto vital del proceso de moldeo por inyección. Características como la ventilación y los canales de refrigeración adecuados pueden marcar una diferencia significativa en el resultado de las piezas moldeadas. La ventilación es esencial para permitir que los gases atrapados salgan durante el proceso de inyección, lo que puede ayudar a evitar defectos. Los canales de refrigeración deben diseñarse para garantizar una refrigeración uniforme en toda la pieza, minimizando el riesgo de alabeo y encogimiento.
Cuando se trata de parámetros de moldeo por inyección, es esencial un control cuidadoso de la temperatura, la presión y la velocidad de inyección. La temperatura de fusión de los plásticos reforzados con nailon suele oscilar entre 230 °C y 260 °C, en función de la formulación específica. Un control adecuado de la velocidad de inyección también puede ayudar a gestionar el flujo de material y minimizar la posibilidad de rotura de fibras. Una velocidad de inyección elevada puede provocar el cizallamiento de las fibras y comprometer las propiedades mecánicas del producto final.
También es crucial minimizar la rotura de fibras durante el procesamiento. La longitud y la orientación de las fibras son factores importantes que influyen en las propiedades mecánicas de las piezas moldeadas. Para evitar daños en las fibras, los fabricantes pueden optimizar los parámetros de procesamiento, garantizar una manipulación adecuada del material y considerar el uso de aditivos diseñados para mejorar la integridad de las fibras.
También hay que prestar atención al tratamiento posterior. Técnicas como el recocido pueden mejorar la estabilidad dimensional de las piezas moldeadas y aliviar las tensiones internas que puedan haberse formado durante el proceso de inyección. El mecanizado puede ser necesario para piezas que requieren tolerancias estrechas o acabados superficiales específicos. Los fabricantes deben tener en cuenta los requisitos de postprocesado durante la fase de diseño para agilizar las operaciones y garantizar que el producto final cumpla las normas de calidad.
Resumen de buenas prácticas:
- Requisitos de secado del material antes del moldeo
- Optimización del diseño de moldes para nailon reforzado
- Parámetros adecuados de moldeo por inyección
- Minimizar la rotura de fibras durante el procesado
- Consideraciones posteriores al tratamiento
El empleo de estas buenas prácticas puede mejorar el rendimiento y la fiabilidad de los productos fabricados con plásticos reforzados con nailon.
6. Aplicaciones del moldeo por inyección reforzado con nailon
Las aplicaciones del moldeo por inyección reforzado con nailon son tan diversas como las industrias que las utilizan. En el sector de la automoción, el plástico reforzado con nailon se utiliza para fabricar componentes como cubiertas de motor, soportes y engranajes. Estas piezas se benefician de las propiedades de resistencia y ligereza del material, lo que permite mejorar la eficiencia del combustible y el rendimiento. Un ejemplo notable es el uso de nailon reforzado con fibra de vidrio en aplicaciones bajo el capó, donde la resistencia al calor del material es fundamental.
La industria de la electrónica de consumo también utiliza ampliamente plásticos reforzados con nailon. Las carcasas de smartphones, tabletas y otros dispositivos suelen requerir materiales robustos que resistan el desgaste diario. Las propiedades aislantes del nailon, unidas a su resistencia mecánica, lo convierten en la opción ideal para piezas estructurales que protegen componentes delicados al tiempo que aportan un atractivo estético.
En la maquinaria industrial, componentes como rodamientos, rodillos y sistemas transportadores aprovechan la resistencia al desgaste y la solidez de los plásticos reforzados con nailon. Estas aplicaciones suelen implicar operaciones a alta velocidad en las que los materiales tradicionales pueden flaquear bajo tensión. Al emplear nailon reforzado, los fabricantes pueden desarrollar componentes más duraderos que reducen el tiempo de inactividad por mantenimiento y mejoran la eficacia operativa.
El sector aeroespacial, conocido por sus rigurosas exigencias, también confía en los plásticos reforzados con nailon. Aquí, las ventajas de ahorro de peso de estos materiales son primordiales, con aplicaciones que van desde componentes interiores a elementos estructurales. El uso de nailon reforzado con fibra de carbono en aeronaves puede suponer importantes reducciones de peso, mejorando la eficiencia del combustible y el rendimiento.
Las aplicaciones médicas son otro campo prometedor para el moldeo por inyección de nailon reforzado. Dada la necesidad de biocompatibilidad y resistencia, los materiales de nailon reforzado pueden utilizarse en diversos dispositivos, como instrumentos quirúrgicos e implantes. La capacidad de moldear con precisión geometrías complejas permite diseños innovadores que pueden cumplir estrictos requisitos normativos.
Resumen de las solicitudes:
- Componentes de automoción (cubiertas de motor, soportes, engranajes)
- Electrónica de consumo (carcasas, piezas estructurales)
- Maquinaria industrial (rodamientos, rodillos)
- Aplicaciones aeroespaciales y médicas
Estas aplicaciones ilustran la versatilidad y eficacia de los plásticos reforzados con nailon, destacando su papel vital en la mejora del rendimiento de los productos en múltiples sectores.
7. Conclusión
En resumen, moldeo por inyección con plástico reforzado con nailon presenta numerosas ventajas que no se pueden pasar por alto. Las propiedades únicas del nailon reforzado, como su alta resistencia mecánica, su excelente resistencia al calor y a los productos químicos y su mayor estabilidad dimensional, lo convierten en un material de elección para una amplia gama de industrias. A pesar de los retos asociados al procesamiento de estos materiales, como las altas temperaturas de moldeo y los problemas de absorción de humedad, la aplicación de las mejores prácticas puede conducir a resultados satisfactorios.
De cara al futuro, se espera que tendencias como el creciente énfasis en la sostenibilidad y el desarrollo de plásticos reforzados con nailon de origen biológico ganen fuerza. Es probable que los fabricantes sigan explorando formas innovadoras de optimizar el rendimiento de los materiales reforzados con nailon, garantizando que sigan siendo competitivos en un mercado cada vez más exigente.
A la hora de seleccionar el tipo adecuado de plástico reforzado con nailon para aplicaciones específicas, es esencial tener en cuenta el entorno operativo, las propiedades mecánicas requeridas y las normas reglamentarias aplicables. Evaluando cuidadosamente estos factores, los fabricantes pueden aprovechar todo el potencial de los plásticos reforzados con nailon, allanando el camino para la próxima generación de componentes ligeros, duraderos y de alto rendimiento.
Con la evolución del panorama de la ciencia de los materiales y la tecnología de fabricación, no cabe duda de que el futuro del moldeo por inyección reforzado con nailon es brillante. A medida que más industrias reconocen las ventajas de este innovador material, las posibilidades de nuevas aplicaciones y mejoras en los productos existentes son ilimitadas. Se anima a los fabricantes a participar en debates, compartir las mejores prácticas y explorar asociaciones que impulsen nuevos avances en este campo.
Dejar una respuesta
¿Quiere participar en el debate?No dude en contribuir.