No mundo acelerado do setor de saúde, a precisão, a limpeza e a conformidade vão além das palavras da moda e são requisitos inegociáveis. Uma das tecnologias subjacentes que possibilita a produção de dispositivos médicos seguros, eficazes e escalonáveis é a moldagem por injeção de plástico médico. Dando forma a seringas e cateteres, instrumentos cirúrgicos e invólucros de diagnóstico, a moldagem por injeção de plástico é importante para impulsionar a medicina moderna, criando as partes constituintes.
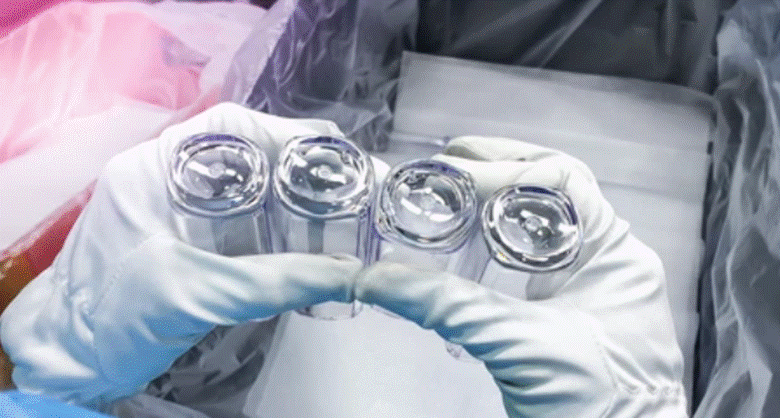
Vale a pena mencionar o fator de selecionar um fabricante confiável de moldes de injeção médica. O fornecedor certo garante que o seu produto esteja em conformidade com os padrões rigorosos do setor, opere com a máxima precisão e permaneça econômico em execuções de produção em larga escala. Essa falha pode ter impactos negativos significativos, como recalls de produtos ou violações de conformidade, ou ameaças à segurança do paciente.
Este artigo fornece uma lista dos 10 principais empresas de moldagem por injeção de plástico médico de várias partes do mundo. Os critérios de consideração das empresas listadas são muito rigorosos, começando pelas certificações, inovação, presença global e desempenho anterior. Apesar do fato de a natureza global do setor envolver participantes de muitas regiões, restringimos a escolha a apenas duas empresas chinesas, sendo a Sincere Tech uma delas, e as demais estão distribuídas nos EUA, na Europa e em Israel.
O que é moldagem por injeção de plástico médico?
É um processo de fabricação de nicho usado para produzir componentes médicos e de saúde auxiliados por plástico altamente precisos e de qualidade. Ele envolve a injeção de plástico derretido em um molde especialmente usinado e seu resfriamento até que ele se solidifique e tome sua forma final.
Principais recursos:
- Precisão e limpeza: A moldagem médica precisa estar em conformidade com tolerâncias rígidas e é levada a ambientes de sala limpa para evitar contaminação.
- Materiais biocompatíveis: Use plásticos de grau médico, como policarbonato, polipropileno e PEEK, que são seguros para uso dentro ou com o corpo humano.
- Conformidade regulatória: Os fabricantes precisam observar padrões como as normas ISO 13485, FDA e CE para garantir a segurança e a eficácia.
- Alto volume e repetibilidade: Perfeito para a produção de grandes séries de peças uniformes e estéreis, como seringas, conjuntos intravenosos, caixas de diagnóstico, artroscópios, instrumentos cirúrgicos e dispositivos de distribuição de medicamentos.
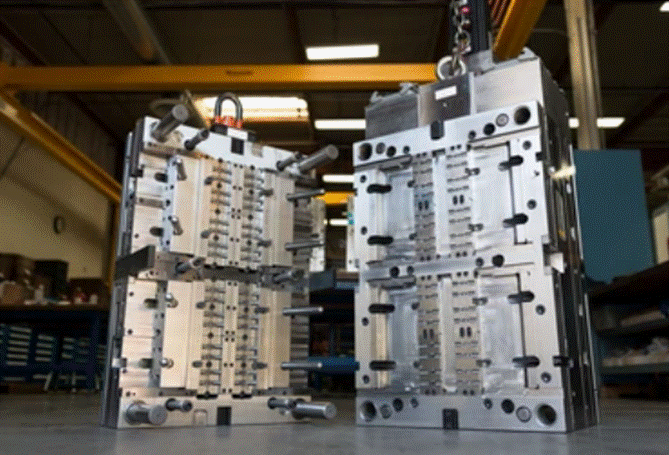
Critérios de seleção
Os critérios a seguir ajudam a decidir qual empresa foi a melhor em moldagem por injeção médica,
1. Certificação ISO 13485 e conformidade regulatória
O padrão internacionalmente aceito para os sistemas de gerenciamento de qualidade do setor de dispositivos médicos é a ISO 13485. Além disso, as empresas precisam cumprir as normas da FDA e da CE quando pretendem vender seus produtos.
2. Tecnologia avançada e recursos de sala limpa
As empresas precisam ser capazes de operar em ambientes de sala limpa (ISO Classe 7 ou superior) e usar a mais recente tecnologia de moldagem por injeção (micro moldagem e moldagem por injeção multi-shot) para atender aos padrões de higiene, contaminação, etc.
3. Foco médico e histórico do setor
A confiabilidade e a experiência na área de fabricação de componentes médicos têm um histórico sólido. As empresas que estão no setor de saúde há muito tempo também entendem melhor as exigências de regulamentação e desempenho.
4. Grande base de clientes do setor de saúde e alcance global
As empresas globais terão infraestruturas robustas de controle de qualidade, logística e regulamentação para atender melhor aos OEMs médicos multinacionais.
5. Recursos de P&D e personalização
Eles não só oferecem fabricação, mas também suporte de engenharia, projeto para fabricação (DFM), bem como parceria de inovação para dar vida a novos produtos de forma rápida e eficiente.
As 10 principais empresas de moldagem por injeção de plásticos médicos.
Esses são alguns dos líderes mundiais no setor de moldagem por injeção de plástico médico. Escolhidos com base em critérios rigorosos, como certificações de qualidade, avanço tecnológico, presença global e compromisso com a inovação, esses fabricantes têm a confiança das principais marcas de dispositivos médicos em todo o mundo. Aqui estão os 10 principais:
1. Sincere Tech (China)
Sincere Tech A Sincere Tech é um dos principais fabricantes chineses envolvidos na moldagem por injeção de plástico médico para clientes globais. Abrangendo moldagem em sala limpa, prototipagem rápida e produção em massa, a Sincere Tech é uma fonte confiável de peças médicas de alta precisão. Eles se dedicam à qualidade seguindo as normas ISO 13485, ferramentas avançadas e processos de validação rigorosos. Além disso, os OEMs médicos podem terceirizar todo o processo, inclusive o projeto do molde, a fabricação e até mesmo a montagem, tornando-o um serviço completo com várias empresas.
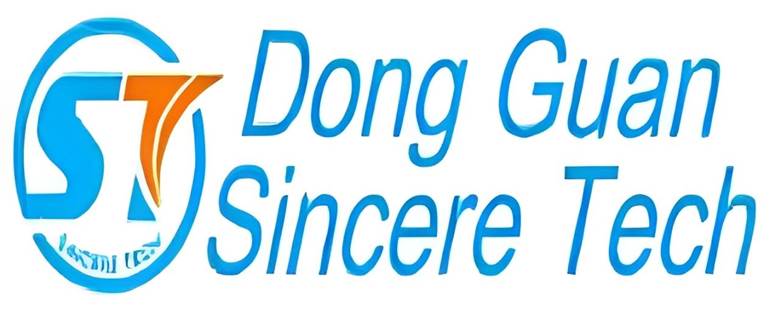
Site: https://www.plasticmold.net/
Perfil da empresa:
Há mais de 15 anos, a Sincere Tech é especializada na fabricação de moldes e peças plásticas precisas na China. Graças à sua qualificação ISO 13485 e às salas limpas de alta qualidade, a empresa oferece peças importantes para OEMs médicos globais que buscam tolerâncias rígidas. Essa empresa cobre o projeto de moldes, lida com ferramentas e realiza o processamento secundário, tudo no mesmo local. Como eles podem gerenciar o desenvolvimento de produtos desde as primeiras etapas até a produção em massa, são valiosos para a fabricação de produtos da área de saúde.
Setores atendidos:
Dispositivos médicos, automotivos, eletrônicos e embalagens.
Por que escolher o Sincere Tech?
- Nossa fábrica de moldagem de precisão de grau médico atende à rigorosa norma ISO 13485.
- Fornece todos os serviços, começando pelo design, prototipagem e terminando com a produção.
- Capacidade de moldar peças em salas limpas para produtos sem contaminação.
- São necessárias uma boa garantia de qualidade e validação.
- Oferecendo preços competitivos para clientes globais de pequeno e grande porte.
2. Phillips-Medisize (EUA)
A Phillips Medisize é uma empresa da Molex e um titã do setor na área de fornecimento integrado de medicamentos, dispositivos de diagnóstico e eletrônicos médicos. Uma moldadora de injeção médica de serviço completo, com presença global e profunda experiência em montagens complexas. Eles têm instalações de sala limpa de última geração, que oferecem serviços de projeto e prototipagem, bem como serviços automatizados de fabricação de alto volume, caso você precise. A empresa é líder em inovação de soluções para conectar a saúde digital e o rastreamento avançado de produtos.
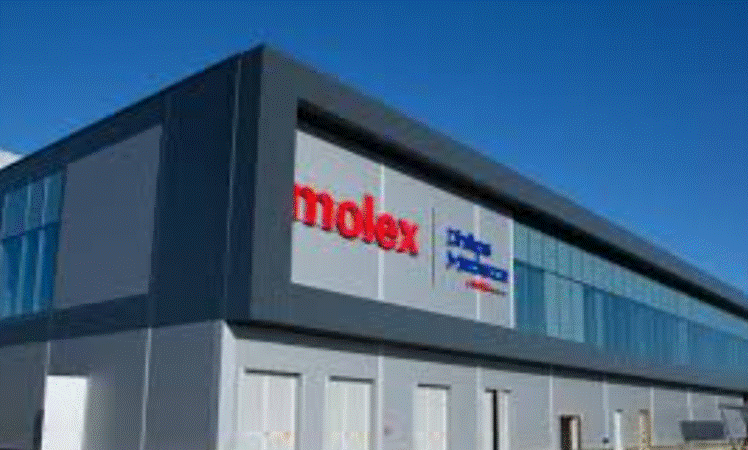
Perfil da empresa:
Operando como uma divisão da Molex, a Phillips-Medisize se concentra na fabricação de dispositivos de administração de medicamentos, diagnóstico e saúde conectada em todo o mundo. Com presença internacional nos EUA, na Europa e na Ásia, a empresa tem salas limpas de Classe 7 a Classe 8 da ISO. Eles fornecem serviços em todas as etapas, cuidando do projeto, do desenvolvimento, dos testes e da produção completa. Entre seus clientes estão algumas das principais empresas farmacêuticas e de dispositivos médicos do mundo.
Setores atendidos:
Administração de medicamentos, diagnósticos e eletrônicos médicos.
Por que escolher a Phillips-Medisize?
- Operação internacional aprimorada pela automação e mantida em ambientes de sala limpa.
- Conhecimento sobre saúde conectada e uso de tecnologia digital.
- Um histórico de cooperação bem-sucedida com as principais empresas de tecnologia médica.
- Todas as nossas operações em todo o mundo estão em conformidade com as normas ISO 13485 e FDA.
- Experiência em lidar com as necessidades de grandes projetos de fabricação.
3. Tessy Plastics (EUA)
A Tessy Plastics vem fornecendo moldagem por injeção de plástico de alta precisão para o setor médico há décadas e é conhecida por sua certificação ISO 13485. Eles têm todos os produtos internamente, desde ferramentas até tudo, da automação à validação. Totalmente dependentes da área médica, eles produzem uma grande variedade de dispositivos médicos cirúrgicos, de diagnóstico e vestíveis que trabalham em estreita colaboração com clientes e parceiros para garantir maior confiabilidade, facilidade de escalabilidade e conformidade com as regulamentações globais. Eles também possuem recursos para micro moldar e inserir moldes para componentes delicados.
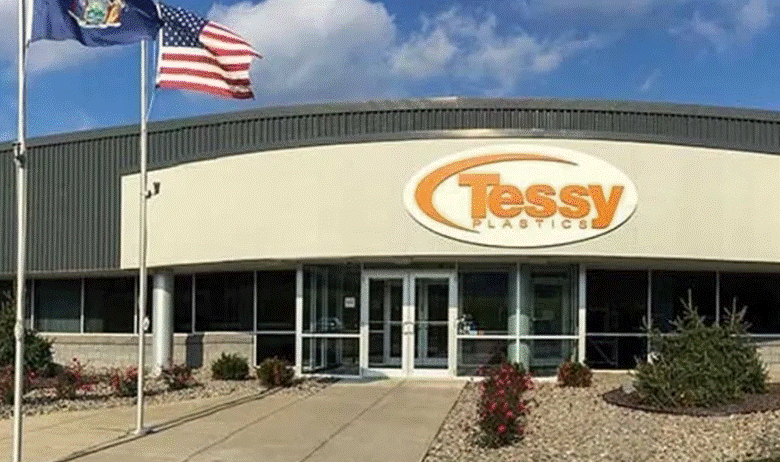
Perfil da empresa:
Desde 1976, a Tessy Plastics opera em Nova York, EUA, como uma empresa familiar na área de moldagem por injeção de precisão. O setor médico da Bosch enfatiza os dispositivos cirúrgicos, de diagnóstico e vestíveis, todos fabricados de acordo com rigorosos padrões de qualidade. A Tessy combina automação, ferramentas avançadas e processos de montagem em seu trabalho. A equipe de engenharia da empresa coopera com os clientes para resolver problemas de design, regulamentos e lançamento rápido.
Setores atendidos:
Produtos médicos, eletrônicos e bens de consumo.
Por que escolher a Tessy?
- Todas as etapas, desde o design até a venda, estão sob uma única autoridade.
- Oferece micro-moldagem e moldagem por inserção como seus principais pontos fortes.
- Mais de 40 anos de fabricação de dispositivos médicos.
- A empresa possui áreas de sala limpa ISO Classe 7.
- A empresa tem certificação ISO 13485 e visa atender a todos os requisitos para dispositivos médicos.
4. Gerresheimer (Alemanha)
A Gerresheimer é líder global em embalagens médicas e farmacêuticas, com uma importante divisão de moldagem por injeção de plástico, capaz de fabricar sistemas de administração de medicamentos, dispositivos de diagnóstico moldados por injeção e seringas pré-cheias. Ela mantém várias instalações de fabricação em salas limpas e opera de acordo com os mais altos padrões regulatórios. Devido à sua integração vertical do projeto do produto à fabricação do molde e, por fim, à montagem final, ela é a parceira preferida das empresas farmacêuticas em todo o mundo.
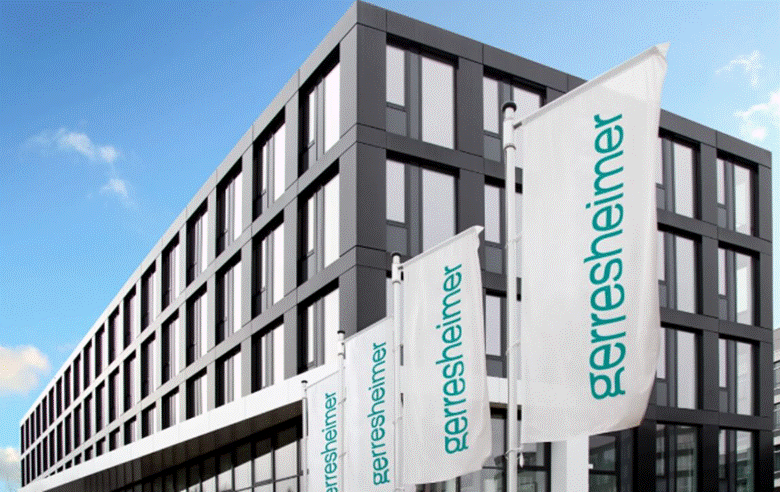
Perfil da empresa:
As empresas de embalagens médicas e farmacêuticas reconhecem amplamente a Gerresheimer e seu longo histórico de moldagem por injeção. As operações globais da empresa incluem mais de 30 unidades, oferecendo aos clientes produtos que variam de canetas de insulina a inaladores e kits de diagnóstico. A empresa é forte porque cobre toda a gama de serviços, desde o projeto até a criação da embalagem final. Graças à sua infraestrutura avançada, ela pode produzir dispositivos médicos de grande porte que atendem a várias regulamentações.
Setores atendidos:
Produtos farmacêuticos, saúde e diagnósticos.
Por que escolher a Gerresheimer?
- Soluções de fabricação que incluem um sistema completo.
- Existem instalações com certificação de sala limpa em diferentes locais do mundo.
- Novos desenvolvimentos em embalagens e dispositivos.
- Muitas das principais organizações farmacêuticas confiam em nós.
- Seguir todas as normas médicas da UE e dos EUA.
5. Nypro Healthcare (Jabil - EUA)
A Nypro Healthcare faz parte da Jabil e oferece soluções de moldagem por injeção de plástico médico de alto volume para mercados de alta complexidade e altamente regulamentados. Com seus recursos de automação e suporte de engenharia, a Nypro tem instalações de fabricação em todo o mundo. A empresa se concentra em aplicações médicas sofisticadas, como fornecimento de medicamentos injetáveis, sistemas de diagnóstico e ferramentas cirúrgicas minimamente invasivas. A Nypro trabalha com os clientes em um modelo de parceria, certificando-se de fornecer P&D, prototipagem e fabricação.
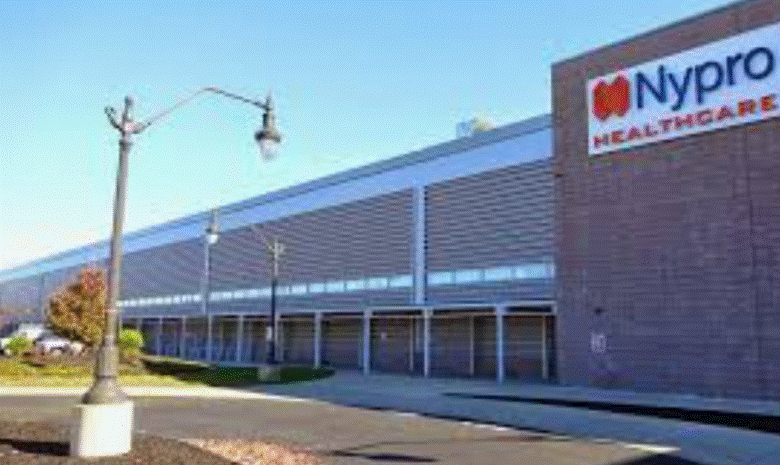
Perfil da empresa:
A Nypro, que pertence à Jabil Healthcare, fornece serviços completos de CDMO e moldagem por injeção para dispositivos médicos. Em cinco regiões do mundo, a Nypro fornece produção de alto volume para as áreas de cirurgia, diagnóstico e administração de medicamentos. Graças à sua habilidade em automação, cumprimento de normas e redução de tamanho, os clientes podem vencer a concorrência. Eles também trabalham na engenharia desde o início, escolhem materiais importantes e constroem protótipos.
Setores atendidos:
Fornecimento de medicamentos, diagnósticos e sistemas cirúrgicos.
Por que escolher Nypro?
- Instalações de fabricação operando em vários países com a capacidade de aumentar a produção.
- Ter conhecimento detalhado das regras dos mercados regulamentados.
- Melhor automação e montagem trazem vantagens para os fabricantes de automóveis.
- Trabalho em equipe inicial entre P&D e design inicial.
- Fornecedor líder na fabricação de dispositivos médicos de alto risco.
6. Röchling Medical (Alemanha)
A Röchling Medical, uma parte do Grupo Röchling, oferece soluções completas de moldagem por injeção para clientes que apoiam os setores farmacêutico, de diagnóstico e de dispositivos médicos. Elas estão disponíveis globalmente na Europa, nos EUA e na China. As competências da Röchling incluem engenharia e conformidade regulatória, moldagem em sala limpa. Seu portfólio abrange tudo, desde componentes lab-on-chip até carcaças de dispositivos cirúrgicos personalizados, muitas vezes produzidos em ambientes Classe 7 totalmente validados.
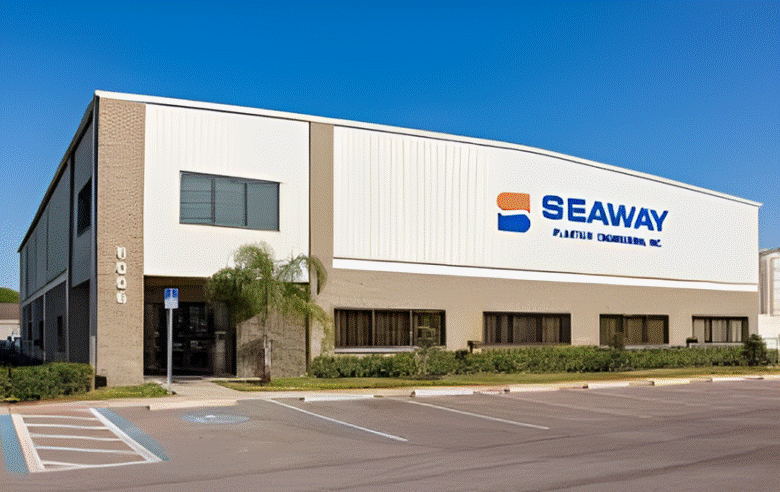
Perfil da empresa:
A Röchling Medical opera como parte do Grupo Röchling, ajudando os setores farmacêutico, de diagnóstico e de tecnologia médica em todo o mundo. Moldagem em sala limpa, lab-on-chip e alojamento de dispositivos são áreas em que se especializam, com fabricação na Alemanha, nos EUA e na China. A Röchling tem assistência técnica, funções regulatórias e suporte completo para o gerenciamento de produtos do início ao fim. Os sistemas de fabricação nessas instalações suportam tanto produções limitadas quanto grandes.
Setores atendidos:
Diagnósticos, produtos farmacêuticos e instrumentos cirúrgicos.
Por que escolher?
- As empresas estão operando em vários países da Europa, China e Estados Unidos.
- Estão disponíveis amplos serviços de fabricação em sala limpa.
- Ter trabalhado em ambientes de moldagem de Classe 7 e Classe 8.
- Fornecimento de ajuda de engenharia para os seguintes regulamentos.
- Temos as habilidades necessárias para desenvolver componentes personalizados para uso médico.
7. Seaway Plastics Engineering (EUA)
A Seaway Plastics, especializada em produção de baixo a médio volume, é uma parceira confiável para OEMs da área médica que precisam de um retorno rápido e suporte flexível. Seus serviços incluem moldagem por injeção em sala limpa, ferramental interno e serviços de montagem. A Seaway tem fama especial no segmento de dispositivos ortopédicos e cirúrgicos. A empresa também fornece protocolos de validação de IQ/OQ/PQ, deixando claro que seus produtos são altamente regulamentados.
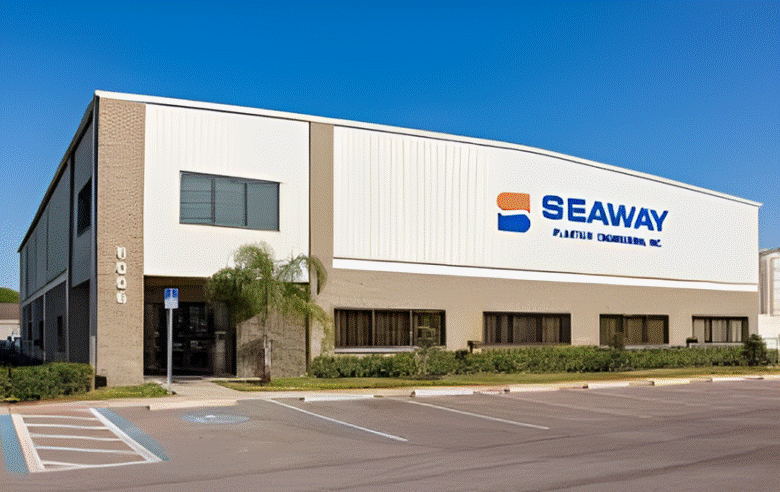
Perfil da empresa:
A Seaway Plastics oferece principalmente moldagem por injeção de baixo a médio volume para empresas de dispositivos médicos. As instalações em salas limpas ISO Classe 7 permitem a fabricação de moldes, bem como a validação e a montagem de produtos finais. A Seaway deixa sua marca principalmente com instrumentação ortopédica e cirúrgica. Devido a seus rápidos tempos de produção, as pessoas procuram essas empresas para projetos de amostra e de pequena escala.
Setores atendidos:
Ortopedia, ferramentas cirúrgicas e diagnósticos.
Por que escolher?
- Oferecemos prototipagem rápida e baixo número de amostras.
- Oferecemos o desenvolvimento e o suporte de nossas próprias ferramentas automatizadas e de teste.
- Você pode confiar que nossas instalações são certificadas pela ISO 13485 e regulamentadas pela FDA.
- A moldagem especial para componentes sensíveis é possível em salas limpas.
- Oferece total flexibilidade ao cliente.
8. MedPlast (atualmente Viant - EUA)
Essa empresa agora é conhecida como Viant e é uma potência na fabricação de dispositivos médicos. Ela realiza atividades de fabricação por contrato, incluindo moldagem por injeção de plástico, extrusão, montagem, embalagem e esterilização. Suas habilidades em moldagem vão além de dispositivos implantáveis, kits de diagnóstico e sistemas de administração de medicamentos. A ênfase da Viant em design para manufaturabilidade (DFM) e intenso controle de qualidade a torna um fornecedor ideal para aplicações médicas de alto risco.
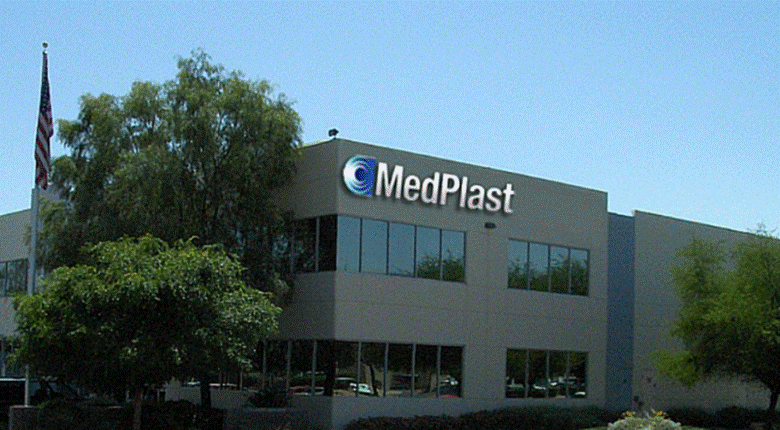
Perfil da empresa:
A empresa opera sob a marca Viant, oferecendo uma variedade de processos de fabricação de dispositivos médicos, por exemplo, moldagem por injeção e esterilização. Seus negócios se estendem aos mercados de ortopedia, diagnóstico e dispositivos de uso único. Graças às habilidades de DFM da Viant e aos recursos regulatórios internos, as soluções são criadas para serem seguras e escalonáveis. Há mais de 25 instalações da Vifor Pharma espalhadas pelo mundo, onde eles aplicam seu know-how regulatório.
Setores atendidos:
Dispositivos implantáveis, diagnósticos e sistemas cirúrgicos.
Por que escolher?
- Oferece serviços de design para fabricação, moldagem e esterilização.
- Experiência comprovada na prestação de cuidados para problemas médicos difíceis de tratar.
- Projetado para o mundo, produzido para o mundo.
- Você pode alterar seu pedido conforme necessário e todos os produtos são controlados quanto à qualidade.
- Todas as nossas instalações têm certificação ISO 13485 e FDA.
9. Technoplast (Israel)
A Technoplast é uma empresa emergente no setor de moldagem de plástico médico de precisão, com sede em Israel. Entre os produtos que oferece estão o design de produtos, a prototipagem rápida e a produção em massa, com grande foco em componentes médicos personalizados. Entre seus clientes estão fabricantes multinacionais de dispositivos médicos, e a empresa é conhecida por sua velocidade de lançamento no mercado, pois suas operações são muito ágeis e conta com um sólido departamento de P&D. A Technoplast é excepcionalmente forte (cardiologia, diagnósticos, dispositivos descartáveis).
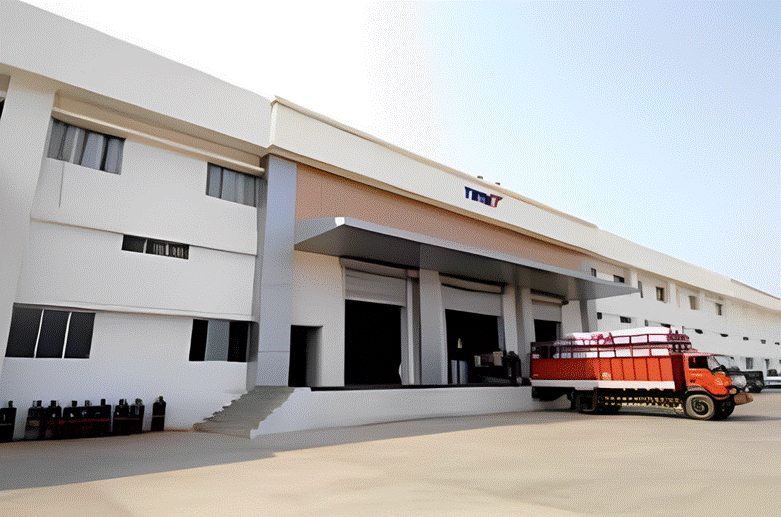
Perfil da empresa:
A Technoplast é uma empresa israelense que fornece moldagem avançada de plástico para uso em dispositivos médicos. As empresas fornecem ajuda para projetar produtos, criar protótipos, fabricar moldes e produzir itens em grande escala. A Technoplast é reconhecida por ser flexível, fazer P&D eficaz e ter experiência na fabricação de produtos para cardiologia, diagnósticos e descartáveis de uso único. A entrega rápida e os baixos custos de fabricação são as principais prioridades da empresa.
Setores atendidos:
Cardiologia, diagnósticos e dispositivos descartáveis.
Por que escolher a Technoplast?
- Melhoria do resultado por meio de ações ágeis e prototipagem rápida.
- Fabricação de moldes de alta precisão para peças médicas detalhadas.
- Realização de P&D inovador para uso médico.
- Altas taxas de colocação de produtos no mercado.
- A certificação ISO 13485 está associada a produtos em conformidade com a CE e a FDA.
10. TK Mold (China)
A TK Mold, a segunda e última empresa chinesa desta lista, é conhecida pelos serviços de moldagem por injeção e ferramental de alta precisão. Eles lidam com moldes e componentes de grau médico, exportando produtos para a América do Norte, Europa e outros mercados asiáticos. Seus pontos fortes são o projeto de engenharia e a capacidade de dar vida a essas ideias por meio da fabricação de moldes e da produção de pequenos e médios volumes. A TK Mold possui um documento ISO certificado e segue os padrões médicos internacionais. Portanto, é uma boa empresa para terceirizar o trabalho de produção.
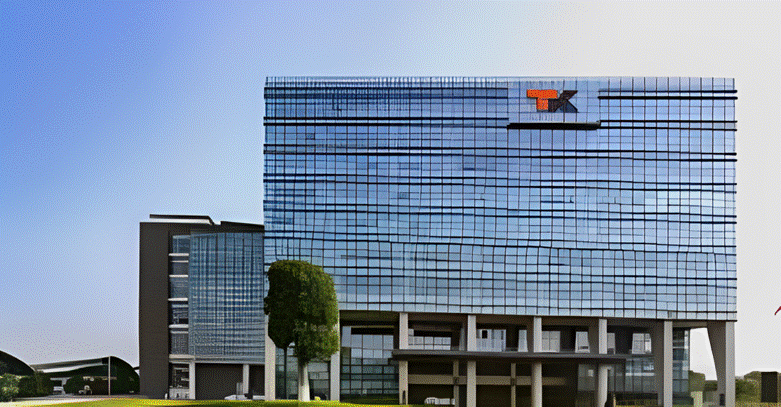
Perfil da empresa
A TK Mold é bem conhecida na China por seus moldes de injeção de alta qualidade e peças para dispositivos médicos. Seus clientes na América do Norte, Europa e Ásia recebem moldes de sala limpa para aplicações de Classe 7. O molde recebe suporte desde seu projeto original até a fabricação de lotes médios e etapas de pós-produção. Por ter a certificação ISO 13485 e atender aos padrões internacionais, a empresa conquistou a confiança de um parceiro offshore.
Setores atendidos
Médico, eletrônico e automotivo.
Por que escolher?
- Apenas um pequeno número de moldes projetados profissionalmente é usado para a produção.
- Prestar atenção especial à inovação em engenharia.
- Com certificação ISO e de acordo com as diretrizes médicas.
- Fornecer conhecimento especializado para a UE, os EUA e a Ásia.
- Métodos econômicos para trabalhar com OEMs.
Perspectivas futuras para empresas de moldagem por injeção de plásticos médicos.
Com o desenvolvimento do setor de saúde, espera-se que as empresas de moldagem por injeção médica se desenvolvam em vários aspectos essenciais. Veja a seguir o que o futuro nos reserva:
1. Adoção de materiais inteligentes
- As empresas estão investindo em materiais como polímeros antimicrobianos, biodegradáveis ou biorreabsorvíveis que oferecem funcionalidade aprimorada.
- Esses suprimentos permitem o uso de dispositivos médicos de uso único mais seguros e sustentáveis.
2. Expansão para microfluídica e miniaturização
- Cada vez mais, as empresas de processamento são forçadas a criar peças ultrapequenas e complexas para lab-on-a-chip, sensores vestíveis e dispositivos de diagnóstico.
- A capacidade de micromoldagem será necessária para manter a competitividade.
3. Integração de automação e indústria 4.0
- No entanto, a automação avançada e a análise de dados em tempo real permitirão que as empresas aprimorem a eficiência de seus processos, a rastreabilidade e o controle de qualidade.
- As fábricas inteligentes com sistemas conectados minimizarão o erro humano e a produtividade aumentará.
4. Personalização e fabricação sob demanda
- Há uma demanda crescente por dispositivos médicos personalizados, por isso as empresas estão adotando um modo de produção flexível e em lote.
- A prototipagem rápida e a manufatura aditiva podem aprimorar os processos tradicionais de moldagem.
5. Sustentabilidade e conformidade ambiental
- Os decretos mundiais estão forçando as empresas a reciclar, reduzir o desperdício e o consumo de energia e diminuir o uso de plásticos não recicláveis.
- Os fabricantes estão adotando as iniciativas e práticas ecológicas da economia circular.
6. Aumento do escrutínio regulatório
- Com o advento de materiais e tecnologias novos e inovadores, as empresas podem esperar protocolos mais rigorosos de validação, rastreabilidade e conformidade.
- Será necessário investir na especialização em burocracia para manter o acesso ao mercado.
7. Parcerias estratégicas com empresas de tecnologia médica
- As empresas estão estabelecendo colaborações mais estreitas com OEMs médicos para co-inovar as soluções inovadoras sensíveis à PI.
- Envolver o projeto em estágio inicial se tornará uma vantagem competitiva.
Conclusão
É importante selecionar o melhor fabricante de moldagem por injeção de plástico médico para garantir que seu dispositivo médico seja bem-sucedido em termos de segurança, produção em escala e toda a conformidade. Esta lista é composta pelas empresas de elite do mundo, não apenas em termos de cumprimento dos requisitos técnicos e regulatórios do setor médico, mas também de soluções inovadoras e orientadas para o cliente.
Desde os gigantes do mundo, como a Phillips-Medisize e a Gerresheimer, até as empresas de nicho, como a Sincere Tech e a Technoplast, cada uma delas tem certa experiência e capacidade comprovadas no campo da saúde. Independentemente de você estar desenvolvendo uma nova ferramenta de diagnóstico ou expandindo a produção de uma peça de maquinário já estabelecida, a colaboração com qualquer um desses confiáveis fornecedores de moldagem por injeção médica o coloca na vanguarda das especificações de qualidade e da corrida competitiva.
Os fornecedores respeitáveis de moldagem por injeção médica garantem a permanência na vanguarda em termos de padrões de qualidade e competitividade no mercado.
Perguntas frequentes
1. O que é a moldagem por injeção de plástico médico?
É um processo de manufatura que fabrica peças plásticas de alta precisão para o ambiente de aplicações médicas com equipamentos e materiais especiais dentro de altos padrões regulatórios.
2. Por que a certificação ISO 13485 é importante para as empresas de moldagem médica?
Ele garante que a empresa esteja em conformidade com os padrões internacionalmente aceitos de sistemas de gerenciamento de qualidade do setor de dispositivos médicos, que é a chave para a conformidade regulatória e a segurança do produto.
3. Quais materiais são normalmente empregados na moldagem por injeção médica?
Os materiais comuns incluem policarbonato de grau médico, polipropileno, polietileno e elastômeros termoplásticos, que devem ser materiais biocompatíveis e esterilizáveis.
4. Qual é o efeito das salas limpas na moldagem por injeção médica?
As salas limpas são um ambiente livre de contaminação, vital para a produção de componentes médicos estéreis/sensíveis, pois minimizam as chances de contaminação por partículas.
5. É possível para as pequenas empresas igualar a produção que os grandes fabricantes produzem aqui?
Sim. Várias pequenas empresas oferecem serviços de especialização de nicho, desenvolvimento ágil e prototipagem rápida que são, de fato, bons parceiros para trabalhos especializados ou personalizados.