Qué es un molde de inyección de plástico
¿Qué es el molde de inyección de plástico?
Moldeo por inyección de plástico es uno de los métodos más eficaces para fabricar componentes de plástico, ya que ofrece altos niveles de precisión y eficiencia de producción. El proceso consiste en fundir materiales plásticos e inyectarlos en un molde prediseñado que da al plástico una forma específica mientras se enfría. Este artículo profundiza en los aspectos esenciales de los moldes de inyección de plástico, detallando los tipos, componentes, procesos de fabricación y consideraciones para seleccionar el molde adecuado a las necesidades específicas de producción.
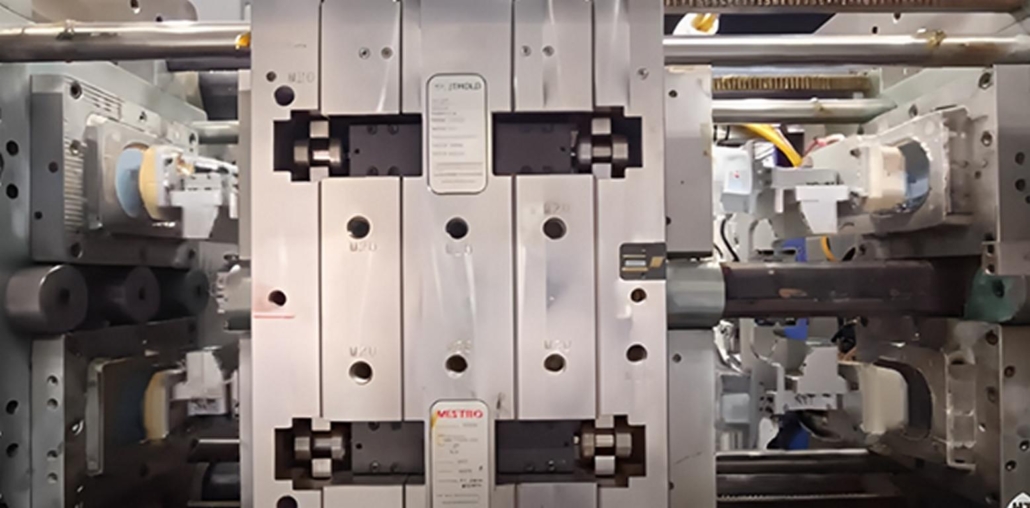
Introducción al moldeo por inyección de plásticos
Moldeo por inyección de plástico es una técnica utilizada para crear piezas de plástico complejas y precisas en grandes cantidades. Desde su desarrollo a finales del siglo XIX, el proceso ha transformado la industria manufacturera, permitiendo la producción a alta velocidad de piezas en una amplia gama de sectores, como la automoción, la electrónica, los dispositivos médicos y los bienes de consumo.
Ventajas del moldeo por inyección de plásticos
- Alta eficiencia y velocidad: El moldeo por inyección ofrece un ciclo de producción corto, lo que permite un ritmo de producción rápido. Varios moldes pueden funcionar simultáneamente para aumentar aún más la producción.
- Repetibilidad: El proceso está diseñado para crear piezas idénticas en múltiples series de producción, lo que resulta especialmente valioso en industrias que requieren gran precisión y uniformidad.
- Capacidades de diseño complejo: Los moldes de inyección son capaces de crear geometrías complejas, como paredes finas, muescas y detalles superficiales complejos.
- Flexibilidad del material: El moldeo por inyección puede utilizar una amplia variedad de termoplásticos y plásticos termoestables, cada uno de ellos elegido para proporcionar propiedades específicas al producto acabado.
- Residuos mínimos: Con moldes correctamente diseñados y controles de proceso avanzados, el moldeo por inyección produce poco o ningún desperdicio de material.
Visión general de los moldes de inyección de plástico
A molde de inyección de plástico es una herramienta compleja diseñada para dar forma al material plástico fundido y convertirlo en un producto acabado. El molde suele ser de acero o aluminio y se compone de dos mitades principales: la cavidad y el núcleo, cada una responsable de formar el exterior y el interior de la pieza final. Debido a las altas presiones que se ejercen en el moldeo por inyección, estos moldes deben ser robustos, resistentes al desgaste y capaces de mantener su forma en ciclos repetidos.
Cada molde incluye múltiples piezas que funcionan al unísono para garantizar la precisión en la formación, refrigeración y expulsión de la pieza. A continuación se desglosan los componentes clave de un molde de inyección y sus respectivas funciones.
Componentes clave del molde
- Cavidad y núcleo del molde de inyección: Son los elementos principales del molde. El lado de la cavidad (normalmente el lado "A") es responsable de dar forma a la superficie exterior de la pieza, mientras que el lado del núcleo (el lado "B") da forma al interior. Juntos forman el espacio hueco que define la geometría de la pieza. La elección de los materiales de la cavidad y el núcleo depende del volumen de producción, ya que los materiales de alto desgaste, como el acero endurecido, suelen utilizarse para la producción de grandes volúmenes, mientras que los metales más blandos pueden bastar para tiradas menores.
- Deslizadores y elevadores: Deslizadores y elevadores permiten crear socavados o geometrías complejas que no pueden formarse con un molde sencillo de dos piezas. Las correderas se mueven lateralmente cuando se abre el molde, creando espacio para cualquier saliente o ranura, mientras que los elevadores se mueven en ángulo para liberar la pieza. Ambos permiten expulsar piezas de formas complejas sin dañarlas.
- Sistemas de bebederos, canales y compuertas: La bebedero canaliza el plástico fundido desde la boquilla de la máquina de inyección hasta el molde, conduciéndolo a la corredor sistema que dirige el plástico a cada cavidad de un molde multicavidades. Puertas son los puntos finales de entrada del plástico fundido en la cavidad, donde se enfría y toma forma. Cada componente de este sistema afecta a la uniformidad y rapidez con que el material llena el molde, lo que influye en la calidad de la pieza y el tiempo de ciclo.
- Sistema eyector: Después de que la pieza moldeada se haya enfriado y solidificado, el sistema eyector empuja la pieza fuera de la cavidad del molde. El sistema de expulsión suele incluir pasadores o placas que aplican fuerza a la pieza desde el lado del núcleo, lo que garantiza que se libere sin sufrir daños. Este sistema debe programarse y controlarse con precisión para evitar que la pieza se deforme o se pegue.
- Canales de refrigeración: Canales de refrigeración son conductos dentro de las placas del molde que transportan refrigerante, normalmente agua, para absorber y disipar el calor del plástico fundido. Una refrigeración eficaz es crucial para el proceso de moldeo, ya que reduce el tiempo de ciclo y afecta a la precisión dimensional y las propiedades mecánicas de la pieza. El diseño de los canales de refrigeración, ya sean canales conformados, deflectores o de burbujeo, puede influir significativamente en el rendimiento y la eficacia del molde.
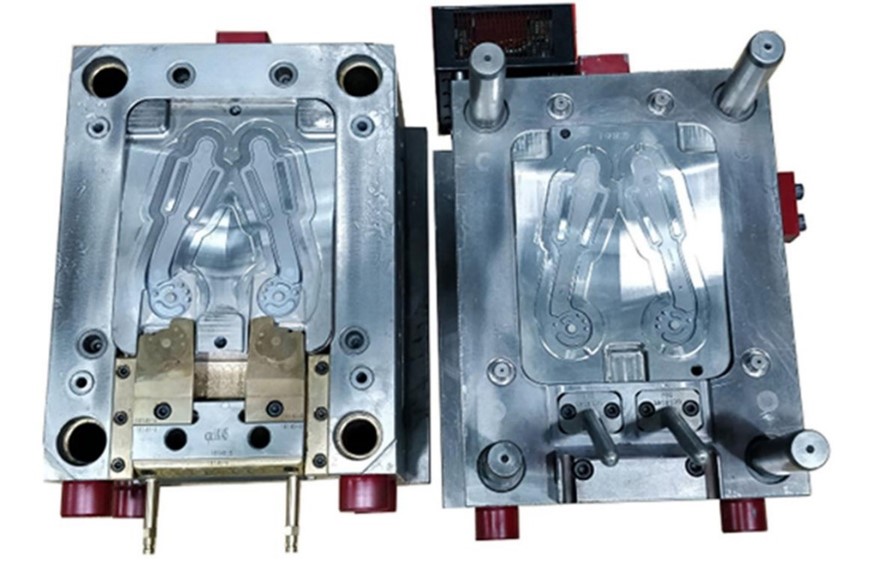
Estructura de un molde de inyección de plástico
La estructura de un molde de inyección de plástico está diseñada para soportar las presiones, temperaturas y tensiones mecánicas de los repetidos ciclos de moldeo. A continuación se describen los componentes estructurales y su funcionamiento en el proceso de moldeo:
- Placas A y B: Son las placas principales del molde que sujetan la cavidad y el núcleo, respectivamente. La placa A es fija, mientras que la placa B se mueve para abrir y cerrar el molde. Estas placas están diseñadas para mantener la alineación y soportar las presiones de la inyección.
- Placas de sujeción: Estas placas fijan el molde dentro de la unidad de cierre de la máquina de moldeo por inyección. Su diseño debe garantizar la estabilidad durante la fase de inyección a alta presión para evitar desalineaciones o movimientos que puedan causar defectos.
- Línea de separación: La línea de partición es el punto de unión de las placas A y B. Una línea de apertura bien alineada es esencial para evitar defectos como las rebabas (finas capas de plástico en las costuras del molde) y garantizar un desmoldeo suave de la pieza. La ubicación de la línea de apertura suele depender del diseño de la pieza y de los requisitos del molde.
- Canales de refrigeración: Los canales de refrigeración son esenciales para mantener el rendimiento del molde y reducir los tiempos de ciclo. Los canales se diseñan cuidadosamente para garantizar un enfriamiento uniforme en toda la cavidad y el núcleo del molde, lo que es fundamental para evitar defectos como alabeos o tensiones internas. Los tipos de canales de refrigeración incluyen:
- Refrigeración conforme: Canales que siguen el contorno de la pieza, proporcionando una refrigeración uniforme que se adapta a la forma de la cavidad del molde.
- Refrigeración por deflectores: Utiliza insertos para guiar el flujo de refrigerante y se suele emplear cuando el tamaño del molde limita la colocación de canales.
- Refrigeración por burbujeo: Los tubos de burbujeo crean una refrigeración adicional en zonas específicas, especialmente para secciones gruesas que requieren una refrigeración más rápida.
- Pasadores de refrigeración: Los pasadores incrustados en el núcleo proporcionan una refrigeración localizada en secciones gruesas, lo que ayuda a gestionar la distribución de la temperatura en moldes más grandes o con varias cavidades.
El diseño de la refrigeración influye enormemente en la duración del ciclo y, por extensión, en el coste y la productividad del proceso de moldeo por inyección.
Tipos de moldes de inyección de plástico
Existen varios tipos de moldes de inyección de plástico para adaptarse a las distintas necesidades de producción, complejidades y requisitos de las piezas. Estos son algunos de los tipos más utilizados:
- Moldes de cavidad única: Estos moldes producen una pieza por ciclo. Suelen utilizarse para volúmenes de producción más pequeños o piezas de alta precisión en las que es necesario un control más estricto de cada pieza. Los moldes de cavidad única tienen la ventaja de una configuración más sencilla y son más rentables para una producción limitada.
- Moldes multicavidad: En los moldes multicavidad, varias cavidades idénticas permiten producir varias piezas en un solo ciclo. Esto aumenta la eficiencia y es ideal para la producción de grandes volúmenes, reduciendo el tiempo de ciclo por pieza y los costes generales. Sin embargo, los moldes multicavidad son más complejos de diseñar y requieren un equilibrio preciso en el sistema de canales para garantizar un llenado uniforme.
- Moldes familiares: Los moldes familiares contienen diferentes cavidades dentro de un único molde, lo que permite la producción de varios componentes en un solo ciclo. Esto resulta especialmente útil cuando es necesario moldear piezas diferentes juntas, como en el caso de los ensamblajes. Sin embargo, equilibrar la tasa de llenado entre piezas de distintos tamaños puede resultar complicado y provocar defectos si no se controla con cuidado.
- Moldes de canal caliente frente a moldes de canal frío:
- Moldes de canal caliente: Utilizan componentes calentados para mantener el plástico fundido dentro del sistema de canalización, lo que minimiza los residuos y acelera el ciclo. Los canales calientes son eficientes para la producción de grandes volúmenes, pero requieren un control cuidadoso y costes iniciales más elevados.
- Moldes de canal frío: Deje que el plástico del canal se enfríe y solidifique con cada ciclo. El canal solidificado se expulsa normalmente con la pieza, cuya extracción puede requerir un proceso secundario. Los moldes de canal frío son más sencillos y menos costosos, por lo que resultan adecuados para producciones de menor volumen.
- Moldes de dos placas frente a moldes de tres placas:
- Moldes de dos placas: Constan de una sola línea de apertura y su diseño es más sencillo. Suelen utilizarse para piezas sencillas con requisitos de una sola puerta.
- Moldes de tres placas: Incluye una placa adicional, creando dos líneas de separación. Esto permite sistemas de separación más complejos, como la separación central, que mejora la estética de la pieza y puede reducir el procesamiento posterior al moldeo.
- Moldes apilables y rotativos:
- Moldes apilables: Los moldes apilados utilizan varios niveles de cavidades, lo que duplica o triplica la capacidad de producción sin aumentar los requisitos de fuerza de cierre de la máquina. Son ventajosos para la producción de grandes volúmenes, pero requieren maquinaria y manipulación avanzadas.
- Moldes rotativos: Los moldes rotativos permiten el sobremoldeo y el ensamblaje en molde mediante la rotación de cavidades entre estaciones. Suelen utilizarse para piezas multimaterial, como las que requieren una combinación de plásticos rígidos y flexibles.
Cada tipo de molde presenta ventajas y retos distintos, y la selección del adecuado depende de factores como el volumen de producción, la complejidad de la pieza y los requisitos de material.

Proceso de moldeo por inyección de plástico
El proceso de moldeo por inyección consta de varios pasos clave, cada uno de ellos fundamental para producir piezas de alta calidad. He aquí un desglose detallado:
- Sujeción: El molde se sujeta firmemente para prepararlo para la inyección de plástico fundido. La fuerza de cierre se calcula en función de la presión de la cavidad para garantizar que no haya fugas de plástico a través de la línea de apertura.
- Inyección: El plástico fundido se inyecta en la cavidad del molde a través del bebedero, el canal y la compuerta. La velocidad de inyección, la presión y la temperatura deben controlarse con precisión, ya que afectan al flujo y la calidad del material en la cavidad.
- Refrigeración: El enfriamiento comienza en cuanto el plástico entra en el molde. La velocidad de enfriamiento debe ser uniforme para evitar defectos, como alabeos o contracciones. Los canales de enfriamiento desempeñan aquí un papel vital, ya que garantizan que el calor se disipe eficazmente del molde. Esta etapa suele representar la mayor parte de la duración del ciclo.
- Expulsión: Una vez que la pieza se ha solidificado, los pasadores o placas eyectoras empujan la pieza fuera del molde. La expulsión debe realizarse con cuidado para evitar dañar la pieza, especialmente si tiene características complejas o está hecha de un material quebradizo.
Cada etapa del proceso de moldeo por inyección requiere un control preciso para producir piezas que cumplan las normas de calidad y, al mismo tiempo, minimizar el tiempo de ciclo y los costes de producción.
Canales de refrigeración de moldes de inyección
Los canales de refrigeración son cruciales en el proceso de moldeo por inyección de plástico, ya que influyen significativamente en el tiempo de ciclo, la calidad de las piezas y la eficacia de la producción. Un diseño de refrigeración adecuado es esencial para evitar defectos como el alabeo, la contracción o las tensiones internas que pueden producirse si el enfriamiento es desigual o demasiado rápido.
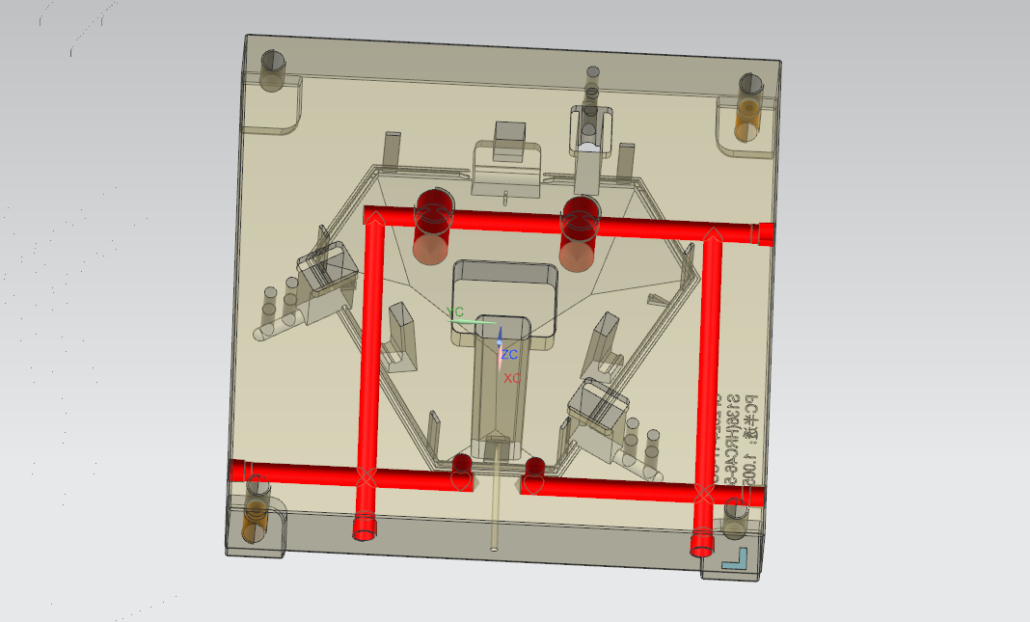
Tipos de canales de refrigeración en moldes de inyección
- Refrigeración conforme: Esta técnica avanzada consiste en diseñar canales de refrigeración que sigan el contorno de la pieza dentro del molde. La refrigeración conformada proporciona una refrigeración uniforme en toda la superficie de la pieza, lo que reduce el tiempo de ciclo y mejora la calidad de la pieza. La refrigeración conformada, que suele conseguirse mediante impresión 3D y otros métodos de fabricación avanzados, es ideal para formas complejas en las que los canales tradicionales resultarían ineficaces.
- Canales rectos de refrigeración: Estos canales son simples trayectorias rectas perforadas en las placas del molde. Aunque son sencillos y rentables, son menos eficaces que la refrigeración conforme en geometrías de molde complejas. Los canales rectos suelen utilizarse en moldes estándar en los que es más fácil conseguir una refrigeración uniforme.
- Refrigeración por deflectores: Los deflectores son insertos planos que redirigen el flujo de refrigerante dentro del molde, especialmente en espacios reducidos donde no llegan los canales rectos. La refrigeración por deflectores es eficaz para controlar la temperatura en moldes pequeños o zonas específicas, pero puede no proporcionar la refrigeración uniforme necesaria para diseños muy complejos.
- Refrigeración por burbujeo: Los burbujeadores son tubos que hacen circular el refrigerante dentro de zonas pequeñas y confinadas del molde, especialmente beneficiosos para secciones gruesas de una pieza que requieren una refrigeración más rápida. Los bubblers son una opción habitual cuando los canales tradicionales no pueden proporcionar suficiente refrigeración para zonas densas.
- Pasadores de refrigeración: Las espigas de enfriamiento se insertan en el núcleo del molde para ayudar a enfriar las piezas más gruesas. Estas clavijas son ideales para la refrigeración localizada en moldes más grandes o en zonas específicas propensas al sobrecalentamiento. También se suelen utilizar en moldes de varias cavidades, donde es difícil mantener temperaturas constantes.
El impacto del diseño del canal de refrigeración en la duración del ciclo y la calidad
El diseño de los canales de refrigeración influye tanto en la eficacia como en la calidad del proceso de moldeo por inyección:
- Reducción del tiempo de ciclo: Los eficientes canales de refrigeración ayudan a acortar el tiempo de ciclo, ya que las piezas se enfrían y solidifican más rápidamente. Unos tiempos de ciclo más cortos se traducen en un mayor rendimiento de la producción y menores costes de fabricación.
- Precisión dimensional: El enfriamiento uniforme en todo el molde ayuda a evitar el alabeo o la contracción, garantizando que las piezas mantengan su forma y dimensiones previstas.
- Acabado superficial: El enfriamiento puede afectar a la calidad de la superficie de las piezas moldeadas. Un enfriamiento uniforme minimiza las tensiones que, de otro modo, podrían estropear la superficie de la pieza, lo que se traduce en un mejor acabado.
El diseño adecuado del canal de refrigeración es una consideración esencial durante la fase de diseño del molde, ya que determina la eficacia del molde y la calidad de las piezas moldeadas.
Defectos y problemas del moldeo por inyección
A pesar de la precisión del moldeo por inyección, pueden producirse varios defectos comunes. Comprender estos problemas y cómo mitigarlos es esencial para mantener la calidad y minimizar los residuos.
Defectos comunes del moldeo por inyección
- Deformación: El alabeo es una deformación que se produce cuando diferentes partes del molde se enfrían a velocidades desiguales. Este defecto suele aparecer en moldes complejos con canales de refrigeración inadecuados o un tiempo de enfriamiento insuficiente. Para evitar el alabeo, los canales de refrigeración deben diseñarse para garantizar un enfriamiento uniforme, y el tiempo de enfriamiento debe controlarse cuidadosamente.
- Marcas de fregadero: Las marcas de hundimiento aparecen como depresiones en la superficie de las secciones más gruesas de una pieza, normalmente debido a un enfriamiento inadecuado o a una presión de sujeción insuficiente. Utilizar una presión óptima y garantizar una refrigeración adecuada, especialmente en las zonas gruesas, puede ayudar a evitar las marcas de hundimiento.
- Flash: Las rebabas se producen cuando el plástico fundido sale de la cavidad en la línea de apertura debido a una presión de inyección excesiva o a una alineación incorrecta. Una alineación precisa y unos ajustes de presión adecuados son cruciales para evitar las rebabas.
- Líneas de flujo: Las líneas de flujo son líneas visibles en la superficie de una pieza causadas por variaciones en la velocidad de enfriamiento del plástico a medida que fluye a través del molde. Ajustar la velocidad de inyección y la temperatura puede ayudar a reducir las líneas de flujo.
- Disparos cortos: Los disparos cortos se producen cuando la cavidad del molde no está completamente llena, a menudo debido a una baja presión de inyección o a una cantidad insuficiente de material. Aumentar la presión de inyección o garantizar una alimentación suficiente de material puede solucionar este problema.
- Líneas de soldadura: Las líneas de soldadura se producen donde se juntan dos frentes de flujo, creando a menudo puntos débiles en la pieza. Ajustar la velocidad de inyección o utilizar un sistema de canal caliente puede reducir las líneas de soldadura.
- Fragilidad y grietas: Estos problemas suelen deberse a una refrigeración inadecuada o a una presión de inyección demasiado alta, que induce tensiones internas. Un diseño de refrigeración adecuado y un control óptimo de la presión ayudan a mitigar la fragilidad y el agrietamiento.
Conociendo y controlando estos factores -como la velocidad de inyección, la temperatura y el diseño de la refrigeración-, los fabricantes pueden reducir los defectos y mejorar la calidad general de las piezas moldeadas.
Proceso de fabricación de moldes de inyección
La fabricación de un molde de inyección implica múltiples pasos, cada uno de ellos esencial para garantizar la durabilidad, precisión y funcionalidad del molde. A continuación se desglosan los pasos típicos de la fabricación de un molde de inyección de plástico:

- Diseño e ingeniería: La fase de diseño del molde es crucial, ya que sienta las bases para todos los pasos posteriores. Utilizando software CAD, los ingenieros crean un modelo 3D del molde, incorporando todos los detalles necesarios, como la forma de la cavidad, los canales de refrigeración, el sistema de expulsión y la línea de separación. A continuación, este modelo se somete a simulaciones para predecir problemas y optimizar el rendimiento antes de iniciar la producción física del molde.
- Selección de materiales: En función del volumen de producción y de los requisitos de la pieza, se seleccionan materiales que ofrezcan durabilidad y resistencia al desgaste. Los materiales más comunes son el acero templado para moldes de gran volumen y el aluminio para aplicaciones de menor volumen. Los moldes de acero son los preferidos para tiradas largas por su durabilidad, mientras que los de aluminio son más fáciles de mecanizar y rentables para tiradas cortas.
- Mecanizado CNC y electroerosión (EDM): El mecanizado CNC (control numérico por ordenador) se utiliza para tallar la forma primaria del molde con gran precisión. A continuación, se emplea la electroerosión para crear geometrías complejas, detalles finos y formas intrincadas en la cavidad del molde que las máquinas CNC no pueden lograr. La combinación de CNC y EDM garantiza tanto la precisión como la complejidad necesarias para el molde.
- Tratamiento térmico y endurecimiento superficial: Los moldes de acero suelen tratarse térmicamente para aumentar su dureza y durabilidad. También se aplican tratamientos superficiales, como la nitruración o el cromado, para mejorar la resistencia al desgaste, reducir la corrosión y prolongar la vida útil del molde. Los moldes de aluminio, aunque son más blandos, también pueden anodizarse para mejorar la dureza de la superficie.
- Montaje y pulido: Tras el mecanizado, se ensamblan los componentes del molde, incluido el ajuste de la cavidad, el núcleo, los pasadores eyectores, las correderas y los canales de refrigeración. A continuación, se aplica un pulido de precisión para conseguir un acabado superficial de alta calidad, especialmente en piezas que requieren una superficie estética o lisa.
- Pruebas y validación: Antes de la producción completa, el molde se somete a una prueba para garantizar que cumple las especificaciones. Este paso, conocido como muestreo T1, comprueba el rendimiento del molde e identifica posibles problemas de refrigeración, expulsión o alineación. Se realizan los ajustes necesarios para optimizar el rendimiento del molde para la producción en serie.
- Garantía de calidad y aprobación: Tras la validación, se inspecciona el molde para confirmar que cumple todas las normas de calidad. Se toman medidas para verificar la precisión dimensional y, si es necesario, se realizan ajustes. Solo después de pasar los controles de calidad se aprueba el molde para la producción completa.
Cada paso del proceso de fabricación de moldes es fundamental para garantizar que el molde final funcione de forma constante y eficaz en entornos de producción de gran volumen.
Elegir el molde de inyección adecuado para su aplicación
Seleccionar el molde de inyección adecuado es crucial para optimizar la producción, minimizar los costes y garantizar la calidad del producto. Estos son algunos factores clave que hay que tener en cuenta a la hora de elegir un molde de inyección:
- Volumen de producción: El volumen de producción previsto desempeña un papel importante en la selección del molde. La producción de grandes volúmenes suele requerir moldes duraderos de acero endurecido, mientras que los moldes de aluminio son adecuados para tiradas cortas o prototipos.
- Parte Complejidad y diseño: Las piezas complejas con geometrías intrincadas, socavados o paredes finas pueden requerir características de molde especializadas como elevadores, correderas o configuraciones multicavidad. Cuanto más compleja es la pieza, más detallado debe ser el molde, lo que puede repercutir tanto en el coste como en el tiempo de producción.
- Elección del material: Los diferentes materiales plásticos tienen características únicas de flujo, contracción y enfriamiento. Los moldes diseñados para materiales rígidos, como el policarbonato, pueden requerir configuraciones de refrigeración o materiales de moldeo diferentes a los de los moldes diseñados para plásticos flexibles, como el polietileno.
- Requisitos de duración del ciclo: Los tiempos de ciclo rápidos son esenciales para la producción de grandes volúmenes. Un molde bien diseñado con canales de refrigeración eficientes y un sistema de expulsión óptimo puede reducir el tiempo de ciclo, aumentar el rendimiento y reducir los costes.
- Consideraciones económicas: Los moldes son una inversión a largo plazo, y los costes pueden variar significativamente en función del material, la complejidad y el tipo de molde. Aunque los moldes multicavidad o de canal caliente pueden ser más caros al principio, a la larga pueden ahorrar costes al aumentar la eficiencia y reducir los residuos.
- Longevidad del moho: Para una producción continua o de gran volumen, los moldes deben estar diseñados para durar, con materiales y tratamientos superficiales resistentes. Características como el endurecimiento y el revestimiento ayudan a garantizar que el molde resista el uso repetido sin desgaste ni degradación.
Evaluando cuidadosamente estos factores, los fabricantes pueden seleccionar el molde adecuado para alcanzar sus objetivos de producción, mantener la calidad de las piezas y maximizar la rentabilidad.
Conclusión
Moldeo por inyección de plástico es una piedra angular de la fabricación moderna, que permite producir piezas de plástico precisas y de alta calidad a bajo coste y alta velocidad. Conocer los distintos aspectos de los moldes de inyección -desde los componentes, los tipos y el proceso de fabricación hasta el diseño de la refrigeración y los posibles problemas- aporta información valiosa para optimizar la producción.
Elegir el molde adecuado, implantar canales de refrigeración eficaces y mantener un control de calidad riguroso pueden mejorar enormemente la eficacia y la calidad del moldeo por inyección de plásticos. Esto no sólo satisface las exigencias de la producción de grandes volúmenes, sino que también garantiza que las piezas moldeadas cumplan las especificaciones y normas estéticas requeridas. Con los avances en materiales, diseño de moldes y tecnologías de refrigeración, el moldeo por inyección de plásticos sigue evolucionando y ofrece aún más posibilidades.
Dejar un comentario
¿Quieres unirte a la conversación?Siéntete libre de contribuir!