Guía completa de moldes de inyección de aluminio y su rentabilidad
Debido a su rentabilidad, rápida velocidad de producción y alta precisión, los moldes de inyección de aluminio se han convertido en herramientas habituales en el campo del moldeo por inyección de plástico. Los moldes están hechos de aleaciones de aluminio de alta calidad y se utilizan ampliamente para la creación de prototipos, producción de volumen bajo a medio, etc. con tiempos de liberación ajustados. El molde de aluminio no tiene un ciclo de enfriamiento largo como el molde de acero, por lo que tiene velocidades de enfriamiento más rápidas que acortan el tiempo de ciclo y mejoran la economía de producción con respecto al molde de acero. Del mismo modo, en el moldeo por inyección de aluminio, el diseño del molde y el mecanizado en CNC avanzado (Control Numérico por Ordenador) de fresado y EDM (Mecanizado por Descarga Eléctrica) se realiza para el proceso de moldeo. Después, el molde está listo para aceptar el plástico fundido, que se inyecta a alta presión en la cavidad. El aluminio tiene una gran conductividad térmica, por lo que el plástico puede enfriarse y solidificarse rápidamente, lo que permite ciclos de producción más rápidos que los utilizados con moldes de acero. A continuación, las piezas moldeadas se recortan y acaban para garantizar su calidad una vez expulsadas.
El menor coste inicial de los moldes de aluminio respecto a los de acero es una de las principales ventajas de los moldes de aluminio para moldeo por inyección. Esto es ideal para los fabricantes que quieren poca producción sin sacrificar la calidad, ya que son diseños baratos pero de calidad para la producción de tiradas cortas. Sin embargo, a diferencia de los moldes de acero, los de aluminio requieren piezas de recambio frecuentes y sólo duran entre 10.000 y 100.000 ciclos, en función del mantenimiento y la selección del material. Es necesario un mantenimiento regular para garantizar que los moldes de inyección de aluminio duren lo máximo posible. Por otra parte, la limpieza después de cada ciclo, la observación del desgaste y los daños, y el recubrimiento para protegerlos y las condiciones de almacenamiento pueden ayudar a aumentar su vida útil.
En este artículo se analiza todo el proceso del aluminio molde de inyección, las ventajas, la vida útil, el mantenimiento y la horquilla de costes.
¿Qué es un molde de inyección de aluminio?
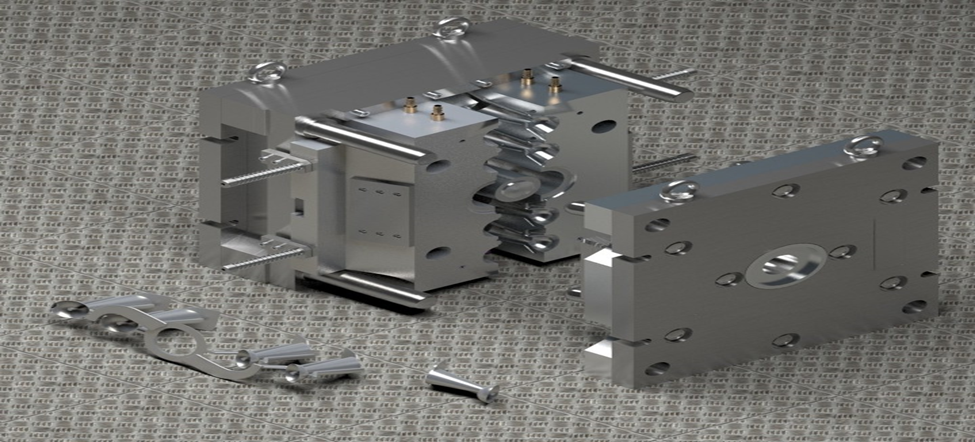
Un molde de inyección de aluminio es un molde fabricado principalmente con aluminio o aleaciones de aluminio para el moldeo por inyección de piezas de plástico. Estos moldes, en comparación con los moldes de acero convencionales, tendrían notables ventajas en la velocidad de producción y la inversión inicial.
En concreto, los moldes de aluminio son ideales para la creación de prototipos, series de producción bajas y medias, y en sectores que requieren iteraciones rápidas de piezas.
Cómo funcionan los moldes de inyección de aluminio
1. Diseño de moldes y mecanizado CNC
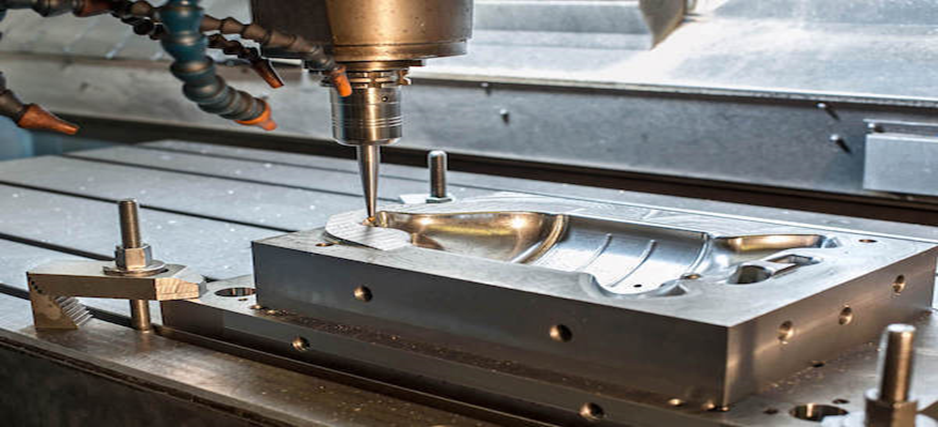
El primer paso en el proceso de diseño de moldes de inyección de aluminio es diseñar el molde de inyección de aluminio basándose en las propiedades plásticas de la pieza deseada. Los ingenieros elaboran modelos en 3D mediante diseño asistido por ordenador (CAD). Una vez decidido el molde, se mecaniza mediante CNC a partir de un bloque de aluminio, por lo que la precisión y la exactitud son muy elevadas.
2. Preparación y montaje del molde
A continuación, tras el mecanizado, se aplican al molde procesos de acabado como el pulido, el revestimiento y el expulsor. Ayudan a mejorar la durabilidad del molde y a suavizar el flujo de plástico. Una vez montado el molde en una máquina de moldeo por inyección, está listo para la producción.
3. Inyección de plástico y llenado del molde
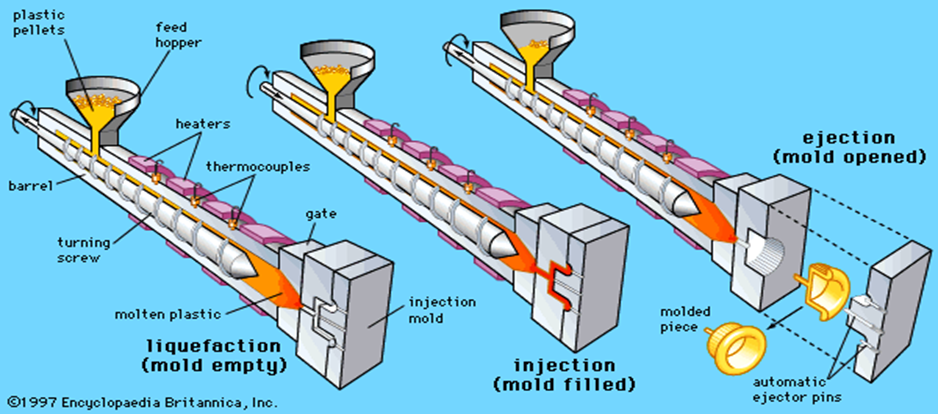
El equipo de moldeo por inyección fundirá gránulos de plástico (ABS, polipropileno, nailon) para crear plástico en estado fundido que se inyectará en la cavidad del molde de aluminio a alta presión. Además, el diseño del molde crea un relleno uniforme para evitar problemas como bolsas de aire y espesores no uniformes.
4. Enfriamiento rápido y solidificación
La conductividad térmica es una de las mejores propiedades térmicas que pueden adquirir los moldes de aluminio para el moldeo por inyección. Debido a su característica superior de disipación del calor, el aluminio se enfriará y solidificará más rápidamente que el acero. Esto reduce el tiempo de ciclo y, por tanto, la producción.
5. Expulsión de la pieza acabada
Cuando el plástico ha alcanzado la temperatura suficiente para solidificarse, unos pasadores eyectores empujan la pieza fuera del molde. El producto final se refina si es necesario, con pequeños recortes o postprocesado.
6. Repita el proceso
El molde se cierra de nuevo y el ciclo continúa para la producción en serie. Los moldes de aluminio son eficaces para ciclos rápidos y, por tanto, este tipo de moldes tiene sentido para la creación rápida de prototipos y tiradas de producción bajas o medias.
Por qué son mejores los moldes de aluminio
- Una mejor disipación del calor que permitirá tiempos de ciclo más rápidos.
- Requiere menos calor (y, por tanto, menos consumo de energía).
- Las modificaciones (cambios de diseño o mejoras) son más fáciles de hacer
El uso de moldes de inyección de aluminio permite a los fabricantes crear piezas de plástico de alta calidad a bajo coste y en poco tiempo.
Vida útil y mantenimiento de los moldes de aluminio

Vida útil de los moldes de inyección de aluminio
La vida útil de los moldes de inyección de aluminio viene determinada por varias causas, como la calidad del material, la cantidad de producción y también el tipo de plástico. Por ejemplo, los moldes de aluminio pueden soportar una media de entre 10.000 y 100.000 ciclos de inyección, razón por la cual los moldes de aluminio se utilizan habitualmente para series de producción de volumen bajo a medio.
Mientras que los moldes de aluminio tienen una vida útil más corta en comparación con los de acero, que pueden soportar entre 500.000 y más de un millón de ciclos. Por supuesto, su vida útil puede prolongarse enormemente mediante un revestimiento protector, un diseño adecuado y mantenimiento.
Varios factores afectan a la vida útil de los moldes de aluminio.
1. Selección de materiales: Las aleaciones de aluminio de grado inferior no son tan fuertes y duraderas como las aleaciones de aluminio de alto grado como 7075 o QC 10.
2. El entorno de producción: Están expuestos a altas presiones de inyección en condiciones de fabricación y están en contacto con materiales muy abrasivos (como plásticos rellenos de vidrio) que contribuyen a un desgaste más rápido.
3. Esto incluiría el enfriamiento y el ciclado térmico: el molde de aluminio se enfría mucho más rápido que un molde de acero, lo que provoca menos tensiones térmicas. Sin embargo, las fluctuaciones extremas de temperatura pueden provocar grietas con el tiempo.
4. Recubrimientos y tratamientos superficiales: El niquelado, el anodizado o los revestimientos duros pueden ser tratamientos eficaces para evitar el desgaste y la corrosión y, por tanto, aumentar la vida útil de un molde.
Aunque los moldes de aluminio no son satisfactorios para grandes series de producción, con un diseño y un cuidado adecuados, pueden durar lo suficiente para realizar prototipos y series de producción bajas o medias a un nivel relativamente rentable.
Mantenimiento de moldes de inyección de aluminio
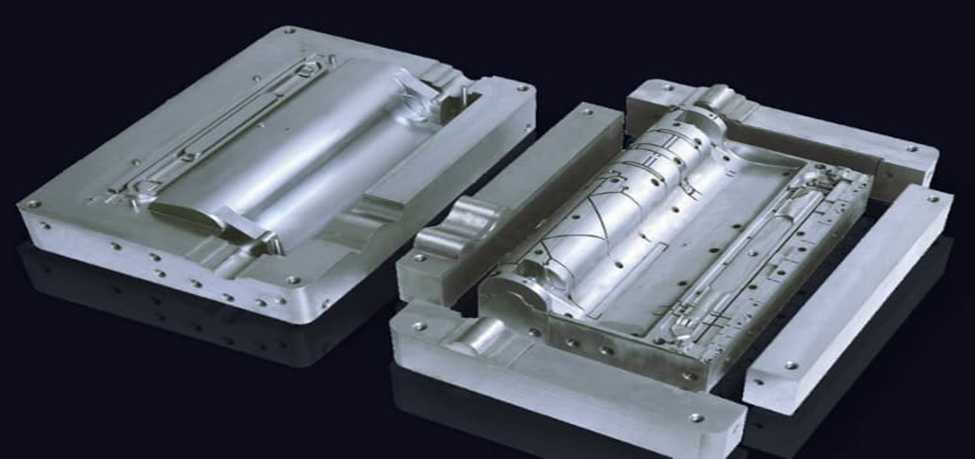
Para conseguir la máxima vida útil de los moldes de aluminio para moldeo por inyección y una calidad constante de las piezas, es necesario realizar un mantenimiento periódico. Los moldes de aluminio, a diferencia de los de acero, son más blandos y más propensos a sufrir arañazos o daños, por lo que es necesario un mayor mantenimiento preventivo.
Procedimientos de mantenimiento diario
Después de cada ciclo de producción, por ejemplo, debe limpiar el molde para eliminar cualquier residuo de plástico, desechos y contaminación. Para evitar arañazos en la superficie del molde, se utilizan productos de limpieza no abrasivos. Para evitar que se pegue al producir, se puede aplicar un ligero agente desmoldeante.
Inspecciones y reparaciones periódicas
Las inspecciones rutinarias permiten identificar a tiempo arañazos superficiales, abolladuras o pequeñas grietas y signos de desgaste prematuro. Asegurarse de que hay suficientes pasadores eyectores, suficientes canales de refrigeración y zonas de ventilación permite que el molde siga funcionando y siga siendo eficiente. Si se detecta desgaste, pueden realizarse pequeñas reparaciones, como pulir o volver a recubrir, para restablecer el rendimiento del molde.
Almacenamiento y protección
Los moldes de aluminio deben almacenarse cuando no se utilicen en un entorno seco y con temperatura controlada para que no se produzca corrosión. Para mantener el molde en buen estado, se recomienda aplicar una capa protectora o un spray antioxidante antes de guardarlo.
Problemas comunes de mantenimiento y soluciones
1. Arañazos superficiales: Los puntos altos pueden reducirse hasta la suavidad utilizando compuestos de pulido fino o revestimientos.
2. 2. Cambio de temperatura (agrietamiento o deformación): No someter a cambios drásticos de temperatura, utilizar calentamiento y enfriamiento graduales.
3. Piezas moldeadas: Aplique los agentes desmoldeantes al diseño de su pieza para mejorar la expulsión del molde.
4. Corrosión u oxidación: Deben almacenarse en un entorno controlado donde estén protegidos por revestimientos.
¿Cuándo debemos optar por producir moldes de inyección de aluminio?
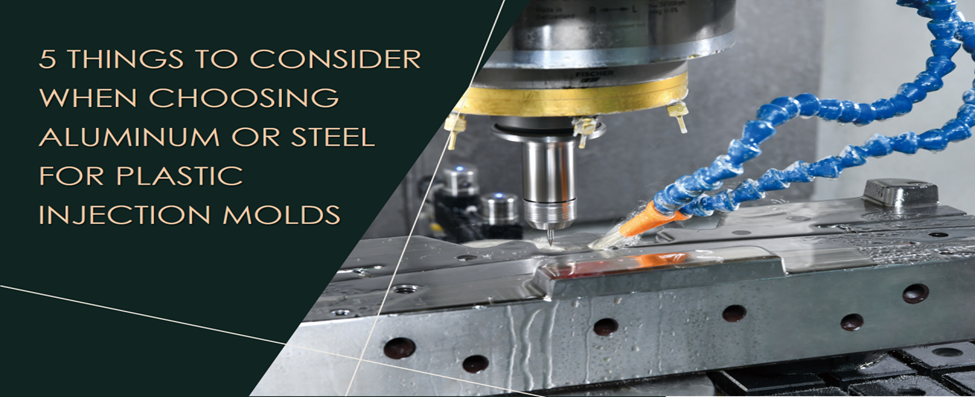
1. Cuándo necesita prototipos rápidos
Cuando una empresa necesita desarrollar un nuevo producto pero necesita los prototipos de forma rápida y económica, los moldes de inyección de aluminio son una solución barata y rápida. A diferencia de los moldes de acero, que pueden tardar meses, estos deben permitir a los fabricantes fabricar piezas de prueba días o semanas después. Además, permiten cambiar rápidamente el diseño y ayudan a reducir los costes de desarrollo antes de pasar a la producción a gran escala.
2. Si su volumen de producción es de bajo a medio
Para la fabricación de entre 10.000 y 100.000 piezas de plástico, el molde de aluminio es una alternativa ideal al molde de acero en beneficio del fabricante. Son baratos al principio, tienen ciclos de producción más cortos y una buena vida útil, lo que los hace perfectos para tiradas cortas o productos de temporada. Los moldes de aluminio, a diferencia de los moldes de acero que requieren una elevada inversión inicial, permiten a la empresa reducir costes sin comprometer la calidad.
3. Cuando la rapidez y la eficacia son importantes
Dado que el aluminio es un material de alta conductividad térmica, el plástico inyectado se enfría mucho más rápido en los moldes de aluminio que en los de acero. De este modo se consiguen tiempos de ciclo más cortos, una mayor eficacia de producción y un menor consumo de energía. Los moldes de aluminio son los preferidos por las empresas que requieren un tiempo de respuesta rápido y que necesitan una mayor eficiencia en el flujo de trabajo.
4. Cuando necesite utillaje rentable
Debido al elevado coste que supone crear moldes de acero para una empresa nueva o pequeña, o para poner a prueba un producto, puede que no sea una inversión decorativa. Por otra parte, los moldes de inyección de aluminio son mucho más baratos que sus homólogos, por lo que es una buena idea seleccionarlos si se dispone de un presupuesto bajo. Para una empresa que no está segura de si su producto requerirá mucha producción de gran volumen, los moldes de aluminio reducen los riesgos financieros, pero hay que asegurarse de que las piezas sean de primera calidad.
5. Cuando se requiere alta precisión y acabado superficial
Los moldes de aluminio son ideales para obtener una gran precisión y un acabado superficial liso. El uso de moldes de aluminio es necesario en la producción de tolerancias ajustadas y superficies sin defectos en las industrias de dispositivos médicos, electrónica de consumo y fabricación aeroespacial. Los métodos actuales de mecanizado y acabado hacen que los proveedores de moldes de aluminio sean capaces de ofrecer una excelente calidad de las piezas y, en ocasiones, de hacer innecesario el procesamiento secundario.
6. En qué pueden no ser adecuados los moldes de aluminio
Hay varias ventajas asociadas a los moldes de inyección de aluminio, pero no todas las situaciones se beneficiarán de su uso. Los moldes de acero, sin embargo, son más adecuados para volúmenes de producción de más de 500.000 piezas debido a su durabilidad y longevidad. En la industria del moldeo a alta presión, los moldes de aluminio pueden desgastarse más rápidamente y, por tanto, no deben utilizarse en condiciones de fabricación extremas.
Ventajas de los moldes de inyección de aluminio
1. Tiempo de producción más rápido
Dado que los moldes de inyección de aluminio ofrecen una disipación del calor mucho mejor que un molde de acero, el plástico inyectado se enfría mucho más rápido. En consecuencia, los ciclos de producción con tales moldes son considerablemente más cortos que con los de acero, lo que también aumenta la eficiencia.
2. Costes iniciales más bajos
Los moldes de aluminio son mucho más baratos de producir que los moldes de acero utilizados en el moldeo por inyección. Esto los convierte en una opción excelente para empresas de nueva creación, fabricantes de lotes pequeños y empresas que trabajan en el desarrollo de prototipos.
3. Mecanizado y modificaciones más sencillos
La fabricación de moldes es más rápida y menos costosa porque el aluminio es más fácil de cortar y moldear que el acero. Además, la flexibilidad del diseño puede lograrse con un menor esfuerzo de modificaciones y ajustes.
4. Acabado superficial de alta calidad
Los moldes de aluminio proporcionan ligereza y un buen acabado de las piezas, sin necesidad de postprocesado. Los moldes de inyección de aluminio se utilizan en muchas industrias para crear piezas con un diseño suave y detallado de gran precisión.
5. 5. Respetuoso con el medio ambiente
Los moldes de inyección de aluminio son una opción sostenible frente a las alternativas de acero, ya que se trata de un material reciclable.
Moldes de inyección de aluminio frente a moldes de acero
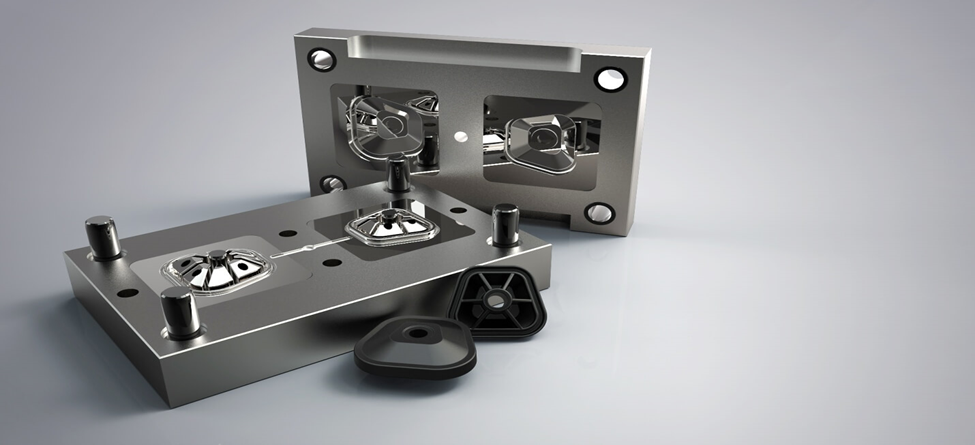
Dos características vitales en la producción de moldes son los moldes de inyección de aluminio junto con los moldes de acero.
- El coste inicial de los moldes de inyección de aluminio sigue siendo inferior, mientras que se mantienen los gastos más elevados de los moldes de acero.
- La velocidad de producción entre los moldes de inyección de aluminio y los moldes de acero varía ya que los moldes de aluminio experimentan un enfriamiento más rápido mientras mantienen ciclos más cortos a diferencia de los moldes de acero que operan con ciclos de producción más largos.
- Los moldes de acero duran más que los moldes de inyección de aluminio debido a su rango operativo de 100.000 a más de 100.000 ciclos, mientras que los moldes de aluminio tienen una vida útil de 10.000 a 100.000 ciclos.
- Los moldes de aluminio son más fáciles de mecanizar que los de acero, pero estos últimos plantean mayores problemas de modificación al usuario.
- El acabado superficial demuestra la alta calidad junto con la necesidad de un acabado adicional mediante pulido.
- Los moldes de aluminio resultan más económicos que los de acero para fabricar productos en entornos de producción cortos o medios, ya que prolongan menos los ciclos de producción.
Aplicaciones de los moldes de inyección de aluminio
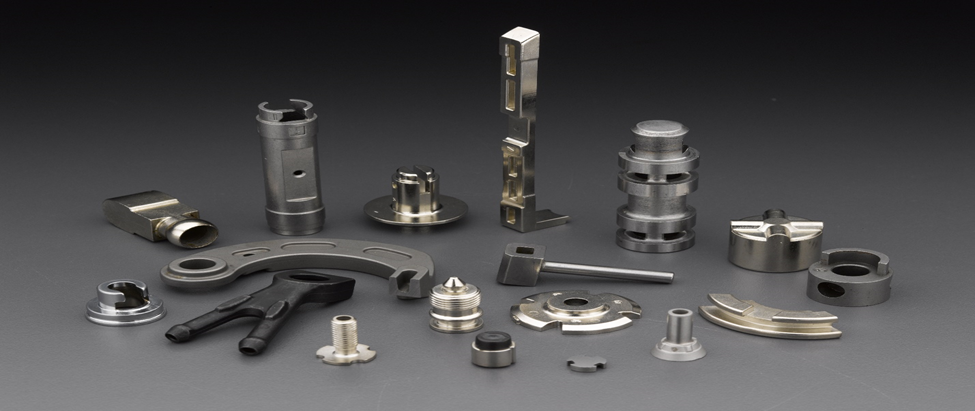
1. Creación de prototipos y desarrollo de productos
Las empresas de prototipado rápido eligen los moldes de inyección de aluminio tanto por su asequibilidad como por su capacidad para realizar modificaciones rápidas en el diseño.
2. Producción de volumen bajo a medio
La combinación de asequibilidad y calidad de suministro hace que los moldes de inyección de aluminio sean adecuados para fabricar entre 10.000 y 100.000 piezas sin efectos negativos.
3. Productos médicos y de consumo
Los moldes de aluminio sirven a múltiples industrias dedicadas a los dispositivos médicos, así como a la fabricación de productos de consumo, ya que estas aplicaciones necesitan componentes precisos fabricados con eficacia.
4. Componentes aeroespaciales y de automoción
Los efectos positivos de los moldes de aluminio incluyen la fabricación de componentes ligeros que crean estructuras vitales de alto rendimiento para los sectores de vehículos aeroespaciales y de transporte de automóviles.
Coste del molde de inyección de aluminio
- Los moldes de inyección de aluminio más caros resultan de la combinación de tres factores principales que son su tamaño complejidad y volumen de producción.
- Varias variables determinan el coste global de la fabricación de moldes de inyección de aluminio.
- Los costes aumentan debido al incremento de las necesidades de material unido al aumento de los gastos de mano de obra cuando se fabrican moldes de aluminio complejos o de gran tamaño.
- Los fabricantes refuerzan los moldes de inyección de aluminio mediante la adición de revestimientos protectores cuando se prevé una producción de gran volumen, ya que estas modificaciones alargan la vida útil del molde.
- El coste aumenta cuando se utilizan moldes de cavidades múltiples que crean simultáneamente numerosas piezas.
- Los cambios introducidos una vez iniciada la producción generarán costes adicionales.
2. El coste de producción de moldes entre los tipos de aluminio y acero merece un examen
La siguiente tabla ofrece un análisis de costes y velocidad de los distintos tipos de moldes de inyección de plástico a lo largo de la producción:
Tipo de molde | Coste inicial | Coste de mantenimiento | Velocidad de producción | Lo mejor para |
Molde de inyección de aluminio | $5,000 – $25,000 | Bajo | Rápido | Prototipos de tiradas bajas-medias |
Molde de inyección de acero | $15,000-$100,000+ | Más alto | Más lento | Producción a gran escala |
Las empresas que necesitan reducir su gasto inicial y desean mantener la calidad de la producción eligen los moldes de aluminio por su carácter asequible.
Cómo elegir el fabricante de moldes de inyección de aluminio adecuado
A la hora de elegir un fabricante de moldes de aluminio para moldeo por inyección, tenga en cuenta:
- Reputación y experiencia con los fabricantes: Trabaje con fabricantes que tengan una excelente reputación y experiencia en la fabricación de moldes de alta calidad.
- Garantía de cierta capacidad de configuración: No debería ser difícil para el fabricante configurar las piezas.
- Mayor durabilidad y longevidad: La calidad del aluminio utilizado es de alto grado, lo que alarga la vida útil del portátil.
- Tiempo de entrega del molde: Cualquier buen fabricante entregará los moldes rápidamente sin comprometer la calidad.
- Mantenimiento y reparación: Elija empresas que ofrezcan asistencia postventa.
Conclusión
Los moldes de inyección de aluminio son una forma eficaz, rentable y rápida de fabricar piezas de plástico. Se utilizan para fabricar prototipos con rapidez, tanto de baja como de media producción, así como en industrias que requieren gran precisión. De este modo, los tiempos de enfriamiento se reducen a fracciones del tiempo de los moldes de acero convencionales y los ciclos de producción son más rápidos. Mientras que los moldes de aluminio tienen un coste inicial más bajo y una fabricación más rápida, el desgaste del acero contra la superficie metálica es mayor y no durará tanto. A pesar de ello, si se mantiene la lubricación, los revestimientos protectores y la limpieza periódica, los fabricantes pueden prolongar su vida útil hasta 100.000 ciclos. En función de los volúmenes de producción, el presupuesto y otros requisitos de un proyecto concreto, se puede decidir entre moldes de aluminio o de acero.
Los moldes de inyección de aluminio son un sustituto ideal de los costosos moldes de acero para proyectos de tirada corta, prototipos y aplicaciones sensibles a los costes. Por el contrario, los moldes de acero son más apropiados para una durabilidad extrema cuando se requiere un alto volumen de producción. Conociendo el proceso, las ventajas y el mantenimiento de los moldes de inyección de aluminio, las empresas pueden equilibrar el coste, la calidad y la eficacia de la producción. Independientemente de si los moldes de plástico se utilizan para la producción de pequeños lotes o para probar nuevos diseños de productos, se consideran un activo importante en la fabricación moderna de plásticos.
Preguntas más frecuentes (FAQ)
1. ¿Por qué se utilizan moldes de inyección de aluminio?
Para la producción de piezas de plástico, una aplicación común de los moldes de inyección de aluminio son los prototipos rápidos, la producción de volumen bajo a medio y las industrias con una necesidad urgente de una entrega rápida. Los sectores médico, automovilístico, aeroespacial y de fabricación de productos de consumo suelen utilizarlos.
2. ¿Cuánto duran los moldes de inyección de aluminio?
Sin embargo, la vida útil de los moldes de aluminio depende de la calidad del material, el mantenimiento y las condiciones de producción. Su ciclo medio oscila entre 10.000 y 100.000 ciclos, lo que los hace adecuados para la producción de series cortas y prototipos.
3. ¿Son los moldes de inyección de aluminio menos caros que los de acero?
El moldeo por inyección de aluminio cuesta mucho menos que el de acero. Para velocidades de producción más rápidas y menos tiempo de mecanizado, menor coste inicial, son económicos para la fabricación de tiradas cortas.
4. ¿Cuáles son los límites de los moldes de aluminio cuando se someten a moldeo por inyección a alta presión?
Aunque los moldes de aluminio son capaces de soportar un moldeo por inyección a presión moderadamente alta, no son tan duraderos como los moldes de acero para presiones de trabajo muy elevadas y aplicaciones de gran volumen. No obstante, pueden reforzarse con revestimientos protectores y refuerzos.
5. ¿A qué industrias benefician más los moldes de inyección de aluminio?
Por esta razón, los moldes de inyección de aluminio son muy útiles para industrias como la de dispositivos médicos, electrónica de consumo, prototipos de automoción e incluso aeroespacial.
Dejar una respuesta
¿Quiere participar en el debate?No dude en contribuir.