En la actualidad, China ha consolidado su posición como líder mundial en empresas de moldeo por inyección y se ha convertido en una valiosa solución de fabricación para empresas de todos los tamaños del mundo, a precios competitivos. Gracias a su gran número de empresas de moldeo por inyección, China se ha convertido en una zona especializada en la producción de componentes de plástico para todo el espectro de industrias, desde la automoción, la electrónica, la sanidad y el envasado hasta los bienes de consumo. Ellas se encargan del trabajo pesado de la tecnología avanzada, la ingeniería de precisión y la automatización se utilizan para fabricar piezas moldeadas con una precisión y eficacia insuperables. Varias ventajas clave construyen la industria china de moldeo por inyección por la que las empresas tienden a optar. Una de las mayores fuerzas de atracción en relación con la rentabilidad de la producción es que los costes laborales y de producción son más baratos en China que en los países occidentales. Además, las empresas de moldeo chinas están cada vez más equipadas con maquinaria y sistemas de robótica de última generación y alta eficiencia, lo que permite una producción eficiente y de gran volumen al mismo tiempo que se mantiene la calidad. La empresa cuenta con certificaciones reconocidas internacionalmente como ISO 9001, ISO 13485 (dispositivos médicos) e IATF 16949 (componentes de automoción) para cumplir las normas de calidad de la industria mundial.
Las empresas chinas de moldeo por inyección también tienen la fuerza de la personalización y la innovación. Los fabricantes chinos tienen la capacidad técnica y la experiencia necesarias para proporcionar moldes personalizados para moldes multicavidad, sobremoldeo, moldeo por inserción y diseños complicados. Para las empresas que buscan rapidez y fiabilidad, su capacidad para ofrecer plazos de entrega rápidos y una producción a gran escala es la opción preferida.
¿Qué es el moldeo por inyección?
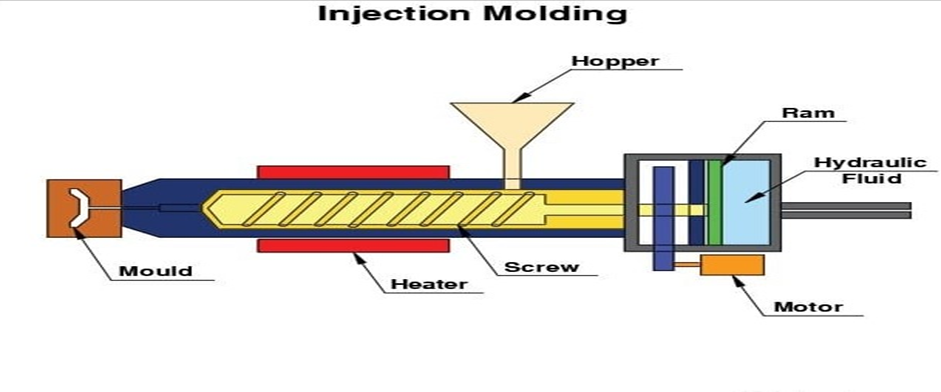
Es un proceso de fabricación de piezas de plástico por inyección de material fundido en un molde. Su uso está muy extendido en los sectores de automoción, medicina, electrónica, envases de plástico y artículos domésticos. Este proceso permite fabricar piezas complejas en serie con gran precisión y consistencia.
¿Por qué recurrir a una empresa china de moldeo por inyección?
En primer lugar, China se ha convertido en un importante centro de moldeo por inyección por diversas razones:
1. Producción rentable
El precio es una de las razones clave por las que las empresas eligen empresas de moldeo chinas. Dado que los costes laborales y operativos en China son más bajos que en los países occidentales, es posible producir componentes moldeados de alta calidad por una fracción del coste.
2. Tecnología de fabricación avanzada
En las modernas empresas chinas de moldeo por inyección se realizan grandes inversiones en automatización y maquinaria de última generación. Muchas empresas utilizan sistemas robotizados, diseño asistido por ordenador (CAD) y sistemas de control de calidad en tiempo real para garantizar la precisión y la máxima productividad.
3. Normas de alta calidad
La mayoría de las empresas chinas de moldeo respetables se rigen por normas de calidad internacionales como ISO 9001, ISO 13485 (para dispositivos médicos) e IATF 16949 (piezas de automoción). Estas certificaciones garantizan que el producto cumple los requisitos de alta calidad.
4. Personalización e innovación
Muchas empresas chinas de moldeo ofrecen soluciones personalizadas adecuadas a las diferentes necesidades de las empresas. Los fabricantes chinos tienen una respuesta para cada necesidad del cliente, desde el sobremoldeo y el moldeo por inserción, y quieren a la necesidad de un cliente de modelos complejos de múltiples cavidades.
5. Plazos de entrega rápidos
Las empresas chinas de moldeo pueden producir en grandes volúmenes con más eficacia y rapidez que la mayoría de sus competidores gracias a unas cadenas de suministro eficientes y a unos procesos de producción racionalizados. Las empresas que dependen de la rapidez para sacar productos al mercado necesitarán el apoyo de esta velocidad.
6. Experiencia y conocimientos
Existen miles de empresas especializadas en la industria china del moldeo por inyección que cuentan con una gran experiencia en todas estas áreas. Se las considera la opción preferida de las empresas mundiales en su dominio del diseño de moldes y la selección de materiales, así como en ingeniería de precisión.
Sectores que se benefician de las empresas chinas de moldeo por inyección

El uso del moldeo por inyección es bastante amplio y se extiende por diferentes industrias, cada una de las cuales tiene sus propias normas y tecnologías.
1. Industria del automóvil
Las empresas chinas de moldeo fabrican piezas como salpicaderos, parachoques, paneles interiores y componentes de iluminación en el sector del automóvil, que depende en gran medida de estas empresas. Una ventaja clave es la capacidad de fabricar piezas de plástico ligeras pero duraderas.
2. Electrónica y bienes de consumo
Para la industria electrónica y de bienes de consumo y otros productos, las empresas chinas de moldeo por inyección están especializadas en la producción de piezas de alta precisión. Cada vez se necesitan más componentes de plástico estéticos, duraderos y funcionales.
3. Medicina y sanidad
Dispositivos como instrumentos quirúrgicos, jeringuillas y conectores intravenosos utilizan piezas fresadas por inyección de alta calidad, y la industria médica no puede prescindir de ellas. Dependiendo del fabricante médico, muchas empresas de moldeo chinas cuentan con instalaciones de sala blanca para cumplir estrictas normas de higiene y seguridad según la fabricación médica.
4. Envasado e industria alimentaria
El moldeo por inyección también se utiliza para otra aplicación importante, a saber, los envases de plástico, que incluyen recipientes, tapones y botellas. Por un lado, los fabricantes chinos producen soluciones de envasado duraderas y de alta calidad y, por otro, son respetuosos con el medio ambiente.
Actores clave de la industria china del moldeo por inyección
El moldeo por inyección ha emergido como líder en China para industrias que van desde la automoción, la sanidad y la electrónica hasta los bienes de consumo, con una alta calidad y rentabilidad. China empresas de moldeo por inyección siguen liderando el mercado mundial gracias a su avanzada capacidad de fabricación, sus equipos de última generación y el cumplimiento de las normas internacionales de calidad. Hay algunos de los conocidos chinos de fabricación de moldes de moldeo moldes de porcelana piezas de plástico empresas de fabricación.
Sincere Tech: Proveedor líder de soluciones de moldeo por inyección de plástico
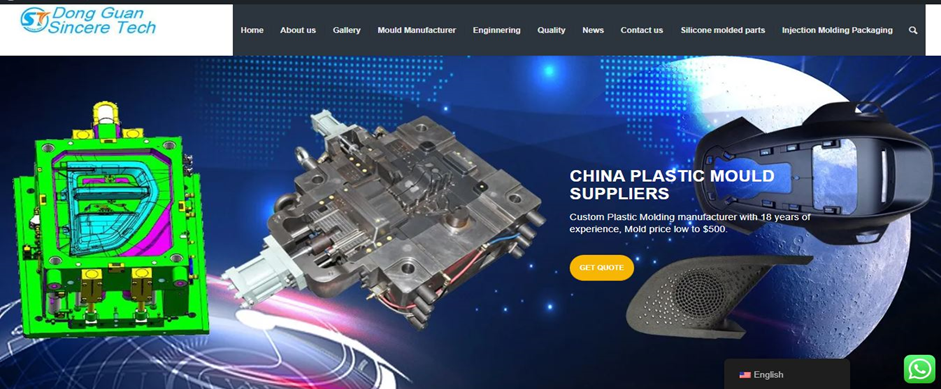
Sincere Tech, fundada en 2005 y situada en la ciudad de la provincia de Dongguan, China, es conocida por llevar más de 10 años prestando servicios de suministro de moldes de inyección de plástico moldeado a empresas. La compañía ha ampliado sus capacidades para incluir cosas como moldes Eddie-casting, moldeo de caucho de silicona, mecanizado CNC, y el montaje completo del producto y participa en una amplia variedad de industrias en todo el mundo.
Amplia gama de servicios
Sincere Tech ofrece soluciones de fabricación totales para aquellos clientes con los siguientes tipos:
- La empresa ofrece productos como moldes de inyección de plástico personalizados con capacidad para diseñar y fabricar moldes de alta precisión para la fabricación en serie de componentes de plástico duraderos y precisos.
- Mecanizado de precisión - El mecanizado CNC, fresado, taladrado, torneado y rectificado realizado por Sincere Tech es con total experiencia, asegurando que cada pieza fabricada es con precisión y alta calidad.
- Para mejorar el proceso de fabricación, la empresa de fabricación de moldes de fundición a presión alcanza el éxito fabricando moldes de fundición a presión de alta calidad y alto rendimiento y ensamblándolos para producir componentes metálicos duraderos que cumplan las especificaciones de los estrictos requisitos de la industria.
- Proporcionamos servicios de moldeo por inyección utilizando máquinas avanzadas de moldeo por inyección de plástico para producir componentes hechos de los siguientes materiales como PP, ABS, PPS, PEEK, PA66+GF30.
- Servicios de montaje de productos - La empresa monta eficazmente subconjuntos, montajes sencillos y productos totalmente montados, siguiendo rigurosas normas de calidad.
- Sincere Tech ofrece soluciones de moldeo de silicona para proyectos específicos en diversas industrias.
Compromiso con la calidad y el avance tecnológico
Sin embargo, sincerely tech mantiene el más alto nivel de calidad mediante el cumplimiento de normas internacionales como ISO 9001:2015 y QS 9000:2015. Para fabricar moldes y piezas de la mejor calidad, la empresa hace uso de maquinaria avanzada que incluye máquinas CMM, máquinas CNC de 5 ejes y maquinaria FANUC. Sincere Tech también ofrece a sus clientes acuerdos de confidencialidad para la protección de la propiedad intelectual y los diseños patentados de los clientes.
Al servicio de la industria mundial
Sincere Tech, una empresa con proyección internacional, suministra componentes de plástico y metal a diversas industrias (automoción, medicina, electrónica, electrodomésticos, jardinería, cosmética, envases alimentarios y conectores eléctricos). La empresa tiene muy buenas ventas en el mercado de exportación, cuyos productos se envían a distintos mercados mundiales, incluida Finlandia, ya que puede cumplir las distintas normas y requisitos específicos de la industria.
Enfoque centrado en el cliente
Sincere Tech valora los precios competitivos, la fabricación de alta calidad y un servicio de buena calidad. Por otro lado, como socio fiable de empresas internacionales, la empresa cuenta con una gran capacidad de gestión de proyectos, una comunicación en inglés técnico clara y un alto grado de satisfacción del cliente.
Seasky Medical
Seasky Medical, empresa china de moldeo por inyección, fabrica plásticos para uso médico. La empresa tiene su sede en Shenzhen, Guangdong, desde 1999 y proporciona las mejores soluciones de moldeo por inyección. Ofrecen un fino diseño de moldes, selección de materiales y moldeo por inyección, además de ocuparse del desarrollo de productos, para que los componentes médicos cumplan las normas más estrictas de calidad y seguridad.
Las operaciones de Seasky Medical, con certificación ISO 8, garantizan la producción de dispositivos médicos como jeringuillas, componentes intravenosos e instrumentos quirúrgicos en un entorno libre de contaminación. Como empresa con más de una década de experiencia, son conocidos por ofrecer un moldeo por inyección médica fiable y preciso en el que prestan servicio a proveedores sanitarios de todo el mundo.
Shenzhen Silver Basis Technology Co., Ltd
Shenzhen Silver Basis Technology es una empresa china profesional de moldeo, dedicada a la fabricación de moldes para automoción e industria. Formada en 1993, la empresa es uno de los proveedores más fiables de marcas famosas del mundo como Peugeot y ZTE, suministrando modelos para diversos usos.
Silver Basis ofrece una amplia gama de servicios de estampación metálica, fundición a presión, fabricación de moldes y pruebas de productos. Gracias a su experiencia en moldeo por inyección para automoción, pueden fabricar piezas interiores y exteriores de vehículos duraderas y precisas. Dado que la empresa se centra en la calidad, ha obtenido los certificados ISO 9001 e ISO 14001, por lo que es una empresa elegida por fabricantes internacionales de automoción y electrónica.
JMT Automotive Mold Co., Ltd
JMT Automotive Mold Co., Ltd es una reputada empresa china de moldeo por inyección que se dedica al diseño y la fabricación de moldes para automóviles. Desde su fundación en 2005 y con sede en Taizhou, Zhejiang, la empresa ha construido un sólido sistema de fabricación para satisfacer las crecientes necesidades de la industria del automóvil.
JMT Automotive Mold cuenta con una experiencia operativa en un centro de producción de 23.000 metros cuadrados y es uno de los fabricantes especializados en moldes SMC, moldes para electrodomésticos y moldes industriales. Cuentan con maquinaria CNC de alta velocidad, equipos de pruebas de precisión y maquinaria de moldeo por inyección de última generación que conducen a un alto nivel de producción. JMT Automotive mantiene el funcionamiento de la innovación tecnológica y la ingeniería de precisión, y seguimos ofreciendo una fabricación de moldes fiable para clientes nacionales y extranjeros.
TK Mold Ltd
Fundada en 1978, TK Mold Ltd es una conocida empresa china de moldeo con más de 40 años en la fabricación de moldes de plástico. La empresa se fundó en 1983 y está especializada en el desarrollo de moldes de alta precisión para aparatos médicos, electrónica de consumo, electrodomésticos inteligentes y componentes de automoción.
TK Mold ofrece soluciones avanzadas de moldeo por inyección a su grupo mundial de clientes desde su base de 5 plantas de producción, incluida una en Alemania. Al ser pionera en la adopción de tecnología punta, automatización y fabricación de precisión, la empresa es muy apreciada por las industrias que exigen componentes de plástico de alto rendimiento. Todos los productos de TK Mold están certificados según las normas ISO 9001, ISO 13485 e ISO 14001 para garantizar que cumplen las normas internacionales de calidad y seguridad.
Guangdong Yizumi Maquinaria de Precisión S.L.
Guangdong Yizumi es una empresa china líder en moldeo por inyección que produce máquinas de moldeo por inyección de alto rendimiento, así como componentes de plástico. Yizumi se fundó en 2002 y su sede central se encuentra en Foshan, Guangdong. Con más de 600.000 metros cuadrados de base de producción y casi 3.000 empleados, Yizumi se ha convertido en una marca mundial.
Yizumi ha ganado numerosos premios del sector por sus innovaciones en tecnología de moldeo por inyección y es conocida por sus innovadoras soluciones de moldeo. En 2015, la empresa se convirtió en la primera compañía china de moldeo en cotizar en la Bolsa de Shenzhen. Yizumi se está centrando en la automoción, la electrónica de consumo y las aplicaciones industriales, y se está convirtiendo en líder del sector gracias a su maquinaria de última generación y al moldeo de alta precisión.
Retos y consideraciones a la hora de elegir una empresa china de moldeo
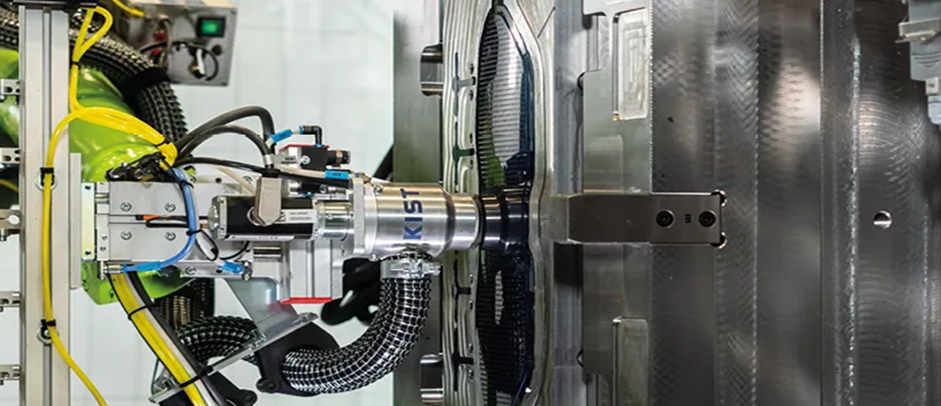
Las empresas mineras chinas presentan muchas ventajas, sin embargo, antes de comprometerse con un fabricante, las empresas deben ser conscientes de algunos aspectos.
1. Control de calidad y conformidad
No todos los fabricantes siguen las mismas normas de calidad. Antes de elegir un proveedor, conviene verificar las certificaciones y probar primero una muestra.
2. Protección de la propiedad intelectual
Fabricar en China puede ser un problema para externalizar la protección de la propiedad intelectual (PI). Para evitar perder sus diseños y mantenerlos a salvo, las empresas deben trabajar con socios de confianza y acuerdos legales.
3. Barreras lingüísticas y de comunicación
Aunque varios fabricantes chinos tienen equipos de ventas que hablan inglés, la comunicación no siempre es sencilla. La documentación y los acuerdos están preparados para evitar malentendidos.
4. Logística y transporte
Sin embargo, tramitar grandes pedidos a escala internacional puede resultar complejo y costoso. Las empresas de moldeo chinas deben comprender la normativa aduanera, los plazos de entrega y los costes de transporte de las empresas.
Tendencias futuras del moldeo por inyección en China
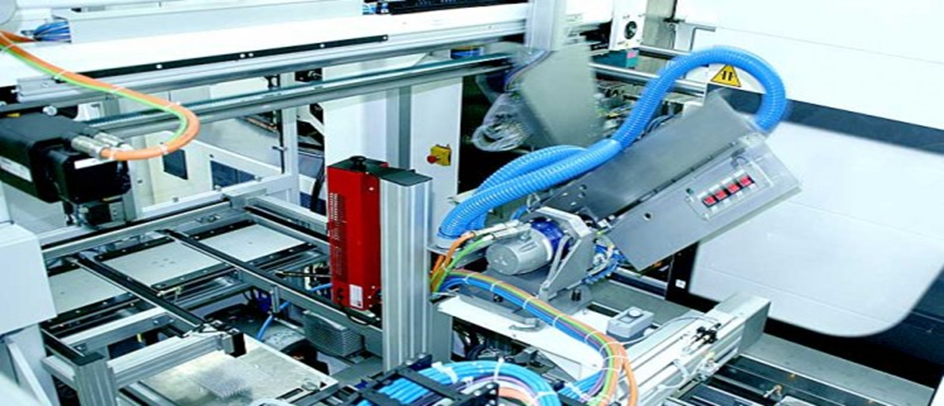
Con las nuevas tecnologías, llega el desarrollo de la industria china del moldeo para satisfacer las nuevas demandas del mercado. Las tendencias clave incluyen:
1. Materiales sostenibles y respetuosos con el medio ambiente
A medida que la preocupación por los residuos plásticos ha ido creciendo en China, muchas empresas de moldeo se han preocupado más por la normativa medioambiental y ahora desarrollan materiales plásticos biodegradables y reciclados.
2. Fabricación inteligente e Industria 4.0
La automatización y el control de calidad impulsado por IA, el cambio completo de un proceso centrado en el ser humano a una fábrica inteligente habilitada para IoT han transformado por completo el proceso de moldeo por inyección y hacen que la producción sea más eficiente y con menos desperdicios.
3. Mayor personalización y producción bajo demanda
Las empresas se están centrando en la producción bajo demanda de lotes pequeños para nichos de mercado y en el desarrollo rápido de productos.
Conclusión
Las empresas chinas de moldeo por inyección son una parte integral de la industria manufacturera mundial, ya que estas empresas proporcionan soluciones rentables, de alta calidad e innovadoras para los clientes. Algunos de estos fabricantes mecanizan piezas de plástico para componentes de automoción, dispositivos médicos y otras industrias relacionadas. A la hora de elegir una empresa china de moldeo, las entidades comerciales deben examinar rigurosamente las normas de calidad, la conveniencia de la comunicación y la logística para asegurarse una asociación satisfactoria. Debido a la continua tendencia de los avances tecnológicos y las prácticas sostenibles, las empresas de moldeo chinas seguirán liderando el moldeo por inyección durante muchos años más. Sin embargo, dadas las numerosas ventajas, las empresas deben sopesar el control de calidad, la protección de la propiedad intelectual, los retos de comunicación y la logística antes de elegir un socio de moldeo chino. Sin embargo, si se ha investigado a fondo y se colabora con fabricantes que produzcan con calidad y estén certificados para el trabajo, las empresas podrán cosechar los beneficios de la experiencia china en moldeo por inyección. En el futuro, el moldeo por inyección en China se caracterizará por materiales sostenibles, fabricación inteligente, producción de alta velocidad y automatización impulsada por la producción junto con plásticos biodegradables y tecnologías de Industria 4.0, China seguirá teniendo los mayores avances en el moldeo por inyección global. A medida que las empresas de moldeo chinas avanzan continuamente y hacen todo lo posible para alterar la cara de la fabricación china, seguirán impulsando la fabricación moderna.
Preguntas más frecuentes (FAQ)
1. ¿Por qué es popular la fabricación de moldeo por inyección en China?
Elegir China para el moldeo por inyección ofrece la ventaja de una producción rentable, tecnología moderna, mano de obra bien formada y una cadena de suministro bien organizada. Hay muchos fabricantes que siguen las normas de calidad internacionales y ofrecen soluciones personalizadas con plazos de entrega muy rápidos.
2. ¿Cómo benefician las empresas chinas de moldeo por inyección a las industrias?
Todas estas industrias han dependido del moldeo por inyección chino, como la automoción, la electrónica, los dispositivos médicos, los envases y los bienes de consumo. Los fabricantes chinos pueden producir de forma eficaz y más barata los componentes de plástico de alta precisión necesarios para estas industrias.
3. ¿Cómo garantizan la calidad del producto las empresas chinas de moldeo por inyección?
Las empresas fiables de moldeo de China controlan estrictamente la calidad desde las materias primas hasta los productos acabados y obtienen los siguientes certificados: ISO 9001, ISO 13485 (médico) e IATF 16949 (piezas de automóvil). El nivel de sus procesos de prueba y sus sistemas de inspección automatizados les permiten alcanzar altos niveles de exigencia.
4. ¿Qué es una selección de fabricantes chinos de molduras?
Las empresas deben tener en cuenta las certificaciones de calidad, la experiencia, la capacidad de producción, la protección de la propiedad intelectual y la capacidad de comunicación y apoyo logístico. Para allanar el camino hacia una buena asociación, deben realizarse pruebas de muestras y garantizar la capacidad de entrega de la empresa.
5. ¿Cuál es la perspectiva de la industria china de moldeo por inyección?
Los tiempos que corren exigen que la industria encuentre nuevas tendencias para resolverlo, como los plásticos sostenibles y biodegradables, la automatización impulsada por IA, las fábricas inteligentes y la producción bajo demanda. Estos avances harán que la fabricación sea más eficiente, se desperdicie menos y se abastezca la demanda en continuo crecimiento de respuestas de fabricación respetuosas con el medio ambiente.