Co to jest plastikowa forma wtryskowa
Czym jest plastikowa forma wtryskowa?
Formowanie wtryskowe tworzyw sztucznych to jedna z najskuteczniejszych metod produkcji komponentów z tworzyw sztucznych, zapewniająca wysoki poziom precyzji i wydajności produkcji. Proces ten polega na topieniu tworzyw sztucznych i wtryskiwaniu ich do wstępnie zaprojektowanej formy, która po schłodzeniu kształtuje plastik do określonej formy. Ten artykuł zagłębia się w podstawy form wtryskowych z tworzyw sztucznych, szczegółowo opisując typy, komponenty, procesy produkcyjne i kwestie związane z wyborem odpowiedniej formy do konkretnych potrzeb produkcyjnych.
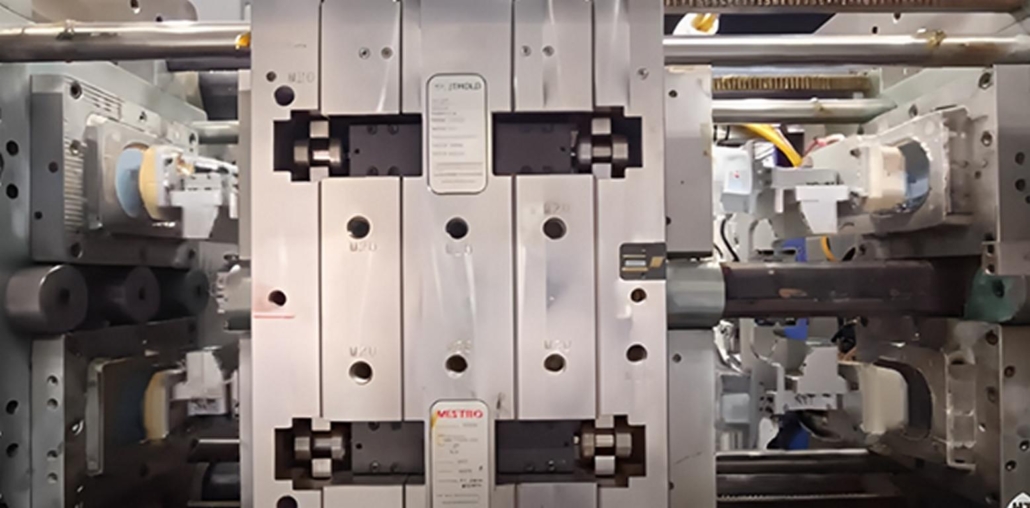
Wprowadzenie do formowania wtryskowego tworzyw sztucznych
Formowanie wtryskowe tworzyw sztucznych to technika wykorzystywana do tworzenia skomplikowanych, precyzyjnych części z tworzyw sztucznych w dużych ilościach. Od czasu jej opracowania pod koniec XIX wieku, proces ten przekształcił przemysł wytwórczy, umożliwiając szybką produkcję części w wielu sektorach, w tym motoryzacyjnym, elektronicznym, urządzeń medycznych i towarów konsumpcyjnych.
Zalety formowania wtryskowego tworzyw sztucznych
- Wysoka wydajność i szybkość: Formowanie wtryskowe oferuje krótki czas cyklu produkcyjnego, pozwalając na szybkie tempo produkcji. Wiele form może pracować jednocześnie, aby jeszcze bardziej zwiększyć wydajność.
- Powtarzalność: Proces ten został zaprojektowany do tworzenia identycznych części w wielu seriach produkcyjnych, co jest szczególnie cenne w branżach wymagających wysokiej precyzji i spójności.
- Złożone możliwości projektowania: Formy wtryskowe są w stanie tworzyć skomplikowane geometrie, w tym cienkie ścianki, podcięcia i złożone detale powierzchni.
- Elastyczność materiału: Formowanie wtryskowe może wykorzystywać szeroką gamę tworzyw termoplastycznych i termoutwardzalnych, z których każdy jest wybierany w celu zapewnienia określonych właściwości gotowego produktu.
- Minimalna ilość odpadów: Dzięki odpowiednio zaprojektowanym formom i zaawansowanej kontroli procesu, formowanie wtryskowe wytwarza niewiele lub nie wytwarza żadnych odpadów materiałowych.
Przegląd form wtryskowych z tworzyw sztucznych
A plastikowa forma wtryskowa to złożone narzędzie zaprojektowane do kształtowania stopionego tworzywa sztucznego w gotowy produkt. Forma jest zwykle wykonana ze stali lub aluminium i składa się z dwóch podstawowych połówek: wnęki i rdzenia, z których każda jest odpowiedzialna za formowanie zewnętrznej i wewnętrznej części końcowej. Ze względu na wysokie ciśnienie związane z formowaniem wtryskowym, formy te muszą być wytrzymałe, odporne na zużycie i zdolne do utrzymania swojego kształtu w powtarzających się cyklach.
Każda forma wtryskowa zawiera wiele części, które współpracują ze sobą, aby zapewnić precyzję formowania, chłodzenia i wyrzucania części. Poniżej znajduje się zestawienie kluczowych elementów formy wtryskowej i ich odpowiednich funkcji.
Kluczowe elementy formy
- Wnęka i rdzeń formy wtryskowej: Są to podstawowe elementy formy. Strona wnęki (zazwyczaj strona "A") jest odpowiedzialna za kształtowanie zewnętrznej powierzchni części, podczas gdy strona rdzenia (strona "B") kształtuje wnętrze. Razem tworzą one pustą przestrzeń, która definiuje geometrię części. Wybór materiałów wnęki i rdzenia zależy od wielkości produkcji, ponieważ materiały o wysokiej odporności na zużycie, takie jak hartowana stal, są często używane do produkcji wielkoseryjnej, podczas gdy bardziej miękkie metale mogą wystarczyć do mniejszych serii.
- Suwaki i podnośniki: Suwaki oraz podnośniki umożliwiają tworzenie podcięć lub złożonych geometrii, których nie można uformować za pomocą prostej formy dwuczęściowej. Suwaki poruszają się na boki, gdy forma się otwiera, tworząc miejsce na wszelkie występy lub rowki, podczas gdy podnośniki wysuwają się pod kątem, aby uwolnić część. Oba te elementy mają zasadnicze znaczenie dla umożliwienia wyrzucania części o złożonych kształtach bez ich uszkodzenia.
- Systemy wlewów, prowadnic i bramek: The wlew kieruje roztopione tworzywo sztuczne z dyszy wtryskarki do formy, prowadząc je do biegacz system, który kieruje tworzywo sztuczne do każdego gniazda w formie wielogniazdowej. Bramki są końcowymi punktami wejścia stopionego tworzywa sztucznego do gniazda, gdzie stygnie i nabiera kształtu. Każdy element tego systemu wpływa na to, jak równomiernie i szybko tworzywo wypełnia formę, wpływając na jakość części i czas cyklu.
- System wyrzutnika: Po ostygnięciu i zestaleniu uformowanej części system wyrzutnika wypycha część z gniazda formy. System wypychacza często zawiera sworznie lub płyty, które wywierają siłę na część od strony rdzenia, zapewniając jej uwolnienie bez uszkodzeń. System ten musi być precyzyjnie taktowany i kontrolowany, aby zapobiec deformacji lub przywieraniu części.
- Kanały chłodzące: Kanały chłodzące to kanały w płytach formy, które przenoszą chłodziwo, zwykle wodę, w celu pochłaniania i rozpraszania ciepła ze stopionego tworzywa sztucznego. Wydajne chłodzenie ma kluczowe znaczenie dla procesu formowania, ponieważ skraca czas cyklu i wpływa na dokładność wymiarową i właściwości mechaniczne części. Konstrukcja kanałów chłodzących - konforemnych, przegrodowych lub bąbelkowych - może znacząco wpłynąć na wydajność i efektywność formy.
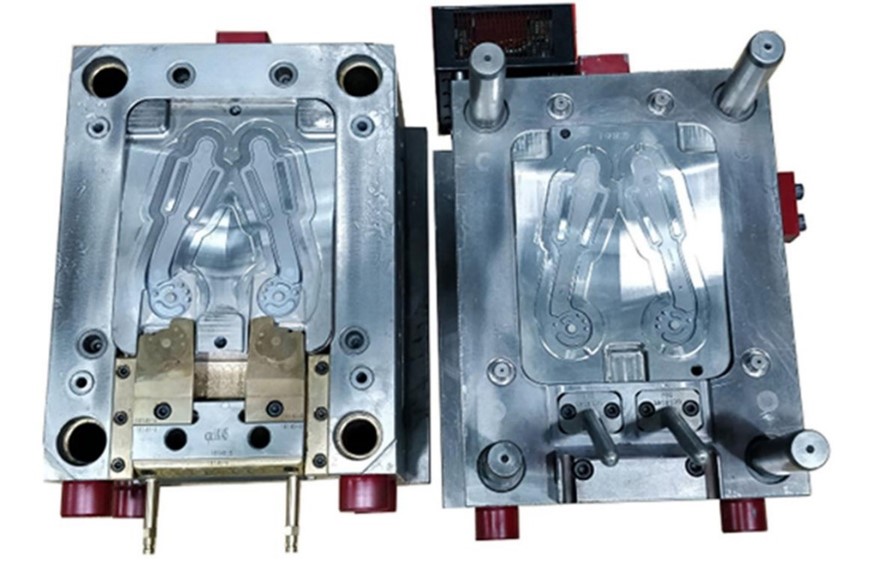
Struktura plastikowej formy wtryskowej
Struktura plastikowej formy wtryskowej została zaprojektowana tak, aby wytrzymać ciśnienie, temperaturę i naprężenia mechaniczne powtarzających się cykli formowania. Oto bliższe spojrzenie na elementy konstrukcyjne i ich działanie w procesie formowania:
- Płyty A i B: Są to główne płyty formy, które utrzymują odpowiednio gniazdo i rdzeń. Płyta A jest nieruchoma, podczas gdy płyta B porusza się, aby otworzyć i zamknąć formę. Płyty te są zaprojektowane tak, aby utrzymać wyrównanie i wytrzymać ciśnienie wtrysku.
- Płytki zaciskowe: Płyty te zabezpieczają formę w jednostce zaciskowej wtryskarki. Ich konstrukcja musi zapewniać stabilność podczas fazy wtrysku pod wysokim ciśnieniem, aby zapobiec niewspółosiowości lub ruchom, które mogą powodować wady.
- Linia rozstania: Linia podziału to miejsce, w którym spotykają się płyty A i B. Dobrze wyrównana linia podziału jest niezbędna, aby zapobiec defektom, takim jak wypływki (cienkie warstwy plastiku na szwach formy) i zapewnić płynne uwalnianie części. Położenie linii podziału często zależy od projektu części i wymagań formy.
- Kanały chłodzące: Kanały chłodzące są integralną częścią utrzymania wydajności formy i skrócenia czasu cyklu. Kanały są starannie zaprojektowane, aby zapewnić równomierne chłodzenie w gnieździe formy i rdzeniu, co ma kluczowe znaczenie dla zapobiegania wadom, takim jak wypaczenia lub naprężenia wewnętrzne. Rodzaje kanałów chłodzących obejmują:
- Chłodzenie konforemne: Kanały, które podążają za konturem części, zapewniając spójne chłodzenie dopasowane do kształtu gniazda formy.
- Przegroda chłodząca: Wykorzystuje wkładki do kierowania przepływem chłodziwa i jest powszechnie stosowany, gdy rozmiar formy ogranicza umieszczenie kanału.
- Chłodzenie Bubbler: Rurki bąbelkowe zapewniają dodatkowe chłodzenie w określonych obszarach, szczególnie w przypadku grubych sekcji, które wymagają szybszego chłodzenia.
- Kołki chłodzące: Kołki osadzone w rdzeniu zapewniają miejscowe chłodzenie w grubych sekcjach, pomagając zarządzać rozkładem temperatury w większych lub wielokomorowych formach.
Konstrukcja chłodzenia ma duży wpływ na czas cyklu, a tym samym na koszt i wydajność procesu formowania wtryskowego.
Rodzaje plastikowych form wtryskowych
Istnieje kilka rodzajów form wtryskowych z tworzyw sztucznych, aby zaspokoić różne potrzeby produkcyjne, złożoność i wymagania dotyczące części. Oto niektóre z najczęściej używanych typów:
- Formy jednogniazdowe: Formy te produkują jedną część na cykl. Są one często używane do mniejszych ilości produkcji lub części o wysokiej precyzji, gdzie wymagana jest ściślejsza kontrola nad każdą pojedynczą częścią. Formy jednogniazdowe mają tę zaletę, że są prostsze w konfiguracji i bardziej opłacalne w przypadku ograniczonej produkcji.
- Formy wielokomorowe: W formach wielogniazdowych kilka identycznych gniazd umożliwia produkcję wielu części w jednym cyklu. Zwiększa to wydajność i jest idealne do produkcji wielkoseryjnej, skracając czas cyklu na część i ogólne koszty. Formy wielogniazdowe są jednak bardziej skomplikowane w projektowaniu i wymagają precyzyjnego wyważenia w systemie kanałów, aby zapewnić równomierne wypełnienie.
- Formy rodzinne: Formy rodzinne zawierają różne wnęki w jednej formie, co pozwala na produkcję różnych komponentów w jednym cyklu. Jest to szczególnie przydatne, gdy różne części muszą być formowane razem, na przykład w zespołach. Jednak zrównoważenie współczynnika wypełnienia części o różnych rozmiarach może być trudne i może prowadzić do wad, jeśli nie jest starannie zarządzane.
- Formy gorącokanałowe a zimnokanałowe:
- Formy do gorących kanałów: Wykorzystanie podgrzewanych komponentów do utrzymywania tworzywa sztucznego w stanie stopionym w systemie kanałów, co minimalizuje ilość odpadów i przyspiesza cykl. Gorące kanały są wydajne w produkcji wielkoseryjnej, ale wymagają starannej kontroli i wyższych kosztów początkowych.
- Formy do pracy na zimno: Tworzywo sztuczne w prowadnicy musi ostygnąć i zestalić się w każdym cyklu. Zestalony kanał jest zazwyczaj wyrzucany wraz z częścią, której usunięcie może wymagać wtórnej obróbki. Formy zimnokanałowe są prostsze i mniej kosztowne, dzięki czemu nadają się do produkcji na mniejszą skalę.
- Formy dwupłytowe i trójpłytowe:
- Formy dwupłytowe: Składają się z pojedynczej linii podziału i mają prostszą konstrukcję. Są one powszechnie stosowane do prostych części z wymaganiami dotyczącymi pojedynczej bramki.
- Formy trzypłytowe: Dołącz dodatkową płytę, tworząc dwie linie podziału. Pozwala to na zastosowanie bardziej złożonych systemów wlewowych, takich jak wlew centralny, co poprawia estetykę części i może ograniczyć obróbkę po formowaniu.
- Formy stosowe i obrotowe:
- Formy stosowe: Formy stosowe wykorzystują wiele poziomów wnęk, skutecznie podwajając lub potrajając wydajność produkcyjną bez zwiększania wymagań dotyczących siły zacisku maszyny. Są one korzystne w przypadku produkcji o bardzo dużej objętości, ale wymagają zaawansowanych maszyn i obsługi.
- Formy obrotowe: Formy obrotowe umożliwiają obtrysk i montaż w formie poprzez obracanie wnęk między stacjami. Są one często używane do części wielomateriałowych, takich jak te wymagające połączenia sztywnych i elastycznych tworzyw sztucznych.
Każdy rodzaj formy ma inne zalety i wyzwania, a wybór odpowiedniej zależy od takich czynników, jak wielkość produkcji, złożoność części i wymagania materiałowe.

Proces formowania wtryskowego tworzyw sztucznych
Proces formowania wtryskowego składa się z kilku kluczowych etapów, z których każdy ma kluczowe znaczenie dla produkcji wysokiej jakości części. Oto szczegółowy podział:
- Zaciskanie: Forma jest mocno zaciśnięta, aby przygotować się do wtrysku stopionego tworzywa sztucznego. Siła zacisku jest obliczana na podstawie ciśnienia w gnieździe, aby zapewnić, że tworzywo sztuczne nie wycieknie przez linię podziału.
- Wstrzyknięcie: Stopione tworzywo sztuczne jest wtryskiwane do gniazda formy przez wlew, kanał i zasuwę. Prędkość wtrysku, ciśnienie i temperatura muszą być precyzyjnie kontrolowane, ponieważ wpływają na przepływ i jakość materiału we wnęce.
- Chłodzenie: Chłodzenie rozpoczyna się, gdy tylko tworzywo sztuczne wejdzie do formy. Szybkość chłodzenia musi być równomierna, aby uniknąć wad, takich jak wypaczenie lub skurcz. Kanały chłodzące odgrywają tutaj istotną rolę, zapewniając skuteczne odprowadzanie ciepła z formy. Ten etap często stanowi największą część czasu cyklu.
- Wyrzut: Po zestaleniu się części, kołki wypychacza lub płyty wypychają część z formy. Wypychanie należy wykonywać ostrożnie, aby uniknąć uszkodzenia części, zwłaszcza jeśli ma ona złożone cechy lub jest wykonana z kruchego materiału.
Każdy etap procesu formowania wtryskowego wymaga precyzyjnej kontroli, aby produkować części spełniające standardy jakości przy jednoczesnej minimalizacji czasu cyklu i kosztów produkcji.
Kanały chłodzące do form wtryskowych
Kanały chłodzące mają kluczowe znaczenie w procesie formowania wtryskowego tworzyw sztucznych, ponieważ znacząco wpływają na czas cyklu, jakość części i wydajność produkcji. Odpowiednia konstrukcja chłodzenia jest niezbędna, aby uniknąć wad, takich jak wypaczanie, kurczenie się lub naprężenia wewnętrzne, które mogą wystąpić, jeśli chłodzenie jest nierównomierne lub zbyt szybkie.
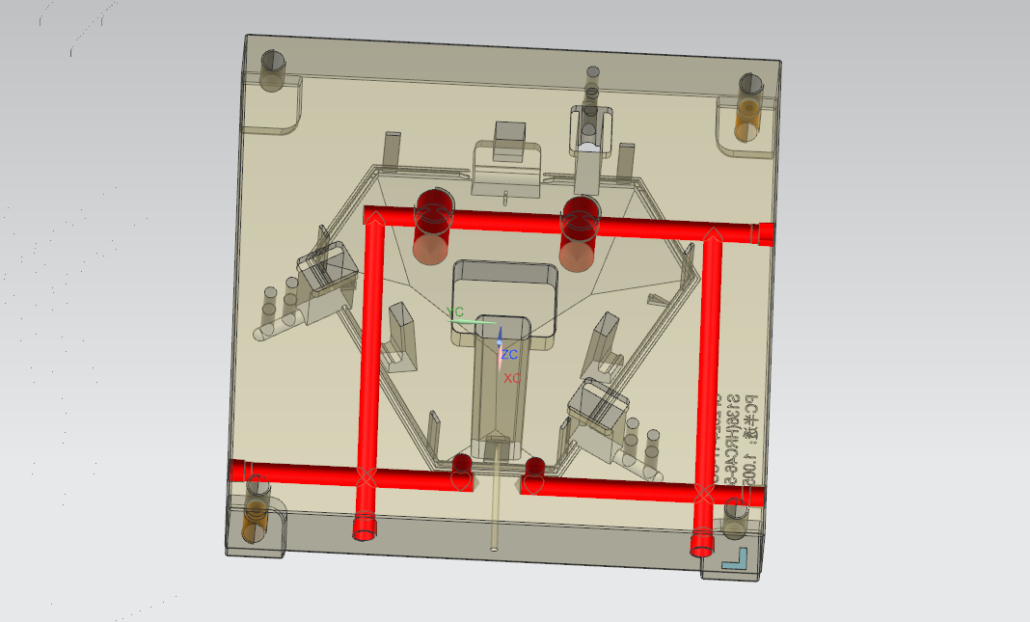
Rodzaje kanałów chłodzących w formach wtryskowych
- Chłodzenie konforemne: Ta zaawansowana technika obejmuje projektowanie kanałów chłodzących, które podążają za konturem części w formie. Chłodzenie konformalne zapewnia spójne chłodzenie na całej powierzchni części, skracając czas cyklu i poprawiając jakość części. Chłodzenie konforemne, zwykle osiągane za pomocą druku 3D i innych zaawansowanych metod produkcji, jest idealne do złożonych kształtów, w których tradycyjne kanały byłyby nieskuteczne.
- Proste kanały chłodzące: Kanały te są prostymi, prostymi ścieżkami wywierconymi w płytach formy. Chociaż są one proste i opłacalne, są mniej wydajne niż chłodzenie konformalne w złożonych geometriach form. Proste kanały są często używane w standardowych formach, gdzie równomierne chłodzenie jest bardziej osiągalne.
- Przegroda chłodząca: Przegrody to płaskie wkładki, które przekierowują przepływ chłodziwa wewnątrz formy, szczególnie w ciasnych przestrzeniach, do których nie docierają proste kanały. Chłodzenie przegrodowe jest skuteczne w zarządzaniu temperaturą w mniejszych formach lub określonych obszarach, ale może nie zapewniać równomiernego chłodzenia niezbędnego w przypadku bardzo złożonych projektów.
- Chłodzenie Bubbler: Bubblery to rurki, które cyrkulują chłodziwo w małych, ograniczonych obszarach formy, co jest szczególnie korzystne w przypadku grubych sekcji części, które wymagają szybszego chłodzenia. Bubblery są powszechnym wyborem, gdy tradycyjne kanały nie mogą zapewnić wystarczającego chłodzenia dla gęstych obszarów.
- Kołki chłodzące: Kołki chłodzące są wkładane do rdzenia formy, aby pomóc w chłodzeniu grubszych części. Kołki te są idealne do miejscowego chłodzenia w większych formach lub określonych obszarach podatnych na przegrzanie. Są one również powszechnie stosowane w formach wielogniazdowych, gdzie utrzymanie stałej temperatury jest wyzwaniem.
Wpływ konstrukcji kanału chłodzącego na czas cyklu i jakość
Konstrukcja kanałów chłodzących wpływa zarówno na wydajność, jak i jakość procesu formowania wtryskowego:
- Redukcja czasu cyklu: Wydajne kanały chłodzące pomagają skrócić czas cyklu, ponieważ części chłodzą się i krzepną szybciej. Krótszy czas cyklu oznacza wyższą wydajność produkcji i niższe koszty produkcji.
- Dokładność wymiarowa: Konsekwentne chłodzenie w całej formie pomaga zapobiegać wypaczaniu lub kurczeniu się, zapewniając, że części zachowują zamierzony kształt i wymiary.
- Wykończenie powierzchni: Chłodzenie może wpływać na jakość powierzchni formowanych części. Równomierne chłodzenie minimalizuje naprężenia, które w przeciwnym razie mogłyby uszkodzić powierzchnię części, co skutkuje lepszym wykończeniem.
Właściwa konstrukcja kanału chłodzącego jest istotnym czynnikiem podczas fazy projektowania formy, ponieważ decyduje o wydajności formy i jakości formowanych części.
Wady i problemy związane z formowaniem wtryskowym
Pomimo precyzji formowania wtryskowego, może wystąpić kilka typowych wad. Zrozumienie tych kwestii i sposobów ich łagodzenia jest niezbędne do utrzymania jakości i zminimalizowania ilości odpadów.
Typowe wady formowania wtryskowego
- Wypaczenie: Wypaczenie to deformacja, która występuje, gdy różne części formy chłodzą się w nierównym tempie. Wada ta często pojawia się w złożonych formach z nieodpowiednimi kanałami chłodzącymi lub niewystarczającym czasem chłodzenia. Aby zapobiec wypaczaniu, kanały chłodzące powinny być zaprojektowane tak, aby zapewnić równomierne chłodzenie, a czas chłodzenia powinien być dokładnie monitorowany.
- Znaki zlewu: Ślady zapadnięć pojawiają się jako wgłębienia na powierzchni grubszych części, zazwyczaj z powodu niewłaściwego chłodzenia lub niewystarczającego docisku. Stosowanie optymalnego ciśnienia i zapewnienie odpowiedniego chłodzenia, zwłaszcza w grubych obszarach, może pomóc w zapobieganiu powstawania śladów zacieków.
- Flash: Błysk występuje, gdy stopione tworzywo sztuczne wydostaje się z wnęki na linii podziału z powodu nadmiernego ciśnienia wtrysku lub niewspółosiowości. Precyzyjne wyrównanie i odpowiednie ustawienia ciśnienia mają kluczowe znaczenie dla zapobiegania wypływowi.
- Linie przepływu: Linie przepływu to widoczne linie na powierzchni części spowodowane zmianami szybkości chłodzenia tworzywa sztucznego podczas jego przepływu przez formę. Regulacja prędkości wtrysku i temperatury może pomóc w zmniejszeniu linii przepływu.
- Krótkie ujęcia: Krótkie strzały zdarzają się, gdy gniazdo formy nie jest całkowicie wypełnione, często z powodu niskiego ciśnienia wtrysku lub niewystarczającej ilości materiału. Zwiększenie ciśnienia wtrysku lub zapewnienie wystarczającej ilości materiału może rozwiązać ten problem.
- Linie spawania: Linie zgrzewu występują w miejscach, w których spotykają się dwa fronty przepływu, często tworząc słabe punkty w części. Dostosowanie prędkości wtrysku lub użycie systemu gorących kanałów może zredukować linie zgrzewu.
- Kruchość i pękanie: Problemy te zazwyczaj wynikają z niewłaściwego chłodzenia lub zbyt wysokiego ciśnienia wtrysku, które wywołuje naprężenia wewnętrzne. Właściwy projekt chłodzenia i optymalna kontrola ciśnienia pomagają złagodzić kruchość i pękanie.
Rozumiejąc i kontrolując te czynniki - takie jak prędkość wtrysku, temperatura i konstrukcja chłodzenia - producenci mogą zmniejszyć liczbę wad i poprawić ogólną jakość formowanych części.
Proces produkcji form wtryskowych
Produkcja formy wtryskowej obejmuje wiele etapów, z których każdy jest niezbędny do zapewnienia trwałości, precyzji i funkcjonalności formy. Oto zestawienie typowych etapów produkcji form wtryskowych z tworzyw sztucznych:

- Projektowanie i inżynieria: Faza projektowania formy jest kluczowa, ponieważ stanowi podstawę dla wszystkich kolejnych kroków. Korzystając z oprogramowania CAD, inżynierowie tworzą model 3D formy, zawierający wszystkie niezbędne szczegóły, w tym kształt wnęki, kanały chłodzące, system wypychania i linię podziału. Model ten jest następnie poddawany symulacjom w celu przewidzenia problemów i optymalizacji wydajności przed rozpoczęciem fizycznej produkcji formy.
- Wybór materiału: W zależności od wielkości produkcji i wymagań dotyczących części, materiały są wybierane pod kątem trwałości i odporności na zużycie. Typowe materiały obejmują hartowaną stal do form o dużej objętości i aluminium do zastosowań o mniejszej objętości. Formy stalowe są preferowane w przypadku długich serii ze względu na ich trwałość, podczas gdy formy aluminiowe są łatwiejsze w obróbce i opłacalne w przypadku produkcji krótkoseryjnej.
- Obróbka CNC i EDM (obróbka elektroerozyjna): Obróbka CNC (Computer Numerical Control) jest wykorzystywana do precyzyjnego wycinania pierwotnego kształtu formy. EDM jest następnie wykorzystywana do tworzenia złożonych geometrii, drobnych detali i skomplikowanych kształtów w gnieździe formy, których maszyny CNC nie są w stanie osiągnąć. Połączenie CNC i EDM zapewnia zarówno dokładność, jak i złożoność wymaganą dla formy.
- Obróbka cieplna i hartowanie powierzchniowe: Formy stalowe są często poddawane obróbce cieplnej w celu zwiększenia twardości i trwałości. Obróbka powierzchni, taka jak azotowanie lub chromowanie, jest również stosowana w celu zwiększenia odporności na zużycie, zmniejszenia korozji i wydłużenia żywotności formy. Formy aluminiowe, choć bardziej miękkie, mogą być również poddawane anodyzacji w celu poprawy twardości powierzchni.
- Montaż i polerowanie: Po obróbce elementy formy są montowane, w tym dopasowanie wnęki, rdzenia, kołków wypychacza, suwaków i kanałów chłodzących. Precyzyjne polerowanie jest następnie stosowane w celu uzyskania wysokiej jakości wykończenia powierzchni, szczególnie w przypadku części wymagających estetycznej lub gładkiej powierzchni.
- Testowanie i walidacja: Przed pełną produkcją, forma przechodzi próbne uruchomienie, aby upewnić się, że spełnia specyfikacje. Ten krok, znany jako próbkowanie T1, testuje wydajność formy, identyfikując potencjalne problemy z chłodzeniem, wyrzutem lub wyrównaniem. Wszelkie korekty są wprowadzane w celu optymalizacji wydajności formy do masowej produkcji.
- Zapewnienie i zatwierdzanie jakości: Po walidacji forma jest sprawdzana w celu potwierdzenia, że spełnia wszystkie standardy jakości. Wykonywane są pomiary w celu zweryfikowania dokładności wymiarowej, a w razie potrzeby dokonywane są korekty. Dopiero po przejściu kontroli jakości forma jest zatwierdzana do pełnej produkcji.
Każdy etap procesu produkcji form ma kluczowe znaczenie dla zapewnienia, że końcowa forma będzie działać konsekwentnie i wydajnie w środowiskach produkcji wielkoseryjnej.
Wybór odpowiedniej formy wtryskowej do danego zastosowania
Wybór odpowiedniej formy wtryskowej ma kluczowe znaczenie dla optymalizacji produkcji, minimalizacji kosztów i zapewnienia jakości produktu. Oto kilka kluczowych czynników, które należy wziąć pod uwagę przy wyborze formy wtryskowej:
- Wielkość produkcji: Przewidywana wielkość produkcji odgrywa znaczącą rolę przy wyborze formy. Produkcja wielkoseryjna zazwyczaj wymaga trwałych form wykonanych z hartowanej stali, podczas gdy formy aluminiowe nadają się do krótkich serii lub prototypowania.
- Złożoność i projektowanie części: Złożone części o skomplikowanej geometrii, podcięciach lub cienkich ściankach mogą wymagać specjalistycznych funkcji formy, takich jak podnośniki, suwaki lub konfiguracje z wieloma gniazdami. Im bardziej złożona część, tym bardziej szczegółowa musi być forma, co może mieć wpływ zarówno na koszty, jak i czas produkcji.
- Wybór materiału: Różne tworzywa sztuczne mają unikalną charakterystykę płynięcia, kurczenia się i chłodzenia. Formy zaprojektowane do sztywnych materiałów, takich jak poliwęglan, mogą wymagać innych konfiguracji chłodzenia lub materiałów formy niż formy zaprojektowane do elastycznych tworzyw sztucznych, takich jak polietylen.
- Wymagania dotyczące czasu cyklu: Krótkie czasy cykli są niezbędne w produkcji wielkoseryjnej. Dobrze zaprojektowana forma z wydajnymi kanałami chłodzenia i optymalnym systemem wyrzucania może skrócić czas cyklu, zwiększając przepustowość i obniżając koszty.
- Rozważania dotyczące kosztów: Formy to inwestycja długoterminowa, a koszty mogą się znacznie różnić w zależności od materiału, złożoności i typu formy. Chociaż formy wielogniazdowe lub gorącokanałowe mogą być początkowo droższe, w dłuższej perspektywie mogą zapewnić oszczędności dzięki zwiększeniu wydajności i zmniejszeniu ilości odpadów.
- Długowieczność formy: W przypadku produkcji wielkoseryjnej lub ciągłej formy muszą być zaprojektowane z myślą o długiej żywotności przy użyciu trwałych materiałów i obróbce powierzchni. Cechy takie jak utwardzanie i powlekanie pomagają zapewnić, że forma wytrzyma wielokrotne użytkowanie bez zużycia lub degradacji.
Starannie oceniając te czynniki, producenci mogą wybrać odpowiednią formę, aby osiągnąć swoje cele produkcyjne, utrzymać jakość części i zmaksymalizować efektywność kosztową.
Wnioski
Formowanie wtryskowe tworzyw sztucznych Formy wtryskowe są kamieniem węgielnym nowoczesnej produkcji, umożliwiając wytwarzanie precyzyjnych, wysokiej jakości części z tworzyw sztucznych przy niskich kosztach i dużej prędkości. Zrozumienie różnych aspektów form wtryskowych - od komponentów, typów i procesu produkcyjnego po konstrukcję chłodzenia i potencjalne problemy - zapewnia cenny wgląd w optymalizację produkcji.
Wybór odpowiedniej formy, wdrożenie skutecznych kanałów chłodzenia i utrzymanie rygorystycznej kontroli jakości może znacznie poprawić wydajność i jakość formowania wtryskowego tworzyw sztucznych. Pozwala to nie tylko sprostać wymaganiom produkcji wielkoseryjnej, ale także zapewnia, że formowane części spełniają wymagane specyfikacje i standardy estetyczne. Wraz z postępem w dziedzinie materiałów, projektowania form i technologii chłodzenia, formowanie wtryskowe tworzyw sztucznych wciąż ewoluuje, oferując jeszcze większy potencjał
Dodaj komentarz
Chcesz się przyłączyć do dyskusji?Zapraszamy do udziału!