What is Plastic Injection Mold?
Plastic injection molding is one of the most effective methods for manufacturing plastic components, providing high levels of precision and production efficiency. The process involves melting plastic materials and injecting them into a pre-designed mold that shapes the plastic into a specific form as it cools. This article delves into the essentials of plastic injection molds, detailing the types, components, manufacturing processes, and considerations for selecting the right mold to meet specific production needs.
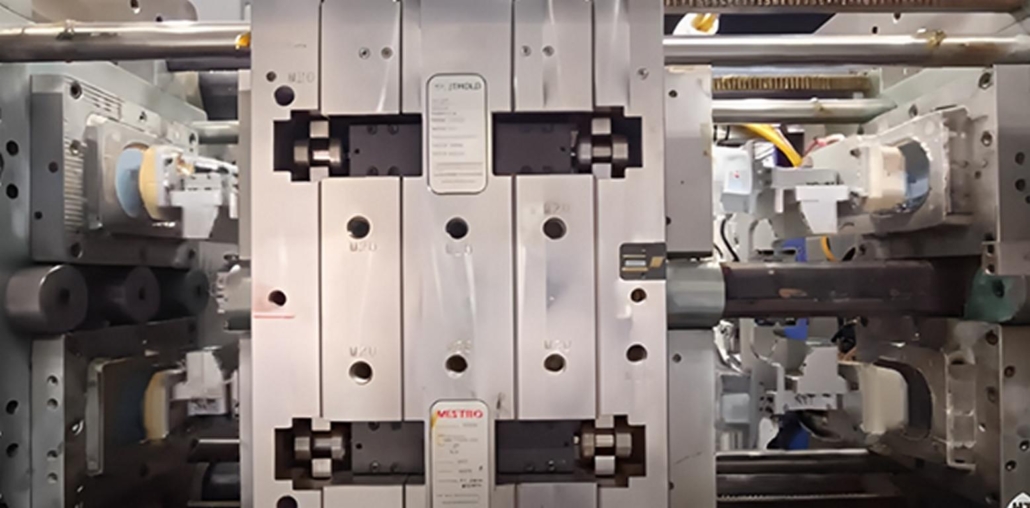
Introduction to Plastic Injection Molding
Plastic injection molding is a technique used to create intricate, precise plastic parts in large quantities. Since its development in the late 19th century, the process has transformed the manufacturing industry, allowing for the high-speed production of parts across a wide range of sectors including automotive, electronics, medical devices, and consumer goods.
Advantages of Plastic Injection Molding
- High Efficiency and Speed: Injection molding offers a short production cycle time, allowing for rapid production rates. Multiple molds can run simultaneously to further increase output.
- Repeatability: The process is designed to create identical parts over multiple production runs, which is especially valuable in industries requiring high precision and consistency.
- Complex Design Capabilities: Injection molds are capable of creating intricate geometries, including thin walls, undercuts, and complex surface details.
- Material Flexibility: Injection molding can use a wide variety of thermoplastics and thermosetting plastics, each chosen to provide specific properties to the finished product.
- Minimal Waste: With properly designed molds and advanced process controls, injection molding produces little to no material waste.
Overview of Plastic Injection Mold
A plastic injection mold is a complex tool designed to shape molten plastic material into a finished product. The mold is usually crafted from steel or aluminum and is composed of two primary halves: the cavity and core, each responsible for forming the exterior and interior of the final part. Due to the high pressures involved in injection molding, these molds must be robust, resistant to wear, and capable of maintaining their shape under repeated cycles.
Each mold includes multiple parts that work in unison to ensure precision in forming, cooling, and ejecting the part. Below is a breakdown of the key components of an injection mold and their respective functions.
Key Mold Components
- Injection Mold Cavity and Core: These are the primary elements of the mold. The cavity side (typically the “A” side) is responsible for shaping the exterior surface of the part, while the core side (the “B” side) shapes the interior. Together, they form the hollow space that defines the part geometry. The choice of cavity and core materials depends on the production volume, as high-wear materials such as hardened steel are often used for high-volume production, while softer metals may suffice for lower runs.
- Sliders and Lifters: Sliders and lifters allow for the creation of undercuts or complex geometries that cannot be formed with a straightforward two-part mold. Sliders move laterally when the mold opens, creating space for any protrusions or grooves, while lifters move out at an angle to release the part. Both are instrumental in allowing parts with complex shapes to be ejected without damage.
- Sprue, Runner, and Gate Systems: The sprue channels molten plastic from the injection machine nozzle into the mold, leading it to the runner system that directs the plastic to each cavity in a multi-cavity mold. Gates are the final entry points for the molten plastic into the cavity, where it cools and takes shape. Each component of this system affects how evenly and quickly the material fills the mold, influencing part quality and cycle time.
- Ejector System: After the molded part has cooled and solidified, the ejector system pushes the part out of the mold cavity. The ejector system often includes pins or plates that apply force to the part from the core side, ensuring it releases without damage. This system must be precisely timed and controlled to prevent deformation or sticking of the part.
- Cooling Channels: Cooling channels are passages within the mold plates that carry coolant, usually water, to absorb and dissipate heat from the molten plastic. Efficient cooling is crucial to the molding process, as it reduces cycle time and affects the dimensional accuracy and mechanical properties of the part. The design of the cooling channels—whether conformal, baffle, or bubbler channels—can significantly impact the performance and efficiency of the mold.
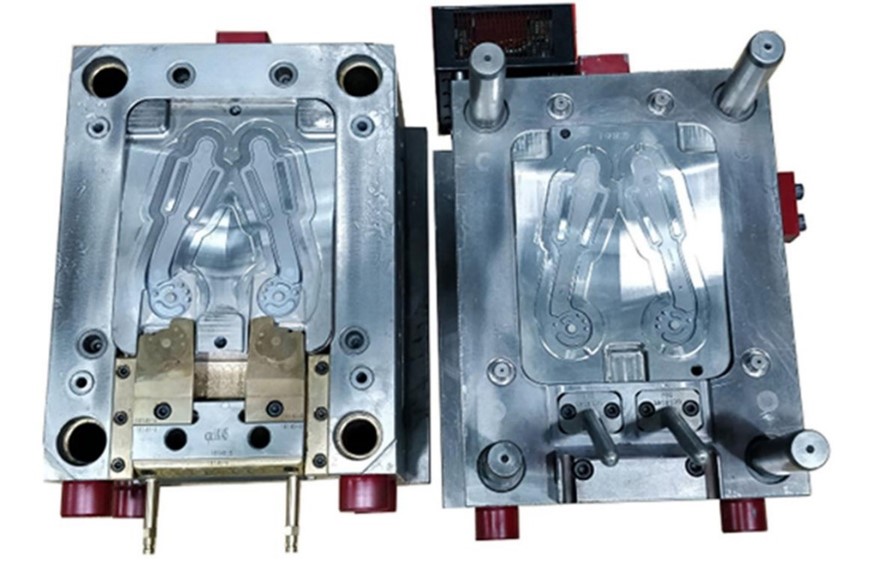
Structure of a Plastic Injection Mold
The structure of a plastic injection mold is designed to withstand the pressures, temperatures, and mechanical stresses of repeated molding cycles. Here is a closer look at the structural components and how they function within the molding process:
- A and B Plates: These are the main plates of the mold that hold the cavity and core, respectively. The A plate is stationary, while the B plate moves to open and close the mold. These plates are designed to maintain alignment and withstand the pressures of injection.
- Clamp Plates: These plates secure the mold within the clamping unit of the injection molding machine. Their design must ensure stability during the high-pressure injection phase to prevent misalignment or movement that could cause defects.
- Parting Line: The parting line is where the A and B plates meet. A well-aligned parting line is essential to prevent defects like flash (thin layers of plastic at the mold seams) and ensure smooth part release. The parting line location often depends on the design of the part and mold requirements.
- Cooling Channels: Cooling channels are integral to maintaining mold performance and reducing cycle times. Channels are carefully designed to ensure even cooling across the mold cavity and core, which is critical for preventing defects like warpage or internal stresses. Types of cooling channels include:
- Conformal Cooling: Channels that follow the contour of the part, providing consistent cooling that matches the shape of the mold cavity.
- Baffle Cooling: Uses inserts to guide the coolant flow and is commonly used when mold size limits channel placement.
- Bubbler Cooling: Bubbler tubes create additional cooling in specific areas, especially for thick sections that require faster cooling.
- Cooling Pins: Pins embedded in the core provide localized cooling in thick sections, helping manage temperature distribution in larger or multi-cavity molds.
The cooling design is highly influential on the cycle time and, by extension, the cost and productivity of the injection molding process.
Types of Plastic Injection Molds
Several types of plastic injection molds exist to accommodate varying production needs, complexities, and part requirements. Here are some of the most commonly used types:
- Single-Cavity Molds: These molds produce one part per cycle. They are often used for smaller production volumes or high-precision parts where tighter control is necessary over each individual part. Single-cavity molds have the advantage of simpler setup and are more cost-effective for limited production.
- Multi-Cavity Molds: In multi-cavity molds, several identical cavities allow for the production of multiple parts in a single cycle. This increases efficiency and is ideal for high-volume production, reducing cycle time per part and overall costs. However, multi-cavity molds are more complex to design and require precise balance in the runner system to ensure even filling.
- Family Molds: Family molds contain different cavities within a single mold, allowing for the production of various components in one cycle. This is particularly useful when different parts need to be molded together, such as in assemblies. However, balancing the fill rate across differently sized parts can be challenging and may lead to defects if not carefully managed.
- Hot Runner vs. Cold Runner Molds:
- Hot Runner Molds: Use heated components to keep the plastic molten within the runner system, minimizing waste and speeding up the cycle. Hot runners are efficient for high-volume production but require careful control and higher initial costs.
- Cold Runner Molds: Allow the plastic in the runner to cool and solidify with each cycle. The solidified runner is typically ejected with the part, which may require secondary processing to remove. Cold runner molds are simpler and less costly, making them suitable for lower-volume production.
- Two-Plate vs. Three-Plate Molds:
- Two-Plate Molds: These consist of a single parting line and are simpler in design. They are commonly used for straightforward parts with single-gate requirements.
- Three-Plate Molds: Include an additional plate, creating two parting lines. This allows for more complex gating systems, such as central gating, which improves part aesthetics and can reduce post-mold processing.
- Stack and Rotary Molds:
- Stack Molds: Stack molds use multiple levels of cavities, effectively doubling or tripling production capacity without increasing the machine’s clamp force requirements. They are advantageous for very high-volume production but require advanced machinery and handling.
- Rotary Molds: Rotary molds allow for overmolding and in-mold assembly by rotating cavities between stations. They are often used for multi-material parts, such as those requiring a combination of rigid and flexible plastics.
Each type of mold has distinct advantages and challenges, and selecting the right one depends on factors like production volume, part complexity, and material requirements.

Plastic Injection Molding Process
The injection molding process consists of several key steps, each critical to producing high-quality parts. Here’s a detailed breakdown:
- Clamping: The mold is clamped tightly to prepare for the injection of molten plastic. Clamping force is calculated based on the cavity pressure to ensure no plastic leaks through the parting line.
- Injection: Molten plastic is injected into the mold cavity through the sprue, runner, and gate. The injection speed, pressure, and temperature must be controlled precisely, as they affect the flow and quality of the material in the cavity.
- Cooling: Cooling begins as soon as the plastic enters the mold. The cooling rate must be uniform to avoid defects, such as warping or shrinkage. Cooling channels play a vital role here by ensuring that heat is effectively dissipated from the mold. This stage often accounts for the largest portion of the cycle time.
- Ejection: Once the part has solidified, ejector pins or plates push the part out of the mold. Ejection must be done carefully to avoid damaging the part, especially if it has complex features or is made of brittle material.
Each stage of the injection molding process requires precise control to produce parts that meet quality standards while minimizing cycle time and production costs.
Injection Mold Cooling Channels
Cooling channels are crucial in the plastic injection molding process, as they significantly influence cycle time, part quality, and production efficiency. Proper cooling design is essential to avoid defects like warping, shrinkage, or internal stresses that can occur if cooling is uneven or too rapid.
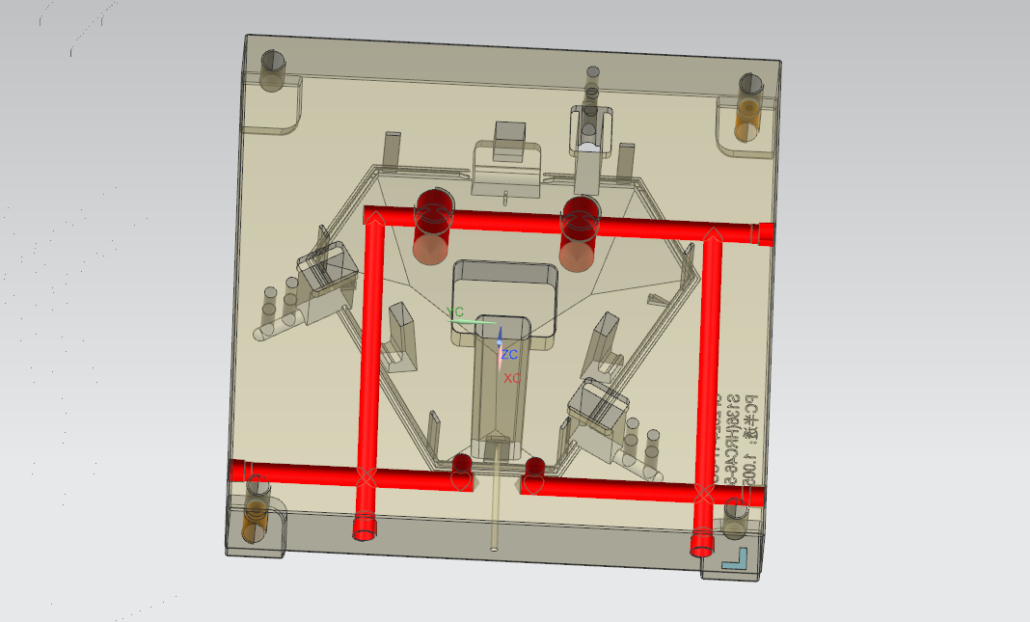
Types of Cooling Channels in Injection Molds
- Conformal Cooling: This advanced technique involves designing cooling channels that follow the contour of the part within the mold. Conformal cooling provides consistent cooling across the entire part surface, reducing cycle time and improving part quality. Typically achieved through 3D printing and other advanced manufacturing methods, conformal cooling is ideal for complex shapes where traditional channels would be ineffective.
- Straight Cooling Channels: These channels are simple, straight paths drilled into the mold plates. While straightforward and cost-effective, they are less efficient than conformal cooling in complex mold geometries. Straight channels are often used in standard molds where even cooling is more achievable.
- Baffle Cooling: Baffles are flat inserts that redirect coolant flow within the mold, especially in tight spaces where straight channels cannot reach. Baffle cooling is efficient for managing temperature in smaller molds or specific areas but may not provide the uniform cooling necessary for highly complex designs.
- Bubbler Cooling: Bubblers are tubes that circulate coolant within small, confined areas of the mold, particularly beneficial for thick sections of a part that require faster cooling. Bubblers are a common choice when traditional channels cannot provide sufficient cooling for dense areas.
- Cooling Pins: Cooling pins are inserted into the mold core to aid in cooling thicker parts. These pins are ideal for localized cooling in larger molds or specific areas prone to overheating. They are also commonly used in multi-cavity molds, where maintaining consistent temperatures is challenging.
The Impact of Cooling Channel Design on Cycle Time and Quality
The design of cooling channels impacts both the efficiency and quality of the injection molding process:
- Cycle Time Reduction: Efficient cooling channels help shorten the cycle time, as parts cool and solidify faster. Shorter cycle times mean higher production output and lower manufacturing costs.
- Dimensional Accuracy: Consistent cooling across the mold helps prevent warping or shrinkage, ensuring parts maintain their intended shape and dimensions.
- Surface Finish: Cooling can affect the surface quality of molded parts. Uniform cooling minimizes stresses that might otherwise mar the part’s surface, resulting in a better finish.
Proper cooling channel design is an essential consideration during the mold design phase, as it determines the mold’s efficiency and the quality of the molded parts.
Injection Molding Defects and Issues
Despite the precision of injection molding, several common defects can occur. Understanding these issues and how to mitigate them is essential for maintaining quality and minimizing waste.
Common Injection Molding Defects
- Warping: Warping is a deformation that occurs when different parts of the mold cool at uneven rates. This defect often arises in complex molds with inadequate cooling channels or insufficient cooling time. To prevent warping, the cooling channels should be designed to ensure even cooling, and cooling time should be carefully monitored.
- Sink Marks: Sink marks appear as depressions on the surface of thicker sections of a part, typically due to improper cooling or inadequate holding pressure. Using optimal pressure and ensuring adequate cooling, especially in thick areas, can help prevent sink marks.
- Flash: Flash occurs when molten plastic escapes from the cavity at the parting line due to excessive injection pressure or misalignment. Precise alignment and proper pressure settings are crucial to prevent flash.
- Flow Lines: Flow lines are visible lines on the surface of a part caused by variations in the plastic’s cooling rate as it flows through the mold. Adjusting injection speed and temperature can help reduce flow lines.
- Short Shots: Short shots happen when the mold cavity isn’t completely filled, often due to low injection pressure or insufficient material. Increasing the injection pressure or ensuring a sufficient feed of material can address this issue.
- Weld Lines: Weld lines occur where two flow fronts meet, often creating weak spots in the part. Adjusting the injection speed or using a hot runner system can reduce weld lines.
- Brittleness and Cracking: These issues typically result from improper cooling or overly high injection pressure, which induces internal stresses. Proper cooling design and optimal pressure control help mitigate brittleness and cracking.
By understanding and controlling these factors—such as injection speed, temperature, and cooling design—manufacturers can reduce defects and improve the overall quality of molded parts.
Injection Mold Manufacturing Process
The manufacturing of an injection mold involves multiple steps, each essential for ensuring the mold’s durability, precision, and functionality. Here’s a breakdown of the typical steps in manufacturing a plastic injection mold:

- Design and Engineering: The mold design phase is crucial as it lays the foundation for all subsequent steps. Using CAD software, engineers create a 3D model of the mold, incorporating all necessary details, including cavity shape, cooling channels, ejection system, and parting line. This model is then subjected to simulations to predict issues and optimize performance before physical mold production begins.
- Material Selection: Depending on the production volume and part requirements, materials are selected for durability and wear resistance. Common materials include hardened steel for high-volume molds and aluminum for lower-volume applications. Steel molds are preferred for long runs due to their durability, while aluminum molds are easier to machine and cost-effective for short-run production.
- CNC Machining and EDM (Electrical Discharge Machining): CNC (Computer Numerical Control) machining is used to carve out the mold’s primary shape with high precision. EDM is then employed for creating complex geometries, fine details, and intricate shapes in the mold cavity that CNC machines cannot achieve. The combination of CNC and EDM ensures both the accuracy and complexity required for the mold.
- Heat Treatment and Surface Hardening: Steel molds are often heat-treated to increase hardness and durability. Surface treatments, such as nitriding or chrome plating, are also applied to enhance wear resistance, reduce corrosion, and extend mold life. Aluminum molds, while softer, may also receive anodization to improve surface hardness.
- Assembly and Polishing: After machining, the mold components are assembled, including fitting the cavity, core, ejector pins, sliders, and cooling channels. Precision polishing is then applied to achieve a high-quality surface finish, especially for parts requiring an aesthetic or smooth surface.
- Testing and Validation: Before full production, the mold undergoes a trial run to ensure it meets specifications. This step, known as T1 sampling, tests the mold’s performance, identifying potential issues with cooling, ejection, or alignment. Any adjustments are made to optimize the mold’s performance for mass production.
- Quality Assurance and Approval: After validation, the mold is inspected to confirm it meets all quality standards. Measurements are taken to verify dimensional accuracy, and adjustments are made if necessary. Only after passing quality checks is the mold approved for full production.
Each step in the mold manufacturing process is critical to ensure that the final mold performs consistently and efficiently in high-volume production environments.
Choosing the Right Injection Mold for Your Application
Selecting the right injection mold is crucial to optimizing production, minimizing costs, and ensuring product quality. Here are some key factors to consider when choosing an injection mold:
- Production Volume: The anticipated production volume plays a significant role in mold selection. High-volume production typically requires durable molds made from hardened steel, while aluminum molds are suitable for short runs or prototyping.
- Part Complexity and Design: Complex parts with intricate geometries, undercuts, or thin walls may require specialized mold features like lifters, sliders, or multi-cavity configurations. The more complex the part, the more detailed the mold needs to be, which can impact both cost and production time.
- Material Choice: Different plastic materials have unique flow, shrinkage, and cooling characteristics. Molds designed for rigid materials like polycarbonate might require different cooling configurations or mold materials than molds designed for flexible plastics like polyethylene.
- Cycle Time Requirements: Fast cycle times are essential for high-volume production. A well-designed mold with efficient cooling channels and an optimal ejection system can reduce cycle time, increasing throughput and reducing costs.
- Cost Considerations: Molds are a long-term investment, and costs can vary significantly based on material, complexity, and mold type. While multi-cavity or hot runner molds can be more expensive initially, they may provide cost savings in the long run by increasing efficiency and reducing waste.
- Mold Longevity: For high-volume or continuous production, molds must be designed for longevity with durable materials and surface treatments. Features like hardening and coating help ensure that the mold withstands repeated use without wear or degradation.
By carefully evaluating these factors, manufacturers can select the right mold to meet their production goals, maintain part quality, and maximize cost-efficiency.
Conclusion
Plastic injection molding is a cornerstone of modern manufacturing, enabling the production of precise, high-quality plastic parts at a low cost and high speed. Understanding the various aspects of injection molds—from the components, types, and manufacturing process to the cooling design and potential issues—provides valuable insights into optimizing production.
Choosing the right mold, implementing effective cooling channels, and maintaining rigorous quality control can greatly enhance the efficiency and quality of plastic injection molding. This not only meets the demands of high-volume production but also ensures that the molded parts meet the required specifications and aesthetic standards. With advances in materials, mold design, and cooling technologies, plastic injection molding continues to evolve, offering even more potential