How Do You Mold ABS Plastic
Acrylonitrile Butadiene Styrene (ABS) plastic has long been a favorite material in manufacturing due to its balance of strength, durability, and versatility. As one of the most commonly used thermoplastics in plastic injection molding, ABS finds its way into countless products, ranging from automotive parts to electronic housings. This article explores the detailed process of molding ABS plastic, its unique properties, and tips for manufacturers and buyers looking to optimize production.

ABS Plastic Material: Properties and Benefits
ABS plastic is a terpolymer, combining three distinct monomers: acrylonitrile, butadiene, and styrene. This combination provides a synergy of properties that are difficult to achieve with other plastics.
Key Properties of ABS Plastic
- Strength and Durability: The butadiene component enhances impact resistance, making ABS ideal for protective housings and automotive parts.
- Thermal Stability: Acrylonitrile contributes to its ability to withstand high temperatures, with a heat deflection temperature ranging from 80°C to 100°C, depending on the grade.
- Chemical Resistance: ABS resists acids, alkalis, and many oils, which is essential for industrial and consumer applications.
- Lightweight and Machinable: Its low density makes it suitable for applications where weight reduction is critical, such as in transportation or portable electronics.
- Aesthetic Versatility: The styrene component gives ABS a glossy surface that is easy to paint, coat, or texture, making it attractive for consumer-facing products.
Common Grades of ABS
- General-Purpose ABS: Standard grade used in everyday applications like toys and household appliances.
- High-Impact ABS: Enhanced toughness, suitable for automotive and industrial uses.
- Flame-Retardant ABS: Used in electronics and environments where fire safety is critical.
- Transparent ABS: Offers clarity for specialized applications like lighting or displays.
By understanding these properties, manufacturers can tailor the ABS injection molding process to specific applications.
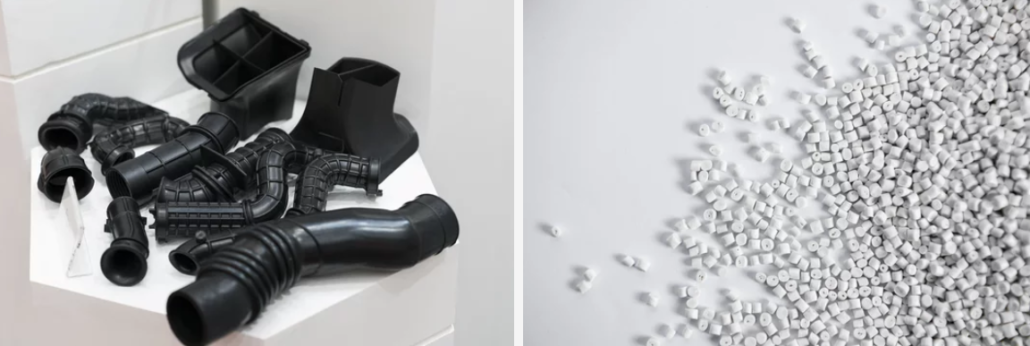
What is ABS Injection Molding?
ABS injection molding is a manufacturing process that involves injecting molten ABS plastic into a mold cavity to form a specific shape. Once cooled and solidified, the plastic takes the shape of the mold, resulting in a high-quality part.
Why Use Injection Molding for ABS?
- Scalability: Ideal for producing large quantities of identical parts.
- Complex Designs: Accommodates intricate geometries, undercuts, and thin walls.
- Consistency: Delivers precise dimensions and uniform quality across batches.
- Cost-Efficiency: While initial tooling costs are high, the per-part cost decreases with volume.
Step-by-Step Guide to ABS Injection Molding
The ABS injection molding process requires careful attention to detail to optimize material flow, cooling, and part quality. Here’s an in-depth look at each stage:
1. Material Preparation
Proper preparation begins with drying the ABS pellets. Moisture content above 0.1% can lead to splay marks, bubbles, and weak mechanical properties. Desiccant dryers are recommended, with typical settings at 80–90°C for 2–4 hours, depending on the pellet size and moisture level.
- Pro Tip: Use inline moisture analyzers to ensure pellets are sufficiently dried before processing.
2. Plasticizing
ABS pellets are fed into the barrel of the injection molding machine, where they are heated and melted. The screw mechanism ensures consistent mixing and heating. ABS typically melts between 220°C and 260°C.
- Challenges: Uneven heating can cause degradation or incomplete melting. Ensure the temperature zones of the barrel are set to match the grade of ABS being used.
3. Injection
The molten ABS is injected into the mold cavity at high pressure. Injection pressures range from 40 to 150 MPa, depending on the part design and material grade.
- Gate Design: Proper gate placement ensures uniform flow and minimizes cosmetic defects like weld lines. A fan or diaphragm gate is often preferred for ABS.
4. Packing and Holding
After injection, the material is subjected to holding pressure to prevent shrinkage and ensure the mold is fully filled. The holding time depends on the wall thickness of the part.
5. Cooling
Cooling is one of the most critical stages in ABS injection molding. The mold incorporates cooling channels to dissipate heat, typically using water as a coolant. Cooling time is influenced by part geometry, wall thickness, and mold temperature.
- Advanced Cooling Techniques: Conformal cooling channels created through additive manufacturing improve cooling efficiency and reduce cycle time.
6. Ejection
Once the part has solidified, ejector pins or a pneumatic system removes the part from the mold. To prevent deformation, draft angles of at least 1–2 degrees are recommended.
7. Post-Processing
After ejection, parts may require secondary operations like trimming, painting, or assembly. ABS is especially suited for secondary processes like ultrasonic welding, heat staking, and chroming due to its machinability and surface finish.
Tips for Molding High-Quality ABS Parts
Achieving defect-free ABS molded parts requires a combination of optimal process control and design considerations. Here are some actionable tips:
1. Design for Manufacturability
- Use uniform wall thickness to avoid warping and sink marks.
- Incorporate ribs instead of thicker walls for added strength without increasing cycle time.
- Position gates strategically to minimize flow lines and weld marks.
2. Fine-Tune Processing Parameters
- Melt temperature: 220°C–260°C.
- Mold temperature: 40°C–80°C, depending on the part’s desired finish.
- Injection speed: Moderate to prevent burn marks or flow hesitations.
3. Avoid Common Defects
- Splay Marks: Caused by moisture; ensure pellets are thoroughly dried.
- Warping: Use proper cooling channels and uniform wall thickness.
- Burn Marks: Reduce injection speed or adjust venting in the mold.
4. Use Advanced Technologies
- Hot Runner Systems: Reduce material waste and improve flow efficiency.
- Scientific Molding Techniques: Use data-driven analysis to optimize parameters and prevent defects.
Applications of ABS Plastic Injection Molding
ABS’s versatility makes it suitable for a wide range of applications:
- Automotive: Dashboards, trims, and protective housings.
- Electronics: Casings for devices, keyboards, and remote controls.
- Consumer Goods: Toys, luggage shells, and kitchen appliances.
- Medical Devices: Instrument panels and diagnostic equipment.
These applications benefit from ABS’s excellent mechanical properties, aesthetic appeal, and ability to undergo secondary processing.
Choosing an ABS Injection Molding Supplier
Selecting a reliable ABS injection molding supplier is vital for ensuring consistent quality and efficient production. Here’s what to look for:
1. Industry Expertise
Suppliers with experience in ABS materials understand its flow behavior, thermal properties, and post-processing requirements.
2. Technology and Equipment
Modern injection molding machines with precise controls for temperature, pressure, and speed are essential for high-quality ABS parts.
3. Quality Assurance
Look for ISO certifications, robust inspection processes, and a proven track record of defect-free production.
4. Design Support
Suppliers offering in-house design assistance can help optimize molds for manufacturability and performance.
5. Sustainable Practices
Eco-conscious suppliers recycle scrap ABS and use energy-efficient machinery to reduce environmental impact.

Challenges and Solutions in ABS Injection Molding
While ABS is versatile, it comes with its challenges:
- Moisture Sensitivity: Even slight moisture can degrade part quality. Invest in high-quality dryers and monitor moisture levels.
- Shrinkage: ABS has a shrinkage rate of 0.4–0.9%, which must be accounted for in mold design. Use simulation tools to predict shrinkage patterns.
- High Melt Viscosity: This can lead to poor flow in thin-walled parts. Adjust injection speed and pressure to ensure proper fill.
By working closely with an experienced supplier and leveraging advanced technologies, these challenges can be mitigated.
Advantages of Partnering with an ABS Injection Molding Supplier
Working with a specialized ABS injection molding supplier offers several benefits:
- Cost Efficiency: Optimized processes reduce production costs while maintaining quality.
- Design Support: Expert advice on mold design and material selection.
- Scalability: Capability to handle both prototype and mass production runs.
- Quick Turnaround: Efficient operations ensure timely delivery of parts.
Sustainability in ABS Injection Molding
Sustainability is becoming increasingly important in the manufacturing industry. Here’s how manufacturers can make ABS injection molding more eco-friendly:
- Recycled ABS: Use regrind material or post-consumer recycled ABS to reduce waste.
- Energy-Efficient Machines: Opt for hybrid or all-electric injection molding machines.
- Material Optimization: Minimize scrap by refining mold designs and using hot runner systems.
Conclusion
ABS plastic injection molding is a versatile and reliable process, capable of producing high-quality, durable, and aesthetically pleasing parts for a variety of applications. From understanding the properties of ABS to optimizing mold design and choosing the right supplier, every step plays a critical role in achieving success.
Whether you’re a product designer, manufacturer, or sourcing specialist, mastering the nuances of ABS molding will help you create parts that meet stringent quality standards while staying cost-effective. With advancements in molding technology and a growing emphasis on sustainability, ABS remains a leading material for modern manufacturing needs.
Leave a Reply
Want to join the discussion?Feel free to contribute!