I den hektiske helseverdenen er presisjon, renhet og etterlevelse ikke bare moteord, men et ufravikelig krav. En av de underliggende teknologiene som gjør det mulig å produsere trygt, effektivt og skalerbart medisinsk utstyr, er sprøytestøping av medisinsk plast. Sprøyter og katetre, kirurgiske instrumenter og diagnostikkhus får sin form gjennom sprøytestøping av plast, og sprøytestøping er en viktig del av den moderne medisinen ved å skape de enkelte komponentene.
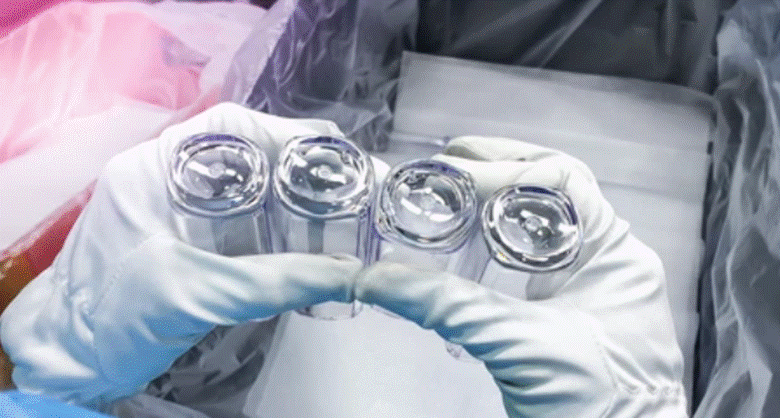
Det er viktig å velge en pålitelig produsent av medisinske sprøytestøpeformer. Den rette leverandøren garanterer at produktet ditt er i samsvar med strenge bransjestandarder, at det fungerer med ytterste presisjon, og at det forblir økonomisk i store produksjonskjøringer. En feil kan ha betydelige negative konsekvenser, for eksempel tilbakekalling av produkter, brudd på regelverket eller trusler mot pasientsikkerheten.
Denne artikkelen inneholder en liste over de 10 viktigste bedrifter som driver med sprøytestøping av medisinsk plast fra ulike deler av verden. Kriteriene for de børsnoterte selskapene er svært strenge, med utgangspunkt i sertifiseringer, innovasjon, deres globale tilstedeværelse og tidligere resultater. Til tross for at bransjen er global og involverer aktører fra mange regioner, har vi begrenset utvalget til kun to kinesiske selskaper, der Sincere Tech er ett av dem, mens resten er distribuert i USA, Europa og Israel.
Hva er medisinsk sprøytestøping av plast?
Det er en nisjeproduksjonsprosess som brukes til å produsere svært nøyaktige og høykvalitets plastkomponenter til medisinske og helsefaglige formål. Det innebærer at smeltet plast sprøytes inn i en spesialbearbeidet form og avkjøles til den stivner og får sin endelige form.
Nøkkelfunksjoner:
- Presisjon og renhet: Medisinsk støping må overholde strenge toleranser og utføres i renrom for å unngå kontaminering.
- Biokompatible materialer: Bruk plast av medisinsk kvalitet, for eksempel polykarbonat, polypropylen og PEEK, som er trygge for bruk i eller med menneskekroppen.
- Overholdelse av lover og regler: Produsentene må overholde standarder som ISO 13485, FDA og CE-forskriftene for å garantere sikkerhet og effektivitet.
- Høyt volum og repeterbarhet: Perfekt for produksjon av store serier med ensartede, sterile deler, for eksempel sprøyter, IV-sett, diagnostikkhus, artroskoper, kirurgiske instrumenter og medisindispenseringsutstyr.
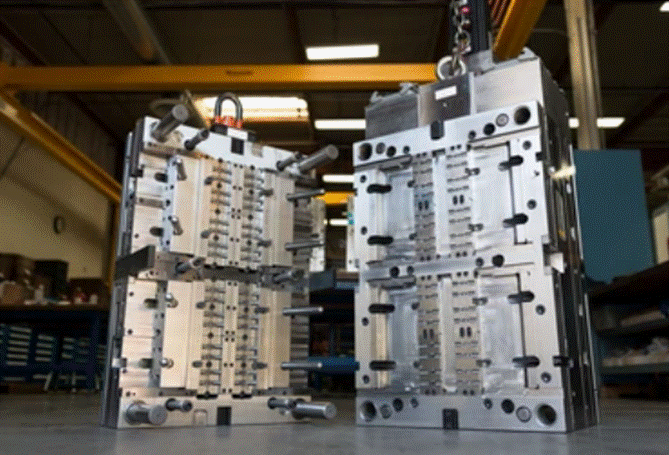
Kriterier for utvelgelse
Følgende kriterier bidro til å avgjøre hvilket selskap som var best på medisinsk sprøytestøping,
1. ISO 13485-sertifisering og overholdelse av regelverk
Den internasjonalt anerkjente standarden for kvalitetsstyringssystemer for medisinsk utstyr er ISO 13485. I tillegg må selskapene oppfylle FDA- og CE-forskriftene når de skal selge produktene sine.
2. Avansert teknologi og renromskapasitet
Bedriftene må kunne operere i renromsmiljøer (ISO-klasse 7 eller bedre) og benytte seg av den nyeste sprøytestøpingsteknologien (mikrostøping og multi-shot sprøytestøping) for å oppfylle standarder for hygiene, forurensning osv.
3. Medisinsk fokus og erfaring fra bransjen
Pålitelighet og ekspertise innen produksjon av medisinske komponenter har en sterk historie. Selskaper som har vært lenge i helsevesenet, har også en bedre forståelse av reguleringer og krav til ytelse.
4. Stor kundebase innen helsevesenet og global rekkevidde
Globale selskaper vil ha robuste infrastrukturer for kvalitetskontroll, logistikk og regelverk for bedre å kunne betjene multinasjonale medisinske OEM-er.
5. FoU- og tilpasningskapasitet
De tilbyr ikke bare produksjon, men også teknisk støtte, design for produksjon (DFM) og innovasjonspartnerskap for å få nye produkter raskt og effektivt ut i livet.
Topp 10 medisinske plastinjeksjonsstøpeselskaper.
Dette er noen av verdens ledende produsenter innen medisinsk plastsprøytestøping. Disse produsentene er valgt ut på grunnlag av strenge kriterier, som kvalitetssertifiseringer, teknologiske fremskritt, global tilstedeværelse og forpliktelse til innovasjon, og de er betrodde av de største merkene innen medisinsk utstyr over hele verden. Her er de 10 beste:
1. Sincere Tech (Kina)
Sincere Tech er en av de ledende kinesiske produsentene som er involvert i medisinsk plastsprøytestøping for globale kunder. Sincere Tech dekker renromsstøping, rask prototyping og masseproduksjon, og er en pålitelig kilde til medisinske deler med høy presisjon. De er opptatt av kvalitet ved å følge ISO 13485-standarder, avansert verktøy og strenge valideringsprosesser. Dessuten kan medisinske OEM-er outsource hele prosessen, inkludert formdesign, fabrikasjon og til og med montering, noe som gjør det til en komplett tjeneste hos ulike selskaper.
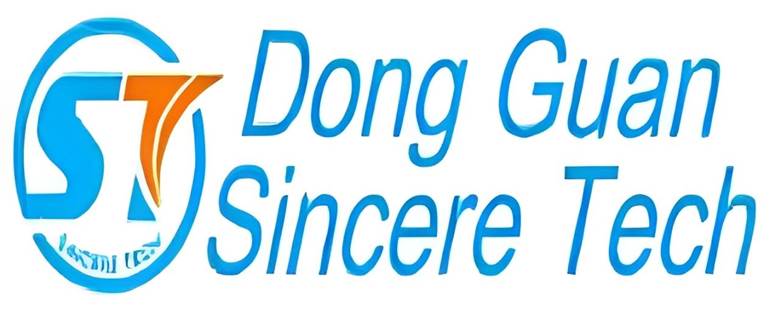
Nettsted: https://www.plasticmold.net/
Selskapets profil:
I over 15 år har Sincere Tech spesialisert seg på både produksjon av støpeformer og fremstilling av nøyaktige plastdeler i Kina. Takket være ISO 13485-kvalifiseringen og renrom av høy kvalitet kan selskapet tilby viktige deler til globale medisinske OEM-er som krever strenge toleranser. Selskapet tar seg av formdesign, håndterer verktøy og utfører sekundær bearbeiding, alt fra samme sted. Siden de kan håndtere produktutvikling fra de første trinnene til masseproduksjon, er de verdifulle for produksjon i helsevesenet.
Bransjer vi betjener:
Medisinsk utstyr, bilindustri, elektronikk og emballasje.
Hvorfor velge Sincere Tech?
- Vår presisjonsstøpefabrikk for medisinsk bruk oppfyller den strenge ISO 13485-standarden.
- Tilbyr alle tjenester, fra design og prototyping til produksjon.
- Mulighet til å støpe deler i renrom for produkter uten forurensning.
- Det er behov for god kvalitetssikring og validering.
- Vi tilbyr konkurransedyktige priser til både små og store globale kunder.
2. Phillips-Medisize (USA)
Phillips Medisize er et Molex-selskap og en industrigigant innen integrert legemiddeladministrasjon, diagnostisk utstyr og medisinsk elektronikk. Phillips Medisize er en fullservicebedrift innen medisinsk injeksjonsstøping, og de har et globalt fotavtrykk og dyp ekspertise innen komplekse sammenstillinger. De har toppmoderne renromsfasiliteter, som tilbyr design- og prototypetjenester samt automatiserte høyvolumsproduksjonstjenester hvis du trenger det. Selskapet er en ledende innovatør av løsninger for å koble sammen digital helse og avansert produktsporing.
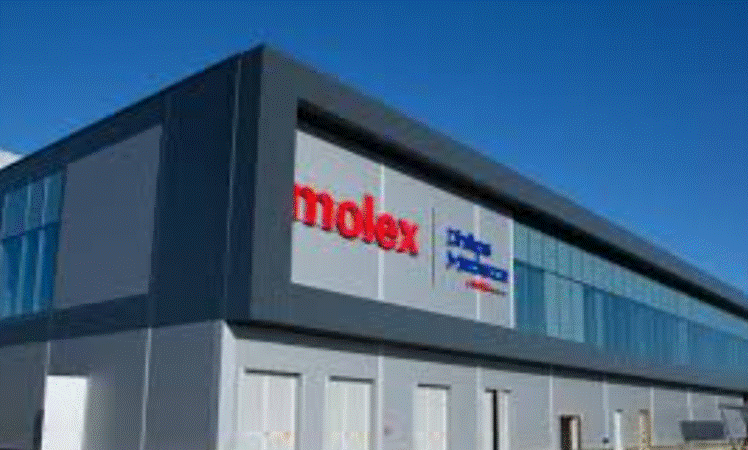
Selskapets profil:
Phillips-Medisize er en del av Molex, og fokuserer på å produsere utstyr for medisinering, diagnostikk og tilkoblet helseutstyr over hele verden. Selskapet er til stede internasjonalt i USA, Europa og Asia, og har renrom fra ISO klasse 7 til klasse 8. De tilbyr tjenester i alle ledd, og tar seg av design, utvikling, testing og full produksjon. Blant kundene deres er noen av verdens ledende farmasøytiske og medisinsktekniske selskaper.
Bransjer vi betjener:
Legemiddeladministrasjon, diagnostikk og medisinsk elektronikk.
Hvorfor velge Phillips-Medisize?
- Internasjonal drift forbedret ved hjelp av automatisering og vedlikehold i renromsmiljøer.
- Kunnskap om tilkoblet helse og bruk av digital teknologi.
- Vi har en lang historie med vellykket samarbeid med ledende MedTech-selskaper.
- Alle våre virksomheter over hele verden overholder ISO 13485- og FDA-standardene.
- Erfaring med å håndtere behovene til store produksjonsprosjekter.
3. Tessy Plastics (USA)
Tessy Plastics har levert sprøytestøping av plast med høy presisjon til den medisinske sektoren i flere tiår og er beryktet for sin ISO 13485-sertifisering. De har alle produktene in-house, fra verktøy til alt fra automatisering til validering. De er helt avhengige av det medisinske feltet, og produserer et bredt utvalg av kirurgisk, diagnostisk og bærbart medisinsk utstyr som samarbeider tett med kunder og partnere for å garantere høyere pålitelighet, enkel skalerbarhet og samsvar med globale forskrifter. De har også kapasitet til å mikrostøpe og sette inn støpeformer for delikate komponenter.
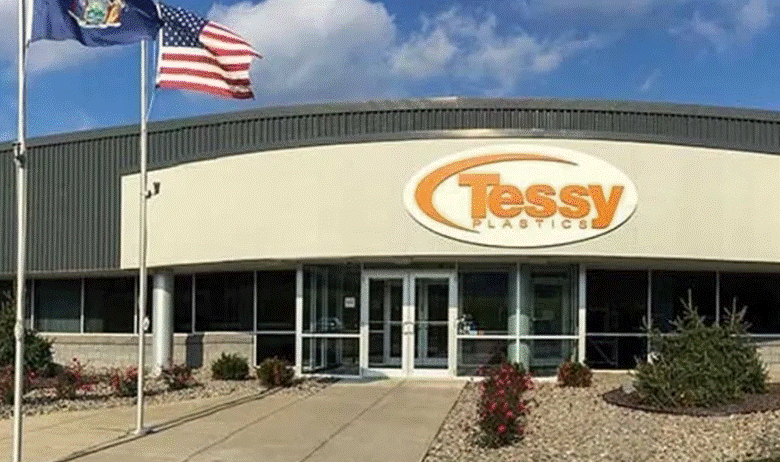
Selskapets profil:
Siden 1976 har Tessy Plastics vært en familiebedrift innen presisjonssprøytestøping i New York, USA. Bosch' medisinske virksomhet omfatter kirurgiske, diagnostiske og bærbare produkter, som alle er laget i henhold til strenge kvalitetsstandarder. Tessy kombinerer automatisering, avanserte verktøy og monteringsprosesser i sitt arbeid. Selskapets ingeniører samarbeider med kundene for å løse problemer med design, regelverk og rask lansering.
Bransjer vi betjener:
Medisin, elektronikk og forbruksvarer.
Hvorfor velge Tessy?
- Alle trinn fra design til salg er under én og samme myndighet.
- Tilbyr mikrostøping og innsatsstøping som sine sterkeste sider.
- Over 40 år med produksjon av medisinsk utstyr.
- Selskapet har renrom i ISO-klasse 7.
- Selskapet er ISO 13485-sertifisert og har som mål å oppfylle alle krav til medisinsk utstyr.
4. Gerresheimer (Tyskland)
Gerresheimer er en global leder innen medisinsk og farmasøytisk emballasje med en viktig avdeling for sprøytestøping av plast som er i stand til å produsere systemer for legemiddeladministrering, sprøytestøpt diagnostisk utstyr og ferdigfylte sprøyter. Selskapet har flere renromsproduksjonsanlegg og følger de strengeste regulatoriske standardene. På grunn av den vertikale integrasjonen fra produktdesign til produksjon av støpeformer og til slutt sluttmontering, er de den foretrukne partneren til farmasøytiske selskaper over hele verden.
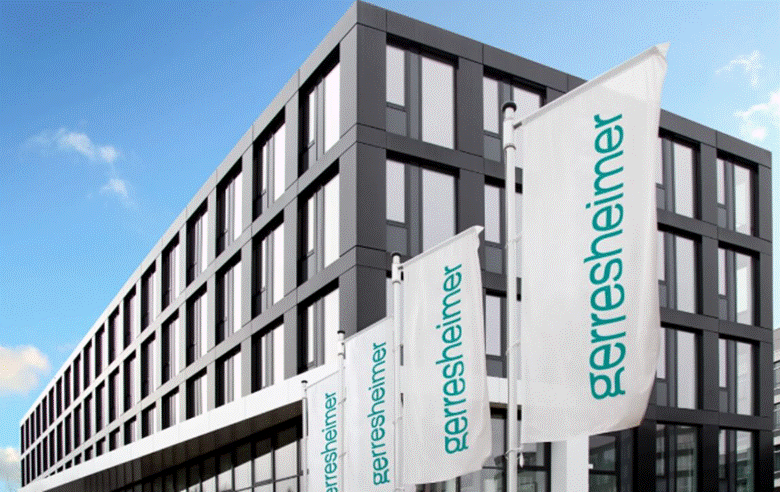
Selskapets profil:
Gerresheimer er et anerkjent selskap innen medisinsk og farmasøytisk emballasje og har lang erfaring med sprøytestøping. Selskapet har mer enn 30 globale avdelinger og tilbyr kundene produkter som spenner fra insulinpenner til inhalatorer og diagnostikksett. Selskapets styrke ligger i at det dekker hele tjenestespekteret, fra design til produksjon av den endelige emballasjen. Takket være den avanserte infrastrukturen kan de produsere store medisinske produkter som er i samsvar med mange forskrifter.
Bransjer vi betjener:
Legemidler, helsetjenester og diagnostikk.
Hvorfor velge Gerresheimer?
- Produksjonsløsninger som omfatter et helt system.
- Det finnes renromssertifiserte anlegg på forskjellige steder i verden.
- Ny utvikling innen både emballasje og utstyr.
- Mange ledende farmasøytiske organisasjoner stoler på oss.
- Følger alle medisinske forskrifter i EU og USA.
5. Nypro Healthcare (Jabil - USA)
Nypro Healthcare er en del av Jabil, og leverer høyvolumløsninger for sprøytestøping av medisinsk plast til kompliserte og strengt regulerte markeder. Nypro har produksjonsanlegg over hele verden, med automatiseringsmuligheter og teknisk støtte. De konsentrerer seg om avanserte medisinske applikasjoner som injiserbare legemidler, diagnostiske systemer og minimalt invasive kirurgiske verktøy. Nypro samarbeider med kundene etter en partnerskapsmodell, og sørger for å tilby FoU, prototyping og produksjon.
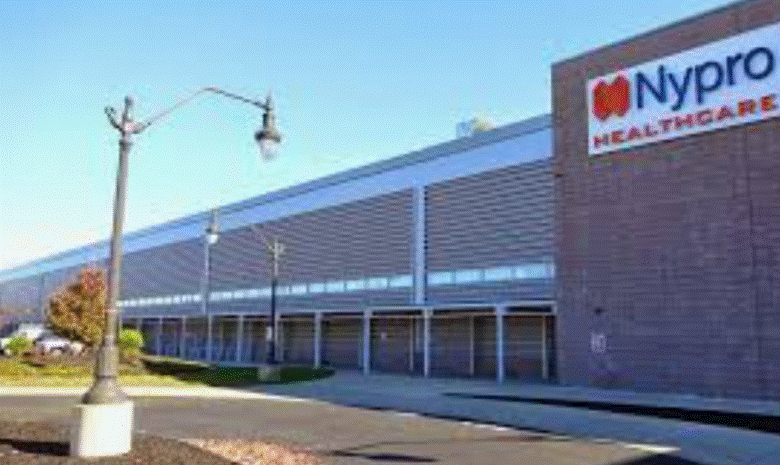
Selskapets profil:
Nypro, som tilhører Jabil Healthcare, tilbyr komplette CDMO-tjenester og sprøytestøping av medisinsk utstyr. Nypro tilbyr høyvolumproduksjon i fem regioner over hele verden for kirurgiske, diagnostiske og medikamentelle produkter. Takket være deres dyktighet innen automatisering, overholdelse av regelverk og mindre enheter kan kundene slå ut konkurrentene. De jobber også med prosjektering i begynnelsen, velger ut viktige materialer og bygger prototyper.
Bransjer vi betjener:
Legemiddeltilførsel, diagnostikk og kirurgiske systemer.
Hvorfor velge Nypro?
- Produksjonsanlegg i flere land med mulighet til å utvide produksjonen.
- Har inngående kjennskap til reglene i regulerte markeder.
- Bedre automatisering og montering gir bilprodusentene fordeler.
- Tidlig samarbeid mellom FoU og tidlig design.
- Ledende leverandør innen produksjon av medisinsk høyrisikoutstyr.
6. Röchling Medical (Tyskland)
Röchling Medical, som er en del av Röchling-gruppen, tilbyr komplette sprøytestøpeløsninger for kunder innen farmasøytisk, diagnostisk og medisinsk utstyr. De er globalt tilgjengelige i Europa, USA og Kina. Röchlings kompetanse omfatter prosjektering, overholdelse av regelverk og renromsstøping. Porteføljen omfatter alt fra lab-on-chip-komponenter til spesialtilpassede innkapslinger for kirurgisk utstyr, som ofte produseres i fullt validerte klasse 7-miljøer.
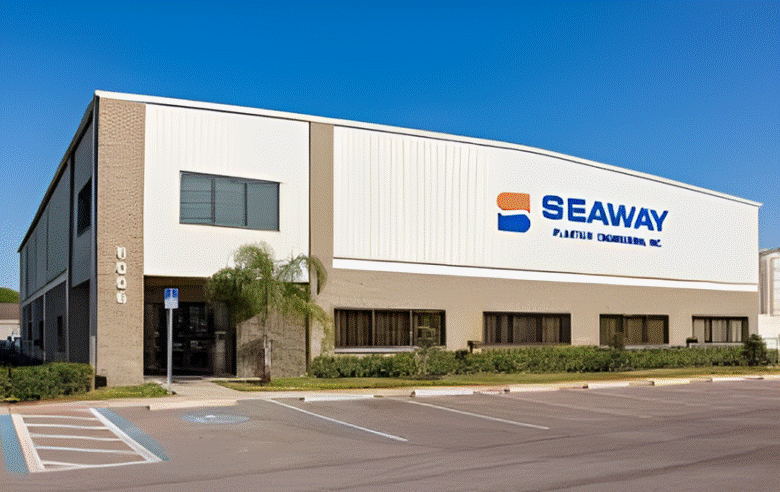
Selskapets profil:
Röchling Medical er en del av Röchling-gruppen, som hjelper farmasøytisk, diagnostisk og medisinsk-teknisk industri over hele verden. De spesialiserer seg på renromsstøping, lab-on-chip og innkapsling av enheter, og har produksjon i Tyskland, USA og Kina. Röchling tilbyr teknisk assistanse, regulatoriske funksjoner og full støtte for produktadministrasjon fra start til slutt. Produksjonssystemene ved disse anleggene støtter både begrensede og store produksjonsserier.
Bransjer vi betjener:
Diagnostikk, farmasi og kirurgiske instrumenter.
Hvorfor velge?
- Selskapene har virksomhet i flere land i Europa, Kina og USA.
- Vi tilbyr et bredt spekter av tjenester for renromsproduksjon.
- Har jobbet i støpemiljøer i klasse 7 og 8.
- Vi leverer teknisk hjelp for følgende regelverk.
- Vi har kompetanse til å utvikle spesialtilpassede komponenter for medisinsk bruk.
7. Seaway Plastics Engineering (USA)
Seaway Plastics, som spesialiserer seg på produksjon av små og mellomstore volumer, er en troverdig partner for medisinske OEM-er som trenger rask levering og fleksibel støtte. De tilbyr tjenester som sprøytestøping i renrom, interne verktøy og monteringstjenester. Seaway er særlig kjent innen segmentet for ortopedisk og kirurgisk utstyr. Selskapet tilbyr også protokoller for IQ/OQ/PQ-validering, noe som gjør det klart at produktene deres er strengt regulerte.
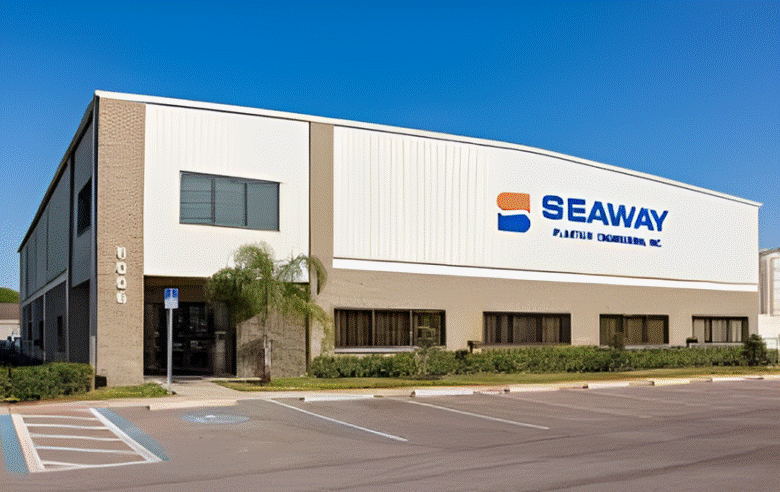
Selskapets profil:
Seaway Plastics tilbyr hovedsakelig sprøytestøping av små og mellomstore volumer til selskaper som produserer medisinsk utstyr. Fasilitetene i ISO-klasse 7-renrom gjør det mulig å lage støpeformer, samt validere og montere sluttprodukter. Seaway gjør seg først og fremst bemerket med ortopediske og kirurgiske instrumenter. På grunn av de raske produksjonstidene henvender folk seg til disse selskapene for både prøveprosjekter og småskalaprosjekter.
Bransjer vi betjener:
Ortopedi, kirurgiske verktøy og diagnostikk.
Hvorfor velge?
- Vi tilbyr rask prototyping og lave antall prøver.
- Vi tilbyr utvikling og support av våre egne test- og automatiseringsverktøy.
- Du kan stole på at anleggene våre er sertifisert i henhold til ISO 13485 og regulert av FDA.
- Spesialstøping for sensitive komponenter er mulig i renrom.
- Gir kunden full fleksibilitet.
8. MedPlast (nå Viant - USA)
Dette selskapet er nå kjent som Viant og er et kraftsenter innen produksjon av medisinsk utstyr. De utfører kontraktsproduksjon, inkludert sprøytestøping av plast, ekstrudering, montering, pakking og sterilisering. Deres kompetanse innen støping omfatter mer enn implanterbart utstyr, diagnostiske sett og systemer for administrering av legemidler. Viants vektlegging av design for produserbarhet (DFM) og intens kvalitetskontroll gjør dem til en ideell leverandør for medisinske høyrisikoapplikasjoner.
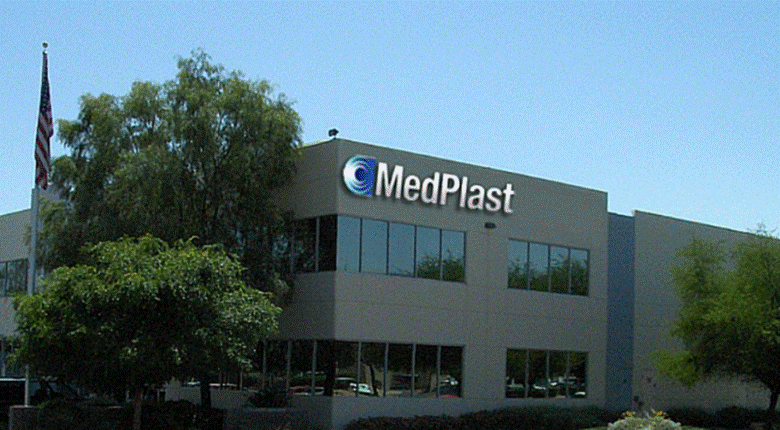
Selskapets profil:
Selskapet drives under varemerket Viant, og tilbyr en rekke ulike produksjonsprosesser for medisinsk utstyr, for eksempel sprøytestøping og sterilisering. Virksomheten omfatter markeder for ortopedi, diagnostikk og engangsutstyr. Takket være Viants DFM-ferdigheter og interne regulatoriske ressurser er løsningene skapt for å være både sikre og skalerbare. Vifor Pharma har mer enn 25 anlegg spredt over hele verden der de bruker sin regulatoriske kunnskap.
Bransjer vi betjener:
Implanterbare enheter, diagnostikk og kirurgiske systemer.
Hvorfor velge?
- Tilbyr tjenester for design for produksjon, støping og sterilisering.
- Dokumenterbar erfaring med å gi behandling for medisinske problemer som er vanskelige å behandle.
- Designet for verden, produsert for verden.
- Du kan endre bestillingen din etter behov, og alle produktene blir kvalitetskontrollert.
- Alle våre anlegg er ISO 13485- og FDA-sertifiserte.
9. Technoplast (Israel)
Technoplast er en voksende aktør innen presisjonsstøping av medisinsk plast, med base i Israel. De tilbyr blant annet produktdesign, hurtig prototyping og masseproduksjon, med hovedvekt på spesialtilpassede medisinske komponenter. Blant kundene er multinasjonale produsenter av medisinsk utstyr, og de er kjent for å være raske til markedet fordi de er svært smidige og har en sterk FoU-avdeling. Technoplast er eksepsjonelt sterke (kardiologi, diagnostikk, engangsutstyr).
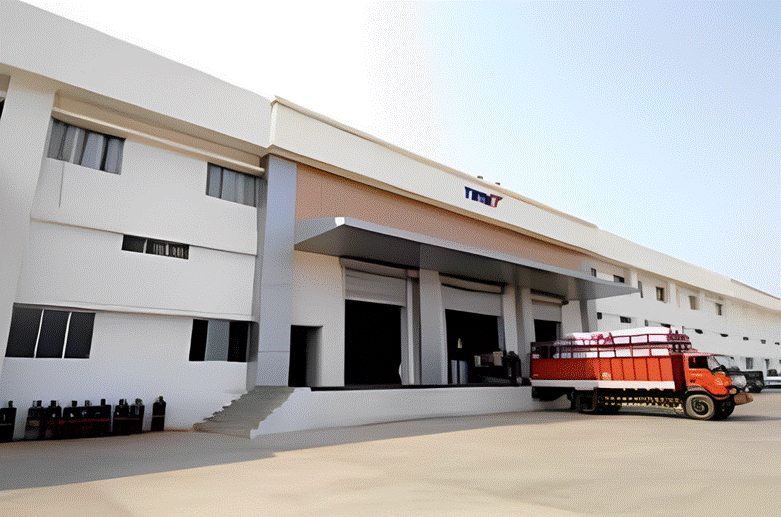
Selskapets profil:
Technoplast er en israelsk virksomhet som leverer avansert plaststøping til bruk i medisinsk utstyr. Bedriftene tilbyr hjelp med å designe produkter, lage prototyper, produsere støpeformer og produsere artikler i stor skala. Technoplast er anerkjent for å være fleksibel, drive effektiv FoU og ha erfaring med å lage produkter for kardiologi, diagnostikk og engangsartikler. Rask levering og lave produksjonskostnader er de viktigste prioriteringene for selskapet.
Bransjer vi betjener:
Kardiologi, diagnostikk og engangsutstyr.
Hvorfor velge Technoplast?
- Forbedret produksjon gjennom smidige handlinger og rask prototyping.
- Støpeformer med høy presisjon for detaljerte medisinske deler.
- Gjør innovativ FoU for medisinsk bruk.
- Høye priser for å få produkter ut på markedet.
- ISO 13485-sertifisering er kombinert med CE- og FDA-kompatible produkter.
10. TK Mold (Kina)
TK Mold, som har to av de siste kinesiske selskapene på denne listen, er kjent for høypresisjonsverktøy og sprøytestøpingstjenester. De arbeider med støpeformer og komponenter av medisinsk kvalitet, og eksporterer produkter til Nord-Amerika, Europa og andre asiatiske markeder. Deres styrke er teknisk design og deres evne til å sette disse ideene ut i livet gjennom både produksjon av støpeformer og produksjon av små og mellomstore serier. TK Mold har et sertifisert ISO-dokument og overholder internasjonale medisinske standarder. Derfor er de et godt selskap å outsource produksjonsarbeid til.
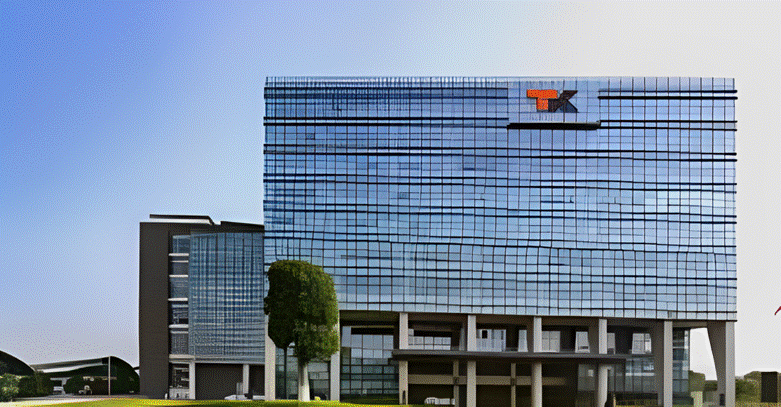
Selskapets profil
TK Mold er velkjent i Kina for sine høykvalitets sprøytestøpeformer og deler til medisinsk utstyr. Kundene deres i Nord-Amerika, Europa og Asia får renromsstøping for klasse 7-applikasjoner. Støpeformen får støtte hele veien fra den opprinnelige designen til produksjon av mellomstore serier og etterproduksjon. Fordi de er ISO 13485-sertifisert og oppfyller internasjonale standarder, har de gjort seg fortjent til tillit som offshore-partner.
Bransjer vi betjener
Medisin, elektronikk og bilindustri.
Hvorfor velge?
- Bare et lite antall profesjonelt utformede støpeformer brukes til produksjon.
- Spesiell oppmerksomhet rettes mot innovasjon innen ingeniørfag.
- ISO-sertifisert og i henhold til medisinske retningslinjer.
- Tilby ekspertise til EU, USA og Asia.
- Rimelige metoder for samarbeid med OEM-er.
Fremtidsutsikter for sprøytestøperfirmaer for medisinsk plast.
Med utviklingen av helsevesenet forventes det at medisinske sprøytestøpeselskaper vil utvikle seg på flere viktige områder. Her er hva fremtiden bringer:
1. Innføring av smarte materialer
- Selskapene investerer i materialer som antimikrobielle, biologisk nedbrytbare eller bioresorberbare polymerer som gir forbedret funksjonalitet.
- Disse forsyningene gjør det mulig å bruke tryggere og mer bærekraftig medisinsk engangsutstyr.
2. Ekspansjon innen mikrofluidikk og miniatyrisering
- Stadig flere prosesseringsselskaper blir tvunget til å lage ultrasmå og intrikate deler til lab-on-a-chip, bærbare sensorer og diagnoseutstyr.
- For å forbli konkurransedyktig vil det være behov for mikrostøping.
3. Automatisering og integrering av Industri 4.0
- Avansert automatisering og dataanalyse i sanntid vil imidlertid gjøre det mulig for selskapene å oppgradere prosesseffektiviteten, sporbarheten og kvalitetskontrollen.
- De smarte fabrikkene med tilkoblede systemer vil minimere menneskelige feil, og produktiviteten vil øke.
4. Tilpasning og produksjon på bestilling
- Etterspørselen etter persontilpasset medisinsk utstyr øker, og derfor satser bedriftene på en fleksibel serieproduksjon.
- Rapid prototyping og additiv produksjon kan forbedre de tradisjonelle støpeprosessene.
5. Bærekraft og overholdelse av miljøkrav
- Verdensdekret tvinger selskaper til å resirkulere, redusere avfalls- og energiforbruket og redusere bruken av ikke-resirkulerbar plast.
- Produsentene omfavner de grønne initiativene og praksisene i den sirkulære økonomien.
6. Økt regulatorisk kontroll
- Med nye og innovative materialer og ny teknologi kan bedriftene forvente strengere protokoller for validering, sporbarhet og samsvar.
- Det vil være behov for å investere i byråkratiekompetanse for å sikre fortsatt markedsadgang.
7. Strategiske partnerskap med MedTech-selskaper
- Selskapene etablerer tettere samarbeid med medisinske OEM-er for å utvikle innovative IP-sensitive løsninger i fellesskap.
- Det vil bli et konkurransefortrinn å involvere design på et tidlig stadium.
Konklusjon
Det er viktig å velge den beste produsenten av medisinsk plastsprøytestøping for å sikre at det medisinske utstyret ditt er vellykket når det gjelder sikkerhet, skalert produksjon og all overholdelse. Denne listen er verdens eliteselskaper, ikke bare når det gjelder å følge de tekniske og regulatoriske kravene i medisinsk industri, men de gir også innovative og kundeorienterte løsninger.
Fra verdens giganter, som Phillips-Medisize og Gerresheimer, til nisjeselskaper som Sincere Tech og Technoplast, har hver og en av dem en viss dokumentert ekspertise og kapasitet på helseområdet. Enten du skal utvikle et nytt diagnostisk verktøy eller utvide produksjonen til en etablert maskin, vil et samarbeid med en av disse pålitelige leverandørene av medisinsk sprøytestøping gi deg en ledende posisjon når det gjelder kvalitetsspesifikasjoner og konkurranse.
Anerkjente leverandører av medisinsk sprøytestøping garanterer at de holder seg i forkant når det gjelder kvalitetsstandarder og konkurransedyktighet på markedet.
Vanlige spørsmål
1. Hva er medisinsk plastinjeksjonsstøping?
Det er en produksjonsprosess som fremstiller plastdeler med høy presisjon for medisinske bruksområder med spesialutstyr og materialer i henhold til strenge regulatoriske standarder.
2. Hvorfor er ISO 13485-sertifisering viktig for bedrifter som driver med medisinsk støping?
Det sikrer at selskapet overholder internasjonalt aksepterte standarder for kvalitetsstyringssystemer i bransjen for medisinsk utstyr, noe som er nøkkelen til overholdelse av regelverk og produktsikkerhet.
3. Hvilke materialer brukes vanligvis i medisinsk sprøytestøping?
De vanligste materialene er polykarbonat, polypropylen, polyetylen og termoplastiske elastomerer av medisinsk kvalitet, som må være biokompatible og steriliserbare materialer.
4. Hva er effekten av renrom i medisinsk sprøytestøping?
Renrom er et miljø som kan være fritt for forurensning, noe som er avgjørende i produksjonen av sterile/sensitive medisinske komponenter ved å minimere risikoen for partikkelforurensning.
5. Er det mulig for små bedrifter å matche produksjonen til de store produsentene her?
Ja. Mange små firmaer tilbyr nisjeekspertise, smidig utvikling og raske prototypetjenester, og de er gode partnere for spesialisering eller spesialtilpasset arbeid.