Obecnie Chiny ugruntowały swoją pozycję globalnego lidera w dziedzinie firm zajmujących się formowaniem wtryskowym i stały się cennym rozwiązaniem produkcyjnym dla firm każdej wielkości na świecie, w konkurencyjnych cenach. Dzięki dużej liczbie firm zajmujących się formowaniem wtryskowym Chiny stały się obszarem specjalizującym się w produkcji komponentów z tworzyw sztucznych dla całego spektrum branż, od motoryzacji, elektroniki, opieki zdrowotnej i opakowań po towary konsumpcyjne. Zaawansowana technologia, inżynieria precyzyjna i automatyzacja są wykorzystywane do produkcji części formowanych z niezrównaną dokładnością i wydajnością. Kilka kluczowych zalet buduje chiński przemysł formowania wtryskowego, na który decydują się firmy. Jedną z największych sił przyciągających w zakresie opłacalności produkcji jest to, że koszty pracy i produkcji są tańsze w Chinach niż w krajach zachodnich. Co więcej, chińskie firmy zajmujące się formowaniem wtryskowym są coraz częściej wyposażone w wysokowydajne, najnowocześniejsze maszyny i systemy robotyki, umożliwiające wydajną i wielkoseryjną produkcję przy jednoczesnym zachowaniu jakości. Firma posiada uznane na całym świecie certyfikaty, takie jak ISO 9001, ISO 13485 (urządzenia medyczne) i IATF 16949 (komponenty motoryzacyjne), aby spełnić globalne standardy jakości w branży.
Chińskie firmy zajmujące się formowaniem wtryskowym mają również siłę dostosowywania i innowacji. Producenci w Chinach mają możliwości techniczne, a także wiedzę specjalistyczną, aby zapewnić niestandardowe formy do form wielogniazdowych klienta, obtryskiwania, formowania wkładek i skomplikowanych projektów. Dla firm poszukujących szybkości i niezawodności, ich zdolność do zapewnienia szybkiego czasu realizacji i produkcji na dużą skalę jest preferowanym wyborem.
Czym jest formowanie wtryskowe?
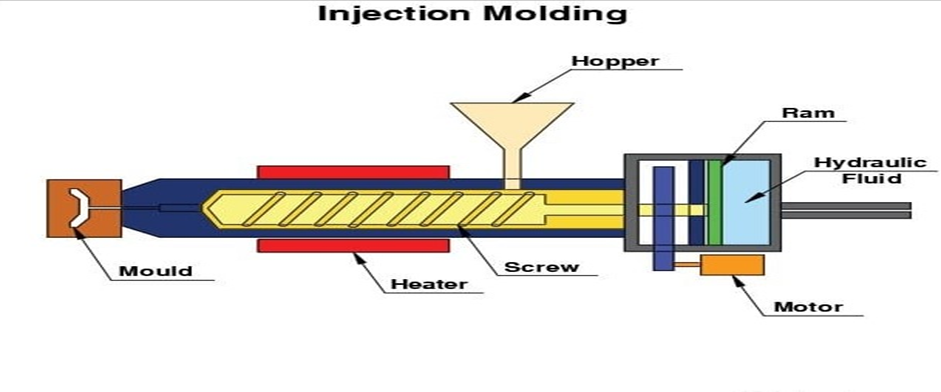
Jest to proces wytwarzania części z tworzyw sztucznych poprzez wtryskiwanie stopionego materiału do formy. Jest szeroko stosowany w branży motoryzacyjnej, medycznej, elektronicznej, opakowań plastikowych i artykułów gospodarstwa domowego. Proces ten pozwala na masową produkcję złożonych części z wysoką precyzją i spójnością.
Dlaczego warto korzystać z usług chińskiej firmy zajmującej się formowaniem wtryskowym?
Po pierwsze, Chiny stały się głównym ośrodkiem formowania wtryskowego z wielu powodów:
1. Ekonomiczna produkcja
Ceny są jednym z kluczowych powodów, dla których firmy wybierają chińskie firmy zajmujące się formowaniem. Ponieważ koszty pracy i eksploatacji w Chinach są niższe niż w krajach zachodnich, możliwe jest produkowanie wysokiej jakości elementów formowanych za ułamek kosztów.
2. Zaawansowana technologia produkcji
W nowoczesnych chińskich firmach zajmujących się formowaniem wtryskowym dokonuje się dużych inwestycji w automatyzację i najnowocześniejsze maszyny. Precyzja i najwyższa produktywność są zapewniane przez wiele firm korzystających z systemów zrobotyzowanych, projektowania wspomaganego komputerowo (CAD) i systemów kontroli jakości w czasie rzeczywistym.
3. Standardy wysokiej jakości
Większość szanowanych chińskich firm zajmujących się formowaniem przestrzega międzynarodowych standardów jakości, takich jak ISO 9001, ISO 13485 (dla urządzeń medycznych) i IATF 16949 (części samochodowe). Certyfikaty te gwarantują, że produkt spełnia wymagania wysokiej jakości.
4. Personalizacja i innowacje
Wiele chińskich firm zajmujących się formowaniem zapewnia rozwiązania dostosowane do różnych potrzeb biznesowych. Chińscy producenci są w stanie zaspokoić potrzeby każdego klienta, począwszy od formowania nadlewów i wkładek, a skończywszy na złożonych modelach wielogniazdowych.
5. Szybki czas realizacji
Chińskie firmy zajmujące się formowaniem mogą produkować w dużych ilościach wydajniej i szybciej niż większość konkurentów ze względu na wydajne łańcuchy dostaw i usprawnione procesy produkcyjne. Firmy, które polegają na szybkości wprowadzania produktów na rynek, będą potrzebować wsparcia w postaci tej szybkości.
6. Doświadczenie i wiedza specjalistyczna
Istnieją tysiące wyspecjalizowanych firm w chińskim przemyśle formowania wtryskowego, które mają głębokie doświadczenie we wszystkich tych obszarach. Są one uważane za preferowany wybór dla globalnych firm w dziedzinie projektowania form i doboru materiałów, a także inżynierii precyzyjnej.
Branże korzystające z chińskich firm zajmujących się formowaniem wtryskowym

Zastosowanie formowania wtryskowego jest dość szerokie i rozprzestrzenia się w różnych branżach, z których każda ma własne standardy i technologie.
1. Przemysł motoryzacyjny
Chińskie firmy zajmujące się formowaniem produkują części takie jak deski rozdzielcze, zderzaki, panele wewnętrzne i elementy oświetlenia w sektorze motoryzacyjnym, który w dużym stopniu polega na tych firmach. Jedną z kluczowych zalet jest możliwość wytwarzania lekkich, ale wytrzymałych części z tworzyw sztucznych.
2. Elektronika i towary konsumpcyjne
Chińskie firmy zajmujące się formowaniem wtryskowym specjalizują się w produkcji precyzyjnych części dla przemysłu elektronicznego i dóbr konsumpcyjnych oraz różnych innych produktów. Potrzeba coraz więcej estetycznych, trwałych i funkcjonalnych komponentów z tworzyw sztucznych.
3. Medycyna i opieka zdrowotna
Urządzenia takie jak narzędzia chirurgiczne, strzykawki i łączniki dożylne wykorzystują wysokiej jakości części frezowane wtryskowo, a przemysł medyczny nie może się bez nich obejść. W zależności od producenta medycznego, wiele chińskich firm zajmujących się formowaniem posiada pomieszczenia sterylne zapewniające ścisłe standardy higieny i bezpieczeństwa zgodnie z produkcją medyczną.
4. Przemysł opakowaniowy i spożywczy
Formowanie wtryskowe jest również wykorzystywane do innego ważnego zastosowania, czyli opakowań z tworzyw sztucznych, które obejmują pojemniki, nakrętki i butelki. Z jednej strony chińscy producenci wytwarzają wysokiej jakości trwałe rozwiązania opakowaniowe, a z drugiej strony są one przyjazne dla środowiska.
Kluczowi gracze w chińskim przemyśle formowania wtryskowego
Formowanie wtryskowe stało się chińskim liderem w branżach takich jak motoryzacja, opieka zdrowotna i elektronika, a także towary konsumpcyjne o wysokiej jakości i opłacalności. Chiński firmy zajmujące się formowaniem wtryskowym utrzymują pozycję lidera na globalnym rynku dzięki zaawansowanym możliwościom produkcyjnym, najnowocześniejszemu sprzętowi i przestrzeganiu międzynarodowych standardów jakości. Istnieje kilka z tych znanych chińskich firm zajmujących się produkcją form do tworzyw sztucznych.
Sincere Tech: Wiodący dostawca rozwiązań w zakresie formowania wtryskowego tworzyw sztucznych
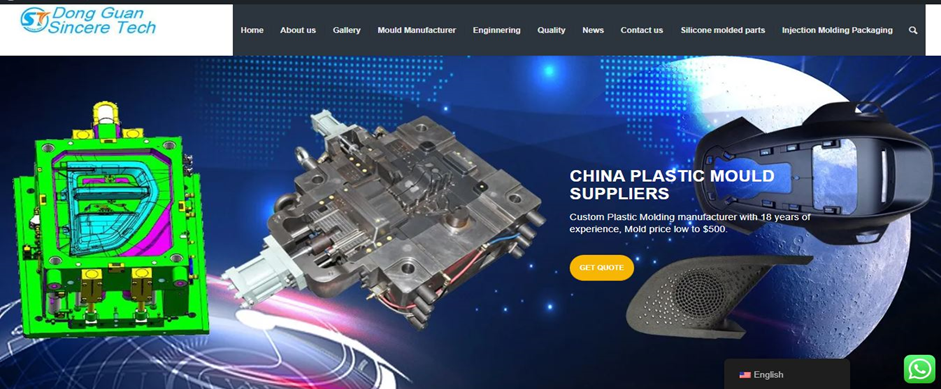
Firma Sincere Tech, założona w 2005 roku i zlokalizowana w prowincji Dongguan w Chinach, jest znana z ponad 10 lat świadczenia usług w zakresie dostarczania form wtryskowych z tworzyw sztucznych. Firma rozszerzyła swoje możliwości o takie rzeczy jak formy odlewnicze Eddie, formowanie gumy silikonowej, obróbkę CNC i kompletny montaż produktów i uczestniczy w wielu różnych branżach na całym świecie.
Zróżnicowany zakres usług
Sincere Tech zapewnia kompleksowe rozwiązania produkcyjne dla klientów z następującymi rodzajami produktów:
- Firma dostarcza produkty takie jak niestandardowe formy wtryskowe z tworzyw sztucznych z możliwością projektowania i produkcji precyzyjnych form do masowej produkcji trwałych i dokładnych elementów z tworzyw sztucznych.
- Precyzyjna obróbka - obróbka CNC, frezowanie, wiercenie, toczenie i szlifowanie wykonywane przez Sincere Tech odbywa się z pełnym doświadczeniem, zapewniając precyzję i wysoką jakość każdej wyprodukowanej części.
- Aby usprawnić proces produkcyjny, firma produkująca formy odlewnicze osiąga sukces poprzez wytwarzanie wysokiej jakości i wysokowydajnych form odlewniczych i montowanie ich w celu produkcji trwałych elementów metalowych, które spełniają specyfikacje surowych wymagań branżowych.
- Świadczymy usługi formowania wtryskowego, wykorzystując zaawansowane maszyny do formowania wtryskowego tworzyw sztucznych do produkcji komponentów wykonanych z następujących materiałów, takich jak PP, ABS, PPS, PEEK, PA66+GF30.
- Usługi montażu produktów - Firma skutecznie montuje podzespoły, proste zespoły i produkty w pełni zmontowane, zgodnie z rygorystycznymi standardami jakości.
- Sincere Tech zapewnia rozwiązania w zakresie formowania silikonu dla konkretnych projektów w różnych branżach.
Zaangażowanie w jakość i postęp technologiczny
Jednak firma szczerze utrzymuje najwyższy standard jakości, przestrzegając międzynarodowych standardów, takich jak ISO 9001: 2015 i QS 9000: 2015. Aby produkować najwyższej jakości formy i części, firma korzysta z zaawansowanych maszyn, w tym maszyn CMM, 5-osiowych maszyn CNC i maszyn FANUC. Sincere Tech zapewnia również klientom umowy o zachowaniu poufności (NDA) w celu ochrony własności intelektualnej klientów i zastrzeżonych projektów w celu zachowania poufności.
Obsługa globalnych branż
Sincere Tech, firma o silnej pozycji międzynarodowej, dostarcza plastikowe i metalowe komponenty do różnych gałęzi przemysłu (motoryzacyjnego, medycznego, elektronicznego, AGD, ogrodniczego, kosmetycznego, opakowań do żywności i złączy elektrycznych). Firma ma bardzo dobrą sprzedaż na rynku eksportowym, którego produkty są wysyłane na różne rynki światowe, w tym do Finlandii, ponieważ może spełniać różne standardy i wymagania branżowe.
Podejście zorientowane na klienta
Sincere Tech ceni sobie konkurencyjne ceny, wysoką jakość produkcji i dobrą jakość usług. Z drugiej strony, jako niezawodny partner dla międzynarodowych firm, umiejętności zarządzania projektami firmy są silne, komunikacja w technicznym języku angielskim jest jasna, a zadowolenie klientów jest wysokie.
Seasky Medical
Seasky Medical, chińska firma zajmująca się formowaniem wtryskowym, produkuje tworzywa sztuczne do zastosowań medycznych. Firma ma siedzibę w Shenzhen, Guangdong, od 1999 roku i zapewnia najlepsze rozwiązania w zakresie formowania wtryskowego. Oferuje precyzyjne projektowanie form, dobór materiałów i formowanie wtryskowe, a także dba o rozwój produktów, dzięki czemu komponenty medyczne spełniają najwyższe standardy jakości i bezpieczeństwa.
Seasky Medical, posiadająca certyfikat ISO 8, zapewnia produkcję urządzeń medycznych, takich jak strzykawki, elementy kroplówek, narzędzia chirurgiczne w środowisku wolnym od zanieczyszczeń. Jako firma z ponad dziesięcioletnim doświadczeniem, jest znana z dostarczania niezawodnych i dokładnych medycznych form wtryskowych, w których obsługuje globalnych dostawców usług medycznych.
Shenzhen Silver Basis Technology Co., Ltd
Shenzhen Silver Basis Technology jest profesjonalną chińską firmą zajmującą się produkcją form samochodowych i przemysłowych. Założona w 1993 roku firma jest jednym z najbardziej niezawodnych dostawców dla znanych światowych marek, takich jak Peugeot i ZTE, dostarczając modele do różnych zastosowań.
Silver Basis oferuje kompleksowy zakres usług w zakresie tłoczenia metali, odlewania ciśnieniowego, produkcji form i testowania produktów. Dzięki specjalistycznej wiedzy w zakresie formowania wtryskowego w branży motoryzacyjnej, firma może produkować wewnętrzne i zewnętrzne części pojazdów, które są trwałe i precyzyjne. Ponieważ firma koncentruje się na jakości, otrzymała certyfikaty ISO 9001 i ISO 14001, dzięki czemu jest wybierana przez międzynarodowych producentów samochodów i elektroniki.
JMT Automotive Mold Co., Ltd
JMT Automotive Mold Co., Ltd jest renomowaną chińską firmą zajmującą się projektowaniem i produkcją form wtryskowych dla przemysłu motoryzacyjnego. Od momentu założenia w 2005 roku z siedzibą w Taizhou, Zhejiang, firma zbudowała solidny system produkcyjny, aby zaspokoić rosnące potrzeby przemysłu motoryzacyjnego.
JMT Automotive Mold posiada doświadczenie operacyjne w zakładzie produkcyjnym o powierzchni 23 000 metrów kwadratowych i jest jednym z producentów specjalizujących się w formach SMC, formach do urządzeń gospodarstwa domowego oraz formach przemysłowych. Dysponuje szybkimi maszynami CNC, precyzyjnym sprzętem testującym i najnowocześniejszymi maszynami do formowania wtryskowego, które zapewniają wysoki standard produkcji. JMT Automotive utrzymuje działalność w zakresie innowacji technologicznych i inżynierii precyzyjnej, a my nadal oferujemy niezawodną produkcję form dla klientów krajowych i zagranicznych.
TK Mold Ltd
Założona w 1978 roku firma TK Mold Ltd jest znaną chińską firmą zajmującą się formowaniem od ponad 40 lat. Firma została założona w 1983 roku i specjalizuje się w opracowywaniu precyzyjnych form do urządzeń medycznych, elektroniki użytkowej, inteligentnych urządzeń domowych i części samochodowych.
TK Mold oferuje zaawansowane rozwiązania w zakresie formowania wtryskowego dla swojej globalnej grupy klientów z bazy 5 zakładów produkcyjnych, w tym jednego w Niemczech. Będąc pionierem w zakresie wdrażania najnowocześniejszych technologii, automatyzacji i precyzyjnej produkcji, firma jest wysoko ceniona przez branże wymagające wysokowydajnych komponentów z tworzyw sztucznych. Wszystkie produkty TK Mold są certyfikowane zgodnie z normami ISO 9001, ISO 13485 i ISO 14001, aby zapewnić, że spełniają międzynarodowe standardy jakości i bezpieczeństwa.
Guangdong Yizumi Precision Machinery Co., Ltd
Guangdong Yizumi jest wiodącą chińską firmą zajmującą się formowaniem wtryskowym, produkującą wysokowydajne wtryskarki oraz komponenty z tworzyw sztucznych. Firma Yizumi została założona w 2002 roku, a jej główna siedziba znajduje się w Foshan, Guangdong. Dysponując bazą produkcyjną o powierzchni ponad 600 000 metrów kwadratowych i prawie 3000 pracowników, Yizumi stało się światową marką.
Firma Yizumi zdobyła wiele nagród branżowych za swoje innowacje w technologii formowania wtryskowego i jest znana z innowacyjnych rozwiązań w zakresie formowania. W 2015 r. firma stała się pierwszą chińską spółką zajmującą się formowaniem wtryskowym notowaną na giełdzie w Shenzhen. Yizumi koncentruje się na motoryzacji, elektronice użytkowej i zastosowaniach przemysłowych, stając się liderem w branży dzięki najnowocześniejszym maszynom i precyzyjnemu formowaniu.
Wyzwania i kwestie do rozważenia przy wyborze chińskiej firmy formierskiej
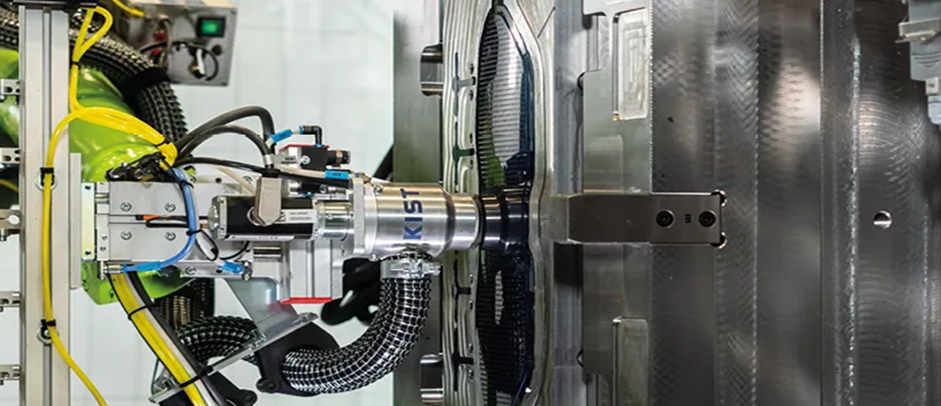
Chińskie firmy wydobywcze mają wiele zalet, jednak przed nawiązaniem współpracy z producentem, firmy powinny być świadome kilku aspektów.
1. Kontrola jakości i zgodność z przepisami
Nie wszyscy producenci przestrzegają tych samych standardów jakości. Przed wyborem dostawcy należy najpierw zweryfikować certyfikaty i przetestować próbkę.
2. Ochrona własności intelektualnej
Produkcja w Chinach może stanowić problem dla outsourcingu ochrony własności intelektualnej (IP). Aby uniknąć utraty swoich projektów i zapewnić im bezpieczeństwo, firmy powinny współpracować z zaufanymi partnerami i umowami prawnymi.
3. Bariery komunikacyjne i językowe
Podczas gdy kilku chińskich producentów posiada anglojęzyczne zespoły sprzedaży, komunikacja nie zawsze jest prosta. Dokumentacja i umowa są przygotowywane, aby zapobiec nieporozumieniom.
4. Logistyka i wysyłka
Jednak obsługa dużych zamówień międzynarodowych może być złożona i kosztowna. Chińskie firmy zajmujące się formowaniem należy rozumieć w ramach przepisów niestandardowych firm, czasów realizacji i kosztów transportu.
Przyszłe trendy w chińskim formowaniu wtryskowym
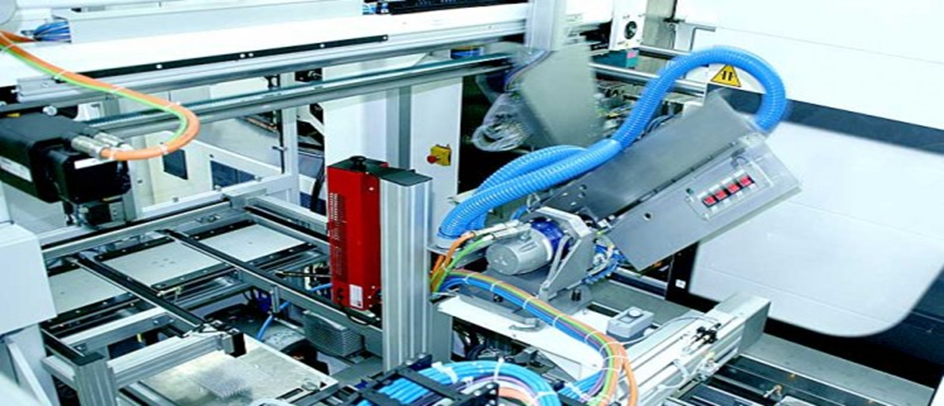
Wraz z nowymi technologiami pojawia się rozwój chińskiego przemysłu formierskiego, aby sprostać nowym wymaganiom rynku. Kluczowe trendy obejmują:
1. Zrównoważone i przyjazne dla środowiska materiały
Ponieważ w Chinach wzrosły obawy związane z odpadami z tworzyw sztucznych, wiele firm zajmujących się formowaniem zaczęło bardziej przejmować się przepisami dotyczącymi ochrony środowiska i obecnie opracowuje biodegradowalne, a także pochodzące z recyklingu materiały z tworzyw sztucznych.
2. Inteligentna produkcja i Przemysł 4.0
Automatyzacja i kontrola jakości oparta na sztucznej inteligencji, całkowite przejście od procesu zorientowanego na człowieka do inteligentnej fabryki z obsługą IoT całkowicie zmieniły proces formowania wtryskowego i sprawiają, że produkcja jest bardziej wydajna i mniej marnotrawstwa.
3. Zwiększona personalizacja i produkcja na żądanie
Firmy koncentrują się na produkcji małoseryjnej na żądanie dla rynków niszowych i szybkim rozwoju produktów.
Wnioski
Chińskie firmy zajmujące się formowaniem wtryskowym są integralną częścią globalnego przemysłu wytwórczego, ponieważ zapewniają klientom opłacalne, wysokiej jakości i innowacyjne rozwiązania. Niektórzy z tych producentów wytwarzają części z tworzyw sztucznych do komponentów samochodowych, urządzeń medycznych i innych powiązanych branż. Wybierając chińską firmę zajmującą się formowaniem, podmioty gospodarcze powinny rygorystycznie badać standardy jakości, wygodę komunikacji i logistykę, aby zapewnić udane partnerstwo. Ze względu na ciągły trend postępu technologicznego i zrównoważonych praktyk, chińskie firmy zajmujące się formowaniem wtryskowym będą nadal wiodły prym przez wiele kolejnych lat. Biorąc pod uwagę wiele zalet, firmy powinny jednak rozważyć kontrolę jakości, ochronę własności intelektualnej, wyzwania komunikacyjne i logistykę przed wyborem chińskiego partnera w zakresie formowania. Jeśli jednak przeprowadzono dokładne badania i podjęto współpracę z producentami, którzy produkują z zachowaniem jakości i są certyfikowani do pracy, firmy mogą czerpać korzyści z chińskiego doświadczenia w formowaniu wtryskowym. W przyszłości formowanie wtryskowe w Chinach będzie charakteryzować się zrównoważonymi materiałami, inteligentną produkcją, szybką produkcją i automatyzacją opartą na produkcji w połączeniu z biodegradowalnymi tworzywami sztucznymi i technologiami Przemysłu 4.0, Chiny nadal będą miały największe postępy w globalnym formowaniu wtryskowym. Ponieważ chińskie firmy zajmujące się formowaniem wtryskowym stale się rozwijają i dokładają wszelkich starań, aby zmienić oblicze chińskiej produkcji, będą one nadal napędzać nowoczesną produkcję.
Często zadawane pytania (FAQ)
1. Dlaczego produkcja wtryskowa z Chin jest popularna?
Wybór Chin do formowania wtryskowego oferuje korzyści w postaci opłacalnej produkcji, nowoczesnej technologii, dobrze wyszkolonej siły roboczej i dobrze zorganizowanego łańcucha dostaw. Istnieje wielu producentów, którzy przestrzegają międzynarodowych standardów jakości i oferują niestandardowe rozwiązania z bardzo krótkim czasem realizacji.
2. W jaki sposób chińskie firmy zajmujące się formowaniem wtryskowym przynoszą korzyści branżom?
Wszystkie te branże są zależne od chińskiego formowania wtryskowego, w tym motoryzacja, elektronika, urządzenia medyczne, opakowania i towary konsumpcyjne. Chińscy producenci mogą skutecznie i taniej wytwarzać precyzyjne elementy z tworzyw sztucznych potrzebne w tych branżach.
3. W jaki sposób chińskie firmy zajmujące się formowaniem wtryskowym gwarantują jakość produktu?
Chińskie niezawodne firmy zajmujące się formowaniem ściśle kontrolują jakość od surowców po gotowe produkty i uzyskują następujące certyfikaty: ISO 9001, ISO 13485 (medyczny) i IATF 16949 (części samochodowe). Ich poziom procesów testowania i zautomatyzowane systemy kontroli spełniają wysokie standardy.
4. Czym jest wybór chińskiego producenta form?
Firmy powinny brać pod uwagę certyfikaty jakości, doświadczenie, możliwości produkcyjne, ochronę własności intelektualnej oraz zdolność do komunikacji i zapewnienia wsparcia logistycznego. Aby utorować drogę do dobrego partnerstwa, należy przeprowadzić testy próbek i zapewnić zdolność firmy do realizacji dostaw.
5. Jakie są perspektywy chińskiego przemysłu formowania wtryskowego?
Czasy, w których żyjemy, wymagają od przemysłu znalezienia nowych trendów, w tym zrównoważonych i biodegradowalnych tworzyw sztucznych, automatyzacji opartej na sztucznej inteligencji, inteligentnych fabryk i produkcji na żądanie. Postępy te sprawią, że produkcja stanie się bardziej wydajna, będzie generować mniej odpadów i zaspokoi stale rosnące zapotrzebowanie na ekologiczne rozwiązania produkcyjne.