Al giorno d'oggi, la Cina ha consolidato la sua posizione di leader globale nelle aziende di stampaggio a iniezione ed è diventata una valida soluzione produttiva per le aziende di tutte le dimensioni nel mondo, a prezzi competitivi. Grazie al gran numero di aziende di stampaggio a iniezione, la Cina è diventata un'area specializzata nella produzione di componenti in plastica per l'intero spettro di settori industriali, dall'automotive all'elettronica, dalla sanità all'imballaggio, fino ai beni di consumo. Le aziende cinesi si occupano di tecnologia avanzata, ingegneria di precisione e automazione per realizzare pezzi stampati con un'accuratezza e un'efficienza imbattibili. L'industria cinese dello stampaggio a iniezione presenta numerosi vantaggi chiave per i quali le aziende tendono a optare. Una delle maggiori forze trainanti per quanto riguarda l'economicità della produzione è che i costi della manodopera e della produzione sono più bassi in Cina rispetto ai Paesi occidentali. Inoltre, le aziende di stampaggio cinesi sono sempre più dotate di macchinari ad alta efficienza e all'avanguardia e di sistemi robotici, che consentono una produzione efficiente e ad alto volume, mantenendo al contempo la qualità. L'azienda dispone di certificazioni riconosciute a livello internazionale come ISO 9001, ISO 13485 (dispositivi medici) e IATF 16949 (componenti automobilistici) per conformarsi agli standard di qualità del settore globale.
Le aziende cinesi di stampaggio a iniezione hanno anche la forza della personalizzazione e dell'innovazione. I produttori cinesi hanno la capacità tecnica e l'esperienza per fornire stampi personalizzati per stampi a più cavità, sovrastampaggio, stampaggio di inserti e progetti complicati. Per le aziende che cercano velocità e affidabilità, la loro capacità di fornire tempi di consegna rapidi e una produzione su larga scala è una scelta preferenziale.
Che cos'è lo stampaggio a iniezione?
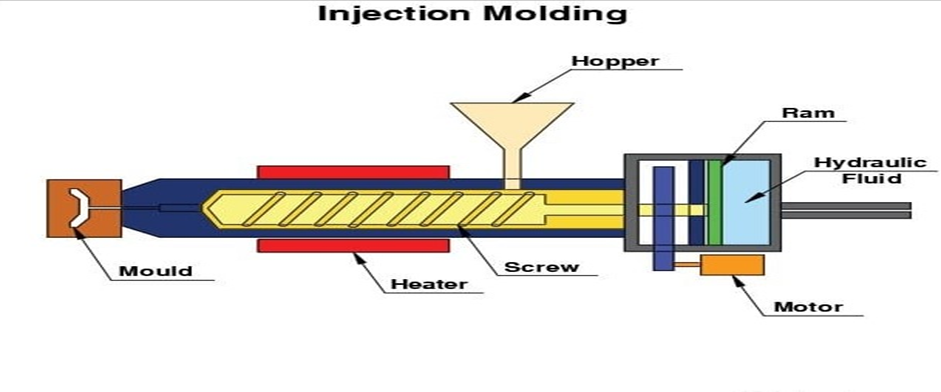
È un processo di produzione di parti in plastica mediante iniezione di materiale fuso in uno stampo. È ampiamente utilizzato nei settori automobilistico, medico, elettronico, degli imballaggi in plastica e dei prodotti per la casa. Questo processo consente di produrre in serie pezzi complessi con elevata precisione e coerenza.
Perché utilizzare un'azienda cinese di stampaggio a iniezione?
In primo luogo, la Cina è diventata un importante centro di stampaggio a iniezione per una serie di motivi:
1. Produzione economicamente vantaggiosa
I prezzi sono uno dei motivi principali per cui le aziende scelgono le società di stampaggio cinesi. Poiché i costi di manodopera e di gestione in Cina sono inferiori a quelli dei Paesi occidentali, è possibile produrre componenti stampati di alta qualità a una frazione del costo.
2. Tecnologia di produzione avanzata
Nelle moderne aziende cinesi di stampaggio a iniezione si investe molto nell'automazione e in macchinari all'avanguardia. La precisione e la massima produttività sono garantite da molte aziende che utilizzano sistemi robotizzati, progettazione assistita da computer (CAD) e sistemi di controllo qualità in tempo reale.
3. Standard di alta qualità
La maggior parte delle aziende cinesi di stampaggio rispetta gli standard di qualità internazionali come ISO 9001, ISO 13485 (per i dispositivi medici) e IATF 16949 (per i componenti automobilistici). Queste certificazioni garantiscono che il prodotto sia conforme ai requisiti di alta qualità.
4. Personalizzazione e innovazione
Molte aziende di stampaggio cinesi offrono soluzioni personalizzate adatte alle diverse esigenze aziendali. I produttori cinesi hanno una risposta per ogni esigenza del cliente, dal sovrastampaggio allo stampaggio di inserti, fino alla richiesta di modelli complessi a più cavità.
5. Tempi rapidi di esecuzione
Le aziende cinesi di stampaggio sono in grado di produrre grandi volumi in modo più efficiente e rapido rispetto alla maggior parte dei concorrenti, grazie a catene di fornitura efficienti e processi di produzione snelli. Le aziende che dipendono dalla velocità di immissione dei prodotti sul mercato avranno bisogno del supporto di questa velocità.
6. Esperienza e competenza
Nel settore dello stampaggio a iniezione cinese esistono migliaia di aziende specializzate che vantano una profonda esperienza in tutti questi settori. Sono considerate la scelta preferita dalle aziende globali per quanto riguarda la progettazione degli stampi, la selezione dei materiali e l'ingegneria di precisione.
Settori che beneficiano delle aziende cinesi di stampaggio a iniezione

L'uso dello stampaggio a iniezione è piuttosto ampio e si diffonde in diversi settori, ognuno dei quali ha i propri standard e tecnologie.
1. Industria automobilistica
Le aziende cinesi di stampaggio producono parti come cruscotti, paraurti, pannelli interni e componenti per l'illuminazione nel settore automobilistico, che fa grande affidamento su queste aziende. Un vantaggio fondamentale è la capacità di produrre parti in plastica leggere ma resistenti.
2. Elettronica e beni di consumo
Per l'industria elettronica e dei beni di consumo e per vari altri prodotti, le aziende cinesi di stampaggio a iniezione sono specializzate nella produzione di pezzi di alta precisione. Sono necessari sempre più componenti in plastica esteticamente gradevoli, durevoli e funzionali.
3. Medicina e assistenza sanitaria
Dispositivi come strumenti chirurgici, siringhe e connettori per flebo utilizzano tutti componenti di alta qualità lavorati a iniezione e l'industria medica non può farne a meno. A seconda del produttore medico, molte aziende di stampaggio cinesi dispongono di strutture in camera bianca per garantire standard igienici e di sicurezza rigorosi, in linea con la produzione medica.
4. Imballaggio e industria alimentare
Lo stampaggio a iniezione viene utilizzato anche per un'altra importante applicazione, ovvero l'imballaggio in plastica, che comprende contenitori, tappi e bottiglie. Da un lato, i produttori cinesi producono soluzioni di imballaggio durevoli e di alta qualità, dall'altro rispettano l'ambiente.
I principali attori dell'industria cinese dello stampaggio a iniezione
Lo stampaggio a iniezione è emerso come leader in Cina per settori che vanno dall'industria automobilistica, alla sanità, all'elettronica, ai beni di consumo, con un'elevata qualità ed economicità. La Cina aziende di stampaggio a iniezione continuano a essere leader nel mercato globale grazie a capacità produttive avanzate, attrezzature all'avanguardia e a una condotta che segue gli standard di qualità internazionali. Ci sono alcune di queste famose aziende cinesi di produzione di stampi per stampaggio, stampi cinesi per la produzione di parti in plastica.
Sincere Tech: un fornitore leader di soluzioni per lo stampaggio a iniezione di materie plastiche
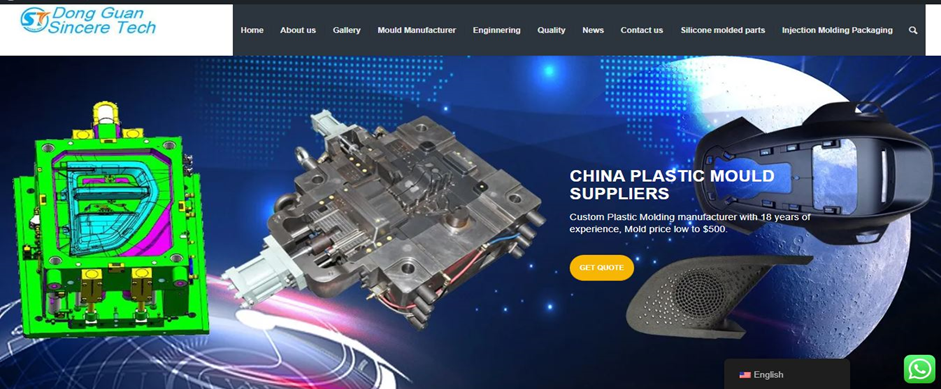
Sincere Tech, fondata nel 2005 e situata nella città della provincia di Dongguan, in Cina, è nota per i suoi oltre 10 anni di servizio di fornitura di stampi a iniezione per materie plastiche. L'azienda ha ampliato le proprie capacità includendo stampi per la fusione di Eddie, stampaggio di gomma siliconica, lavorazione CNC e assemblaggio completo dei prodotti e partecipa a un'ampia varietà di settori industriali in tutto il mondo.
Una vasta gamma di servizi
Sincere Tech fornisce soluzioni di produzione complete per i clienti con i seguenti tipi di prodotti:
- L'azienda fornisce prodotti come gli stampi a iniezione di plastica personalizzati, con la capacità di progettare e produrre stampi ad alta precisione per la produzione di massa di componenti in plastica durevoli e precisi.
- Lavorazione di precisione - La lavorazione CNC, la fresatura, la foratura, la tornitura e la rettifica effettuate da Sincere Tech sono eseguite con competenza completa, garantendo che ogni pezzo prodotto sia di precisione e di alta qualità.
- Per migliorare il processo di produzione, l'azienda produttrice di stampi per pressofusione raggiunge il successo producendo stampi per pressofusione di alta qualità e ad alte prestazioni e assemblandoli per produrre componenti metallici durevoli che soddisfano le specifiche dei severi requisiti del settore.
- Forniamo servizi di stampaggio a iniezione utilizzando macchine avanzate per lo stampaggio a iniezione di materie plastiche per produrre componenti realizzati con i seguenti materiali: PP, ABS, PPS, PEEK, PA66+GF30.
- Servizi di assemblaggio prodotti - L'azienda assembla in modo efficiente sottogruppi, assemblaggi semplici e prodotti completamente assemblati, seguendo rigorosi standard di qualità.
- Sincere Tech fornisce soluzioni di stampaggio del silicone per progetti specifici in vari settori industriali.
Impegno per la qualità e il progresso tecnologico
Tuttavia, sinceramente tech mantiene il più alto standard di qualità rispettando gli standard internazionali come ISO 9001:2015 e QS 9000:2015. Per produrre stampi e parti della migliore qualità, l'azienda si avvale di macchinari avanzati, tra cui macchine CMM, macchine CNC a 5 assi e macchinari FANUC. Sincere Tech offre ai clienti anche accordi NDA (Non-Disclosure Agreement) per la protezione della proprietà intellettuale e dei progetti proprietari dei clienti a fini di riservatezza.
Al servizio delle industrie globali
Azienda forte a livello internazionale, Sincere Tech fornisce componenti in plastica e metallo a diversi settori (automobilistico, medico, elettronico, elettrodomestici, giardinaggio, cosmetici, confezioni alimentari e connettori elettrici). L'azienda registra ottime vendite nel mercato delle esportazioni e i suoi prodotti vengono spediti in diversi mercati globali, tra cui la Finlandia, in quanto è in grado di soddisfare i diversi standard e requisiti specifici del settore.
Approccio incentrato sul cliente
Sincere Tech apprezza i prezzi competitivi, l'alta qualità della produzione e la buona qualità del servizio. D'altra parte, in qualità di partner affidabile per le aziende internazionali, le capacità di gestione dei progetti dell'azienda sono forti, la comunicazione in inglese tecnico è chiara e la soddisfazione dei clienti è elevata.
Seasky Medical
Seasky Medical, azienda cinese di stampaggio a iniezione, produce materie plastiche per uso medico. L'azienda ha sede a Shenzhen, nel Guangdong, dal 1999 e fornisce le migliori soluzioni di stampaggio a iniezione. Offre una progettazione accurata degli stampi, la selezione dei materiali e lo stampaggio a iniezione, oltre a occuparsi dello sviluppo dei prodotti, in modo che i componenti medicali siano all'altezza dei più alti standard di qualità e sicurezza.
La certificazione ISO 8 di Seasky Medical garantisce la produzione di dispositivi medici come siringhe, componenti per flebo e strumenti chirurgici in un ambiente privo di contaminazioni. L'azienda, con oltre dieci anni di esperienza, è nota per la fornitura di uno stampaggio a iniezione medicale affidabile e accurato, con il quale serve i fornitori di servizi sanitari a livello mondiale.
Shenzhen Silver Basis Technology Co.
Shenzhen Silver Basis Technology è un'azienda cinese di stampaggio professionale, dedicata alla produzione di stampi per il settore automobilistico e industriale. Costituita nel 1993, l'azienda è uno dei fornitori più affidabili per marchi famosi al mondo come Peugeot e ZTE, fornendo modelli per diversi usi.
Silver Basis offre una gamma completa di servizi per lo stampaggio dei metalli, la pressofusione, la fabbricazione di stampi e il collaudo dei prodotti. Grazie alla sua esperienza nello stampaggio a iniezione per il settore automobilistico, l'azienda è in grado di produrre parti interne ed esterne del veicolo che sono durevoli e precise. Poiché l'azienda si concentra sulla qualità, ha ottenuto le certificazioni ISO 9001 e ISO 14001 e per questo motivo è stata scelta dai produttori internazionali di automobili e di elettronica.
JMT Automotive Mold Co., Ltd
JMT Automotive Mold Co., Ltd è una rinomata azienda cinese di stampaggio a iniezione che si occupa di progettazione e produzione di stampi per autoveicoli. Dalla sua fondazione nel 2005 con sede a Taizhou, Zhejiang, l'azienda ha costruito un solido sistema di produzione per soddisfare le crescenti esigenze dell'industria automobilistica.
JMT Automotive Mold ha un'esperienza operativa in un sito produttivo di 23.000 metri quadrati ed è uno dei produttori specializzati in stampi SMC, stampi per elettrodomestici e stampi industriali. Dispone di macchinari CNC ad alta velocità, di attrezzature per test di precisione e di macchinari all'avanguardia per lo stampaggio a iniezione che garantiscono un elevato standard di produzione. JMT Automotive mantiene l'innovazione tecnologica e l'ingegneria di precisione e continua a offrire una produzione di stampi affidabile per i clienti nazionali ed esteri.
TK Mold Ltd
Fondata nel 1978, TK Mold Ltd è una nota azienda cinese di stampaggio con oltre 40 anni di esperienza nella produzione di stampi in plastica. L'azienda è stata fondata nel 1983 ed è specializzata nello sviluppo di stampi ad alta precisione per apparecchi medici, elettronica di consumo, elettrodomestici intelligenti e componenti automobilistici.
TK Mold offre soluzioni avanzate di stampaggio a iniezione per il suo gruppo globale di clienti dalla sua base di 5 impianti di produzione, tra cui uno in Germania. Essendo un pioniere nell'adozione di tecnologie all'avanguardia, automazione e produzione di precisione, l'azienda è molto apprezzata dalle industrie che richiedono componenti in plastica ad alte prestazioni. Tutti i prodotti di TK Mold sono certificati ISO 9001, ISO 13485 e ISO 14001 per garantire che rientrino negli standard internazionali di qualità e sicurezza.
Guangdong Yizumi Precision Machinery Co., Ltd
Guangdong Yizumi è un'azienda cinese leader nello stampaggio a iniezione che produce macchine per lo stampaggio a iniezione ad alte prestazioni e componenti in plastica. Yizumi è stata fondata nel 2002 e la sua sede centrale si trova a Foshan, nel Guangdong. Con una base produttiva di oltre 600.000 metri quadrati e quasi 3.000 dipendenti, Yizumi si è trasformata in un marchio mondiale.
Yizumi ha vinto numerosi premi di settore per le sue innovazioni nella tecnologia di stampaggio a iniezione ed è nota per le sue soluzioni di stampaggio innovative. Nel 2015, l'azienda è diventata la prima società cinese di stampaggio ad essere quotata alla Borsa di Shenzhen. Yizumi si sta concentrando sul settore automobilistico, sull'elettronica di consumo e sulle applicazioni industriali, diventando un leader del settore grazie ai suoi macchinari all'avanguardia e allo stampaggio ad alta precisione.
Sfide e considerazioni nella scelta di un'azienda cinese di stampaggio
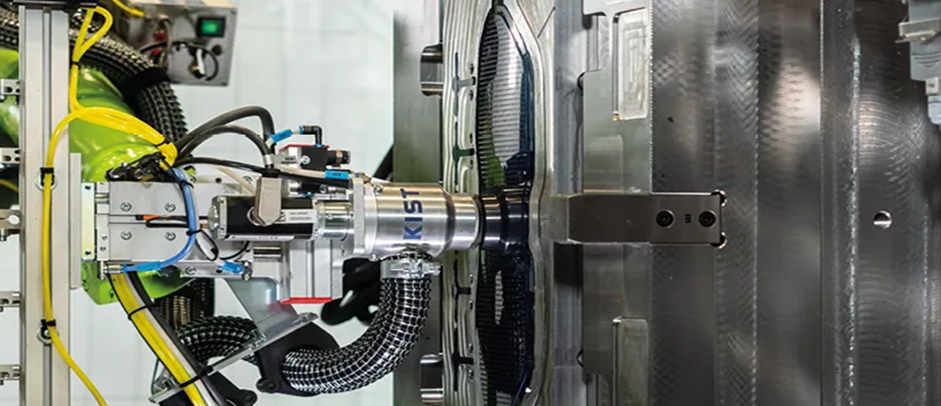
Le società minerarie cinesi presentano molti vantaggi, tuttavia, prima di impegnarsi con un produttore, le aziende dovrebbero essere consapevoli di alcuni aspetti.
1. Controllo qualità e conformità
I produttori non seguono tutti gli stessi standard di qualità. Prima di scegliere un fornitore, è bene verificare le certificazioni e testare un campione.
2. Protezione della proprietà intellettuale
La produzione in Cina può essere un problema per l'outsourcing della protezione della proprietà intellettuale (IP). Per evitare di perdere i propri progetti e mantenerli al sicuro, le aziende dovrebbero collaborare con partner fidati e accordi legali.
3. Barriere linguistiche e di comunicazione
Anche se diversi produttori cinesi dispongono di team di vendita che parlano inglese, la comunicazione non è sempre semplice. La documentazione e gli accordi sono preparati per evitare malintesi.
4. Logistica e spedizioni
Tuttavia, gestire grandi ordini a livello internazionale può essere complesso e costoso. Le aziende di stampaggio cinesi devono essere consapevoli delle normative doganali, dei tempi di consegna e dei costi di trasporto.
Tendenze future dello stampaggio a iniezione in Cina
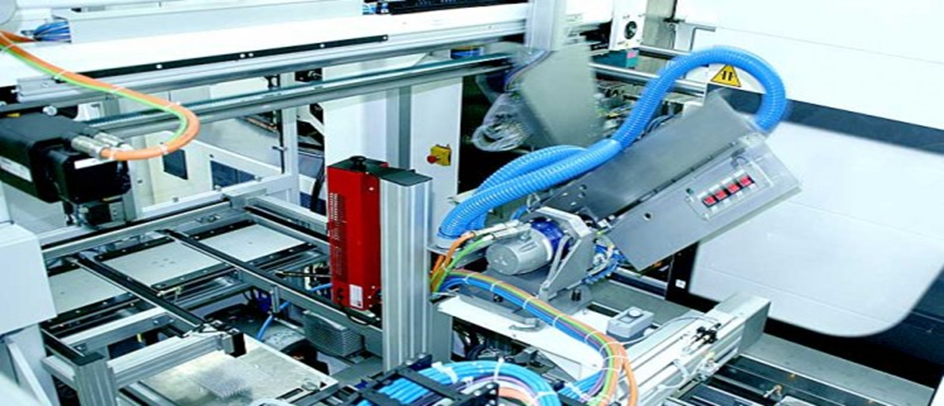
Con le nuove tecnologie, si sviluppa l'industria cinese dello stampaggio per soddisfare le nuove esigenze del mercato. Le tendenze principali includono:
1. Materiali sostenibili ed eco-compatibili
Con l'aumento dei rifiuti plastici in Cina, molte aziende di stampaggio sono diventate più attente alle normative ambientali e stanno sviluppando materiali plastici biodegradabili e riciclati.
2. Produzione intelligente e Industria 4.0
L'automazione e il controllo qualità guidato dall'intelligenza artificiale, il passaggio completo da un processo incentrato sull'uomo a una fabbrica intelligente abilitata dall'IoT hanno trasformato completamente il processo di stampaggio a iniezione, rendendo la produzione più efficiente e riducendo gli sprechi.
3. Maggiore personalizzazione e produzione su richiesta
L'attenzione delle aziende si sta spostando verso la produzione on-demand e in piccoli lotti per i mercati di nicchia e lo sviluppo rapido dei prodotti.
Conclusione
Le aziende cinesi di stampaggio a iniezione sono parte integrante dell'industria manifatturiera globale, in quanto forniscono soluzioni innovative, di alta qualità ed economicamente vantaggiose per i clienti. Alcuni di questi produttori lavorano parti in plastica per componenti automobilistici, dispositivi medici e altri settori correlati. Quando scelgono un'azienda di stampaggio cinese, le entità commerciali devono esaminare rigorosamente gli standard di qualità, la convenienza della comunicazione e la logistica per assicurarsi una partnership di successo. Grazie alla continua tendenza al progresso tecnologico e alle pratiche sostenibili, le aziende di stampaggio cinesi continueranno a essere leader nello stampaggio a iniezione per molti anni ancora. A fronte dei numerosi vantaggi, le aziende dovrebbero comunque valutare il controllo della qualità, la protezione della proprietà intellettuale, le difficoltà di comunicazione e la logistica prima di scegliere un partner di stampaggio cinese. Tuttavia, se la ricerca è stata condotta in modo approfondito e se si collabora con produttori che producono con qualità e sono certificati per il lavoro, le aziende possono raccogliere i benefici dell'esperienza cinese nello stampaggio a iniezione. In futuro, lo stampaggio a iniezione in Cina sarà caratterizzato da materiali sostenibili, produzione intelligente, produzione ad alta velocità e automazione guidata dalla produzione, abbinata a plastiche biodegradabili e tecnologie dell'Industria 4.0, la Cina farà ancora i maggiori passi avanti nello stampaggio a iniezione globale. Le aziende di stampaggio cinesi, con i loro continui progressi e il loro impegno per modificare il volto della produzione cinese, continueranno a dare impulso alla produzione moderna.
Domande frequenti (FAQ)
1. Perché è popolare la produzione di stampaggio a iniezione dalla Cina?
La scelta della Cina per lo stampaggio a iniezione offre il vantaggio di una produzione conveniente, di una tecnologia moderna, di una forza lavoro ben formata e di una catena di fornitura ben organizzata. Ci sono molti produttori che seguono gli standard di qualità internazionali e offrono soluzioni personalizzate con tempi di consegna molto rapidi.
2. In che modo le aziende cinesi di stampaggio a iniezione possono beneficiare delle industrie?
Tutti questi settori dipendono dallo stampaggio a iniezione cinese, come quello automobilistico, elettronico, dei dispositivi medici, dell'imballaggio e dei beni di consumo. I produttori cinesi sono in grado di produrre in modo efficace ed economico i componenti in plastica di alta precisione necessari per questi settori.
3. Come fanno le aziende cinesi di stampaggio a iniezione a garantire la qualità dei prodotti?
Le aziende affidabili di stampaggio cinesi controllano rigorosamente la qualità dalle materie prime ai prodotti finiti e ottengono i seguenti certificati: ISO 9001, ISO 13485 (medicale) e IATF 16949 (componenti automobilistici). Il livello dei processi di collaudo e i sistemi di ispezione automatizzati li rendono all'altezza di standard elevati.
4. Una selezione di produttori di stampaggio cinesi qual è?
Le aziende devono prendere in considerazione le certificazioni di qualità, l'esperienza, le capacità produttive, la protezione della proprietà intellettuale e la capacità di comunicare e fornire supporto logistico. Per spianare la strada a una buona collaborazione, è necessario effettuare test a campione e garantire la capacità di consegna dell'azienda.
5. Quali sono le prospettive dell'industria cinese dello stampaggio a iniezione?
I tempi che stiamo vivendo impongono all'industria di trovare nuove tendenze per risolverli, tra cui le plastiche sostenibili e biodegradabili, l'automazione alimentata dall'intelligenza artificiale, le fabbriche intelligenti e la produzione on demand. Questi progressi renderanno la produzione più efficiente, ridurranno gli sprechi e forniranno alla domanda in continua crescita di risposte produttive ecocompatibili.