O que é molde de injeção plástica?
O que é molde de injeção de plástico?
Moldagem por injeção de plástico é um dos métodos mais eficazes de fabricação de componentes plásticos, proporcionando altos níveis de precisão e eficiência de produção. O processo envolve a fusão de materiais plásticos e sua injeção em um molde pré-projetado que molda o plástico em uma forma específica à medida que ele esfria. Este artigo aborda os fundamentos dos moldes de injeção de plástico, detalhando os tipos, os componentes, os processos de fabricação e as considerações para selecionar o molde certo para atender a necessidades específicas de produção.
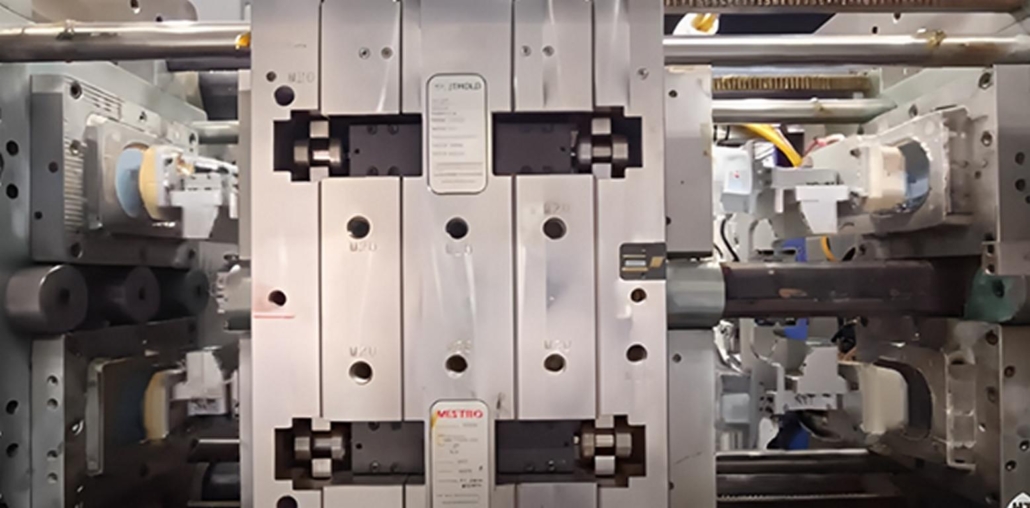
Introdução à moldagem por injeção de plástico
Moldagem por injeção de plástico é uma técnica usada para criar peças plásticas complexas e precisas em grandes quantidades. Desde o seu desenvolvimento no final do século XIX, o processo transformou o setor de manufatura, permitindo a produção em alta velocidade de peças em uma ampla gama de setores, incluindo automotivo, eletrônico, dispositivos médicos e bens de consumo.
Vantagens da moldagem por injeção de plástico
- Alta eficiência e velocidade: A moldagem por injeção oferece um tempo de ciclo de produção curto, permitindo taxas de produção rápidas. Vários moldes podem ser executados simultaneamente para aumentar ainda mais a produção.
- Repetibilidade: O processo foi projetado para criar peças idênticas em várias execuções de produção, o que é especialmente valioso em setores que exigem alta precisão e consistência.
- Capacidades de projeto complexas: Os moldes de injeção são capazes de criar geometrias complexas, incluindo paredes finas, cortes inferiores e detalhes de superfície complexos.
- Flexibilidade do material: A moldagem por injeção pode usar uma ampla variedade de termoplásticos e plásticos termofixos, cada um escolhido para fornecer propriedades específicas ao produto acabado.
- Desperdício mínimo: Com moldes adequadamente projetados e controles de processo avançados, a moldagem por injeção produz pouco ou nenhum desperdício de material.
Visão geral do molde de injeção plástica
A molde de injeção plástica é uma ferramenta complexa projetada para moldar material plástico fundido em um produto acabado. O molde geralmente é feito de aço ou alumínio e é composto de duas metades principais: a cavidade e o núcleo, cada um responsável por formar o exterior e o interior da peça final. Devido às altas pressões envolvidas na moldagem por injeção, esses moldes devem ser robustos, resistentes ao desgaste e capazes de manter sua forma sob ciclos repetidos.
Cada molde inclui várias peças que trabalham em uníssono para garantir a precisão na formação, no resfriamento e na ejeção da peça. Veja a seguir um detalhamento dos principais componentes de um molde de injeção e suas respectivas funções.
Principais componentes do molde
- Cavidade e núcleo do molde de injeção: Esses são os principais elementos do molde. O lado da cavidade (normalmente o lado "A") é responsável por moldar a superfície externa da peça, enquanto o lado do núcleo (o lado "B") molda o interior. Juntos, eles formam o espaço oco que define a geometria da peça. A escolha dos materiais da cavidade e do núcleo depende do volume de produção, pois os materiais de alto desgaste, como o aço temperado, costumam ser usados para a produção de grandes volumes, enquanto os metais mais macios podem ser suficientes para as produções menores.
- Controles deslizantes e levantadores: Controles deslizantes e levantadores permitem a criação de cortes inferiores ou geometrias complexas que não podem ser formadas com um molde simples de duas partes. Os controles deslizantes se movem lateralmente quando o molde se abre, criando espaço para quaisquer saliências ou ranhuras, enquanto os levantadores se movem em um ângulo para liberar a peça. Ambos são fundamentais para permitir que peças com formas complexas sejam ejetadas sem danos.
- Sistemas de canal, canal e porta: O abeto canaliza o plástico derretido do bico da máquina de injeção para o molde, conduzindo-o para o corredor sistema que direciona o plástico para cada cavidade em um molde com várias cavidades. Portões são os pontos de entrada finais do plástico fundido na cavidade, onde ele esfria e toma forma. Cada componente desse sistema afeta a uniformidade e a rapidez com que o material preenche o molde, influenciando a qualidade da peça e o tempo de ciclo.
- Sistema de ejetor: Após o resfriamento e a solidificação da peça moldada, o sistema ejetor empurra a peça para fora da cavidade do molde. O sistema ejetor geralmente inclui pinos ou placas que aplicam força à peça pelo lado do núcleo, garantindo que ela seja liberada sem danos. Esse sistema deve ser cronometrado e controlado com precisão para evitar a deformação ou a aderência da peça.
- Canais de resfriamento: Canais de resfriamento são passagens dentro das placas do molde que transportam o líquido de arrefecimento, geralmente água, para absorver e dissipar o calor do plástico fundido. O resfriamento eficiente é fundamental para o processo de moldagem, pois reduz o tempo de ciclo e afeta a precisão dimensional e as propriedades mecânicas da peça. O projeto dos canais de resfriamento - sejam canais conformes, defletores ou borbulhantes - pode afetar significativamente o desempenho e a eficiência do molde.
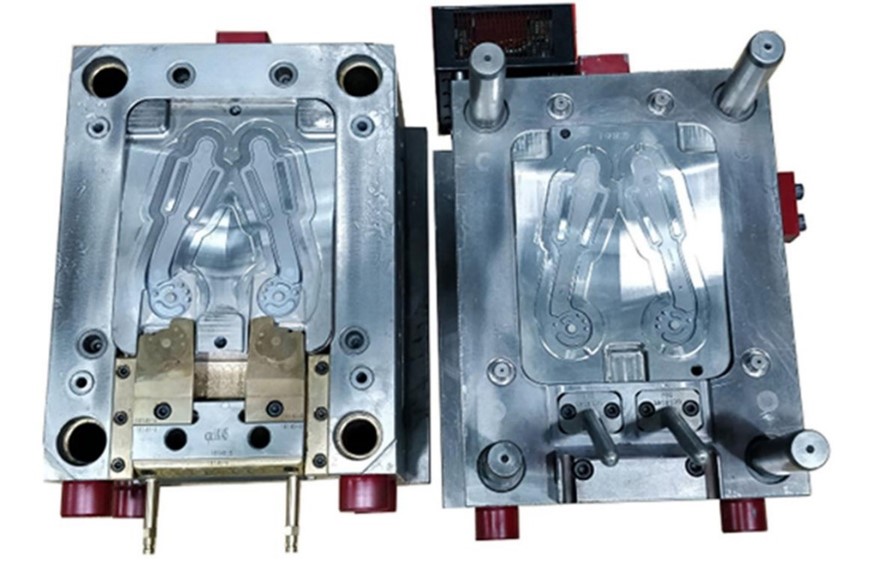
Estrutura de um molde de injeção plástica
A estrutura de um molde de injeção de plástico é projetada para suportar as pressões, as temperaturas e as tensões mecânicas dos repetidos ciclos de moldagem. Veja a seguir uma análise mais detalhada dos componentes estruturais e como eles funcionam no processo de moldagem:
- Placas A e B: Essas são as placas principais do molde que seguram a cavidade e o núcleo, respectivamente. A placa A é estacionária, enquanto a placa B se move para abrir e fechar o molde. Essas placas são projetadas para manter o alinhamento e suportar as pressões da injeção.
- Placas de fixação: Essas placas prendem o molde dentro da unidade de fixação da máquina de moldagem por injeção. Seu design deve garantir a estabilidade durante a fase de injeção de alta pressão para evitar desalinhamentos ou movimentos que possam causar defeitos.
- Linha de separação: A linha de separação é onde as placas A e B se encontram. Uma linha de partição bem alinhada é essencial para evitar defeitos como flash (camadas finas de plástico nas costuras do molde) e garantir uma liberação suave da peça. A localização da linha de partição geralmente depende do projeto da peça e dos requisitos do molde.
- Canais de resfriamento: Os canais de resfriamento são essenciais para manter o desempenho do molde e reduzir os tempos de ciclo. Os canais são cuidadosamente projetados para garantir o resfriamento uniforme da cavidade e do núcleo do molde, o que é fundamental para evitar defeitos como empenamento ou tensões internas. Os tipos de canais de resfriamento incluem:
- Resfriamento conformacional: Canais que seguem o contorno da peça, proporcionando um resfriamento consistente que corresponde ao formato da cavidade do molde.
- Resfriamento por baffle: Utiliza insertos para guiar o fluxo de refrigerante e é comumente usado quando o tamanho do molde limita a colocação do canal.
- Resfriamento de borbulhador: Os tubos borbulhadores criam resfriamento adicional em áreas específicas, especialmente para seções espessas que exigem resfriamento mais rápido.
- Pinos de resfriamento: Os pinos embutidos no núcleo proporcionam resfriamento localizado em seções espessas, ajudando a gerenciar a distribuição de temperatura em moldes maiores ou com várias cavidades.
O projeto de resfriamento é altamente influente no tempo de ciclo e, por extensão, no custo e na produtividade do processo de moldagem por injeção.
Tipos de moldes de injeção de plástico
Existem vários tipos de moldes de injeção de plástico para atender às diferentes necessidades de produção, complexidades e requisitos de peças. Veja a seguir alguns dos tipos mais comumente usados:
- Moldes de cavidade única: Esses moldes produzem uma peça por ciclo. Geralmente, são usados para volumes de produção menores ou peças de alta precisão em que é necessário um controle mais rígido de cada peça individual. Os moldes de cavidade única têm a vantagem de uma configuração mais simples e são mais econômicos para uma produção limitada.
- Moldes de múltiplas cavidades: Nos moldes de múltiplas cavidades, várias cavidades idênticas permitem a produção de várias peças em um único ciclo. Isso aumenta a eficiência e é ideal para a produção de grandes volumes, reduzindo o tempo de ciclo por peça e os custos gerais. No entanto, os moldes com múltiplas cavidades são mais complexos de projetar e exigem um equilíbrio preciso no sistema de canais para garantir um enchimento uniforme.
- Moldes familiares: Os moldes familiares contêm diferentes cavidades em um único molde, permitindo a produção de vários componentes em um único ciclo. Isso é particularmente útil quando diferentes peças precisam ser moldadas juntas, como em montagens. No entanto, equilibrar a taxa de enchimento em peças de tamanhos diferentes pode ser um desafio e pode levar a defeitos se não for gerenciado com cuidado.
- Moldes de câmara quente vs. moldes de câmara fria:
- Moldes de câmara quente: Use componentes aquecidos para manter o plástico derretido dentro do sistema de canal, minimizando o desperdício e acelerando o ciclo. Os canais quentes são eficientes para produção de alto volume, mas exigem controle cuidadoso e custos iniciais mais altos.
- Moldes de câmara fria: Permita que o plástico no canal esfrie e solidifique a cada ciclo. O canal solidificado normalmente é ejetado com a peça, que pode exigir processamento secundário para ser removida. Os moldes de canal frio são mais simples e menos dispendiosos, o que os torna adequados para produção de menor volume.
- Moldes de duas placas vs. moldes de três placas:
- Moldes de duas placas: Consistem em uma única linha de corte e são mais simples em seu design. São comumente usados para peças simples com requisitos de porta única.
- Moldes de três placas: Inclua uma placa adicional, criando duas linhas de separação. Isso permite sistemas de canais mais complexos, como o canal central, que melhora a estética da peça e pode reduzir o processamento pós-molde.
- Moldes rotativos e de pilha:
- Moldes de empilhamento: Os moldes empilhados usam vários níveis de cavidades, dobrando ou triplicando efetivamente a capacidade de produção sem aumentar os requisitos de força de fixação da máquina. Eles são vantajosos para a produção de volumes muito altos, mas exigem maquinário e manuseio avançados.
- Moldes rotativos: Os moldes rotativos permitem a sobremoldagem e a montagem no molde por meio da rotação das cavidades entre as estações. Eles costumam ser usados para peças multimateriais, como as que exigem uma combinação de plásticos rígidos e flexíveis.
Cada tipo de molde tem vantagens e desafios distintos, e a seleção do molde certo depende de fatores como volume de produção, complexidade da peça e requisitos de material.

Processo de moldagem por injeção de plástico
O processo de moldagem por injeção consiste em várias etapas importantes, cada uma delas essencial para a produção de peças de alta qualidade. Veja a seguir uma análise detalhada:
- Fixação: O molde é fixado com firmeza para preparar a injeção de plástico fundido. A força de fixação é calculada com base na pressão da cavidade para garantir que não haja vazamento de plástico pela linha de separação.
- Injeção: O plástico derretido é injetado na cavidade do molde por meio do jito, do canal e da porta. A velocidade, a pressão e a temperatura da injeção devem ser controladas com precisão, pois afetam o fluxo e a qualidade do material na cavidade.
- Resfriamento: O resfriamento começa assim que o plástico entra no molde. A taxa de resfriamento deve ser uniforme para evitar defeitos, como deformação ou encolhimento. Os canais de resfriamento desempenham um papel fundamental aqui, garantindo que o calor seja efetivamente dissipado do molde. Esse estágio geralmente é responsável pela maior parte do tempo do ciclo.
- Ejeção: Depois que a peça se solidifica, os pinos ou placas ejetores empurram a peça para fora do molde. A ejeção deve ser feita com cuidado para evitar danos à peça, especialmente se ela tiver características complexas ou for feita de material frágil.
Cada estágio do processo de moldagem por injeção requer um controle preciso para produzir peças que atendam aos padrões de qualidade e, ao mesmo tempo, minimizem o tempo de ciclo e os custos de produção.
Canais de resfriamento de moldes de injeção
Os canais de resfriamento são cruciais no processo de moldagem por injeção de plástico, pois influenciam significativamente o tempo de ciclo, a qualidade da peça e a eficiência da produção. O projeto de resfriamento adequado é essencial para evitar defeitos como empenamento, encolhimento ou tensões internas que podem ocorrer se o resfriamento for desigual ou muito rápido.
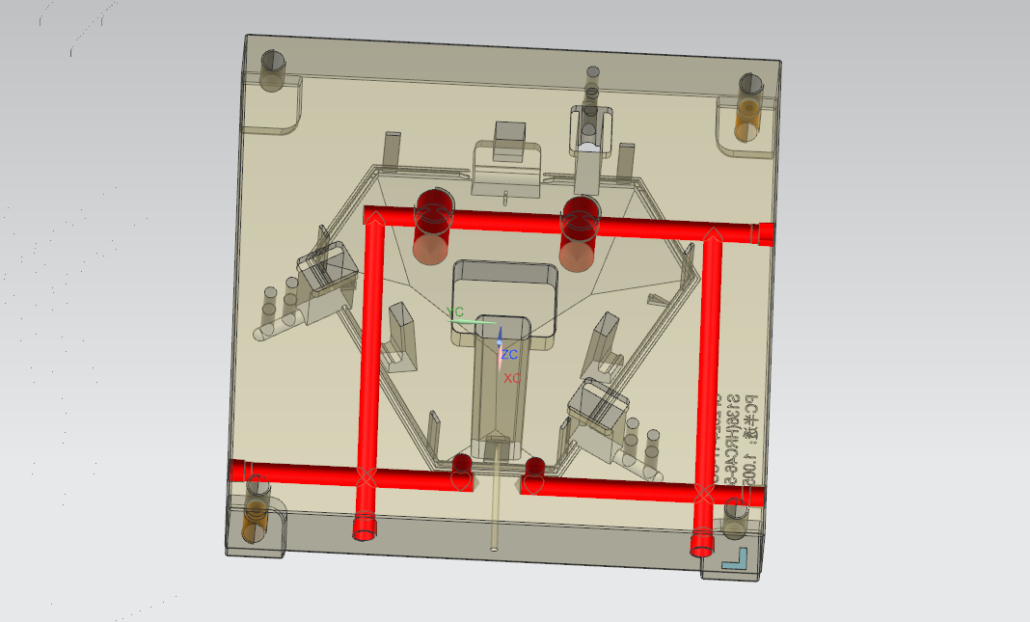
Tipos de canais de resfriamento em moldes de injeção
- Resfriamento conformacional: Essa técnica avançada envolve o projeto de canais de resfriamento que seguem o contorno da peça dentro do molde. O resfriamento conformal proporciona um resfriamento consistente em toda a superfície da peça, reduzindo o tempo de ciclo e melhorando a qualidade da peça. Normalmente obtido por meio de impressão 3D e outros métodos avançados de fabricação, o resfriamento conformacional é ideal para formas complexas em que os canais tradicionais seriam ineficazes.
- Canais de resfriamento retos: Esses canais são caminhos simples e retos perfurados nas placas do molde. Embora sejam simples e econômicos, eles são menos eficientes do que o resfriamento conformacional em geometrias de molde complexas. Os canais retos são usados com frequência em moldes padrão, onde é possível obter um resfriamento uniforme.
- Resfriamento por baffle: Baffles são inserções planas que redirecionam o fluxo de refrigerante dentro do molde, especialmente em espaços apertados onde os canais retos não conseguem chegar. O resfriamento por defletores é eficiente para gerenciar a temperatura em moldes menores ou áreas específicas, mas pode não proporcionar o resfriamento uniforme necessário para projetos altamente complexos.
- Resfriamento de borbulhador: Os borbulhadores são tubos que circulam o líquido de arrefecimento em áreas pequenas e confinadas do molde, o que é particularmente benéfico para seções espessas de uma peça que requerem resfriamento mais rápido. Os borbulhadores são uma opção comum quando os canais tradicionais não conseguem fornecer resfriamento suficiente para áreas densas.
- Pinos de resfriamento: Os pinos de resfriamento são inseridos no núcleo do molde para auxiliar no resfriamento de peças mais espessas. Esses pinos são ideais para resfriamento localizado em moldes maiores ou em áreas específicas propensas a superaquecimento. Eles também são comumente usados em moldes com várias cavidades, onde a manutenção de temperaturas consistentes é um desafio.
O impacto do design do canal de resfriamento no tempo de ciclo e na qualidade
O projeto dos canais de resfriamento afeta tanto a eficiência quanto a qualidade do processo de moldagem por injeção:
- Redução do tempo de ciclo: Canais de resfriamento eficientes ajudam a reduzir o tempo de ciclo, pois as peças esfriam e solidificam mais rapidamente. Tempos de ciclo mais curtos significam maior rendimento da produção e menores custos de fabricação.
- Precisão dimensional: O resfriamento consistente em todo o molde ajuda a evitar deformações ou encolhimento, garantindo que as peças mantenham a forma e as dimensões pretendidas.
- Acabamento da superfície: O resfriamento pode afetar a qualidade da superfície das peças moldadas. O resfriamento uniforme minimiza as tensões que, de outra forma, poderiam danificar a superfície da peça, resultando em um melhor acabamento.
O projeto adequado do canal de resfriamento é uma consideração essencial durante a fase de projeto do molde, pois determina a eficiência do molde e a qualidade das peças moldadas.
Defeitos e problemas de moldagem por injeção
Apesar da precisão da moldagem por injeção, podem ocorrer vários defeitos comuns. Entender esses problemas e como reduzi-los é essencial para manter a qualidade e minimizar o desperdício.
Defeitos comuns de moldagem por injeção
- Deformação: O empenamento é uma deformação que ocorre quando diferentes partes do molde são resfriadas em taxas desiguais. Esse defeito geralmente surge em moldes complexos com canais de resfriamento inadequados ou tempo de resfriamento insuficiente. Para evitar o empenamento, os canais de resfriamento devem ser projetados para garantir um resfriamento uniforme, e o tempo de resfriamento deve ser cuidadosamente monitorado.
- Marcas de pia: As marcas de afundamento aparecem como depressões na superfície de seções mais espessas de uma peça, geralmente devido a resfriamento inadequado ou pressão de retenção inadequada. Usar a pressão ideal e garantir o resfriamento adequado, especialmente em áreas espessas, pode ajudar a evitar marcas de afundamento.
- Flash: O flash ocorre quando o plástico fundido escapa da cavidade na linha de separação devido à pressão excessiva de injeção ou ao desalinhamento. O alinhamento preciso e as configurações de pressão adequadas são fundamentais para evitar o flash.
- Linhas de fluxo: As linhas de fluxo são linhas visíveis na superfície de uma peça causadas por variações na taxa de resfriamento do plástico à medida que ele flui pelo molde. O ajuste da velocidade e da temperatura de injeção pode ajudar a reduzir as linhas de fluxo.
- Fotos curtas: Os disparos curtos ocorrem quando a cavidade do molde não é completamente preenchida, geralmente devido à baixa pressão de injeção ou à insuficiência de material. Aumentar a pressão de injeção ou garantir uma alimentação suficiente de material pode resolver esse problema.
- Linhas de solda: As linhas de solda ocorrem onde duas frentes de fluxo se encontram, geralmente criando pontos fracos na peça. O ajuste da velocidade de injeção ou o uso de um sistema de canal quente pode reduzir as linhas de solda.
- Fragilidade e rachaduras: Esses problemas geralmente resultam de resfriamento inadequado ou pressão de injeção excessivamente alta, o que induz a tensões internas. O projeto de resfriamento adequado e o controle ideal da pressão ajudam a reduzir a fragilidade e as rachaduras.
Ao compreender e controlar esses fatores - como velocidade de injeção, temperatura e projeto de resfriamento -, os fabricantes podem reduzir os defeitos e melhorar a qualidade geral das peças moldadas.
Processo de fabricação de moldes de injeção
A fabricação de um molde de injeção envolve várias etapas, cada uma delas essencial para garantir a durabilidade, a precisão e a funcionalidade do molde. Veja a seguir um detalhamento das etapas típicas da fabricação de um molde de injeção de plástico:

- Design e engenharia: A fase de projeto do molde é crucial, pois estabelece a base para todas as etapas subsequentes. Usando o software CAD, os engenheiros criam um modelo 3D do molde, incorporando todos os detalhes necessários, inclusive o formato da cavidade, os canais de resfriamento, o sistema de ejeção e a linha de separação. Esse modelo é então submetido a simulações para prever problemas e otimizar o desempenho antes do início da produção física do molde.
- Seleção de materiais: Dependendo do volume de produção e dos requisitos da peça, os materiais são selecionados de acordo com a durabilidade e a resistência ao desgaste. Entre os materiais comuns estão o aço endurecido para moldes de grande volume e o alumínio para aplicações de menor volume. Os moldes de aço são preferidos para longas tiragens devido à sua durabilidade, enquanto os moldes de alumínio são mais fáceis de usinar e econômicos para produção de pequenas tiragens.
- Usinagem CNC e EDM (usinagem por descarga elétrica): A usinagem CNC (Controle Numérico Computadorizado) é usada para esculpir a forma primária do molde com alta precisão. A EDM é então empregada para criar geometrias complexas, detalhes finos e formas intrincadas na cavidade do molde que as máquinas CNC não conseguem alcançar. A combinação de CNC e EDM garante a precisão e a complexidade necessárias para o molde.
- Tratamento térmico e endurecimento de superfície: Os moldes de aço geralmente são tratados termicamente para aumentar a dureza e a durabilidade. Tratamentos de superfície, como nitretação ou cromagem, também são aplicados para aumentar a resistência ao desgaste, reduzir a corrosão e prolongar a vida útil do molde. Os moldes de alumínio, embora mais macios, também podem receber anodização para melhorar a dureza da superfície.
- Montagem e polimento: Após a usinagem, os componentes do molde são montados, incluindo o encaixe da cavidade, do núcleo, dos pinos ejetores, dos controles deslizantes e dos canais de resfriamento. O polimento de precisão é então aplicado para obter um acabamento superficial de alta qualidade, especialmente para peças que exigem uma superfície estética ou lisa.
- Testes e validação: Antes da produção total, o molde passa por um teste de funcionamento para garantir que atenda às especificações. Essa etapa, conhecida como amostragem T1, testa o desempenho do molde, identificando possíveis problemas com resfriamento, ejeção ou alinhamento. Todos os ajustes são feitos para otimizar o desempenho do molde para a produção em massa.
- Garantia de qualidade e aprovação: Após a validação, o molde é inspecionado para confirmar que atende a todos os padrões de qualidade. São feitas medições para verificar a precisão dimensional e, se necessário, são feitos ajustes. Somente depois de passar pelas verificações de qualidade é que o molde é aprovado para produção total.
Cada etapa do processo de fabricação do molde é fundamental para garantir que o molde final tenha um desempenho consistente e eficiente em ambientes de produção de alto volume.
Escolhendo o molde de injeção certo para sua aplicação
A seleção do molde de injeção correto é fundamental para otimizar a produção, minimizar os custos e garantir a qualidade do produto. Aqui estão alguns fatores importantes a serem considerados na escolha de um molde de injeção:
- Volume de produção: O volume de produção previsto desempenha um papel importante na seleção do molde. A produção de alto volume normalmente requer moldes duráveis feitos de aço temperado, enquanto os moldes de alumínio são adequados para pequenas tiragens ou prototipagem.
- Complexidade e design de peças: Peças complexas com geometrias intrincadas, cortes inferiores ou paredes finas podem exigir recursos de molde especializados, como elevadores, controles deslizantes ou configurações de múltiplas cavidades. Quanto mais complexa a peça, mais detalhado deve ser o molde, o que pode afetar o custo e o tempo de produção.
- Escolha do material: Diferentes materiais plásticos têm características exclusivas de fluxo, encolhimento e resfriamento. Os moldes projetados para materiais rígidos, como o policarbonato, podem exigir configurações de resfriamento ou materiais de molde diferentes dos moldes projetados para plásticos flexíveis, como o polietileno.
- Requisitos de tempo de ciclo: Tempos de ciclo rápidos são essenciais para a produção de alto volume. Um molde bem projetado com canais de resfriamento eficientes e um sistema de ejeção ideal pode reduzir o tempo de ciclo, aumentando a produtividade e reduzindo os custos.
- Considerações sobre custos: Os moldes são um investimento de longo prazo, e os custos podem variar significativamente com base no material, na complexidade e no tipo de molde. Embora os moldes de múltiplas cavidades ou de câmara quente possam ser mais caros inicialmente, eles podem proporcionar economia de custos a longo prazo, aumentando a eficiência e reduzindo o desperdício.
- Longevidade do molde: Para produção contínua ou de alto volume, os moldes devem ser projetados para longevidade com materiais duráveis e tratamentos de superfície. Recursos como endurecimento e revestimento ajudam a garantir que o molde resista ao uso repetido sem desgaste ou degradação.
Ao avaliar cuidadosamente esses fatores, os fabricantes podem selecionar o molde certo para atender às suas metas de produção, manter a qualidade das peças e maximizar a eficiência de custos.
Conclusão
Moldagem por injeção de plástico O molde de injeção é um dos pilares da manufatura moderna, permitindo a produção de peças plásticas precisas e de alta qualidade a baixo custo e em alta velocidade. A compreensão dos vários aspectos dos moldes de injeção - desde os componentes, tipos e processo de fabricação até o projeto de resfriamento e possíveis problemas - fornece informações valiosas para otimizar a produção.
A escolha do molde certo, a implementação de canais de resfriamento eficazes e a manutenção de um rigoroso controle de qualidade podem aumentar muito a eficiência e a qualidade da moldagem por injeção de plástico. Isso não apenas atende às demandas da produção de alto volume, mas também garante que as peças moldadas atendam às especificações e aos padrões estéticos exigidos. Com os avanços em materiais, design de moldes e tecnologias de resfriamento, a moldagem por injeção de plástico continua a evoluir, oferecendo ainda mais potencial
Deixe uma resposta
Quer participar da discussão?Sinta-se à vontade para contribuir!