Ce este matrița de injecție din plastic
Ce este mucegaiul de injecție din plastic?
Turnare prin injecție de plastic este una dintre cele mai eficiente metode de fabricare a componentelor din plastic, oferind niveluri ridicate de precizie și eficiență a producției. Procesul implică topirea materialelor plastice și injectarea lor într-o matriță prestabilită care modelează plasticul într-o formă specifică pe măsură ce se răcește. Acest articol analizează elementele esențiale ale matrițelor de injecție din plastic, detaliind tipurile, componentele, procesele de fabricație și considerentele pentru selectarea matriței potrivite pentru a răspunde nevoilor specifice de producție.
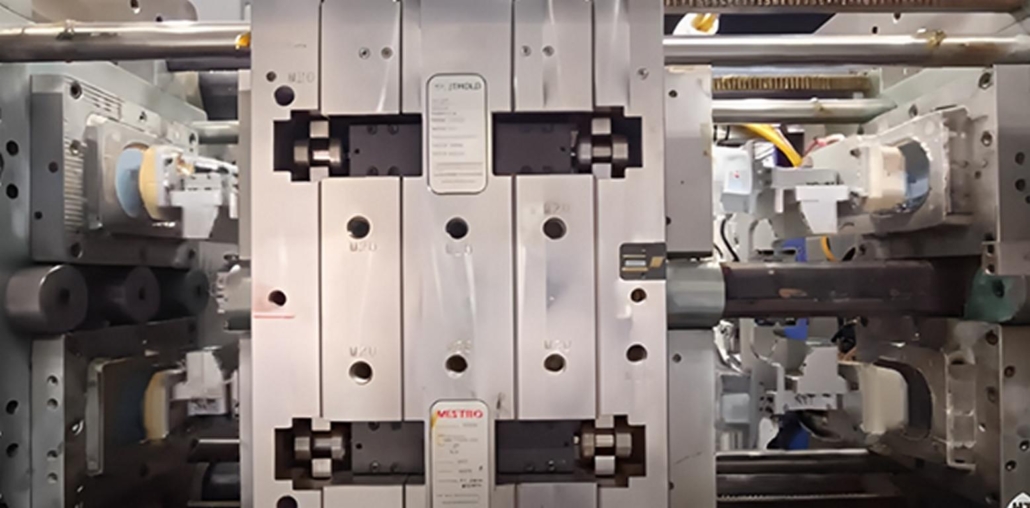
Introducere în turnarea prin injecție a materialelor plastice
Turnare prin injecție de plastic este o tehnică utilizată pentru a crea piese din plastic complexe și precise în cantități mari. De la dezvoltarea sa la sfârșitul secolului al XIX-lea, procesul a transformat industria prelucrătoare, permițând producția de piese la viteză mare într-o gamă largă de sectoare, inclusiv industria auto, electronică, dispozitive medicale și bunuri de consum.
Avantajele turnării prin injecție a plasticului
- Eficiență și viteză ridicate: Turnarea prin injecție oferă o durată scurtă a ciclului de producție, permițând rate rapide de producție. Mai multe matrițe pot funcționa simultan pentru a crește și mai mult producția.
- Repetabilitate: Procesul este conceput pentru a crea piese identice pe parcursul mai multor serii de producție, ceea ce este deosebit de valoros în industriile care necesită precizie și consecvență ridicate.
- Capacități complexe de proiectare: Matrițele de injecție sunt capabile să creeze geometrii complicate, inclusiv pereți subțiri, decupaje și detalii de suprafață complexe.
- Flexibilitatea materialului: Turnarea prin injecție poate utiliza o mare varietate de materiale plastice termoplastice și termorezistente, fiecare fiind ales pentru a oferi proprietăți specifice produsului finit.
- Deșeuri minime: Cu matrițe proiectate corespunzător și controale avansate ale procesului, turnarea prin injecție produce puține sau deloc deșeuri de material.
Prezentare generală a matriței de injecție din plastic
A matriță de injecție din plastic este un instrument complex conceput pentru a modela materialul plastic topit într-un produs finit. Matrița este de obicei fabricată din oțel sau aluminiu și este compusă din două jumătăți principale: cavitatea și miezul, fiecare responsabilă de formarea exteriorului și interiorului piesei finale. Datorită presiunilor ridicate implicate în turnarea prin injecție, aceste matrițe trebuie să fie robuste, rezistente la uzură și capabile să își mențină forma în cadrul unor cicluri repetate.
Fiecare matriță include mai multe părți care lucrează la unison pentru a asigura precizia în formarea, răcirea și ejectarea piesei. Mai jos este prezentată o defalcare a componentelor cheie ale unei matrițe de injecție și a funcțiilor lor respective.
Componente cheie ale matriței
- Cavitatea și miezul matriței de injecție: Acestea sunt elementele principale ale matriței. Partea cavității (de obicei partea "A") este responsabilă de modelarea suprafeței exterioare a piesei, în timp ce partea miezului (partea "B") modelează interiorul. Împreună, acestea formează spațiul gol care definește geometria piesei. Alegerea materialelor cavității și ale miezului depinde de volumul de producție, deoarece materialele cu uzură ridicată, cum ar fi oțelul călit, sunt adesea utilizate pentru producția de volum mare, în timp ce metalele mai moi pot fi suficiente pentru producții mai mici.
- Glisiere și ridicătoare: Slideri și ridicătoare permit crearea de adâncituri sau geometrii complexe care nu pot fi formate cu o matriță simplă din două părți. Glisierele se deplasează lateral atunci când matrița se deschide, creând spațiu pentru orice proeminențe sau caneluri, în timp ce elevatorii se deplasează în unghi pentru a elibera piesa. Ambele sunt esențiale pentru a permite ca piesele cu forme complexe să fie ejectate fără deteriorări.
- Sisteme de caneluri, canale și porți: The sprue canalizează plasticul topit din duza mașinii de injecție în matriță, conducându-l la alergător sistem care direcționează plasticul către fiecare cavitate a unei matrițe cu mai multe cavități. Porți sunt punctele finale de intrare a plasticului topit în cavitate, unde acesta se răcește și capătă formă. Fiecare componentă a acestui sistem afectează uniformitatea și rapiditatea cu care materialul umple matrița, influențând calitatea piesei și durata ciclului.
- Sistem ejector: După ce piesa turnată s-a răcit și s-a solidificat, sistem ejector împinge piesa afară din cavitatea matriței. Sistemul de ejecție include adesea pini sau plăci care aplică forță asupra piesei din partea miezului, asigurându-se că aceasta se eliberează fără a fi deteriorată. Acest sistem trebuie să fie sincronizat și controlat cu precizie pentru a preveni deformarea sau lipirea piesei.
- Canale de răcire: Canale de răcire sunt pasaje din plăcile matriței care transportă lichidul de răcire, de obicei apă, pentru a absorbi și disipa căldura din plasticul topit. Răcirea eficientă este esențială pentru procesul de turnare, deoarece reduce durata ciclului și afectează precizia dimensională și proprietățile mecanice ale piesei. Proiectarea canalelor de răcire - fie că este vorba de canale conforme, deflectoare sau cu barbotare - poate avea un impact semnificativ asupra performanței și eficienței matriței.
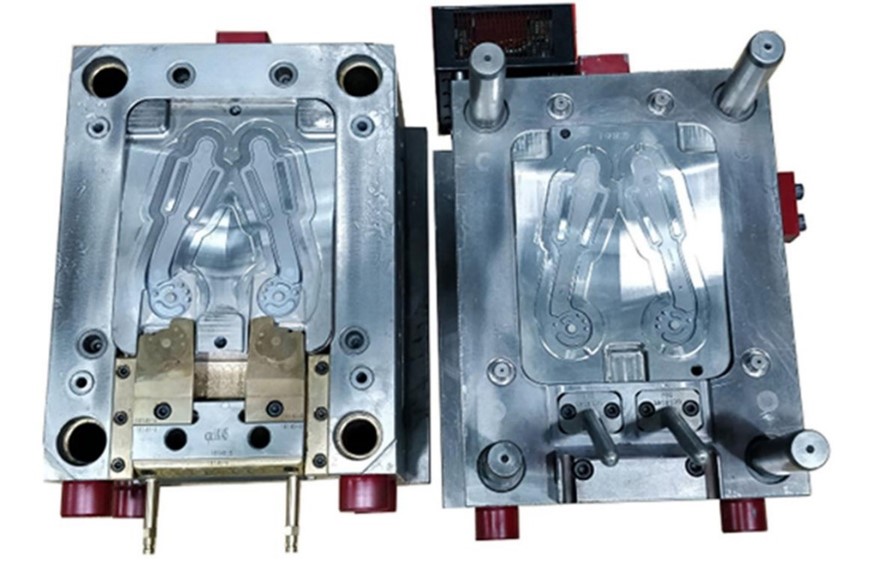
Structura unei matrițe de injecție din plastic
Structura unei matrițe de injecție din plastic este concepută pentru a rezista la presiunile, temperaturile și solicitările mecanice ale ciclurilor repetate de turnare. Iată o privire mai atentă la componentele structurale și la modul în care acestea funcționează în cadrul procesului de turnare:
- Plăci A și B: Acestea sunt plăcile principale ale matriței care susțin cavitatea și, respectiv, miezul. Placa A este fixă, în timp ce placa B se mișcă pentru a deschide și închide matrița. Aceste plăci sunt concepute pentru a menține alinierea și a rezista presiunilor de injectare.
- Plăci de prindere: Aceste plăci fixează matrița în unitatea de prindere a mașinii de turnare prin injecție. Proiectarea lor trebuie să asigure stabilitatea în timpul fazei de injecție la presiune ridicată pentru a preveni dezalinierea sau mișcarea care ar putea cauza defecte.
- Linia de despărțire: Linia de separație este locul unde se întâlnesc plăcile A și B. O linie de separație bine aliniată este esențială pentru a preveni defecte precum flash-ul (straturi subțiri de plastic la îmbinările matriței) și pentru a asigura eliberarea fără probleme a piesei. Locația liniei de separație depinde adesea de designul piesei și de cerințele matriței.
- Canale de răcire: Canalele de răcire sunt esențiale pentru menținerea performanței matriței și reducerea duratei ciclurilor. Canalele sunt proiectate cu atenție pentru a asigura o răcire uniformă în cavitatea și miezul matriței, ceea ce este esențial pentru prevenirea defectelor precum deformarea sau tensiunile interne. Tipurile de canale de răcire includ:
- Răcire conformă: Canale care urmăresc conturul piesei, asigurând o răcire constantă care se potrivește cu forma cavității matriței.
- Răcire Baffle: Utilizează inserții pentru a ghida fluxul de lichid de răcire și este utilizat în mod obișnuit atunci când dimensiunea matriței limitează amplasarea canalului.
- Bubbler Răcire: Tuburile Bubbler creează o răcire suplimentară în anumite zone, în special pentru secțiunile groase care necesită o răcire mai rapidă.
- Pini de răcire: Pini încorporați în miez asigură răcirea localizată în secțiuni groase, ajutând la gestionarea distribuției temperaturii în matrițe mai mari sau cu mai multe cavități.
Designul de răcire influențează foarte mult durata ciclului și, prin extensie, costul și productivitatea procesului de turnare prin injecție.
Tipuri de matrițe de injecție din plastic
Există mai multe tipuri de matrițe de injecție din plastic pentru a răspunde diferitelor nevoi de producție, complexități și cerințe privind piesele. Iată câteva dintre cele mai frecvent utilizate tipuri:
- Matrițe cu o singură cavitate: Aceste matrițe produc o piesă pe ciclu. Acestea sunt adesea utilizate pentru volume de producție mai mici sau pentru piese de înaltă precizie, unde este necesar un control mai strict asupra fiecărei piese în parte. Matrițele cu o singură cavitate au avantajul unei configurații mai simple și sunt mai rentabile pentru producția limitată.
- Matrițe cu cavități multiple: În matrițele multi-cavitate, mai multe cavități identice permit producerea mai multor piese într-un singur ciclu. Acest lucru crește eficiența și este ideal pentru producția de volum mare, reducând timpul de ciclu pe piesă și costurile globale. Cu toate acestea, proiectarea matrițelor cu cavități multiple este mai complexă și necesită un echilibru precis al sistemului de canal pentru a asigura o umplere uniformă.
- Modele de familie: Matrițele de familie conțin cavități diferite în cadrul unei singure matrițe, permițând producția de diverse componente într-un singur ciclu. Acest lucru este deosebit de util atunci când diferite piese trebuie să fie turnate împreună, cum ar fi în cazul asamblărilor. Cu toate acestea, echilibrarea ratei de umplere pentru piese de dimensiuni diferite poate fi o provocare și poate duce la defecte dacă nu este gestionată cu atenție.
- Matrițe Hot Runner vs. Cold Runner:
- Matrițe Hot Runner: Utilizați componente încălzite pentru a menține plasticul topit în cadrul sistemului de canale, minimizând deșeurile și accelerând ciclul. Conductele fierbinți sunt eficiente pentru producția de volume mari, dar necesită un control atent și costuri inițiale mai ridicate.
- Matrițe de rulare la rece: Permiteți plasticului din canalul de rulare să se răcească și să se solidifice cu fiecare ciclu. Ruloul solidificat este de obicei ejectat împreună cu piesa, care poate necesita o prelucrare secundară pentru a fi îndepărtată. Matrițele cu canal rece sunt mai simple și mai puțin costisitoare, ceea ce le face potrivite pentru producția de volum redus.
- Matrițe cu două plăci vs. matrițe cu trei plăci:
- Matrițe cu două plăci: Acestea constau într-o singură linie de separație și sunt mai simple în proiectare. Acestea sunt utilizate în mod obișnuit pentru piese simple cu cerințe pentru o singură poartă.
- Matrițe cu trei plăci: Includeți o placă suplimentară, creând două linii de separare. Acest lucru permite utilizarea unor sisteme de separare mai complexe, cum ar fi separarea centrală, care îmbunătățește estetica pieselor și poate reduce procesarea ulterioară turnării.
- Matrițe suprapuse și rotative:
- Stack Molds: Matrițele stivuite utilizează mai multe niveluri de cavități, dublând sau triplând efectiv capacitatea de producție fără a crește cerințele de forță de strângere a mașinii. Acestea sunt avantajoase pentru producția de volume foarte mari, dar necesită utilaje și manipulare avansate.
- Matrițe rotative: Matrițele rotative permit supramodelarea și asamblarea în matriță prin rotirea cavităților între stații. Acestea sunt adesea utilizate pentru piese multi-materiale, cum ar fi cele care necesită o combinație de materiale plastice rigide și flexibile.
Fiecare tip de matriță are avantaje și provocări distincte, iar selectarea celei potrivite depinde de factori precum volumul de producție, complexitatea pieselor și cerințele privind materialele.

Procesul de turnare prin injecție a plasticului
Procesul de turnare prin injecție constă în mai multe etape cheie, fiecare fiind esențială pentru producerea de piese de înaltă calitate. Iată o defalcare detaliată:
- Strângere: Matrița este fixată strâns pentru a pregăti injectarea plasticului topit. Forța de strângere este calculată pe baza presiunii din cavitate pentru a se asigura că nu există scurgeri de plastic prin linia de separație.
- Injecție: Plasticul topit este injectat în cavitatea matriței prin canelură, canal și poartă. Viteza de injecție, presiunea și temperatura trebuie controlate cu precizie, deoarece acestea afectează fluxul și calitatea materialului din cavitate.
- Răcire: Răcirea începe imediat ce plasticul intră în matriță. Rata de răcire trebuie să fie uniformă pentru a evita defectele, cum ar fi deformarea sau contracția. Canalele de răcire joacă un rol vital aici, asigurându-se că căldura este disipată eficient din matriță. Această etapă reprezintă adesea cea mai mare parte din durata ciclului.
- Ejecție: Odată ce piesa s-a solidificat, știfturile sau plăcile de ejecție împing piesa afară din matriță. Ejectarea trebuie făcută cu atenție pentru a evita deteriorarea piesei, în special dacă aceasta are caracteristici complexe sau este fabricată din material fragil.
Fiecare etapă a procesului de turnare prin injecție necesită un control precis pentru a produce piese care îndeplinesc standardele de calitate, minimizând în același timp durata ciclului și costurile de producție.
Canale de răcire a matrițelor de injecție
Canalele de răcire sunt esențiale în procesul de turnare prin injecție a plasticului, deoarece influențează semnificativ durata ciclului, calitatea pieselor și eficiența producției. Proiectarea corectă a răcirii este esențială pentru a evita defectele precum deformarea, contracția sau tensiunile interne care pot apărea dacă răcirea este neuniformă sau prea rapidă.
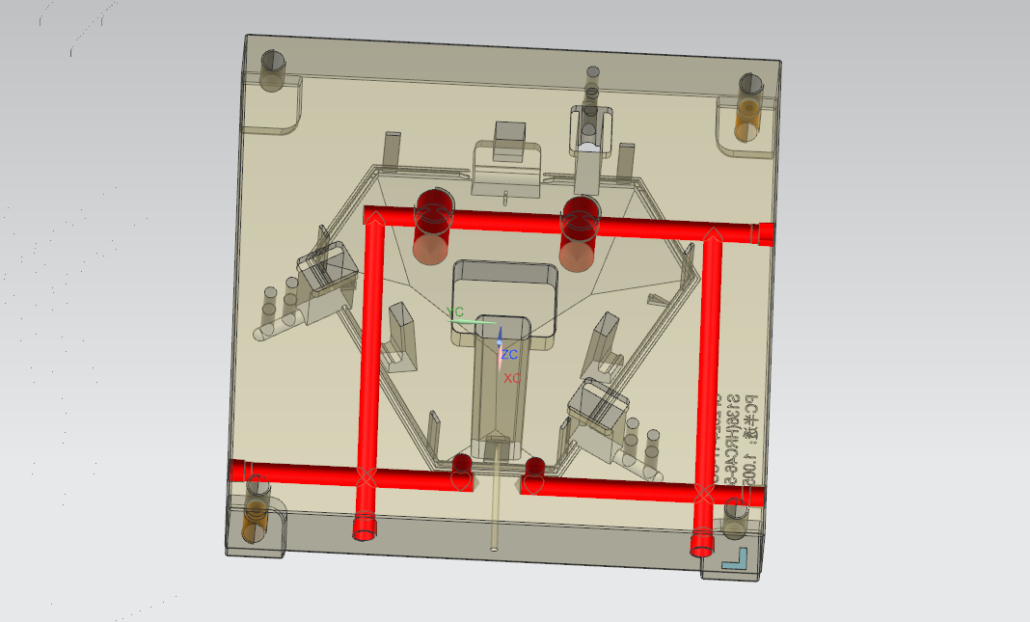
Tipuri de canale de răcire în matrițele de injecție
- Răcire conformă: Această tehnică avansată implică proiectarea unor canale de răcire care urmează conturul piesei în interiorul matriței. Răcirea conformă asigură o răcire uniformă pe întreaga suprafață a piesei, reducând timpul de ciclu și îmbunătățind calitatea piesei. Realizată de obicei prin imprimare 3D și alte metode avansate de fabricație, răcirea conformă este ideală pentru formele complexe în care canalele tradiționale ar fi ineficiente.
- Canale de răcire drepte: Aceste canale sunt căi simple, drepte, forate în plăcile matriței. Deși simple și rentabile, acestea sunt mai puțin eficiente decât răcirea conformă în cazul geometriei complexe a matrițelor. Canalele drepte sunt adesea utilizate în matrițele standard unde răcirea uniformă este mai ușor de realizat.
- Răcire Baffle: Deflectoarele sunt inserții plate care redirecționează fluxul de agent de răcire în interiorul matriței, în special în spații înguste unde canalele drepte nu pot ajunge. Răcirea cu deflectoare este eficientă pentru gestionarea temperaturii în matrițe mai mici sau în zone specifice, dar poate să nu asigure răcirea uniformă necesară pentru modele foarte complexe.
- Bubbler Răcire: Bubblers sunt tuburi care fac să circule lichidul de răcire în zone mici și restrânse ale matriței, deosebit de benefice pentru secțiunile groase ale unei piese care necesită o răcire mai rapidă. Bubblers sunt o alegere obișnuită atunci când canalele tradiționale nu pot asigura o răcire suficientă pentru zonele dense.
- Pini de răcire: Pinii de răcire sunt introduși în miezul matriței pentru a ajuta la răcirea pieselor mai groase. Acești pini sunt ideali pentru răcirea localizată în matrițe mai mari sau în zone specifice predispuse la supraîncălzire. De asemenea, sunt frecvent utilizate în matrițe cu mai multe cavități, unde menținerea unor temperaturi constante este o provocare.
Impactul designului canalelor de răcire asupra timpului de ciclu și calității
Proiectarea canalelor de răcire influențează atât eficiența, cât și calitatea procesului de turnare prin injecție:
- Reducerea timpului de ciclu: Canalele de răcire eficiente ajută la scurtarea timpului de ciclu, deoarece piesele se răcesc și se solidifică mai repede. O durată mai scurtă a ciclului înseamnă un randament de producție mai mare și costuri de fabricație mai mici.
- Precizia dimensională: Răcirea consecventă de-a lungul matriței ajută la prevenirea deformării sau contracției, asigurând menținerea formei și dimensiunilor dorite ale pieselor.
- Finisaj de suprafață: Răcirea poate afecta calitatea suprafeței pieselor turnate. Răcirea uniformă minimizează tensiunile care altfel ar putea afecta suprafața piesei, rezultând un finisaj mai bun.
Proiectarea corectă a canalelor de răcire este un aspect esențial în timpul fazei de proiectare a matriței, deoarece determină eficiența matriței și calitatea pieselor turnate.
Defecte și probleme legate de turnarea prin injecție
În ciuda preciziei turnării prin injecție, pot apărea mai multe defecte comune. Înțelegerea acestor probleme și a modului de atenuare a lor este esențială pentru menținerea calității și minimizarea deșeurilor.
Defecte comune ale turnării prin injecție
- deformare: Deformarea este o deformare care apare atunci când diferite părți ale matriței se răcesc la viteze inegale. Acest defect apare adesea în cazul matrițelor complexe cu canale de răcire inadecvate sau timp de răcire insuficient. Pentru a preveni deformarea, canalele de răcire trebuie proiectate pentru a asigura o răcire uniformă, iar timpul de răcire trebuie monitorizat cu atenție.
- Mărci de chiuvetă: Urmele de scufundare apar ca depresiuni pe suprafața secțiunilor mai groase ale unei piese, de obicei din cauza răcirii necorespunzătoare sau a unei presiuni de fixare inadecvate. Utilizarea unei presiuni optime și asigurarea unei răciri adecvate, în special în zonele groase, pot ajuta la prevenirea semnelor de scufundare.
- Flash: Flash-ul apare atunci când plasticul topit iese din cavitate la linia de separare din cauza presiunii de injecție excesive sau a unei alinieri greșite. Alinierea precisă și reglarea corectă a presiunii sunt esențiale pentru a preveni flash-ul.
- Linii de curgere: Liniile de curgere sunt linii vizibile pe suprafața unei piese cauzate de variațiile ratei de răcire a plasticului în timp ce curge prin matriță. Reglarea vitezei de injecție și a temperaturii poate ajuta la reducerea liniilor de curgere.
- Fotografii scurte: Împușcăturile scurte au loc atunci când cavitatea matriței nu este complet umplută, adesea din cauza presiunii scăzute de injectare sau a materialului insuficient. Creșterea presiunii de injectare sau asigurarea unei alimentări suficiente cu material pot rezolva această problemă.
- Linii de sudură: Liniile de sudură apar acolo unde se întâlnesc două fronturi de curgere, creând adesea puncte slabe în piesă. Ajustarea vitezei de injecție sau utilizarea unui sistem cu canal cald poate reduce liniile de sudură.
- Fragilitate și fisurare: Aceste probleme rezultă de obicei din răcirea necorespunzătoare sau din presiunea de injecție prea mare, care induce tensiuni interne. Proiectarea corectă a răcirii și controlul optim al presiunii ajută la atenuarea fragilității și fisurării.
Prin înțelegerea și controlul acestor factori - cum ar fi viteza de injecție, temperatura și designul de răcire - producătorii pot reduce defectele și îmbunătăți calitatea generală a pieselor turnate.
Procesul de fabricație a matrițelor de injecție
Fabricarea unei matrițe de injecție implică mai multe etape, fiecare esențială pentru asigurarea durabilității, preciziei și funcționalității matriței. Iată o defalcare a etapelor tipice în fabricarea unei matrițe de injecție din plastic:

- Proiectare și inginerie: Faza de proiectare a matriței este crucială, deoarece pune bazele tuturor etapelor ulterioare. Folosind software CAD, inginerii creează un model 3D al matriței, încorporând toate detaliile necesare, inclusiv forma cavității, canalele de răcire, sistemul de ejecție și linia de separare. Acest model este apoi supus unor simulări pentru a prevedea problemele și a optimiza performanța înainte de începerea producției fizice de matrițe.
- Selectarea materialului: În funcție de volumul de producție și de cerințele pieselor, materialele sunt selectate pentru durabilitate și rezistență la uzură. Printre materialele uzuale se numără oțelul călit pentru matrițe de volum mare și aluminiul pentru aplicații de volum mai mic. Matrițele din oțel sunt preferate pentru serii lungi datorită durabilității lor, în timp ce matrițele din aluminiu sunt mai ușor de prelucrat și rentabile pentru producția de serie scurtă.
- Prelucrare CNC și EDM (prelucrare prin descărcare electrică): Prelucrarea CNC (Computer Numerical Control) este utilizată pentru a sculpta forma primară a matriței cu o precizie ridicată. EDM este apoi utilizată pentru a crea geometrii complexe, detalii fine și forme complicate în cavitatea matriței pe care mașinile CNC nu le pot realiza. Combinația de CNC și EDM asigură atât precizia, cât și complexitatea necesară pentru matriță.
- Tratamentul termic și întărirea suprafeței: Matrițele din oțel sunt adesea tratate termic pentru a crește duritatea și durabilitatea. Tratamentele de suprafață, cum ar fi nitrurarea sau cromarea, sunt de asemenea aplicate pentru a spori rezistența la uzură, a reduce coroziunea și a prelungi durata de viață a matriței. Matrițele din aluminiu, deși sunt mai moi, pot fi, de asemenea, anodizate pentru a îmbunătăți duritatea suprafeței.
- Asamblare și lustruire: După prelucrare, componentele matriței sunt asamblate, inclusiv montarea cavității, a miezului, a pinilor de ejecție, a glisierelor și a canalelor de răcire. Se aplică apoi polizarea de precizie pentru a obține un finisaj de suprafață de înaltă calitate, în special pentru piesele care necesită o suprafață estetică sau netedă.
- Testare și validare: Înainte de producția completă, matrița este supusă unui proces de testare pentru a se asigura că îndeplinește specificațiile. Această etapă, cunoscută sub numele de eșantionare T1, testează performanța matriței, identificând eventualele probleme legate de răcire, ejecție sau aliniere. Orice ajustări sunt efectuate pentru a optimiza performanța matriței pentru producția în serie.
- Asigurarea și aprobarea calității: După validare, matrița este inspectată pentru a confirma că îndeplinește toate standardele de calitate. Se fac măsurători pentru a verifica precizia dimensională și se fac ajustări dacă este necesar. Numai după trecerea verificărilor de calitate, matrița este aprobată pentru producția completă.
Fiecare etapă a procesului de fabricare a matrițelor este esențială pentru a se asigura că matrița finală funcționează constant și eficient în medii de producție de volum mare.
Alegerea mucegaiului de injecție potrivit pentru aplicația dvs.
Selectarea matriței de injecție potrivite este esențială pentru optimizarea producției, minimizarea costurilor și asigurarea calității produselor. Iată câțiva factori cheie de care trebuie să țineți cont atunci când alegeți o matriță de injecție:
- Volumul producției: Volumul de producție anticipat joacă un rol semnificativ în selectarea matriței. Producția de volume mari necesită, de obicei, matrițe durabile din oțel călit, în timp ce matrițele din aluminiu sunt potrivite pentru serii scurte sau prototipuri.
- Complexitatea și proiectarea părților: Piesele complexe cu geometrii complicate, decupaje sau pereți subțiri pot necesita caracteristici specializate ale matriței, cum ar fi dispozitive de ridicare, glisiere sau configurații cu mai multe cavități. Cu cât este mai complexă piesa, cu atât mai detaliată trebuie să fie matrița, ceea ce poate afecta atât costul, cât și timpul de producție.
- Alegerea materialului: Diferitele materiale plastice au caracteristici unice de curgere, contracție și răcire. Matrițele concepute pentru materiale rigide precum policarbonatul pot necesita configurații de răcire sau materiale de matriță diferite față de matrițele concepute pentru materiale plastice flexibile precum polietilena.
- Cerințe privind durata ciclului: Timpii de ciclu rapizi sunt esențiali pentru producția de volum mare. O matriță bine proiectată, cu canale de răcire eficiente și un sistem de ejecție optim, poate reduce durata ciclului, crescând producția și reducând costurile.
- Considerații privind costurile: Matrițele sunt o investiție pe termen lung, iar costurile pot varia semnificativ în funcție de material, complexitate și tipul de matriță. În timp ce matrițele multi-cavitate sau cu canal cald pot fi mai scumpe inițial, acestea pot oferi economii pe termen lung prin creșterea eficienței și reducerea deșeurilor.
- Longevitatea mucegaiului: Pentru volumele mari sau producția continuă, matrițele trebuie să fie proiectate pentru longevitate cu materiale și tratamente de suprafață durabile. Caracteristici precum întărirea și acoperirea ajută la asigurarea faptului că matrița rezistă utilizării repetate fără uzură sau degradare.
Prin evaluarea atentă a acestor factori, producătorii pot selecta matrița potrivită pentru a-și atinge obiectivele de producție, a menține calitatea pieselor și a maximiza eficiența costurilor.
Concluzie
Turnare prin injecție de plastic este o piatră de temelie a producției moderne, permițând producția de piese din plastic precise, de înaltă calitate, la un cost redus și la o viteză mare. Înțelegerea diferitelor aspecte ale matrițelor de injecție - de la componente, tipuri și procese de fabricație până la proiectarea răcirii și eventualele probleme - oferă informații valoroase pentru optimizarea producției.
Alegerea matriței potrivite, implementarea unor canale de răcire eficiente și menținerea unui control riguros al calității pot spori considerabil eficiența și calitatea turnării prin injecție a plasticului. Acest lucru nu numai că satisface cerințele producției de volum mare, dar asigură, de asemenea, că piesele turnate îndeplinesc specificațiile și standardele estetice necesare. Datorită progreselor în materie de materiale, proiectare a matrițelor și tehnologii de răcire, turnarea prin injecție a plasticului continuă să evolueze, oferind și mai mult potențial
Lasă un răspuns
Doriți să participați la discuție?Nu ezitați să contribuiți!