I den snabba utvecklingen inom sjukvården är precision, renlighet och efterlevnad mer än bara modeord - det är ett icke förhandlingsbart krav. En av de underliggande tekniker som gör det möjligt att producera säkra, effektiva och skalbara medicintekniska produkter är formsprutning av medicinsk plast. Formsprutning av plast ger form åt sprutor och katetrar, kirurgiska instrument och diagnostiska höljen och är viktigt för att driva modern medicin genom att skapa de ingående delarna.
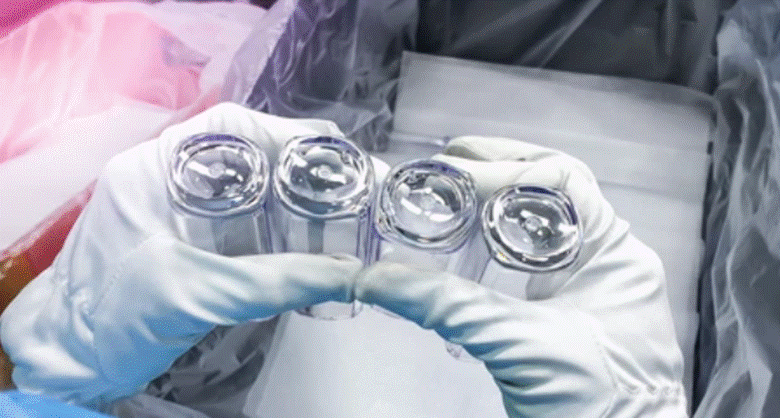
Det är värt att nämna faktorn att välja en pålitlig tillverkare av medicinsk formsprutning. Rätt leverantör garanterar att din produkt uppfyller strikta branschstandarder, fungerar med största precision och förblir ekonomisk i storskaliga produktionskörningar. Ett misslyckande kan få betydande negativa konsekvenser, t.ex. produktåterkallelser, bristande efterlevnad eller hot mot patientsäkerheten.
Denna artikel innehåller en lista över de 10 bästa Formsprutningsföretag för medicinsk plast från olika delar av världen. Kriterierna för de listade bolagen är mycket strikta, med utgångspunkt från certifieringar, innovation, deras globala närvaro och tidigare resultat. Trots att branschens globala karaktär involverar många regioners aktörer har vi begränsat valet till endast två kinesiska företag, varav Sincere Tech är ett av dem, och resten är fördelade i USA, Europa och Israel.
Vad är formsprutning av medicinsk plast?
Det är en nischad tillverkningsprocess som används för att producera mycket exakta och högkvalitativa plaststödda komponenter inom medicin och sjukvård. Det innebär att smält plast sprutas in i en specialbearbetad form och kyls tills den stelnar och får sin slutliga form.
Viktiga egenskaper:
- Precision och renlighet: Medicinsk gjutning måste uppfylla snäva toleranser och tas in i renrumsmiljöer för att undvika kontaminering.
- Biokompatibla material: Använd plast av medicinsk kvalitet, t.ex. polykarbonat, polypropylen och PEEK, som är säkra att använda i eller med människokroppen.
- Efterlevnad av regelverk: Tillverkarna måste följa standarder som ISO 13485, FDA och CE för att kunna garantera säkerhet och effekt.
- Hög volym och repeterbarhet: Perfekt för tillverkning av stora serier av enhetliga, sterila delar, t.ex. sprutor, IV-set, diagnostiska höljen, artroskop, kirurgiska instrument och läkemedelsdispenseringsanordningar.
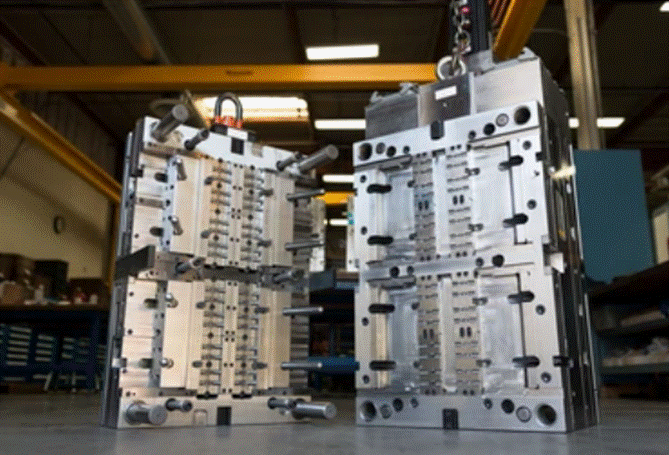
Kriterier för urval
Följande kriterier hjälpte till att avgöra vilket företag som var bäst på formsprutning av medicintekniska produkter,
1. ISO 13485-certifiering och efterlevnad av regelverk
Den internationellt accepterade standarden för kvalitetsledningssystem för den medicintekniska industrin är ISO 13485. Dessutom måste företagen uppfylla FDA- och CE-bestämmelserna när de avser att sälja sina produkter.
2. Avancerad teknik och renrumskapacitet
Företagen måste kunna arbeta i renrumsmiljöer (ISO klass 7 eller bättre) och använda sig av den senaste formsprutningstekniken (mikroformsprutning och flerskottsformsprutning) för att uppfylla kraven på hygien, kontaminering etc.
3. Medicinskt fokus och branschens meritlista
Tillförlitlighet och expertis inom tillverkning av medicinska komponenter har en stark historia. Företag som har varit verksamma inom sjukvårdssektorn under lång tid har också bättre förståelse för regleringar och prestandakrav.
4. Stor kundbas inom hälso- och sjukvården och global räckvidd
Globala företag kommer att ha robusta infrastrukturer för kvalitetskontroll, logistik och reglering för att bättre kunna betjäna multinationella OEM-företag inom medicinteknik.
5. FoU och kapacitet för kundanpassning
De erbjuder inte bara tillverkning, utan även teknisk support, design för tillverkning (DFM) samt innovationspartnerskap för att snabbt och effektivt ta fram nya produkter.
Topp 10 företag inom formsprutning av medicinsk plast.
Dessa är några av de världsledande inom formsprutningsindustrin för medicinsk plast. Dessa tillverkare har valts ut utifrån strikta kriterier, såsom kvalitetscertifieringar, tekniska framsteg, global närvaro och engagemang för innovation, och de är betrodda av de främsta varumärkena för medicintekniska produkter över hela världen. Här är de 10 bästa:
1. Sincere Tech (Kina)
Sincere Tech är en av de ledande kinesiska tillverkarna som är involverade i formsprutning av medicinsk plast för globala kunder. Sincere Tech täcker renrumsgjutning, snabb prototypning och massproduktion och är en pålitlig källa till medicinska delar med hög precision. De är dedikerade till kvalitet genom att följa ISO 13485-standarder, avancerade verktyg och rigorösa valideringsprocesser. Dessutom kan medicinska OEM-företag lägga ut hela processen, inklusive formdesign, tillverkning och till och med montering, vilket gör det till en komplett tjänst med olika företag.
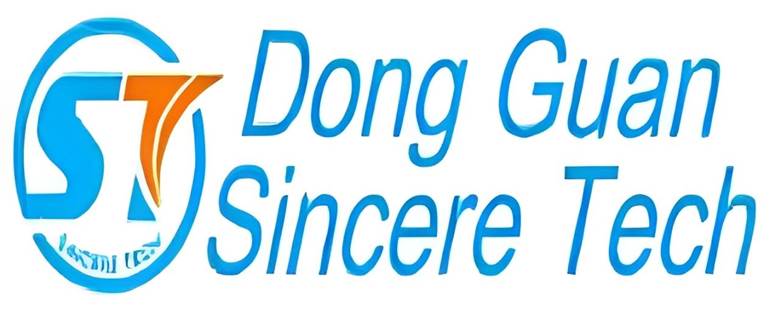
Hemsida: https://www.plasticmold.net/
Företagsprofil:
I över 15 år har Sincere Tech specialiserat sig på både formtillverkning och tillverkning av exakta plastdetaljer i Kina. Tack vare ISO 13485-certifiering och högkvalitativa renrum kan företaget erbjuda viktiga delar till globala OEM-företag inom medicinteknik som kräver snäva toleranser. Företaget står för formkonstruktion, verktygstillverkning och sekundär bearbetning, allt från samma plats. Eftersom de kan hantera produktutveckling från de första stegen till massproduktion är de värdefulla för tillverkning inom sjukvården.
Industrier som betjänas:
Medicintekniska produkter, fordonsindustri, elektronik och förpackningar.
Varför välja Sincere Tech?
- Vår fabrik för precisionsgjutning av medicinsk kvalitet uppfyller den strikta ISO 13485-standarden.
- Erbjuder alla tjänster, från design och prototypframtagning till produktion.
- Möjlighet att gjuta delar i renrum för produkter utan kontaminering.
- Det krävs god kvalitetssäkring och validering.
- Vi erbjuder konkurrenskraftiga priser till både små och stora globala kunder.
2. Phillips-Medisize (USA)
Phillips Medisize är ett Molex-företag och en industrigigant inom integrerad läkemedelstillförsel, diagnostiska enheter och medicinsk elektronik. Medisize är ett fullserviceföretag inom medicinsk formsprutning och har en global närvaro och djup expertis inom komplexa monteringar. De har toppmoderna renrumsanläggningar, som tillhandahåller design- och prototyptjänster samt automatiserade tillverkningstjänster i hög volym om du behöver det. Företaget är en ledande innovatör av lösningar för att koppla samman digital hälsa och av avancerad produktspårning.
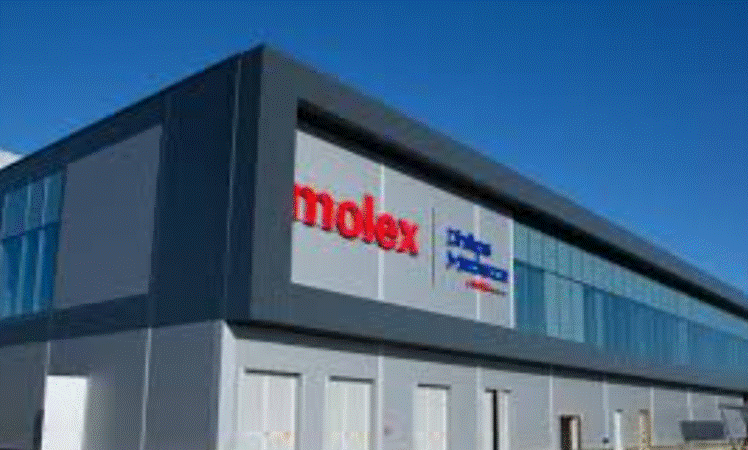
Företagsprofil:
Phillips-Medisize är en division inom Molex och fokuserar på att tillverka utrustning för läkemedelstillförsel, diagnostik och uppkopplad hälsa över hela världen. Företaget har internationell närvaro i USA, Europa och Asien och har renrum från ISO klass 7 till klass 8. De tillhandahåller tjänster i varje steg och tar hand om design, utveckling, testning och full produktion. Bland kunderna finns några av världens ledande läkemedels- och medicintekniska företag.
Industrier som betjänas:
Läkemedelstillförsel, diagnostik och medicinsk elektronik.
Varför välja Phillips-Medisize?
- Internationell verksamhet som förbättras genom automatisering och bibehålls i renrumsmiljöer.
- Kunskap om uppkopplad hälsa och användning av digital teknik.
- En historia av framgångsrikt samarbete med ledande MedTech-företag.
- Alla våra verksamheter över hela världen uppfyller ISO 13485 och FDA-standarder.
- Erfarenhet av att hantera behoven hos stora tillverkningsprojekt.
3. Tessy Plastics (USA)
Tessy Plastics har levererat formsprutning av plast med hög precision till den medicinska sektorn i årtionden och är känt för sin ISO 13485-certifiering. De har alla produkter in-house, från verktyg till allt från automation till validering. De är helt beroende av det medicinska området och producerar ett brett utbud av kirurgiska, diagnostiska och bärbara medicintekniska produkter som arbetar nära kunder och partners för att garantera högre tillförlitlighet, enkel skalbarhet och efterlevnad av globala regler. De har också kapacitet att mikroforma och insättningsforma för känsliga komponenter.
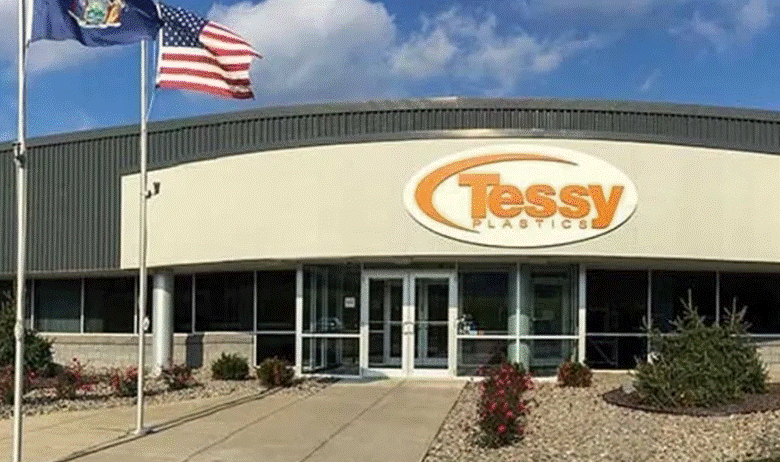
Företagsprofil:
Sedan 1976 har Tessy Plastics varit verksamt i New York, USA, som ett familjeföretag inom formsprutning med hög precision. Den medicinska sidan av Bosch betonar kirurgiska, diagnostiska och bärbara enheter, som alla tillverkas enligt höga kvalitetsstandarder. Tessy kombinerar automation, avancerade verktyg och monteringsprocesser i sitt arbete. Företagets ingenjörer samarbetar med kunderna för att lösa problem med design, regler och snabb lansering.
Industrier som betjänas:
Medicinteknik, elektronik och konsumentvaror.
Varför välja Tessy?
- Alla steg från design till försäljning ligger under en och samma myndighet.
- Har mikroformning och insatsformning som sina främsta styrkor.
- Över 40 års erfarenhet av tillverkning av medicintekniska produkter.
- Företaget har ISO klass 7-områden med renrum.
- Företaget är ISO 13485-certifierat och har som mål att uppfylla alla krav för medicintekniska produkter.
4. Gerresheimer (Tyskland)
Gerresheimer är en global ledare inom förpackningar för medicin och läkemedel med en viktig division för formsprutning av plast som kan tillverka system för läkemedelstillförsel, formsprutade diagnostiska enheter och förfyllda sprutor. Företaget har flera renrumsanläggningar och arbetar enligt de högsta regulatoriska standarderna. På grund av sin vertikala integration av produktdesign till mögeltillverkning och slutligen till slutmontering är de den föredragna partnern för läkemedelsföretag över hela världen.
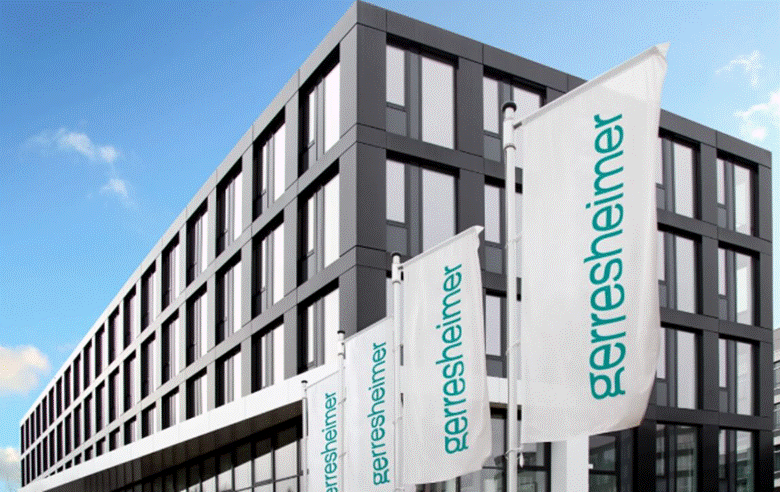
Företagsprofil:
Förpackningsföretag inom medicin och läkemedel känner väl till Gerresheimer och dess långa erfarenhet av formsprutning. Företagets globala verksamhet omfattar mer än 30 anläggningar och ger kunderna produkter som sträcker sig från insulinpennor till inhalatorer och diagnostiska kit. Företaget är starkt eftersom det täcker hela tjänsteutbudet, från design till skapande av den slutliga förpackningen. Tack vare sin avancerade infrastruktur kan de producera stora medicintekniska produkter som uppfyller många regler.
Industrier som betjänas:
Läkemedel, hälsovård och diagnostik.
Varför välja Gerresheimer?
- Tillverkningslösningar som omfattar ett helt system.
- Det finns renrumscertifierade anläggningar på olika platser i världen.
- Nya utvecklingar inom både förpackningar och enheter.
- Många ledande läkemedelsorganisationer förlitar sig på oss.
- Följa alla EU:s och USA:s medicinska föreskrifter.
5. Nypro Healthcare (Jabil - USA)
Nypro Healthcare är en del av Jabil och levererar lösningar för formsprutning av medicinteknisk plast i stora volymer för marknader med hög komplexitet och stark reglering. Med sin automationsförmåga och sitt tekniska stöd har Nypro tillverkningsanläggningar över hela världen. De koncentrerar sig på sofistikerade medicinska applikationer som injicerbar läkemedelstillförsel, diagnostiska system och minimalt invasiva kirurgiska verktyg. Nypro arbetar med kunderna enligt en partnerskapsmodell och ser till att tillhandahålla FoU, prototyptillverkning och tillverkning.
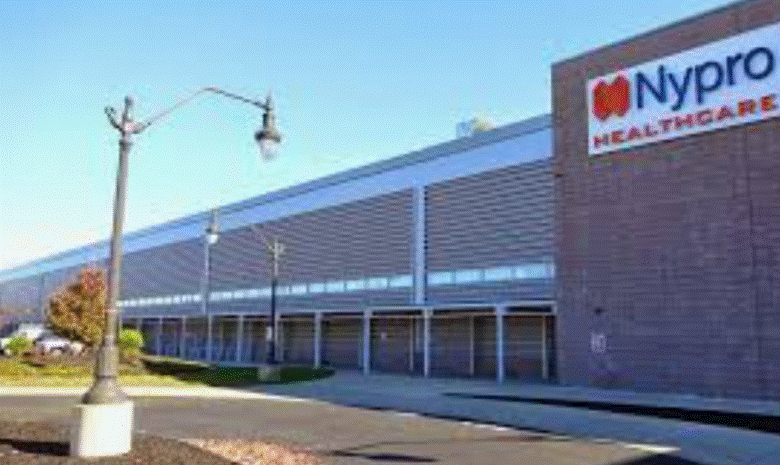
Företagsprofil:
Nypro, som ingår i Jabil Healthcare, erbjuder kompletta CDMO-tjänster och formsprutning för medicintekniska produkter. I fem världsregioner erbjuder Nypro högvolymproduktion för kirurgiska och diagnostiska områden samt för läkemedelstillförsel. Tack vare sin skicklighet när det gäller automatisering, att uppfylla regler och att göra saker mindre kan kunderna slå ut konkurrenterna. De arbetar också med teknik i början, väljer ut viktiga material och bygger prototyper.
Industrier som betjänas:
System för läkemedelstillförsel, diagnostik och kirurgi.
Varför välja Nypro?
- Produktionsanläggningar i flera länder med möjlighet att utöka produktionen.
- Ha detaljerad kunskap om reglerna på reglerade marknader.
- Bättre automatisering och montering ger biltillverkarna fördelar.
- Tidigt samarbete mellan FoU och tidig design.
- Ledande leverantör inom tillverkning av medicintekniska produkter med hög risk.
6. Röchling Medical (Tyskland)
Röchling Medical, en del av Röchlingkoncernen, erbjuder kompletta formsprutningslösningar för kunder inom läkemedels-, diagnostik- och medicinteknisk industri. De är globalt tillgängliga i Europa, USA och Kina. Röchlings kompetens omfattar teknik och regelefterlevnad samt gjutning i renrum. Deras portfölj omfattar allt från lab-on-chip-komponenter till anpassade höljen för kirurgiska enheter, ofta tillverkade i fullt validerade klass 7-miljöer.
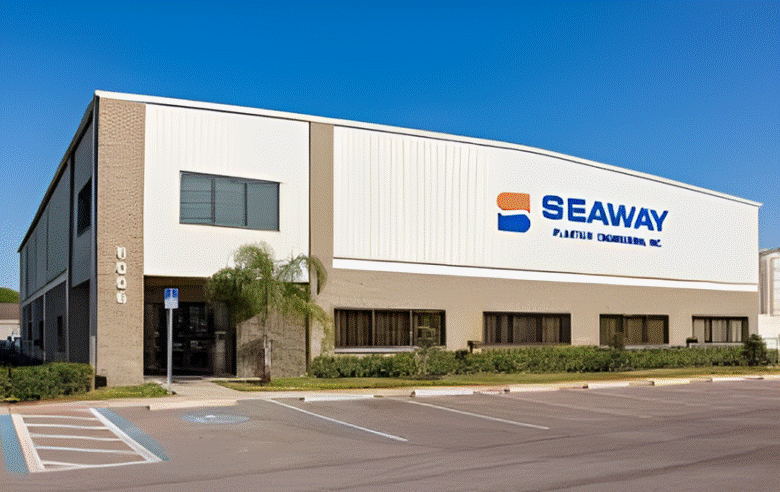
Företagsprofil:
Röchling Medical ingår i Röchlingkoncernen och hjälper läkemedels-, diagnostik- och medicintekniska industrier runt om i världen. Renrumsgjutning, lab-on-chip och enhetshus är områden som de specialiserar sig på med tillverkning i Tyskland, USA och Kina. Röchling har teknisk assistans, regulatoriska funktioner och fullt stöd för produkthantering från början till slut. Tillverkningssystemen vid dessa anläggningar stöder både begränsade och stora produktionsserier.
Industrier som betjänas:
Diagnostik, läkemedel och kirurgiska instrument.
Varför välja?
- Bolagen är verksamma i flera länder i Europa, Kina och USA.
- Breda tjänster för tillverkning i renrum finns tillgängliga.
- Har arbetat i klass 7- och klass 8-gjutningsmiljöer.
- Levererar teknisk hjälp för följande föreskrifter.
- Vi har kompetens att utveckla specialanpassade komponenter för medicinskt bruk.
7. Seaway Plastics Engineering (USA)
Seaway Plastics, som specialiserar sig på låg- till medelvolymproduktion, är en trovärdig partner för medicinska OEM-företag som kräver snabba leveranser och flexibelt stöd. Deras tjänster omfattar formsprutning i renrum, egna verktyg och monteringstjänster. Seaway är särskilt känt inom segmentet för ortopediska och kirurgiska produkter. Företaget tillhandahåller också protokoll för IQ/OQ/PQ-validering, vilket gör det tydligt att deras produkter är mycket reglerade.
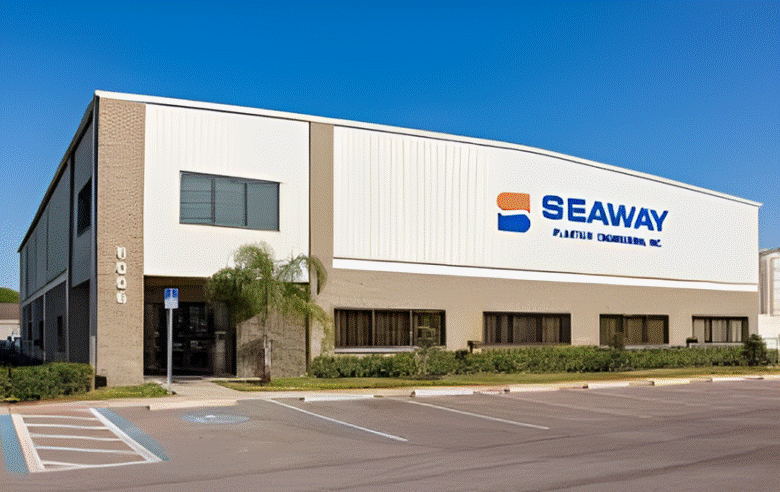
Företagsprofil:
Seaway Plastics erbjuder främst formsprutning av små och medelstora volymer till medicintekniska företag. Anläggningarna i renrum enligt ISO klass 7 möjliggör såväl formtillverkning som validering och montering av slutprodukter. Seaway gör sig främst gällande inom ortopediska och kirurgiska instrument. På grund av de snabba produktionstiderna vänder sig många till dessa företag för både prov- och småskaliga projekt.
Industrier som betjänas:
Ortopedi, kirurgiska verktyg och diagnostik.
Varför välja?
- Snabb prototyptillverkning och låga antal prover erbjuds.
- Vi erbjuder utveckling och support av våra egna test- och automatiseringsverktyg.
- Du kan lita på att våra anläggningar är certifierade enligt både ISO 13485 och reglerade av FDA.
- Specialgjutning för känsliga komponenter är möjlig i renrum.
- Erbjuder fullständig flexibilitet för kunden.
8. MedPlast (nu Viant - USA)
Detta företag är nu känt som Viant och är ett kraftpaket inom tillverkning av medicintekniska produkter. De utför kontraktstillverkning, inklusive formsprutning av plast, extrudering, montering, förpackning och sterilisering. Deras kompetens inom formsprutning sträcker sig längre än till implanterbara enheter, diagnostiska kit och system för läkemedelstillförsel. Viants betoning på design för tillverkningsbarhet (DFM) och intensiv kvalitetskontroll gör dem till en idealisk leverantör för medicinska applikationer med hög risk.
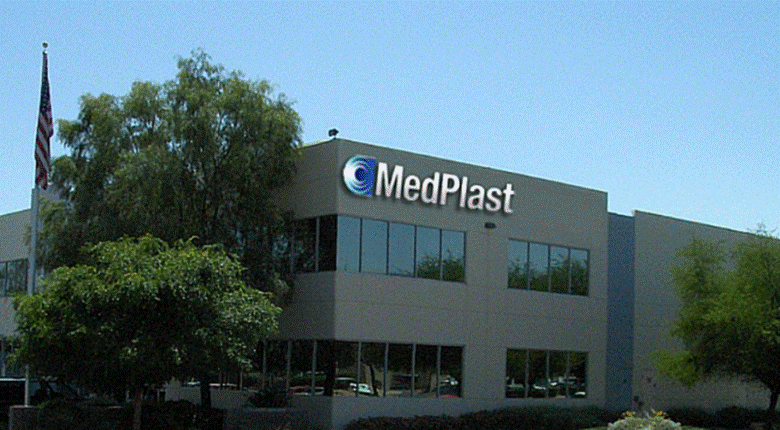
Företagsprofil:
Företaget drivs under varumärket Viant och erbjuder en rad olika tillverkningsprocesser för medicintekniska produkter, till exempel formsprutning och sterilisering. Verksamheten sträcker sig till marknader för ortopedi, diagnostik och engångsprodukter. Tack vare Viants DFM-kompetens och interna regulatoriska resurser skapas lösningar som är både säkra och skalbara. Det finns mer än 25 Vifor Pharma-anläggningar runt om i världen där de tillämpar sin regulatoriska know-how.
Industrier som betjänas:
Implanterbara enheter, diagnostik och kirurgiska system.
Varför välja?
- Erbjuder tjänster för design för tillverkning, gjutning och sterilisering.
- Dokumenterad erfarenhet av att ge vård för medicinska problem som är svåra att behandla.
- Designad för världen, producerad för världen.
- Du kan ändra din beställning efter behov och alla produkter är kvalitetskontrollerade.
- Alla våra anläggningar är ISO 13485- och FDA-certifierade.
9. Technoplast (Israel)
Technoplast är en framväxande aktör inom medicinsk plastgjutning med hög precision, baserad i Israel. Bland de produkter som erbjuds finns produktdesign, snabb prototypframtagning och massproduktion med stort fokus på kundanpassade medicinska komponenter. Bland kunderna finns multinationella tillverkare av medicintekniska produkter, och företaget är känt för sin snabba marknadsintroduktion eftersom verksamheten är mycket flexibel och har en stark FoU-avdelning. Technoplast är exceptionellt starkt (kardiologi, diagnostik, engångsartiklar).
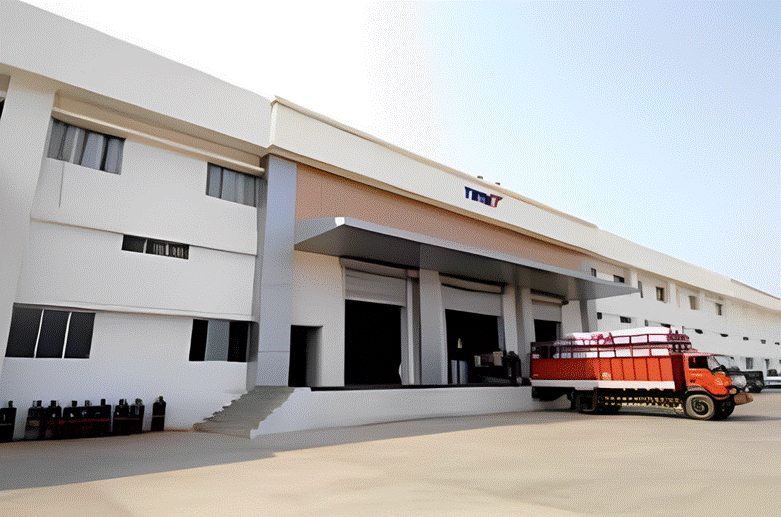
Företagsprofil:
Technoplast är ett israeliskt företag som levererar avancerad plastgjutning för användning i medicintekniska produkter. Företagen erbjuder hjälp med att designa produkter, prototyper, tillverka formar och producera artiklar i stor skala. Technoplast är känt för att vara flexibelt, bedriva effektiv forskning och utveckling samt ha erfarenhet av att tillverka produkter för kardiologi, diagnostik och engångsartiklar. Snabba leveranser och låga tillverkningskostnader är högsta prioritet för företaget.
Industrier som betjänas:
Kardiologi, diagnostik och engångsartiklar.
Varför välja Technoplast?
- Förbättrad produktion genom agila åtgärder och snabb prototypframtagning.
- Formtillverkning med hög precision för detaljerade medicinska delar.
- Innovativ forskning och utveckling för medicinskt bruk.
- Höga priser för att få ut produkter på marknaden.
- ISO 13485-certifiering kombineras med CE- och FDA-kompatibla produkter.
10. TK Mold (Kina)
TK Mold, som är det andra och sista kinesiska företaget på denna lista, är känt för sina verktygs- och formsprutningstjänster med hög precision. De arbetar med formar och komponenter av medicinsk kvalitet och exporterar produkter till Nordamerika, Europa och andra asiatiska marknader. Deras styrkor är teknisk design och deras förmåga att förverkliga dessa idéer genom både tillverkning av formar och produktion av små till medelstora volymer. TK Mold har ett certifierat ISO-dokument och följer internationella medicinska standarder. Därför är de ett bra företag att lägga ut produktionsarbete på.
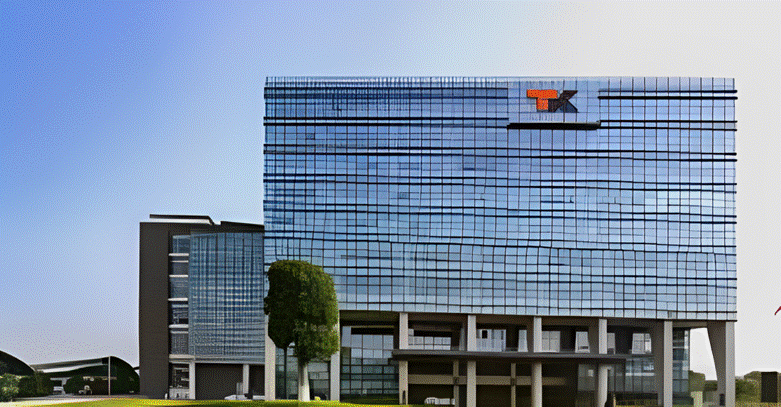
Företagets profil
TK Mold är välkänt i Kina för sina högkvalitativa formsprutningsverktyg och delar till medicintekniska produkter. Deras kunder i Nordamerika, Europa och Asien får renrumsgjutning för klass 7-applikationer. Gjutformen stöds hela vägen från sin ursprungliga design genom tillverkning av medelstora partier och efterproduktionssteg. Eftersom de är ISO 13485-certifierade och uppfyller internationella standarder har de förtjänat förtroende som en offshore-partner.
Industrier som betjänas
Medicinteknik, elektronik och fordonsindustri.
Varför välja?
- Endast ett litet antal professionellt utformade formar används för produktion.
- Särskild uppmärksamhet ägnas åt innovation inom teknik.
- ISO-certifierade och i enlighet med medicinska riktlinjer.
- Tillhandahålla expertis till EU, USA och Asien.
- Prisvärda metoder för att arbeta med OEM-tillverkare.
Framtidsutsikter för företag som tillverkar formsprutningsverktyg för medicinsk plast.
Med utvecklingen av sjukvårdsindustrin förväntas medicinska formsprutningsföretag utvecklas i flera viktiga aspekter. Här är vad framtiden har att erbjuda:
1. Antagande av smarta material
- Företagen investerar i material som antimikrobiella, biologiskt nedbrytbara eller bioresorberbara polymerer som ger förbättrad funktionalitet.
- Dessa tillbehör gör det möjligt att använda säkrare och mer hållbara medicintekniska produkter för engångsbruk.
2. Expansion inom mikrofluidik och miniatyrisering
- Allt fler bearbetningsföretag tvingas skapa ultrasmå och invecklade delar för lab-on-a-chip, bärbara sensorer och diagnosutrustning.
- Förmågan att gjuta i mikroformat kommer att behövas för att behålla konkurrenskraften.
3. Automation & Industri 4.0-integration
- Avancerad automatisering och dataanalys i realtid kommer dock att göra det möjligt för företagen att uppgradera sin processeffektivitet, spårbarhet och kvalitetskontroll.
- De smarta fabrikerna med uppkopplade system kommer att minimera mänskliga fel och produktiviteten kommer att öka.
4. Anpassning och tillverkning på begäran
- Det finns en ökande efterfrågan på personligt anpassade medicintekniska produkter, så företagen använder sig av en flexibel serieproduktion.
- Snabb prototypframtagning och additiv tillverkning kan förbättra de traditionella gjutningsprocesserna.
5. Hållbarhet och efterlevnad av miljölagstiftningen
- Världsdekret tvingar företag att återvinna, minska avfallet och energiförbrukningen samt minska användningen av plast som inte kan återvinnas.
- Tillverkarna tar till sig de gröna initiativen och metoderna i den cirkulära ekonomin.
6. Ökad granskning av tillsynsmyndigheter
- I och med tillkomsten av nya och innovativa material och tekniker kan företagen förvänta sig mer rigorösa protokoll för validering, spårbarhet och efterlevnad.
- Det kommer att finnas ett behov av att investera i expertis inom byråkrati för att få fortsatt marknadstillträde.
7. Strategiska partnerskap med MedTech-företag
- Företagen etablerar tätare samarbeten med OEM-företag inom medicinteknik för att tillsammans ta fram innovativa IP-känsliga lösningar.
- Det kommer att bli en konkurrensfördel att involvera design i ett tidigt skede.
Slutsats
Det är viktigt att välja den bästa tillverkaren av formsprutning av medicinsk plast för att säkerställa att din medicinska enhet är framgångsrik när det gäller säkerhet, skalad produktion och all efterlevnad. Denna lista är världens elitföretag, inte bara när det gäller att följa de tekniska och lagstadgade kraven inom den medicinska industrin, utan de ger också innovativa och kundorienterade lösningar.
Från världens giganter, som Phillips-Medisize och Gerresheimer, till nischföretag som Sincere Tech och Technoplast, har var och en av dem viss beprövad expertis och kapacitet inom sjukvårdsområdet. Oavsett om du utvecklar ett nytt diagnostiskt verktyg eller utökar produktionen av en etablerad maskin, samarbetar du med någon av dessa pålitliga leverantörer av medicinsk formsprutning och sätter dig i framkant av kvalitetsspecifikationer och konkurrenskraftiga lopp.
Välrenommerade leverantörer av medicinsk formsprutning garanterar att de håller sig framme när det gäller kvalitetsriktmärken och konkurrens på marknaden.
Vanliga frågor
1. Vad är den medicinska plastinsprutningsgjutningen?
Det är en tillverkningsprocess som tillverkar plastdetaljer med hög precision för medicinska tillämpningar i miljöer med specialutrustning och material enligt höga regleringsstandarder.
2. Varför är ISO 13485-certifiering viktig för företag inom medicinsk gjutning?
Det säkerställer att företaget uppfyller internationellt accepterade standarder för kvalitetsledningssystem inom den medicintekniska industrin, vilket är nyckeln till regelefterlevnad och produktsäkerhet.
3. Vilka material används vanligtvis vid formsprutning av medicintekniska produkter?
De vanligaste materialen är polykarbonat av medicinsk kvalitet, polypropen, polyeten och termoplastiska elastomerer som måste vara biokompatibla och steriliserbara.
4. Vad är effekten av renrum vid medicinsk formsprutning?
Renrum är en miljö som kan vara fri från föroreningar, vilket är viktigt vid produktion av sterila/känsliga medicinska komponenter genom att minimera risken för partikelkontaminering.
5. Är det möjligt för små företag att matcha den produktion som stora tillverkare producerar här?
Ja, det gör vi. Många små företag tillhandahåller nischad expertis, agil utveckling och snabba prototyptjänster som verkligen är bra partners för specialisering eller anpassat arbete.