Polyetheretherketone (PEEK) is a high-performance thermoplastic renowned for its exceptional mechanical, thermal, and chemical properties. As one of the most versatile materials in engineering, PEEK plastic material is extensively used in industries such as aerospace, medical, automotive, and electronics. This article explores the key properties of PEEK, its molding processes, and guidelines for achieving optimal results in PEEK injection molding.
What is PEEK Plastic Material?
PEEK (Polyetheretherketone) is a semi-crystalline thermoplastic belonging to the polyaryletherketone (PAEK) family. Its unique combination of properties makes it ideal for applications requiring strength, heat resistance, and chemical stability.
Key Features of PEEK Plastic
- High Temperature Resistance: With a melting point of approximately 343°C and a continuous use temperature of 260°C, PEEK excels in high-temperature environments.
- Mechanical Strength: PEEK exhibits remarkable tensile strength, with values exceeding 90 MPa in unfilled grades, and even higher when reinforced.
- Chemical Resistance: PEEK resists a wide range of chemicals, including acids, alkalis, and organic solvents, making it suitable for harsh chemical environments.
- Wear and Friction: Its low coefficient of friction and wear resistance are ideal for applications such as bushings and bearings.
- Biocompatibility: FDA-approved grades of PEEK make it a preferred material for medical implants and prosthetics.
PEEK is available in several grades, including:
- Unfilled PEEK: General-purpose grade with high purity.
- Glass-Filled PEEK: Enhanced stiffness and strength for structural applications.
- Carbon-Filled PEEK: Excellent for applications requiring superior wear resistance and thermal conductivity.
Can PEEK Be Injection Molded?
Yes, PEEK can be injection molded, but its high processing temperatures and material characteristics require specialized equipment and expertise. Injection molded PEEK parts are valued for their precision, consistency, and ability to meet tight tolerances.
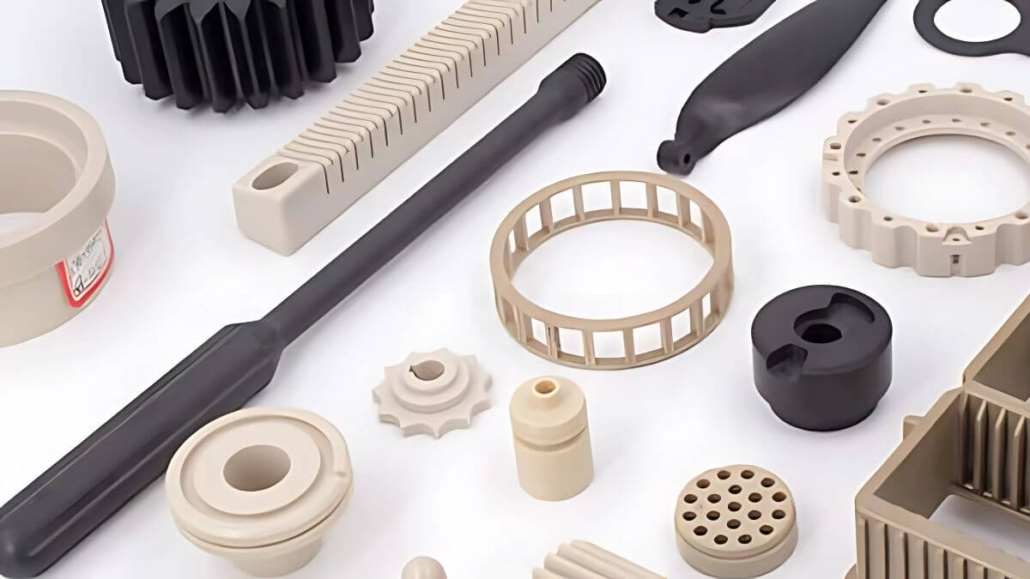
Why Use Injection Molding for PEEK?
- Scalability: Injection molding enables the efficient production of high volumes of parts.
- Design Complexity: Allows for intricate geometries that are challenging to achieve through machining.
- Material Optimization: Waste is minimized, and properties are tailored through reinforcement or fillers.
Challenges in PEEK Injection Molding
- High Processing Temperature: PEEK’s melt temperature requires molds and machines capable of withstanding extreme heat.
- Shrinkage: With a shrinkage rate of 1.2–2.5%, mold designs must account for dimensional stability.
- Material Cost: PEEK is more expensive than standard thermoplastics, making precision critical to reduce waste.
PEEK Plastic Properties: Why It Stands Out
Understanding the properties of PEEK plastic is crucial to optimizing its use in injection molding and other applications.
1. Thermal Properties
- Melting Point: ~343°C
- Glass Transition Temperature (Tg): ~143°C
- Continuous Use Temperature: Up to 260°C
PEEK maintains its mechanical properties even at high temperatures, making it suitable for environments such as engine compartments and industrial machinery.
2. Mechanical Properties
- Tensile Strength: 90–100 MPa (unfilled), up to 170 MPa (reinforced)
- Flexural Strength: PEEK provides exceptional resistance to bending forces, critical for structural components.
- Impact Resistance: Despite its rigidity, PEEK absorbs energy effectively, preventing sudden failures.
3. Chemical Resistance
PEEK is virtually inert to most chemicals, including:
- Hydrocarbons
- Strong acids and bases
- Halogens and solvents
Its chemical stability makes it ideal for piping, valves, and chemical processing equipment.
4. Electrical Properties
- Dielectric Strength: 20–25 kV/mm
- Low Dielectric Constant: PEEK is an excellent insulator, used in connectors and cable insulation.
PEEK Injection Molding Guide
Injection molding PEEK requires meticulous attention to detail. Here’s a step-by-step guide to mastering PEEK plastic injection molding.
1. Pre-Processing: Material Preparation
PEEK pellets must be dried thoroughly to prevent moisture-related defects. Use a desiccant dryer set to 150°C for 3–4 hours, reducing moisture content below 0.02%.
2. Machine Requirements
A specialized injection molding machine is essential for handling PEEK’s high melt temperature. Key features include:
- Barrel Temperature Capability: Up to 400°C
- Screw Design: Wear-resistant, with low shear to avoid material degradation.
- Mold Temperature Control: Maintain mold temperatures between 160°C and 200°C.
3. Injection Molding Temperature Settings
- Melt Temperature: 360°C–400°C
- Mold Temperature: 160°C–200°C
- Injection Pressure: 80–120 MPa
These parameters vary based on the part’s geometry, wall thickness, and the grade of PEEK used.
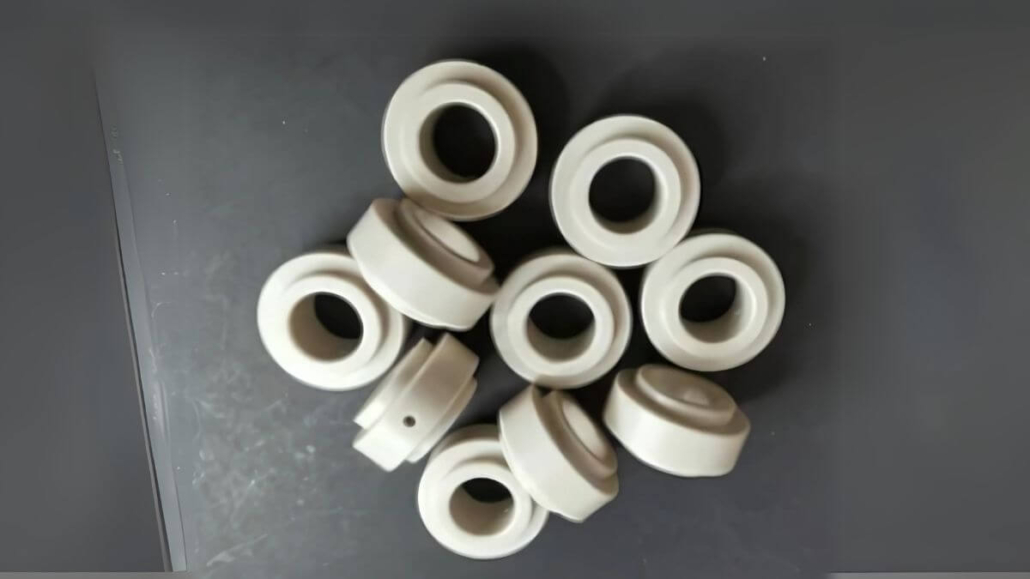
4. Cooling and Ejection
Cooling PEEK requires precision to prevent warping and ensure dimensional stability. Cooling time depends on the part’s complexity and wall thickness but is typically longer than standard thermoplastics.
Ejector pins and draft angles must be incorporated into the mold design to facilitate smooth ejection without damaging the part.
Applications of Injection Molded PEEK
Injection molded PEEK parts are indispensable in industries where performance under extreme conditions is critical. Key applications include:
1. Aerospace and Defense
- Aircraft components: Fasteners, brackets, and bushings
- Engine parts: High-temperature-resistant seals and housings
2. Medical Devices
- Surgical instruments: Handles, guides, and implants
- Prosthetics: Lightweight and biocompatible components
3. Automotive
- Transmission components
- Under-hood applications such as sensors and insulators
4. Electronics
- High-performance connectors and insulators
- Microchip sockets and encapsulation
Tips for Successful PEEK Plastic Molding
Achieving consistent quality with PEEK plastic molding requires expertise and strict adherence to best practices. Here are some tips:
1. Optimize Mold Design
- Use uniform wall thickness to prevent warping.
- Include conformal cooling channels to ensure even temperature distribution.
- Design molds with sufficient draft angles (at least 2–3°) for smooth part ejection.
2. Monitor Processing Parameters
- Regularly calibrate temperature and pressure settings to prevent degradation.
- Avoid prolonged residence times in the barrel, as PEEK can degrade under heat.
3. Prevent Common Defects
- Voids: Caused by trapped air; use proper venting and higher packing pressure.
- Flash: Ensure tight mold alignment and control injection pressure.
- Warpage: Minimize cooling imbalances with well-designed molds.
Advanced Techniques in PEEK Injection Molding
Injection molding PEEK can be elevated using advanced techniques that enhance productivity, reduce defects, and expand design possibilities. Here are some cutting-edge methods:
1. Overmolding
PEEK can be overmolded onto other materials to create multi-functional components. For example:
- Metal Overmolding: Provides mechanical reinforcement while maintaining a lightweight structure.
- Other Thermoplastics: Combines the mechanical strength of PEEK with the flexibility of softer plastics like TPU (Thermoplastic Polyurethane).
Overmolding requires precise control of melt and mold temperatures to ensure adhesion between materials.
2. Insert Molding
Incorporating metal inserts during the molding process adds functionality and strength to PEEK parts. Applications include threaded fasteners or conductive inserts in electronic housings.
3. Gas-Assisted Injection Molding
For thicker PEEK parts, gas-assisted injection molding helps reduce material usage and eliminates sink marks. The process injects gas into the molten PEEK, hollowing out specific sections to create lightweight yet durable components.
Sustainability in PEEK Plastic Molding
As industries strive for sustainability, PEEK injection molding offers opportunities to reduce environmental impact:
1. Recycling PEEK
Although PEEK’s high-performance nature makes it costlier than other thermoplastics, its recyclability offsets material expenses:
- Post-Industrial Regrind: Scrap material from production can be reprocessed into usable pellets without significant degradation.
- End-of-Life Reuse: Used PEEK components can be recycled, particularly in less critical applications like non-load-bearing structures.
2. Energy Efficiency
PEEK requires high processing temperatures, but modern machines with advanced heating and cooling systems help reduce energy consumption:
- Hybrid and electric molding machines optimize energy use.
- Conformal cooling channels lower cooling times, reducing overall cycle duration.
3. Long-Lasting Applications
PEEK’s durability ensures a longer lifecycle for components, minimizing the need for replacements. This reduces waste in industries like aerospace and medical, where PEEK components are critical for safety and performance.
Finding the Right PEEK Injection Molding Supplier
- Selecting a reliable supplier for PEEK injection molding products is critical for ensuring quality and meeting production requirements. Key considerations include:
- 1. Technical Expertise
- Choose suppliers with experience in handling high-performance plastics like PEEK. They should have the capability to process reinforced grades and meet tight tolerances.
- 2. Advanced Equipment
- Ensure the supplier uses state-of-the-art machinery capable of maintaining precise temperature and pressure controls.
- 3. Quality Assurance
- A trustworthy supplier will have robust quality control processes, including material testing, process validation, and finished part inspections.
- 4. Customization and Scalability
- Look for suppliers that offer customized solutions, from prototype development to mass production.
Examples of Injection Molded PEEK Applications
1. Medical Field
PEEK’s biocompatibility and sterilization capabilities make it a leading material for medical applications:
- Orthopedic Implants: Spinal cages, hip joints, and bone plates.
- Dental Components: Frameworks for prosthetics and implants.
- Surgical Instruments: Handles and guides designed for repeated sterilization.
2. Automotive
PEEK’s lightweight and high-strength properties are used in:
- Powertrain Components: Gears, seals, and housings exposed to high heat.
- Fuel Systems: Valves and connectors that resist aggressive fuels and chemicals.
3. Aerospace
Injection molded PEEK parts reduce weight while maintaining structural integrity:
- Brackets and Clips: Used in aircraft interiors to meet stringent fire and smoke regulations.
- Cable Insulators: Excellent electrical properties and temperature resistance.
4. Electronics
PEEK’s dielectric strength ensures reliability in:
- Connector Housings: Protect delicate electronics from heat and chemicals.
- Microchips and Insulation: Thermal stability ensures performance in compact, high-temperature environments.
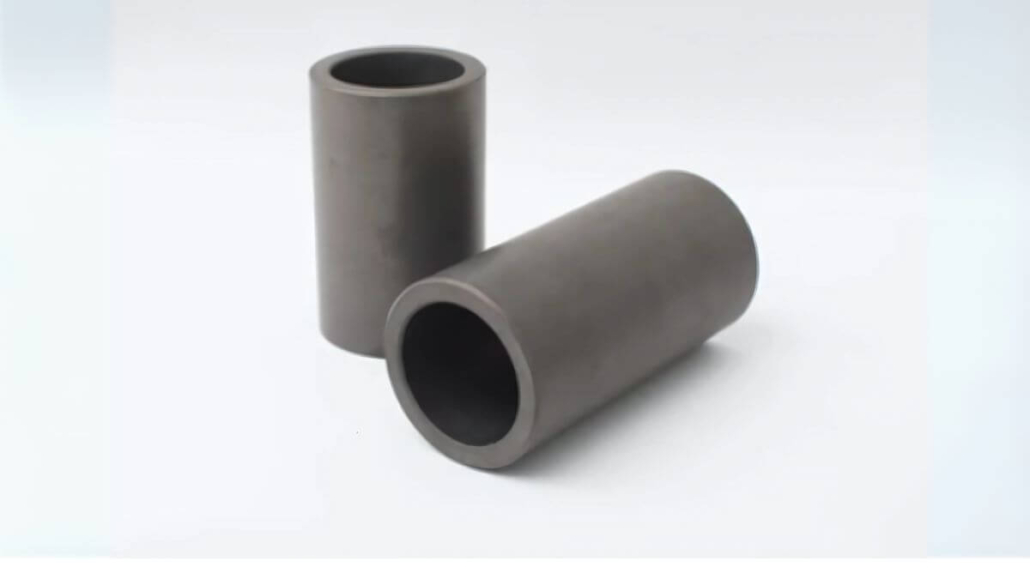
PEEK Plastic Molding: Best Practices for Optimal Results
1. Choose the Right Grade
Different PEEK grades cater to specific needs:
- Unfilled PEEK: General-purpose applications.
- Glass-Filled PEEK: Ideal for parts requiring enhanced stiffness and low thermal expansion.
- Carbon-Filled PEEK: Best for high-load, wear-resistant applications.
2. Optimize Mold Design
PEEK molding benefits from well-thought-out mold designs:
- Use venting to release trapped gases and prevent burn marks.
- Incorporate high-performance coatings on mold surfaces to reduce material adhesion.
3. Validate Process Parameters
Using scientific molding techniques ensures consistency:
- Conduct Design of Experiments (DOE) to optimize processing conditions.
- Monitor melt flow rate (MFR) to detect potential degradation during long production runs.
4. Collaborate with Experts
For complex parts, consult injection molding specialists familiar with PEEK’s unique behavior.
Future of PEEK in Injection Molding
With advancements in material science and processing technology, PEEK’s potential is expanding:
- 3D Printing Integration: Combining injection molding with additive manufacturing enables rapid prototyping and complex designs.
- Hybrid Materials: New PEEK composites are emerging, offering tailored properties for specific industries.
- Sustainability Initiatives: Increased focus on recycled and bio-based PEEK variants.
As demand for high-performance materials grows, PEEK will continue to shape industries requiring unmatched reliability and durability.
Questions About PEEK Plastic Material
1. Can PEEK Be Injection Molded?
Yes, PEEK is ideal for injection molding, but it requires specialized equipment and expertise due to its high melting point and processing temperatures.
2. What are the Ideal Applications for PEEK?
PEEK excels in demanding environments, including:
- High-Temperature Applications: Aerospace engine components.
- Medical Implants: Spinal cages and dental prosthetics.
- Chemical Processing: Pipe fittings and valve seats.
3. What are the Limitations of PEEK?
While PEEK offers unmatched properties, there are some challenges:
- Cost: PEEK is significantly more expensive than standard thermoplastics like nylon or polypropylene.
- Processing Requirements: The need for high-precision machinery and expertise increases production costs.
Conclusion
PEEK plastic material is a game-changer in modern engineering, offering unparalleled strength, thermal stability, and chemical resistance. Through PEEK injection molding, industries can produce complex, high-quality components for the most demanding environments. By adhering to best practices, leveraging advanced techniques, and working with experienced suppliers, manufacturers can unlock the full potential of PEEK while meeting efficiency and sustainability goals.
Whether you’re exploring injection molded PEEK for a new application or refining an existing process, understanding PEEK’s properties and molding techniques ensures success in high-performance manufacturing. With its unmatched versatility, PEEK remains at the forefront of innovation in materials engineering.