China Injection molding cost
1. What Is Plastic Injection Molding?
Plastic injection molding is a manufacturing process used to create plastic parts in large volumes. The process involves injecting molten plastic into a mold, cooling it, and ejecting a solid product. It’s widely used across industries, from automotive and electronics to medical devices and consumer goods.
Key advantages of plastic injection molding:
- High production efficiency: Suitable for large-scale production.
- Consistency: Produces uniform parts with minimal variation.
- Flexibility: Works with a wide range of materials and designs.
2. Why Choose China for Injection Molding?
China has solidified its reputation as a global leader in manufacturing, offering unparalleled benefits for businesses seeking cost-effective and high-quality injection molding services. Below is an in-depth look at why China injection molding companies are a top choice for businesses worldwide.

a. Competitive Pricing
One of the primary reasons companies turn to China for injection molding is the significantly lower production costs. Chinese manufacturers benefit from reduced labor costs and streamlined operations. These cost advantages allow businesses to save as much as 30-50% compared to production in Western countries, making it an ideal solution for small and large-scale projects alike. This affordability is particularly attractive for startups or companies working within tight budgets without sacrificing quality.
b. Advanced mold Manufacturing Technology
China has invested heavily in modernizing its manufacturing sector, including injection molding. Many China injection molding companies are equipped with cutting-edge machinery capable of producing complex molds with high precision. Advanced Computer Numerical Control (CNC) machines, robotic arms, and automated systems ensure that the finished products meet exacting standards. These technological advancements allow manufacturers to deliver consistent results, even for intricate designs and tight tolerances.
c. Diverse Capabilities
Chinese manufacturers cater to a broad range of industries, including automotive, medical devices, electronics, and consumer goods. Whether you need specialized materials like medical-grade plastics or molds with complex geometries, China injection molding companies can meet your requirements. They can handle everything from low-volume prototypes to high-volume mass production, ensuring flexibility for businesses at all stages of development.
d. Established Supply Chain
China’s robust and well-integrated supply chain is another key advantage. From raw materials to logistics, the country’s infrastructure supports seamless production. This established network enables manufacturers to source high-quality resins and components quickly, reducing lead times and ensuring timely delivery of finished products. Furthermore, many Chinese suppliers have long-standing relationships with global shipping companies, which simplifies the export process.
In summary, China injection molding offers a powerful combination of affordability, advanced technology, industry expertise, and logistical efficiency. These factors make China a strategic choice for businesses aiming to optimize their manufacturing processes while maintaining top-notch quality.

3. Key Factors Affecting Injection Molding Cost in China
Understanding the key factors that influence injection molding costs in China is crucial for planning your budget and making informed decisions. These factors vary based on material selection, mold complexity, production volume, labor, and lead time. Below, we break down how each element impacts pricing.
a. Materials
The choice of materials significantly influences costs.
- Material Type: Common plastics like polypropylene (PP) and acrylonitrile butadiene styrene (ABS) are cost-effective and widely used. However, specialty materials like PEEK, polycarbonate, or medical-grade plastics are more expensive due to their unique properties, such as heat resistance or biocompatibility.
- Material Grade: Higher-grade plastics designed for critical industries, such as automotive or healthcare, come with a premium. These grades are selected to meet strict industry standards.
- Resin Prices: The global market impacts resin costs, which fluctuate based on demand, supply chain conditions, and crude oil prices. Choosing alternative materials during price spikes can mitigate costs.
b. Mold Complexity
Mold design and construction account for a significant portion of the total cost.
- Design Intricacy: Intricate designs with tight tolerances require additional precision, increasing tooling expenses.
- Cavities: Molds with multiple cavities boost production efficiency but involve higher upfront costs. They are ideal for high-volume production to offset the initial investment.
- Mold Material: Durable materials like hardened steel last longer and produce high-quality parts but are more expensive than aluminum, which is often used for low-volume or prototype molds.
c. Production Volume
Higher production volumes reduce the per-unit cost due to economies of scale. For small orders, the fixed costs of mold manufacturing can dominate, making the overall unit cost higher. Bulk production distributes these costs, offering substantial savings.
d. Labor Costs
China’s labor costs remain competitive but vary based on expertise. Skilled operations, such as precision tooling or mold maintenance, command higher wages. Nonetheless, the overall labor cost in China is lower compared to Western countries, providing a cost advantage.
e. Lead Time
Tight deadlines can add to costs. When expedited services are required, manufacturers may need to allocate additional resources or work overtime, leading to increased expenses. Proper planning can avoid these extra charges.
By analyzing these factors, businesses can optimize their China injection molding costs to achieve the best balance between quality and affordability.
4. Typical Cost Breakdown of China Injection Molding
Understanding the cost components of China injection molding is essential for budgeting and ensuring a fair deal. While prices vary based on project specifics, the typical cost breakdown includes mold manufacturing, materials, labor, overhead, and logistics. Below is an expanded explanation of each element.
Mold Cost (30-50%)
Mold costs represent the most significant portion of injection molding expenses, influenced by factors such as mold type, material, and complexity. Single-use molds are less expensive but have limited durability, making them ideal for low-volume production or prototyping. Multi-use molds, on the other hand, require a higher upfront investment due to their durability and capability to produce thousands or even millions of parts. These molds are cost-effective for high-volume production, as the per-unit cost decreases significantly over time.
Material Cost (20-40%)
Material expenses are influenced by the type of plastic resin, its grade, and the volume required. Common resins like polypropylene and ABS are more affordable, while specialty plastics like polycarbonate or medical-grade materials are more expensive. The global market price of resin, determined by supply and demand dynamics, also impacts the material cost.
Labor Cost (10-20%)
Labor costs in China remain competitive but vary depending on the skill level required. Basic tasks like machine operation incur lower costs, while specialized tasks such as mold maintenance or precision adjustments demand higher wages. Labor also includes quality control and product assembly, ensuring the final output meets desired standards.
Overhead (10-15%)
Overhead costs include electricity to operate machinery, facility maintenance, and administrative expenses. Efficient manufacturing processes in China often keep these costs relatively low compared to other countries.
Logistics (5-10%)
The cost of shipping finished products to your location depends on factors like distance, weight, and shipping mode (air or sea). Many Chinese manufacturers offer end-to-end solutions, simplifying this process and ensuring cost-effective delivery.
Understanding this breakdown allows businesses to better plan and manage their injection molding projects in China.

5. Benefits of Working with a China Injection Molding Company
Choosing to work with a China injection molding company can be a game-changer for businesses aiming to balance quality, efficiency, and cost. China’s expertise in the manufacturing sector makes it an attractive destination for companies seeking reliable and scalable production solutions. Below are the key benefits in detail.
Cost Savings
One of the most compelling reasons to collaborate with a Chinese injection molding company is the potential for significant cost savings. Lower labor costs, operational efficiency, and access to affordable raw materials allow Chinese manufacturers to offer competitive pricing. Businesses can save up to 30-50% on production costs compared to Western countries without sacrificing quality or precision.
Customization
China’s injection molding companies excel in providing customized solutions tailored to unique designs and specifications. Whether you need complex geometries, specific material grades, or unique color requirements, these manufacturers possess the expertise and flexibility to bring your vision to life. Their advanced tooling capabilities and diverse material options ensure the product meets exact industry standards and customer requirements.
High Precision
China’s investment in advanced manufacturing technologies has resulted in injection molding companies equipped with cutting-edge machinery. This ensures exceptional precision, tight tolerances, and consistent quality, even for intricate or large-scale projects. With Computer Numerical Control (CNC) equipment, robotics, and automated quality checks, Chinese manufacturers are capable of producing high-quality parts for industries like automotive, medical, and electronics.
Global Shipping Expertise
Many Chinese injection molding companies are well-versed in handling international logistics. They simplify the export process by offering end-to-end solutions, including packaging, customs documentation, and shipping. This expertise minimizes delays and ensures that finished products reach clients efficiently, no matter their location.
Partnering with a China injection molding company ensures a cost-effective, high-quality, and seamless production experience, making it a strategic choice for businesses worldwide.
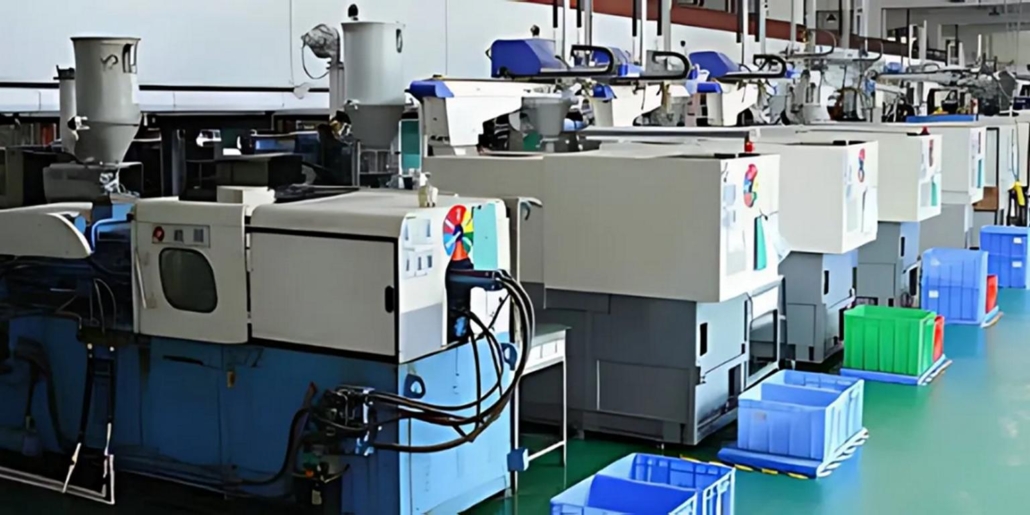
6. How to Choose the Right China Injection Molding Partner
Selecting the right China injection molding company is a critical step in ensuring the success of your manufacturing project. With numerous companies offering injection molding services, careful evaluation and research are essential to find a partner that meets your quality, cost, and timeline requirements. Below are key steps to guide your decision-making process.
Assess Capabilities
Start by evaluating the company’s technical capabilities. Ensure the manufacturer can handle your specific material, design, and volume needs. Some companies specialize in low-volume prototypes, while others focus on high-volume mass production. Check if they have experience with your required materials, whether it’s basic plastics like ABS or specialty materials such as medical-grade polymers.
Check Certifications
Certifications demonstrate a company’s commitment to quality and compliance with industry standards. Look for ISO certifications, which indicate adherence to international quality management standards. For industry-specific needs, check for certifications related to sectors like automotive, medical devices, or electronics to ensure they meet regulatory requirements.
Request a Quote
A detailed quote provides clarity on pricing and helps you compare services between companies. Ensure the quote includes a breakdown of mold costs, material costs, labor, overhead, and logistics. This transparency helps identify hidden fees and determine the most cost-effective option.
Review Customer Feedback
Client testimonials, case studies, and online reviews are valuable resources for assessing a company’s reputation. Positive feedback on timely delivery, product quality, and customer service is a good indicator of reliability. Ask for references if needed and speak with previous clients about their experience.
Conduct a Factory Audit
If feasible, visit the manufacturer’s facility. A factory audit allows you to inspect their equipment, production processes, and quality control measures. It also gives you insight into their operational standards and capabilities.
By following these steps, you can confidently select a China injection molding partner that aligns with your project goals and ensures a successful collaboration.
7. FAQs About China Injection Molding Costs
Q1: What is the average mold cost in China?
Mold costs in China range from $3,000 to $10,000, depending on complexity, size, and material.
Q2: How do labor costs in China compare to other countries?
China offers competitive labor rates, often 30-50% lower than Western countries.
Q3: Can I get small production runs in China?
Yes, many China injection molding companies cater to small batches, but unit costs may be higher.
Q4: How long does it take to produce a mold in China?
Mold manufacturing usually takes 3-8 weeks, depending on complexity.
Conclusion
China injection molding offers an attractive balance of quality, affordability, and efficiency. By understanding the factors influencing China injection molding cost and choosing the right partner, businesses can achieve cost-effective and high-quality production. Whether you’re a startup or an established enterprise, China remains a go-to destination for plastic injection molding solutions.
For assistance in finding the perfect China injection molding company, begin with a thorough evaluation of capabilities, pricing, and reviews to ensure a successful collaboration. With the right approach, you can unlock the full potential of injection molding in China.
Leave a Reply
Want to join the discussion?Feel free to contribute!