I dag har Kina befæstet sin position som global leder inden for sprøjtestøbevirksomheder og er blevet en værdifuld produktionsløsning for virksomheder i alle størrelser i hele verden til konkurrencedygtige priser. Takket være det store antal sprøjtestøbevirksomheder er Kina blevet et specialiseret område inden for produktion af plastkomponenter til hele spektret af industrier, fra bilindustrien, elektronik, sundhedspleje og emballage til forbrugsvarer. De gør det tunge arbejde med avanceret teknologi, præcisionsteknik og automatisering, der bruges til at fremstille støbte dele med uovertruffen nøjagtighed og effektivitet. Der er flere vigtige fordele ved den kinesiske sprøjtestøbningsindustri, som virksomheder har tendens til at vælge. En af de største trækplastre, når det gælder omkostningseffektiv produktion, er, at arbejds- og produktionsomkostningerne er billigere i Kina end i de vestlige lande. Desuden er kinesiske støbevirksomheder i stigende grad udstyret med højeffektive, topmoderne maskiner og robotsystemer, der muliggør effektiv produktion i store mængder, samtidig med at kvaliteten opretholdes. Virksomheden har internationalt anerkendte certificeringer som ISO 9001, ISO 13485 (medicinsk udstyr) og IATF 16949 (bilkomponenter) for at overholde de globale industristandarder for kvalitet.
Kinesiske sprøjtestøbevirksomheder har også styrken i tilpasning og innovation. Producenter i Kina har den tekniske kapacitet såvel som ekspertisen til at levere tilpassede forme til en kundes multihulrumsforme, overmolding, indsatsstøbning og komplicerede designs. For virksomheder, der leder efter hastighed og pålidelighed, er deres evne til at levere hurtig ekspeditionstid og produktion i stor skala et foretrukket valg.
Hvad er sprøjtestøbning?
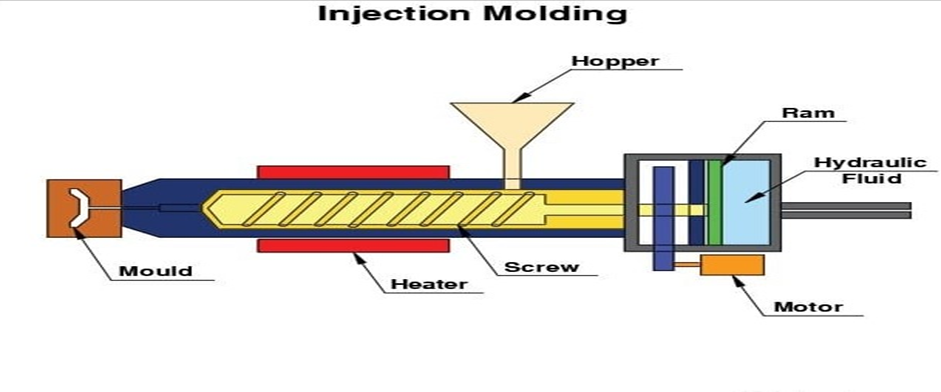
Det er en proces, hvor man fremstiller plastdele ved at sprøjte smeltet materiale ind i en form. Den er meget udbredt inden for f.eks. bilindustrien, medicin, elektronik, plastemballage og husholdningsartikler. Denne proces gør det muligt at fremstille komplekse dele i masseproduktion med høj præcision og ensartethed.
Hvorfor bruge en kinesisk sprøjtestøbevirksomhed?
For det første er Kina blevet et vigtigt knudepunkt for sprøjtestøbning af flere forskellige årsager:
1. Omkostningseffektiv produktion
Priserne er en af de vigtigste grunde til, at virksomheder vælger kinesiske støbevirksomheder. Fordi arbejds- og driftsomkostningerne i Kina er lavere end i de vestlige lande, er det muligt at producere støbte komponenter af høj kvalitet til en brøkdel af prisen.
2. Avanceret produktionsteknologi
I moderne kinesiske sprøjtestøbevirksomheder investeres der kraftigt i automatisering og topmoderne maskiner. Præcision og den højeste produktivitet sikres af mange virksomheder, der bruger robotsystemer, computerstøttet design (CAD) og kvalitetskontrolsystemer i realtid.
3. Standarder af høj kvalitet
De fleste respektable kinesiske støbevirksomheder overholder internationale kvalitetsstandarder som ISO 9001, ISO 13485 (til medicinsk udstyr) og IATF 16949 (dele til bilindustrien). Disse certificeringer garanterer, at produktet opfylder kravene til høj kvalitet.
4. Tilpasning og innovation
Tilpassede løsninger, der passer til forskellige forretningsbehov, leveres af mange kinesiske støbevirksomheder. Kinesiske producenter har et svar på enhver kundes behov fra overstøbning og indsatsstøbning til en kundes behov for komplekse modeller med flere hulrum.
5. Hurtig ekspeditionstid
Kinesiske støbevirksomheder kan producere i store mængder mere effektivt og hurtigt end de fleste konkurrenter på grund af effektive forsyningskæder og strømlinede produktionsprocesser. Virksomheder, der er afhængige af hastighed for at bringe produkter på markedet, har brug for støtte fra denne hastighed.
6. Erfaring og ekspertise
Der er tusindvis af specialiserede virksomheder i Kinas sprøjtestøbningsindustri, som har stor erfaring inden for alle disse områder. De betragtes som det foretrukne valg for globale virksomheder inden for deres domæne af formdesign og materialevalg samt præcisionsteknik.
Brancher, der nyder godt af kinesiske sprøjtestøbevirksomheder

Brugen af sprøjtestøbning er ret bred og spredes ud i forskellige industrier, som hver især har deres egne standarder og teknologier.
1. Bilindustrien
Kinesiske støbevirksomheder producerer dele som instrumentbrætter, kofangere, indvendige paneler og belysningskomponenter til bilindustrien, som er meget afhængig af disse virksomheder. En vigtig fordel er evnen til at fremstille lette, men holdbare plastdele.
2. Elektronik og forbrugsvarer
Til elektronik- og forbrugsvareindustrien og forskellige andre produkter har kinesiske sprøjtestøbevirksomheder specialiseret sig i at producere dele med høj præcision. Der er brug for flere og flere æstetisk tiltalende, holdbare og funktionelle plastkomponenter.
3. Medicin og sundhedspleje
Enheder som kirurgiske instrumenter, sprøjter og IV-stik bruger alle sprøjtestøbte dele af høj kvalitet, og den medicinske industri kan ikke undvære dem. Afhængigt af den medicinske producent har mange kinesiske støbevirksomheder renrumsfaciliteter til strenge hygiejne- og sikkerhedsstandarder i henhold til den medicinske produktion.
4. Emballage og fødevareindustri
Sprøjtestøbning bruges også til et andet vigtigt formål, nemlig plastemballage, som omfatter beholdere, kapsler og flasker. På den ene side producerer kinesiske producenter holdbare emballageløsninger af høj kvalitet, mens de på den anden side er miljøvenlige.
Nøglespillere i den kinesiske sprøjtestøbningsindustri
Sprøjtestøbning har vist sig at være førende i Kina inden for industrier som bilindustrien, sundhedssektoren, elektronik og forbrugsvarer med høj kvalitet og omkostningseffektivitet. Kinesisk Sprøjtestøbevirksomheder bliver ved med at være førende på det globale marked ved hjælp af avancerede produktionsmuligheder, topmoderne udstyr og ved at følge internationale kvalitetsstandarder. Der er et par af disse velkendte kinesiske støbeforme, der fremstiller Kinaforme, der fremstiller plastdele.
Sincere Tech: En førende leverandør af løsninger til plastsprøjtestøbning
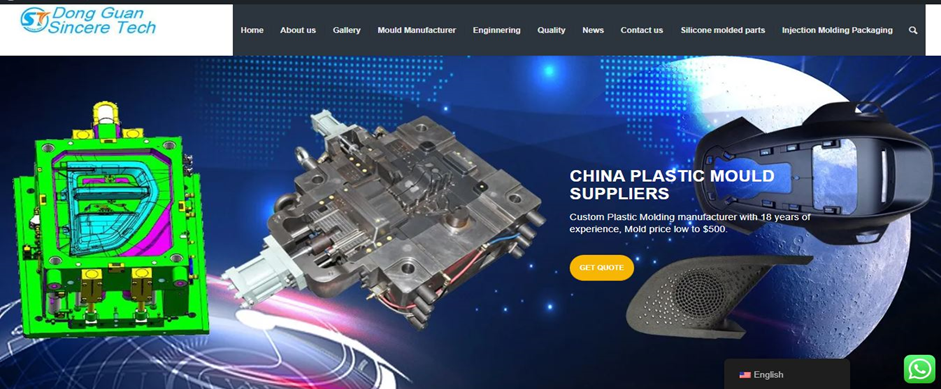
Sincere Tech, der blev grundlagt i 2005 og ligger i byen Dongguan i Kina, er kendt for mere end 10 års levering af forretningsstøbte plastindsprøjtningsforme. Virksomheden har udvidet sin kapacitet til at omfatte ting som Eddie-støbeforme, silikonegummistøbning, CNC-bearbejdning og komplet produktsamling og deltager i en lang række industrier over hele verden.
Mangfoldigt udvalg af tjenester
Sincere Tech leverer samlede produktionsløsninger til de kunder, der har følgende typer:
- Virksomheden leverer produkter som f.eks. specialfremstillede plastsprøjtestøbeforme med mulighed for at designe og fremstille højpræcisionsforme til massefremstilling af holdbare og præcise plastkomponenter.
- Præcisionsbearbejdning - CNC-bearbejdning, fræsning, boring, drejning og slibning udført af Sincere Tech er med fuld ekspertise, hvilket sikrer, at hver del, der fremstilles, er med præcision og af høj kvalitet.
- For at øge fremstillingsprocessen opnår virksomheden, der fremstiller trykstøbningsforme, succes ved at fremstille højkvalitets og højtydende trykstøbningsforme og samle dem for at producere holdbare metalkomponenter, der opfylder specifikationerne i de strenge branchekrav.
- Vi leverer sprøjtestøbningstjenester ved at bruge avancerede plastsprøjtestøbemaskiner til at producere komponenter lavet af følgende materialer som PP, ABS, PPS, PEEK, PA66+GF30.
- Produktsamlingstjenester - Virksomheden samler effektivt underenheder, enkle samlinger og fuldt monterede produkter i henhold til strenge kvalitetsstandarder.
- Sincere Tech leverer silikonestøbningsløsninger til specifikke projekter i forskellige brancher.
Forpligtelse til kvalitet og teknologiske fremskridt
Men oprigtigt talt opretholder tech den højeste kvalitetsstandard ved at overholde internationale standarder som ISO 9001:2015 og QS 9000:2015. For at fremstille forme og dele af den bedste kvalitet gør virksomheden brug af avancerede maskiner, herunder CMM-maskiner, 5-aksede CNC-maskiner og FANUC-maskiner. Sincere Tech matcher også kunder med NDA'er (Non-Disclosure Agreements) til beskyttelse af kundernes intellektuelle ejendom og proprietære design til fortrolighedsformål.
Betjener globale industrier
Sincere Tech er en internationalt stærk virksomhed, der leverer plast- og metalkomponenter til forskellige brancher (bilindustrien, medicinalindustrien, elektronik, husholdningsapparater, havearbejde, kosmetik, fødevareemballage og elektriske stik). Virksomheden har et meget godt salg på eksportmarkedet, hvis produkter sendes til forskellige globale markeder, herunder Finland, da de kan opfylde de forskellige branchespecifikke standarder og krav.
Kundefokuseret tilgang
Sincere Tech værdsætter konkurrencedygtige priser, produktion af høj kvalitet og god service. På den anden side, som en pålidelig partner for internationale virksomheder, er virksomhedens projektledelsesevner stærke, kommunikationen på teknisk engelsk er klar, og kundetilfredsheden er høj.
Seasky Medical
Seasky Medical er en kinesisk sprøjtestøbevirksomhed, der fremstiller plast til medicinsk brug. Virksomheden har haft hovedkvarter i Shenzhen, Guangdong, siden 1999 og leverer de bedste løsninger inden for sprøjtestøbning. De tilbyder fint formdesign, materialevalg og sprøjtestøbning samt tager sig af produktudvikling, så medicinske komponenter lever op til de højeste kvalitets- og sikkerhedsstandarder.
ISO 8-certificeret drift hos Seasky Medical sikrer produktion af medicinsk udstyr som sprøjter, IV-komponenter og kirurgiske instrumenter i et forureningsfrit miljø. Som en virksomhed med over et årtis erfaring er de kendt for at levere pålidelig og præcis medicinsk sprøjtestøbning, hvor de betjener globale sundhedsudbydere.
Shenzhen Silver Basis Technology Co, Ltd
Shenzhen Silver Basis Technology er en professionel kinesisk støbevirksomhed, der er dedikeret til fremstilling af støbeforme til bilindustrien og industrien. Virksomheden blev dannet i 1993 og er en af de mest pålidelige leverandører til verdens berømte mærker som Peugeot og ZTE og leverer modeller til forskellige anvendelser.
Silver Basis tilbyder et omfattende udvalg af tjenester inden for metalstempling, trykstøbning, formfremstilling og produkttest. På grund af deres ekspertise inden for sprøjtestøbning til biler kan de fremstille indvendige og udvendige køretøjsdele, der er holdbare og præcise. Da virksomheden er fokuseret på kvalitet, har den fået tildelt ISO 9001- og ISO 14001-certifikater, og derfor er den en virksomhed, der vælges af internationale bil- og elektronikproducenter.
JMT Automotive Mold Co., Ltd
JMT Automotive Mold Co, Ltd er en velrenommeret kinesisk sprøjtestøbevirksomhed, der beskæftiger sig med design og fremstilling af støbeforme til biler. Siden grundlæggelsen i 2005 og med base i Taizhou, Zhejiang, har virksomheden opbygget et solidt produktionssystem for at imødekomme bilindustriens stigende behov.
JMT Automotive Mold har en driftserfaring på et produktionssted på 23.000 kvadratmeter og er en af de producenter, der har specialiseret sig i SMC-form, husholdningsapparatform samt industriel form. De har højhastigheds-CNC-maskiner, præcisionstestudstyr og topmoderne sprøjtestøbemaskiner, der fører til en høj produktionsstandard. JMT Automotive opretholder driften af teknologisk innovation og præcisionsteknik, og vi tilbyder stadig pålidelig formfremstilling til indenlandske og udenlandske kunder.
TK Mold Ltd
TK Mold Ltd blev grundlagt i 1978 og er et velkendt kinesisk støbefirma med mere end 40 års erfaring inden for fremstilling af plastforme. Virksomheden blev grundlagt i 1983 og har specialiseret sig i udvikling af højpræcisionsforme til medicinske apparater, forbrugerelektronik, intelligente husholdningsapparater og bilkomponenter.
TK Mold tilbyder avancerede sprøjtestøbeløsninger til sin globale kundegruppe fra sin base med 5 produktionsanlæg, herunder et i Tyskland. Virksomheden er en pioner inden for anvendelse af avanceret teknologi, automatisering og præcisionsfremstilling og er meget værdsat af industrier, der kræver højtydende plastkomponenter. Alle produkter fra TK Mold er certificeret under ISO 9001, ISO 13485 og ISO 14001 for at sikre, at de falder inden for de internationale kvalitets- og sikkerhedsstandarder.
Guangdong Yizumi Precision Machinery Co, Ltd
Guangdong Yizumi er en førende kinesisk sprøjtestøbevirksomhed, der producerer højtydende sprøjtestøbemaskiner samt plastkomponenter. Yizumi blev grundlagt i 2002, og hovedkvarteret ligger i Foshan, Guangdong. Med en produktionsbase på over 600.000 kvadratmeter og næsten 3.000 ansatte har Yizumi udviklet sig til et verdensmærke.
Yizumi har vundet adskillige branchepriser for sine innovationer inden for sprøjtestøbningsteknologi og er kendt for sine innovative støbeløsninger. I 2015 blev virksomheden den første kinesiske støberivirksomhed, der blev noteret på Shenzhen Stock Exchange. Yizumi fokuserer på bilindustrien, forbrugerelektronik og industrielle applikationer og er ved at blive førende i branchen med sine topmoderne maskiner og støbning med høj præcision.
Udfordringer og overvejelser, når du vælger en kinesisk støberivirksomhed
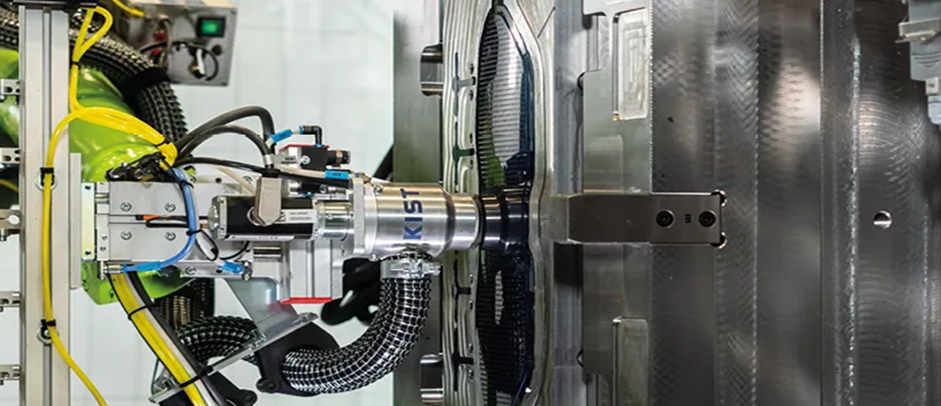
Kinesiske mineselskaber har mange fordele, men inden man binder sig til en producent, bør man være opmærksom på nogle få aspekter.
1. Kvalitetskontrol og overholdelse
Ikke alle producenter følger de samme kvalitetsstandarder. Før du vælger en leverandør, bør du kontrollere certificeringer og teste en prøve først.
2. Beskyttelse af intellektuel ejendom
Produktion i Kina kan være et problem for outsourcing af beskyttelse af intellektuel ejendom (IP). For at undgå at miste deres design og holde dem sikre, bør virksomheder arbejde med pålidelige partnere og juridiske aftaler.
3. Kommunikations- og sprogbarrierer
Selv om flere kinesiske producenter har engelsktalende salgsteams, er kommunikationen ikke altid ligetil. Dokumentation og aftaler udarbejdes for at forhindre misforståelser.
4. Logistik og forsendelse
Det kan dog være komplekst og dyrt at håndtere store ordrer internationalt. Kinesiske støbevirksomheder skal have forståelse for virksomhedernes toldregler, leveringstider og fragtomkostninger.
Fremtidige tendenser inden for kinesisk sprøjtestøbning
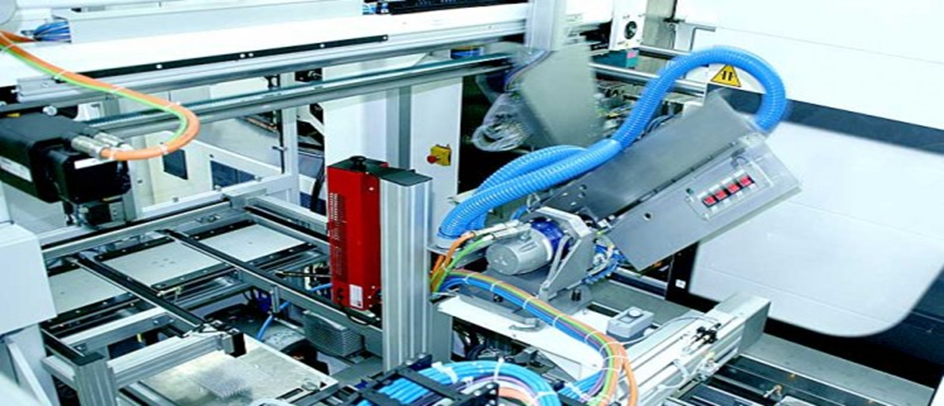
Med nye teknologier kommer udviklingen af den kinesiske støbeindustri for at imødekomme de nye markedskrav. De vigtigste tendenser omfatter:
1. Bæredygtige og miljøvenlige materialer
Efterhånden som bekymringen for plastaffald er vokset i Kina, er mange støbevirksomheder blevet mere bekymrede for miljøbestemmelser og udvikler nu biologisk nedbrydelige og genbrugte plastmaterialer.
2. Smart produktion og industri 4.0
Automatiseringen og den AI-drevne kvalitetskontrol, den komplette overgang fra en menneskecentreret proces til en IoT-aktiveret smart fabrik har fuldstændig forvandlet sprøjtestøbningsprocessen, og det gør produktionen mere effektiv og mindre spild.
3. Øget tilpasning og on demand-produktion
Virksomhedernes fokus flytter sig til on-demand, produktion af små partier til nichemarkeder og hurtig produktudvikling.
Konklusion
Kinesiske sprøjtestøbevirksomheder er en integreret del af den globale fremstillingsindustri, da disse virksomheder leverer omkostningseffektive og innovative løsninger af høj kvalitet til kunderne. Nogle af disse producenter bearbejder plastdele til bilkomponenter, medicinsk udstyr og andre relaterede industrier. Når man vælger en kinesisk støberivirksomhed, bør man nøje undersøge kvalitetsstandarder, kommunikationsmuligheder og logistik for at sikre et vellykket partnerskab. På grund af den kontinuerlige tendens til teknologiske fremskridt og bæredygtig praksis vil kinesiske støbevirksomheder fortsat være førende inden for sprøjtestøbning i mange år endnu. I betragtning af de mange fordele bør virksomheder dog tage højde for kvalitetskontrol, beskyttelse af intellektuel ejendomsret, kommunikationsudfordringer og logistik, før de vælger en kinesisk støbepartner. Men hvis der er foretaget grundig research og samarbejde med producenter, der producerer med kvalitet og er certificeret til arbejdet, kan virksomhederne høste fordelene ved Kinas ekspertise inden for sprøjtestøbning. I fremtiden vil sprøjtestøbning i Kina være præget af bæredygtige materialer, smart produktion, højhastighedsproduktion og produktionsdrevet automatisering kombineret med bionedbrydelig plast og Industri 4.0-teknologier, og Kina vil stadig have de største fremskridt inden for global sprøjtestøbning. Når de kinesiske sprøjtestøbevirksomheder hele tiden udvikler sig og gør deres bedste for at ændre den kinesiske produktion, vil de fortsætte med at drive den moderne produktion fremad.
Ofte stillede spørgsmål (FAQ)
1. Hvorfor er produktion af sprøjtestøbning fra Kina populær?
At vælge Kina til sprøjtestøbning giver fordelen af omkostningseffektiv produktion, moderne teknologi, veluddannet arbejdsstyrke og velorganiseret forsyningskæde. Der er mange producenter, der følger internationale kvalitetsstandarder, og de tilbyder tilpassede løsninger med meget hurtigere ekspeditionstid.
2. Hvordan gavner kinesiske sprøjtestøbevirksomheder industrien?
Alle disse industrier har været afhængige af kinesisk sprøjtestøbning, herunder bilindustrien, elektronik, medicinsk udstyr, emballage og forbrugsvarer. Kinesiske producenter kan effektivt og billigere producere de højpræcise plastkomponenter, der er nødvendige for disse industrier.
3. Hvordan garanterer kinesiske sprøjtestøbevirksomheder produktkvalitet?
Kina støber pålidelige virksomheder, der strengt kontrollerer kvaliteten fra råvarer til færdige produkter og opnår følgende certifikater: ISO 9001, ISO 13485 (medicinsk) og IATF 16949 (dele til bilindustrien). Deres niveau af testprocesser og automatiserede inspektionssystemer holder dem op til høje standarder.
4. Hvad er valget af en kinesisk støbeproducent?
Kvalitetscertificeringer, erfaring, produktionskapacitet, beskyttelse af intellektuel ejendomsret og evnen til at kommunikere og yde logistiksupport bør tages i betragtning af virksomhederne. For at bane vejen for et godt partnerskab bør man foretage stikprøver og sikre, at virksomheden er i stand til at levere.
5. Hvad er udsigterne for den kinesiske sprøjtestøbningsindustri?
De tider, vi lever i, kræver, at industrien finder nye tendenser til at løse dem, herunder bæredygtig og biologisk nedbrydelig plast, AI-drevet automatisering, intelligente fabrikker og produktion efter behov. Disse fremskridt vil gøre produktionen mere effektiv, give mindre spild og imødekomme den stadigt voksende efterspørgsel efter miljøvenlige produktionsløsninger.