Was ist eine Kunststoff-Spritzgussform?
Kunststoff-Spritzgießen ist eine der effektivsten Methoden zur Herstellung von Kunststoffteilen und bietet ein hohes Maß an Präzision und Produktionseffizienz. Bei diesem Verfahren werden Kunststoffe geschmolzen und in eine zuvor entworfene Form gespritzt, die den Kunststoff beim Abkühlen in eine bestimmte Form bringt. Dieser Artikel befasst sich mit den Grundlagen von Kunststoff-Spritzgießwerkzeugen und beschreibt die Arten, Komponenten, Herstellungsverfahren und Überlegungen zur Auswahl des richtigen Werkzeugs für die jeweiligen Produktionsanforderungen.
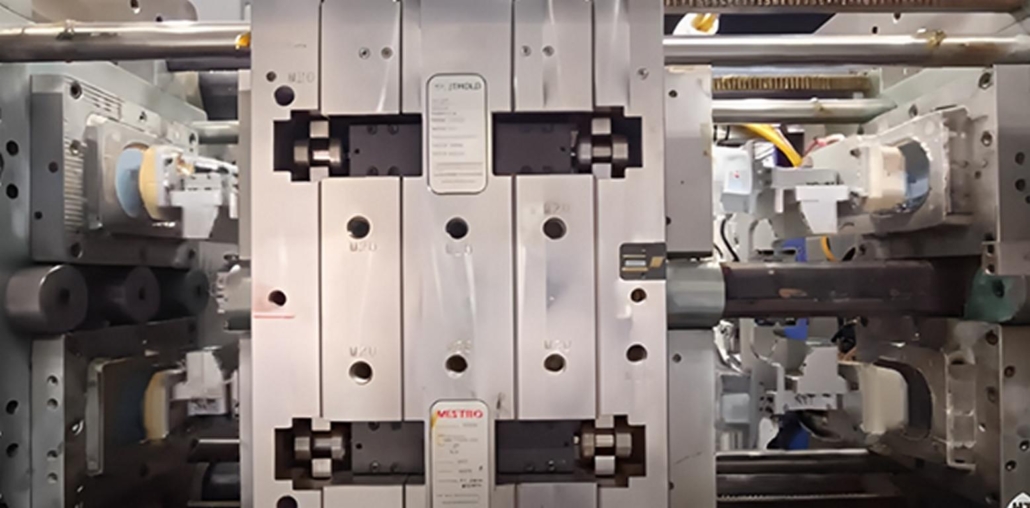
Einführung in das Kunststoffspritzgießen
Kunststoff-Spritzgießen ist eine Technik zur Herstellung komplizierter, präziser Kunststoffteile in großen Mengen. Seit seiner Entwicklung im späten 19. Jahrhundert hat das Verfahren die Fertigungsindustrie verändert und ermöglicht die Hochgeschwindigkeitsproduktion von Teilen in einer Vielzahl von Sektoren, darunter Automobilbau, Elektronik, medizinische Geräte und Konsumgüter.
Vorteile des Kunststoffspritzgießens
- Hohe Effizienz und Geschwindigkeit: Das Spritzgießen bietet eine kurze Produktionszykluszeit, was schnelle Produktionsraten ermöglicht. Mehrere Formen können gleichzeitig laufen, um den Ausstoß weiter zu erhöhen.
- Reproduzierbarkeit: Das Verfahren ist so konzipiert, dass identische Teile in mehreren Produktionsläufen hergestellt werden können, was besonders in Branchen, die hohe Präzision und Konsistenz erfordern, von Vorteil ist.
- Komplexe Konstruktionsfähigkeiten: Mit Spritzgießwerkzeugen lassen sich komplizierte Geometrien herstellen, darunter dünne Wände, Hinterschneidungen und komplexe Oberflächendetails.
- Flexibles Material: Beim Spritzgießen kann eine Vielzahl von thermoplastischen und duroplastischen Kunststoffen verwendet werden, die jeweils so ausgewählt werden, dass sie dem Endprodukt spezifische Eigenschaften verleihen.
- Minimaler Abfall: Bei richtig konzipierten Formen und fortschrittlichen Prozesskontrollen entsteht beim Spritzgießen wenig bis gar kein Materialabfall.
Überblick über Kunststoff-Spritzgussformen
A Kunststoffspritzgussform ist ein komplexes Werkzeug, mit dem geschmolzenes Kunststoffmaterial zu einem fertigen Produkt geformt wird. Die Form wird in der Regel aus Stahl oder Aluminium hergestellt und besteht aus zwei Haupthälften: der Kavität und dem Kern, die jeweils für die Formung des Äußeren und des Inneren des fertigen Teils verantwortlich sind. Aufgrund der hohen Drücke, die beim Spritzgießen auftreten, müssen diese Formen robust und verschleißfest sein und ihre Form auch bei wiederholten Zyklen beibehalten können.
Jede Form besteht aus mehreren Teilen, die zusammenarbeiten, um die Präzision beim Formen, Kühlen und Auswerfen des Teils zu gewährleisten. Nachstehend finden Sie eine Aufschlüsselung der wichtigsten Komponenten einer Spritzgussform und ihrer jeweiligen Funktionen.
Wichtige Komponenten der Form
- Spritzgussform Kavität und Kern: Dies sind die Hauptelemente der Form. Die Hohlraumseite (in der Regel die "A"-Seite) ist für die Gestaltung der Außenfläche des Teils verantwortlich, während die Kernseite (die "B"-Seite) das Innere gestaltet. Zusammen bilden sie den Hohlraum, der die Geometrie des Teils bestimmt. Die Wahl des Hohlraum- und Kernmaterials hängt vom Produktionsvolumen ab, da verschleißfeste Werkstoffe wie gehärteter Stahl häufig für die Großserienproduktion verwendet werden, während weichere Metalle für kleinere Serien ausreichen können.
- Schieber und Heber: Schieberegler und Heber ermöglichen die Herstellung von Hinterschneidungen oder komplexen Geometrien, die mit einer einfachen zweiteiligen Form nicht geformt werden können. Schieber bewegen sich seitlich, wenn sich das Werkzeug öffnet, und schaffen so Platz für Vorsprünge oder Nuten, während sich Heber in einem Winkel nach außen bewegen, um das Teil zu lösen. Beide tragen dazu bei, dass Teile mit komplexen Formen ohne Beschädigung ausgeworfen werden können.
- Anguss-, Angusskanal- und Anschnittsysteme: Die Anguss leitet den geschmolzenen Kunststoff von der Düse der Spritzgussmaschine in die Form und führt ihn zum Läufer System, das den Kunststoff in jede Kavität einer Mehrkavitätenform leitet. Pforten sind die endgültigen Eintrittsstellen für den geschmolzenen Kunststoff in die Kavität, wo er abkühlt und seine Form annimmt. Jede Komponente dieses Systems wirkt sich darauf aus, wie gleichmäßig und schnell das Material die Form füllt, was sich auf die Teilequalität und die Zykluszeit auswirkt.
- Auswerfersystem: Nachdem das Formteil abgekühlt und erstarrt ist, wird die Auswerfersystem drückt das Teil aus dem Formhohlraum. Das Auswerfersystem umfasst häufig Stifte oder Platten, die von der Kernseite her Kraft auf das Teil ausüben und dafür sorgen, dass es sich ohne Beschädigung löst. Dieses System muss genau getaktet und gesteuert werden, um eine Verformung oder ein Verkleben des Teils zu verhindern.
- Kühlungskanäle: Kühlungskanäle sind Kanäle in den Formplatten, durch die Kühlmittel, in der Regel Wasser, geleitet wird, um die Wärme der Kunststoffschmelze aufzunehmen und abzuleiten. Eine effiziente Kühlung ist für den Formgebungsprozess von entscheidender Bedeutung, da sie die Zykluszeit verkürzt und sich auf die Maßhaltigkeit und die mechanischen Eigenschaften des Teils auswirkt. Das Design der Kühlkanäle - ob konforme, Ablenkungs- oder Bubbler-Kanäle - kann die Leistung und Effizienz der Form erheblich beeinflussen.
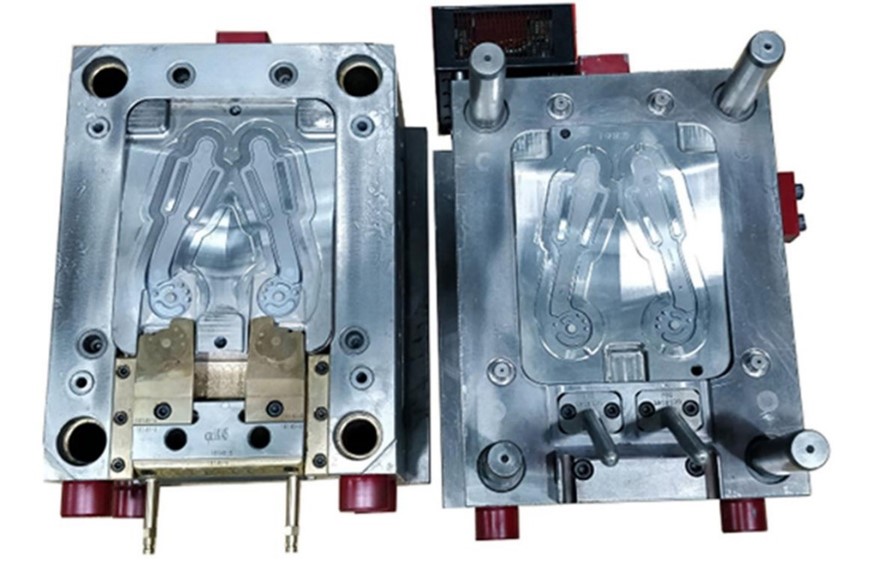
Aufbau einer Kunststoff-Spritzgussform
Die Struktur einer Kunststoff-Spritzgussform ist so konzipiert, dass sie dem Druck, den Temperaturen und den mechanischen Beanspruchungen bei wiederholten Spritzgusszyklen standhält. Hier ein genauerer Blick auf die strukturellen Komponenten und ihre Funktion im Formgebungsprozess:
- A- und B-Schilder: Dies sind die Hauptplatten der Form, die die Kavität bzw. den Kern halten. Die A-Platte ist feststehend, während die B-Platte sich zum Öffnen und Schließen der Form bewegt. Diese Platten sind so konzipiert, dass sie die Ausrichtung beibehalten und dem Druck beim Einspritzen standhalten.
- Klemmbleche: Diese Platten sichern das Werkzeug in der Schließeinheit der Spritzgießmaschine. Ihre Konstruktion muss die Stabilität während der Hochdruck-Einspritzphase gewährleisten, um Fehlausrichtungen oder Bewegungen zu vermeiden, die zu Fehlern führen könnten.
- Trennungslinie: Die Trennebene ist die Stelle, an der sich die A- und B-Platten treffen. Eine gut ausgerichtete Trennebene ist wichtig, um Defekte wie Grate (dünne Kunststoffschichten an den Formnähten) zu vermeiden und eine reibungslose Entformung des Teils zu gewährleisten. Die Lage der Trennebene hängt oft von der Konstruktion des Teils und den Anforderungen der Form ab.
- Kühlungskanäle: Kühlkanäle sind ein wesentlicher Faktor für die Aufrechterhaltung der Formleistung und die Verkürzung der Zykluszeiten. Die Kanäle werden sorgfältig konstruiert, um eine gleichmäßige Kühlung des Formhohlraums und des Kerns zu gewährleisten, was entscheidend ist, um Defekte wie Verzug oder innere Spannungen zu vermeiden. Zu den Arten von Kühlkanälen gehören:
- Konforme Kühlung: Kanäle, die der Kontur des Teils folgen und für eine gleichmäßige Kühlung sorgen, die der Form des Formhohlraums entspricht.
- Baffle-Kühlung: Verwendet Einsätze zur Führung des Kühlmittelflusses und wird üblicherweise verwendet, wenn die Größe der Form die Platzierung der Kanäle begrenzt.
- Bubbler-Kühlung: Bubbler-Rohre sorgen für zusätzliche Kühlung in bestimmten Bereichen, insbesondere bei dicken Abschnitten, die eine schnellere Kühlung erfordern.
- Kühlungsstifte: In den Kern eingebettete Stifte sorgen für eine lokale Kühlung in dicken Abschnitten und helfen bei der Temperaturverteilung in größeren Formen oder Formen mit mehreren Kavitäten.
Das Kühlungsdesign hat einen großen Einfluss auf die Zykluszeit und damit auf die Kosten und die Produktivität des Spritzgießprozesses.
Arten von Kunststoff-Spritzgießformen
Es gibt verschiedene Arten von Kunststoff-Spritzgussformen, die den unterschiedlichen Produktionsanforderungen, Komplexitäten und Teileanforderungen gerecht werden. Hier sind einige der am häufigsten verwendeten Typen:
- Ein-Kavitäten-Werkzeuge: Diese Formen produzieren ein Teil pro Zyklus. Sie werden häufig für kleinere Produktionsmengen oder hochpräzise Teile verwendet, bei denen eine genauere Kontrolle über jedes einzelne Teil erforderlich ist. Einzelkavitäten-Werkzeuge haben den Vorteil, dass sie einfacher einzurichten und für eine begrenzte Produktion kostengünstiger sind.
- Mehrkavitäten-Werkzeuge: In Mehrkavitätenwerkzeugen ermöglichen mehrere identische Kavitäten die Herstellung mehrerer Teile in einem einzigen Zyklus. Dies steigert die Effizienz und ist ideal für die Großserienproduktion, da die Zykluszeit pro Teil und die Gesamtkosten reduziert werden. Allerdings sind Mehrkavitätenwerkzeuge komplexer zu konstruieren und erfordern ein präzises Gleichgewicht im Angusssystem, um eine gleichmäßige Füllung zu gewährleisten.
- Familie Schimmelpilze: Familienformen enthalten verschiedene Kavitäten in einer einzigen Form und ermöglichen die Herstellung verschiedener Komponenten in einem Zyklus. Dies ist besonders nützlich, wenn verschiedene Teile zusammen gegossen werden müssen, wie z. B. bei Baugruppen. Allerdings kann es eine Herausforderung sein, die Füllrate für unterschiedlich große Teile auszugleichen, was zu Defekten führen kann, wenn nicht sorgfältig gearbeitet wird.
- Heißkanal vs. Kaltkanalformen:
- Heißkanal-Werkzeuge: Die Verwendung von beheizten Komponenten hält den Kunststoff innerhalb des Kanalsystems geschmolzen, wodurch der Abfall minimiert und der Zyklus beschleunigt wird. Heißkanäle sind effizient für die Großserienproduktion, erfordern jedoch eine sorgfältige Kontrolle und höhere Anschaffungskosten.
- Formen für Kaltkanäle: Lassen Sie den Kunststoff im Anguss bei jedem Zyklus abkühlen und erstarren. Der verfestigte Anguss wird in der Regel zusammen mit dem Teil ausgeworfen, das unter Umständen durch eine Nachbearbeitung entfernt werden muss. Kaltkanalwerkzeuge sind einfacher und kostengünstiger und eignen sich daher für die Produktion kleinerer Stückzahlen.
- Zwei-Platten- vs. Drei-Platten-Werkzeuge:
- Zwei-Platten-Formen: Sie bestehen aus einer einzigen Trennebene und sind einfacher aufgebaut. Sie werden in der Regel für einfache Teile verwendet, die nur einen Anschnitt benötigen.
- Drei-Platten-Formen: Einfügen einer zusätzlichen Platte, die zwei Trennlinien erzeugt. Dies ermöglicht komplexere Anschnittsysteme, wie z. B. den zentralen Anschnitt, der die Ästhetik der Teile verbessert und die Nachbearbeitung reduziert.
- Etagen- und Rotationsgussformen:
- Stapel-Formen: Etagenwerkzeuge verwenden mehrere Ebenen von Kavitäten und verdoppeln oder verdreifachen die Produktionskapazität, ohne dass die Schließkraft der Maschine erhöht werden muss. Sie sind vorteilhaft für die Produktion von sehr hohen Stückzahlen, erfordern aber fortschrittliche Maschinen und Handhabung.
- Rotationsformen: Rotationsformen ermöglichen das Umspritzen und die Montage im Werkzeug durch Drehen der Kavitäten zwischen den Stationen. Sie werden häufig für Teile aus mehreren Materialien verwendet, z. B. für solche, die eine Kombination aus starren und flexiblen Kunststoffen erfordern.
Jede Art von Form hat ihre eigenen Vorteile und Herausforderungen, und die Wahl der richtigen Form hängt von Faktoren wie Produktionsvolumen, Komplexität der Teile und Materialanforderungen ab.

Kunststoff-Spritzgießverfahren
Der Spritzgießprozess besteht aus mehreren wichtigen Schritten, die alle für die Herstellung hochwertiger Teile entscheidend sind. Hier ist eine detaillierte Aufschlüsselung:
- Klemmen: Die Form wird fest eingespannt, um das Einspritzen des geschmolzenen Kunststoffs vorzubereiten. Die Schließkraft wird auf der Grundlage des Werkzeuginnendrucks berechnet, um sicherzustellen, dass kein Kunststoff durch die Trennebene entweicht.
- Einspritzung: Geschmolzener Kunststoff wird durch den Anguss, den Angusskanal und den Anschnitt in den Formhohlraum eingespritzt. Die Einspritzgeschwindigkeit, der Druck und die Temperatur müssen genau gesteuert werden, da sie den Fluss und die Qualität des Materials in der Kavität beeinflussen.
- Kühlung: Die Abkühlung beginnt, sobald der Kunststoff in die Form eintritt. Die Abkühlungsgeschwindigkeit muss gleichmäßig sein, um Defekte wie Verzug oder Schrumpfung zu vermeiden. Die Kühlkanäle spielen hier eine wichtige Rolle, da sie dafür sorgen, dass die Wärme effektiv aus der Form abgeleitet wird. Auf diese Phase entfällt oft der größte Teil der Zykluszeit.
- Auswurf: Sobald das Teil erstarrt ist, drücken Auswerferstifte oder -platten das Teil aus der Form. Der Ausstoß muss sorgfältig erfolgen, um das Teil nicht zu beschädigen, insbesondere wenn es komplexe Merkmale aufweist oder aus sprödem Material besteht.
Jede Phase des Spritzgießprozesses erfordert eine präzise Steuerung, um Teile herzustellen, die den Qualitätsstandards entsprechen und gleichzeitig die Zykluszeit und die Produktionskosten minimieren.
Kühlkanäle für Spritzgussformen
Kühlkanäle sind beim Kunststoffspritzgießen von entscheidender Bedeutung, da sie die Zykluszeit, die Teilequalität und die Produktionseffizienz erheblich beeinflussen. Die richtige Auslegung der Kühlung ist entscheidend, um Defekte wie Verzug, Schrumpfung oder innere Spannungen zu vermeiden, die bei ungleichmäßiger oder zu schneller Kühlung auftreten können.
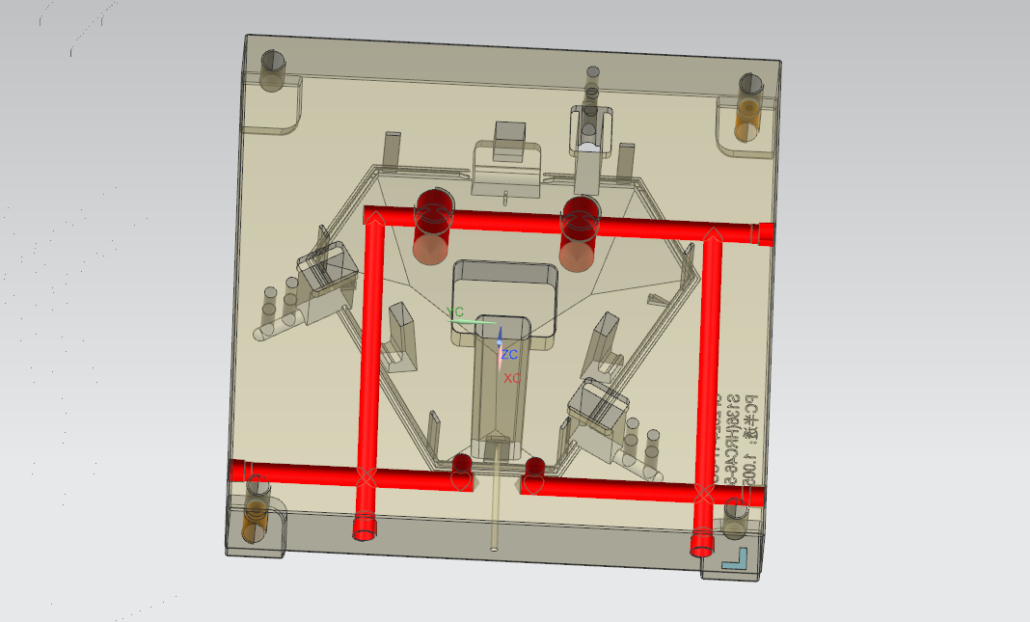
Arten von Kühlkanälen in Spritzgießwerkzeugen
- Konforme Kühlung: Bei dieser fortschrittlichen Technik werden Kühlkanäle entworfen, die der Kontur des Teils in der Form folgen. Die konforme Kühlung bietet eine gleichmäßige Kühlung über die gesamte Oberfläche des Teils, wodurch die Zykluszeit verkürzt und die Qualität des Teils verbessert wird. Die konforme Kühlung, die in der Regel durch 3D-Druck und andere fortschrittliche Fertigungsverfahren erreicht wird, ist ideal für komplexe Formen, bei denen herkömmliche Kanäle unwirksam wären.
- Gerade Kühlkanäle: Diese Kanäle sind einfache, gerade Bahnen, die in die Formplatten gebohrt werden. Sie sind zwar einfach und kostengünstig, aber bei komplexen Formgeometrien weniger effizient als die konforme Kühlung. Gerade Kanäle werden häufig in Standardformen verwendet, wo eine gleichmäßige Kühlung besser möglich ist.
- Baffle-Kühlung: Leitbleche sind flache Einsätze, die den Kühlmittelfluss innerhalb der Form umleiten, insbesondere in engen Bereichen, die von geraden Kanälen nicht erreicht werden können. Die Baffle-Kühlung ist effizient für das Temperaturmanagement in kleineren Formen oder bestimmten Bereichen, bietet aber möglicherweise nicht die gleichmäßige Kühlung, die für hochkomplexe Designs erforderlich ist.
- Bubbler-Kühlung: Bubbler sind Rohre, die das Kühlmittel in kleinen, begrenzten Bereichen der Form zirkulieren lassen. Sie sind besonders vorteilhaft für dicke Bereiche eines Teils, die eine schnellere Kühlung erfordern. Bubbler sind eine häufige Wahl, wenn herkömmliche Kanäle keine ausreichende Kühlung für dichte Bereiche bieten können.
- Kühlungsstifte: Kühlungsstifte werden in den Formkern eingesetzt, um die Kühlung dickerer Teile zu unterstützen. Diese Stifte sind ideal für die örtliche Kühlung in größeren Formen oder in bestimmten Bereichen, die zur Überhitzung neigen. Sie werden auch häufig in Werkzeugen mit mehreren Kavitäten verwendet, wo die Aufrechterhaltung gleichmäßiger Temperaturen eine Herausforderung darstellt.
Der Einfluss der Kühlkanalkonstruktion auf Zykluszeit und Qualität
Die Gestaltung der Kühlkanäle wirkt sich sowohl auf die Effizienz als auch auf die Qualität des Spritzgießprozesses aus:
- Reduzierung der Zykluszeit: Effiziente Kühlkanäle tragen zur Verkürzung der Zykluszeit bei, da die Teile schneller abkühlen und erstarren. Kürzere Zykluszeiten bedeuten eine höhere Produktionsleistung und niedrigere Herstellungskosten.
- Maßgenauigkeit: Die gleichmäßige Abkühlung über die gesamte Form hinweg verhindert Verformungen oder Schrumpfung und sorgt dafür, dass die Teile die vorgesehene Form und die Abmessungen beibehalten.
- Oberfläche: Die Kühlung kann die Oberflächenqualität von Gussteilen beeinflussen. Eine gleichmäßige Kühlung minimiert Spannungen, die andernfalls die Oberfläche des Teils beeinträchtigen könnten, was zu einer besseren Oberfläche führt.
Die korrekte Gestaltung der Kühlkanäle ist ein wesentlicher Faktor in der Phase der Werkzeugkonstruktion, da sie die Effizienz des Werkzeugs und die Qualität der geformten Teile bestimmt.
Fehler und Probleme beim Spritzgießen
Trotz der Präzision des Spritzgießens können verschiedene allgemeine Fehler auftreten. Diese Probleme zu verstehen und zu wissen, wie man sie vermeidet, ist für die Aufrechterhaltung der Qualität und die Minimierung von Ausschuss unerlässlich.
Häufige Fehler beim Spritzgießen
- Verziehen: Verzug ist eine Verformung, die auftritt, wenn verschiedene Teile der Form ungleichmäßig abkühlen. Dieser Fehler tritt häufig bei komplexen Formen mit unzureichenden Kühlkanälen oder unzureichender Kühlzeit auf. Um Verzug zu vermeiden, sollten die Kühlkanäle so gestaltet sein, dass eine gleichmäßige Abkühlung gewährleistet ist, und die Kühlzeit sollte sorgfältig überwacht werden.
- Sinkende Markierungen: Einfallstellen erscheinen als Vertiefungen auf der Oberfläche dickerer Abschnitte eines Teils, die in der Regel auf unsachgemäße Kühlung oder unzureichenden Nachdruck zurückzuführen sind. Die Verwendung eines optimalen Drucks und die Sicherstellung einer angemessenen Kühlung, insbesondere in dicken Bereichen, können dazu beitragen, Einfallstellen zu vermeiden.
- Blitzlicht: Flash tritt auf, wenn geschmolzener Kunststoff aufgrund eines zu hohen Einspritzdrucks oder einer falschen Ausrichtung aus der Kavität an der Trennebene austritt. Eine präzise Ausrichtung und die richtige Druckeinstellung sind entscheidend, um das Entweichen zu verhindern.
- Durchfluss-Linien: Fließlinien sind sichtbare Linien auf der Oberfläche eines Teils, die durch Schwankungen in der Abkühlgeschwindigkeit des Kunststoffs beim Fließen durch die Form verursacht werden. Die Anpassung von Einspritzgeschwindigkeit und Temperatur kann helfen, Fließlinien zu reduzieren.
- Kurze Schüsse: Kurze Schüsse entstehen, wenn der Formhohlraum nicht vollständig gefüllt ist, was häufig auf einen zu niedrigen Einspritzdruck oder zu wenig Material zurückzuführen ist. Eine Erhöhung des Einspritzdrucks oder die Sicherstellung einer ausreichenden Materialzufuhr kann dieses Problem beheben.
- Schweißnähte: Bindenähte entstehen dort, wo zwei Fließfronten aufeinandertreffen, was oft zu Schwachstellen im Teil führt. Eine Anpassung der Einspritzgeschwindigkeit oder die Verwendung eines Heißkanalsystems kann die Bildung von Bindenähten verringern.
- Sprödigkeit und Rissbildung: Diese Probleme sind in der Regel auf eine unsachgemäße Kühlung oder einen zu hohen Einspritzdruck zurückzuführen, der zu inneren Spannungen führt. Eine ordnungsgemäße Kühlung und eine optimale Druckregelung tragen dazu bei, Sprödigkeit und Rissbildung zu verringern.
Durch das Verständnis und die Kontrolle dieser Faktoren - wie Einspritzgeschwindigkeit, Temperatur und Kühlung - können die Hersteller Fehler reduzieren und die Gesamtqualität der Gussteile verbessern.
Herstellungsprozess von Spritzgussformen
Die Herstellung einer Spritzgussform umfasst mehrere Schritte, von denen jeder einzelne für die Haltbarkeit, Präzision und Funktionalität der Form entscheidend ist. Im Folgenden finden Sie eine Aufschlüsselung der typischen Schritte bei der Herstellung einer Kunststoff-Spritzgussform:

- Design und Technik: Die Phase der Werkzeugkonstruktion ist von entscheidender Bedeutung, da sie die Grundlage für alle nachfolgenden Schritte bildet. Mithilfe von CAD-Software erstellen die Ingenieure ein 3D-Modell der Form, das alle notwendigen Details enthält, einschließlich der Form des Hohlraums, der Kühlkanäle, des Auswerfersystems und der Trennlinie. Dieses Modell wird dann Simulationen unterzogen, um Probleme vorherzusagen und die Leistung zu optimieren, bevor die physische Formherstellung beginnt.
- Auswahl des Materials: Je nach Produktionsvolumen und Anforderungen an die Teile werden die Materialien nach Haltbarkeit und Verschleißfestigkeit ausgewählt. Gängige Materialien sind gehärteter Stahl für Großserienformen und Aluminium für Anwendungen mit geringeren Stückzahlen. Stahlformen werden aufgrund ihrer Langlebigkeit für hohe Stückzahlen bevorzugt, während Aluminiumformen einfacher zu bearbeiten und für die Produktion von Kleinserien kostengünstiger sind.
- CNC-Bearbeitung und EDM (Electrical Discharge Machining): Die CNC-Bearbeitung (Computer Numerical Control) wird eingesetzt, um die Grundform der Form mit hoher Präzision auszufräsen. Mit Hilfe der Funkenerosion werden dann komplexe Geometrien, feine Details und komplizierte Formen im Formhohlraum hergestellt, die mit CNC-Maschinen nicht möglich sind. Die Kombination von CNC- und EDM-Maschinen gewährleistet sowohl die für die Form erforderliche Genauigkeit als auch die Komplexität.
- Wärmebehandlung und Oberflächenhärtung: Stahlformen werden häufig wärmebehandelt, um die Härte und Haltbarkeit zu erhöhen. Oberflächenbehandlungen wie Nitrieren oder Verchromen werden ebenfalls durchgeführt, um die Verschleißfestigkeit zu erhöhen, die Korrosion zu verringern und die Lebensdauer der Formen zu verlängern. Aluminiumformen sind zwar weicher, können aber auch anodisiert werden, um die Oberflächenhärte zu verbessern.
- Montage und Polieren: Nach der Bearbeitung werden die Formteile zusammengebaut, einschließlich der Montage von Kavität, Kern, Auswerferstiften, Schiebern und Kühlkanälen. Anschließend wird eine Präzisionspolitur durchgeführt, um eine hochwertige Oberflächenbeschaffenheit zu erzielen, insbesondere bei Teilen, die eine ästhetische oder glatte Oberfläche erfordern.
- Prüfung und Validierung: Vor der vollen Produktion wird die Form einem Probelauf unterzogen, um sicherzustellen, dass sie den Spezifikationen entspricht. In diesem Schritt, der als T1-Probeentnahme bezeichnet wird, wird die Leistung der Form getestet, um mögliche Probleme mit der Kühlung, dem Auswerfen oder der Ausrichtung zu erkennen. Eventuelle Anpassungen werden vorgenommen, um die Leistung der Form für die Massenproduktion zu optimieren.
- Qualitätssicherung und Zulassung: Nach der Validierung wird die Form geprüft, um sicherzustellen, dass sie alle Qualitätsstandards erfüllt. Es werden Messungen vorgenommen, um die Maßhaltigkeit zu überprüfen, und gegebenenfalls werden Anpassungen vorgenommen. Erst nach bestandener Qualitätsprüfung wird die Form für die Produktion freigegeben.
Jeder Schritt im Formherstellungsprozess ist von entscheidender Bedeutung, um sicherzustellen, dass die endgültige Form in einer hochvolumigen Produktionsumgebung konsistent und effizient funktioniert.
Auswahl der richtigen Spritzgussform für Ihre Anwendung
Die Auswahl der richtigen Spritzgussform ist entscheidend für die Optimierung der Produktion, die Minimierung der Kosten und die Gewährleistung der Produktqualität. Hier sind einige Schlüsselfaktoren, die bei der Auswahl einer Spritzgussform zu berücksichtigen sind:
- Produktionsvolumen: Das erwartete Produktionsvolumen spielt bei der Auswahl der Form eine wichtige Rolle. Für die Großserienproduktion sind in der Regel langlebige Formen aus gehärtetem Stahl erforderlich, während Aluminiumformen für Kleinserien oder die Herstellung von Prototypen geeignet sind.
- Teil Komplexität und Design: Komplexe Teile mit komplizierten Geometrien, Hinterschneidungen oder dünnen Wänden können spezielle Formmerkmale wie Heber, Schieber oder Multikavitätenkonfigurationen erfordern. Je komplexer das Teil ist, desto detaillierter muss die Form sein, was sich sowohl auf die Kosten als auch auf die Produktionszeit auswirken kann.
- Wahl des Materials: Verschiedene Kunststoffe haben einzigartige Fließ-, Schrumpf- und Kühleigenschaften. Formen, die für starre Materialien wie Polycarbonat konzipiert sind, erfordern möglicherweise andere Kühlkonfigurationen oder Formmaterialien als Formen für flexible Kunststoffe wie Polyethylen.
- Anforderungen an die Zykluszeit: Schnelle Zykluszeiten sind für die Großserienproduktion unerlässlich. Eine gut konzipierte Form mit effizienten Kühlkanälen und einem optimalen Auswerfersystem kann die Zykluszeit verkürzen, den Durchsatz erhöhen und die Kosten senken.
- Kostenüberlegungen: Formen sind eine langfristige Investition, und die Kosten können je nach Material, Komplexität und Formtyp erheblich variieren. Mehrkavitäten- oder Heißkanalwerkzeuge können zwar anfangs teurer sein, bieten aber auf lange Sicht Kosteneinsparungen durch höhere Effizienz und weniger Abfall.
- Langlebigkeit der Form: Bei hohen Stückzahlen oder kontinuierlicher Produktion müssen die Formen für eine lange Lebensdauer mit haltbaren Materialien und Oberflächenbehandlungen ausgelegt sein. Merkmale wie Härtung und Beschichtung tragen dazu bei, dass die Form wiederholtem Gebrauch ohne Abnutzung oder Verschlechterung standhält.
Durch die sorgfältige Bewertung dieser Faktoren können Hersteller die richtige Form auswählen, um ihre Produktionsziele zu erreichen, die Qualität der Teile zu erhalten und die Kosteneffizienz zu maximieren.
Schlussfolgerung
Kunststoff-Spritzgießen ist ein Eckpfeiler der modernen Fertigung und ermöglicht die Herstellung präziser, hochwertiger Kunststoffteile zu niedrigen Kosten und mit hoher Geschwindigkeit. Das Verständnis der verschiedenen Aspekte von Spritzgießwerkzeugen - von den Komponenten, Typen und dem Herstellungsverfahren bis hin zum Kühlungsdesign und möglichen Problemen - bietet wertvolle Einblicke in die Optimierung der Produktion.
Die Wahl der richtigen Form, die Implementierung effektiver Kühlkanäle und eine strenge Qualitätskontrolle können die Effizienz und Qualität des Kunststoffspritzgießens erheblich verbessern. Dadurch werden nicht nur die Anforderungen der Großserienproduktion erfüllt, sondern es wird auch sichergestellt, dass die gegossenen Teile den erforderlichen Spezifikationen und ästhetischen Standards entsprechen. Mit den Fortschritten bei den Materialien, der Werkzeugkonstruktion und den Kühltechnologien entwickelt sich das Kunststoffspritzgießen ständig weiter und bietet noch mehr Möglichkeiten.