Hva er plastinjeksjonsform
Hva er sprøytestøping av plast?
Sprøytestøping av plast er en av de mest effektive metodene for produksjon av plastkomponenter, og gir høy presisjon og produksjonseffektivitet. Prosessen går ut på å smelte plastmaterialer og sprøyte dem inn i en forhåndsdesignet form som former plasten til en bestemt form når den avkjøles. Denne artikkelen tar for seg det viktigste ved sprøytestøpeformer for plast, og beskriver typer, komponenter, produksjonsprosesser og hva man må ta hensyn til når man skal velge riktig form for å oppfylle spesifikke produksjonsbehov.
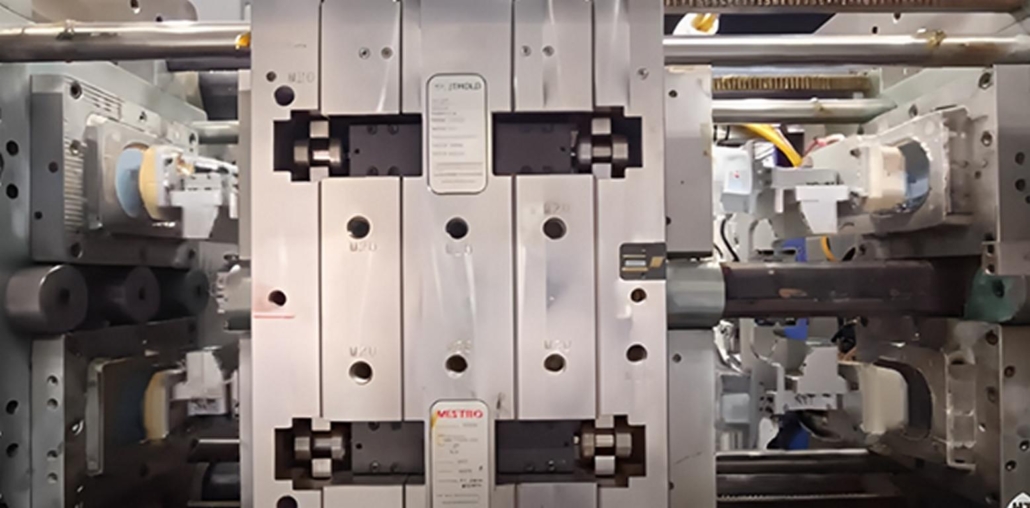
Introduksjon til sprøytestøping av plast
Sprøytestøping av plast er en teknikk som brukes til å lage intrikate, presise plastdeler i store mengder. Siden den ble utviklet på slutten av 1800-tallet, har prosessen forandret produksjonsindustrien og gjort det mulig å produsere deler i høy hastighet i en lang rekke sektorer, inkludert bilindustrien, elektronikk, medisinsk utstyr og forbruksvarer.
Fordeler med sprøytestøping av plast
- Høy effektivitet og hastighet: Sprøytestøping gir en kort produksjonssyklus, noe som muliggjør raske produksjonshastigheter. Flere former kan kjøres samtidig for å øke produksjonen ytterligere.
- Repeterbarhet: Prosessen er utviklet for å skape identiske deler over flere produksjonsserier, noe som er spesielt verdifullt i bransjer som krever høy presisjon og konsistens.
- Komplekse designfunksjoner: Sprøytestøpeformer er i stand til å skape intrikate geometrier, inkludert tynne vegger, underskjæringer og komplekse overflatedetaljer.
- Fleksibilitet i materialet: Sprøytestøping kan bruke et bredt utvalg av termoplaster og herdeplaster, hver og en valgt for å gi spesifikke egenskaper til det ferdige produktet.
- Minimalt med avfall: Med riktig utformede støpeformer og avansert prosesskontroll produserer sprøytestøping lite eller ingen materialavfall.
Oversikt over sprøytestøpeformer av plast
A sprøytestøpeform for plast er et komplekst verktøy som er utformet for å forme smeltet plastmateriale til et ferdig produkt. Formen er vanligvis laget av stål eller aluminium og består av to primære halvdeler: hulrommet og kjernen, som hver har ansvar for å forme utsiden og innsiden av den endelige delen. På grunn av det høye trykket som er involvert i sprøytestøping, må disse formene være robuste, motstandsdyktige mot slitasje og i stand til å opprettholde formen under gjentatte sykluser.
Hver form består av flere deler som jobber sammen for å sikre presisjon i formingen, kjølingen og utstøtingen av delen. Nedenfor følger en oversikt over de viktigste komponentene i en sprøytestøpeform og deres respektive funksjoner.
Viktige formkomponenter
- Hulrom og kjerne i sprøytestøpeformen: Dette er de primære elementene i formen. Kavitetssiden (vanligvis "A"-siden) er ansvarlig for å forme den utvendige overflaten av delen, mens kjernesiden (B-siden) former det innvendige. Sammen danner de det hule rommet som definerer delens geometri. Valget av hulrom- og kjernematerialer avhenger av produksjonsvolumet, ettersom slitesterke materialer som herdet stål ofte brukes til høyvolumproduksjon, mens mykere metaller kan være tilstrekkelig for mindre serier.
- Glidebrytere og løftere: Glidebrytere og løftere gjør det mulig å lage underskjæringer eller komplekse geometrier som ikke kan formes med en enkel todelt form. Glidebryterne beveger seg sideveis når formen åpnes, slik at det blir plass til eventuelle fremspring eller spor, mens løfterne beveger seg ut i en vinkel for å frigjøre delen. Begge deler bidrar til at deler med komplekse former kan støpes ut uten å bli skadet.
- Systemer for gran, løper og port: The gran kanaliserer smeltet plast fra sprøytemaskinens dyse inn i formen og fører den til løper system som styrer plasten til hvert hulrom i en flerkavitetsform. Portene er de siste inngangspunktene for den smeltede plasten inn i hulrommet, der den avkjøles og tar form. Hver komponent i dette systemet påvirker hvor jevnt og raskt materialet fyller formen, noe som igjen påvirker kvaliteten og syklustiden.
- Ejektorsystem: Etter at den støpte delen er avkjølt og størknet, kan ejektorsystem skyver delen ut av formhulen. Utstøtersystemet inkluderer ofte pinner eller plater som påfører kraft på delen fra kjernesiden, slik at den frigjøres uten skade. Dette systemet må være nøyaktig tidsinnstilt og kontrollert for å forhindre at delen deformeres eller kleber seg fast.
- Kjølekanaler: Kjølekanaler er passasjer i formplatene som fører kjølevæske, vanligvis vann, for å absorbere og spre varmen fra den smeltede plasten. Effektiv kjøling er avgjørende for støpeprosessen, ettersom det reduserer syklustiden og påvirker detaljens dimensjonsnøyaktighet og mekaniske egenskaper. Utformingen av kjølekanalene - enten det er konforme kanaler, baffler eller boblekanaler - kan ha stor innvirkning på formens ytelse og effektivitet.
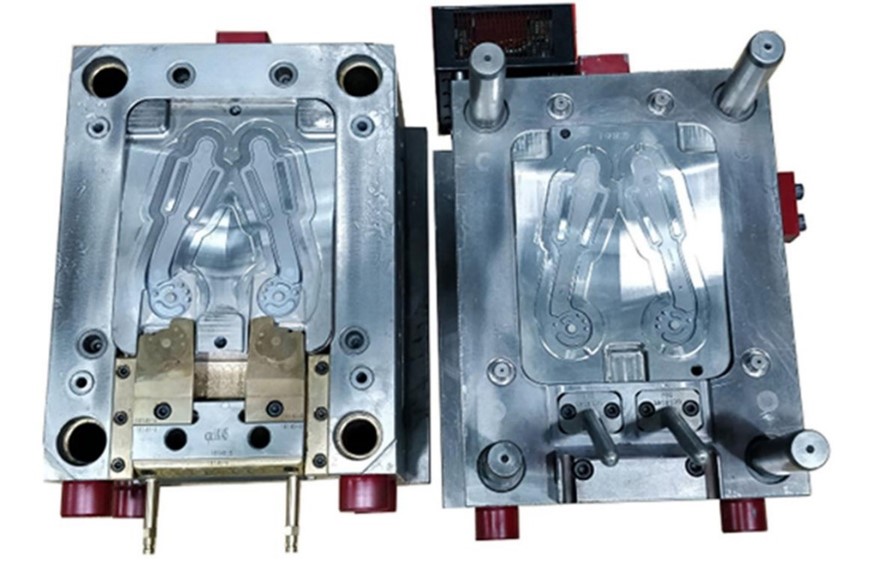
Strukturen til en sprøytestøpeform av plast
Strukturen i en plastsprøytestøpeform er konstruert for å tåle trykk, temperaturer og mekaniske påkjenninger i gjentatte støpesykluser. Her ser vi nærmere på de strukturelle komponentene og hvordan de fungerer i støpeprosessen:
- A- og B-plater: Dette er formens hovedplater som holder henholdsvis hulrommet og kjernen. A-platen er stasjonær, mens B-platen beveger seg for å åpne og lukke formen. Disse platene er konstruert for å opprettholde justeringen og motstå trykket ved injeksjon.
- Klemmeplater: Disse platene fester formen i klemmeenheten til sprøytestøpemaskinen. Utformingen må sikre stabilitet under høytrykksinjeksjonsfasen for å forhindre feiljustering eller bevegelse som kan forårsake defekter.
- Avskjedslinje: Skillelinjen er der A- og B-platene møtes. En godt justert skillelinje er avgjørende for å forhindre defekter som flash (tynne lag med plast i formens sømmer) og sikre jevn frigjøring av delen. Avskjæringslinjens plassering avhenger ofte av detaljens design og kravene til formen.
- Kjølekanaler: Kjølekanaler er avgjørende for å opprettholde formens ytelse og redusere syklustidene. Kanalene er nøye utformet for å sikre jevn kjøling over hele formhulen og kjernen, noe som er avgjørende for å forhindre defekter som skjevhet eller indre spenninger. Typer kjølekanaler inkluderer:
- Konform kjøling: Kanaler som følger konturen til delen, noe som gir jevn kjøling som samsvarer med formen på formhulrommet.
- Baffelkjøling: Bruker innsatser for å styre kjølevæskestrømmen og brukes vanligvis når formstørrelsen begrenser kanalplasseringen.
- Bubbler kjøling: Bubblerør skaper ekstra kjøling i bestemte områder, spesielt for tykke seksjoner som krever raskere kjøling.
- Kjølestifter: Stifter innebygd i kjernen gir lokal kjøling i tykke seksjoner, noe som bidrar til å styre temperaturfordelingen i større former eller former med flere hulrom.
Kjøleutformingen har stor innvirkning på syklustiden og dermed også på kostnadene og produktiviteten i sprøytestøpeprosessen.
Typer sprøytestøpeformer av plast
Det finnes flere typer plastsprøytestøpeformer som passer til ulike produksjonsbehov, kompleksitet og krav til delene. Her er noen av de mest brukte typene:
- Støpeformer med én kavitet: Disse formene produserer én del per syklus. De brukes ofte til mindre produksjonsvolumer eller deler med høy presisjon, der det er nødvendig med tettere kontroll over hver enkelt del. Former med én kavitet har fordelen av enklere oppsett og er mer kostnadseffektive for begrenset produksjon.
- Støpeformer med flere hulrom: I flerkavitetsformer kan flere identiske kaviteter brukes til å produsere flere deler i én enkelt syklus. Dette øker effektiviteten og er ideelt for høyvolumproduksjon, noe som reduserer syklustiden per del og de totale kostnadene. Det er imidlertid mer komplisert å konstruere formene med flere kaviteter, og de krever presis balanse i løpesystemet for å sikre jevn fylling.
- Familieformer: Familieformer inneholder ulike hulrom i en og samme form, noe som gjør det mulig å produsere ulike komponenter i én syklus. Dette er spesielt nyttig når ulike deler skal støpes sammen, for eksempel i sammenstillinger. Det kan imidlertid være utfordrende å balansere fyllingsgraden for deler av ulik størrelse, og det kan føre til defekter hvis det ikke håndteres nøye.
- Varmkanals- kontra kaldkanalsformer:
- Støpeformer for varme løpere: Bruk oppvarmede komponenter for å holde plasten smeltet i kanalsystemet, noe som minimerer avfall og gjør syklusen raskere. Varmløpere er effektive for produksjon av store volumer, men krever nøye kontroll og høyere startkostnader.
- Støpeformer for kalde løpere: La plasten i løperen kjøle seg ned og stivne for hver syklus. Den størknede løperen kastes vanligvis ut sammen med delen, som kan kreve sekundær behandling for å fjernes. Kaldkanalformer er enklere og rimeligere, noe som gjør dem egnet for produksjon av mindre volumer.
- To-plate vs. tre-plate støpeformer:
- Støpeformer med to plater: Disse består av en enkelt skillelinje og er enklere i design. De brukes vanligvis til enkle deler med krav om én enkelt port.
- Støpeformer med tre plater: Inkluder en ekstra plate som skaper to skillelinjer. Dette gir mulighet for mer komplekse grensesystemer, for eksempel sentral grinding, noe som forbedrer emnets estetikk og kan redusere bearbeidingen etter støpingen.
- Stabel- og rotasjonsformer:
- Stabelformer: Stabelformer bruker flere nivåer av hulrom, noe som effektivt dobler eller tredobler produksjonskapasiteten uten å øke maskinens krav til klemmekraft. De er fordelaktige for produksjon av svært store volumer, men krever avanserte maskiner og håndtering.
- Roterende støpeformer: Roterende støpeformer gir mulighet for overstøping og montering i støpeformen ved å rotere hulrom mellom stasjonene. De brukes ofte til deler i flere materialer, for eksempel deler som krever en kombinasjon av stiv og fleksibel plast.
Hver type støpeform har sine egne fordeler og utfordringer, og valget av riktig støpeform avhenger av faktorer som produksjonsvolum, emnets kompleksitet og materialkrav.

Prosess for sprøytestøping av plast
Sprøytestøpingsprosessen består av flere viktige trinn, som hver for seg er avgjørende for å produsere deler av høy kvalitet. Her er en detaljert oversikt:
- Klemming: Formen klemmes fast for å forberede injeksjon av smeltet plast. Klemmekraften beregnes ut fra trykket i hulrommet for å sikre at det ikke lekker plast gjennom skillelinjen.
- Injeksjon: Smeltet plast sprøytes inn i formhulrommet gjennom granen, løperen og porten. Injeksjonshastighet, trykk og temperatur må kontrolleres nøyaktig, ettersom de påvirker materialets flyt og kvalitet i hulrommet.
- Kjøling: Avkjølingen begynner så snart plasten kommer inn i formen. Avkjølingshastigheten må være jevn for å unngå defekter, som for eksempel vridning eller krymping. Kjølekanaler spiller en viktig rolle her ved å sørge for at varmen ledes effektivt ut av formen. Denne fasen står ofte for den største delen av syklustiden.
- Utstøting: Når delen har størknet, skyver utstøtingspinner eller -plater delen ut av formen. Utstøtingen må gjøres forsiktig for å unngå å skade delen, spesielt hvis den har komplekse funksjoner eller er laget av sprøtt materiale.
Hvert trinn i sprøytestøpeprosessen krever nøyaktig kontroll for å produsere deler som oppfyller kvalitetsstandardene, samtidig som syklustiden og produksjonskostnadene minimeres.
Kjølekanaler for sprøytestøpeformer
Kjølekanaler er avgjørende i sprøytestøpeprosessen for plast, ettersom de har stor innvirkning på syklustid, delkvalitet og produksjonseffektivitet. Riktig kjølekonstruksjon er avgjørende for å unngå defekter som vridning, krymping eller indre spenninger som kan oppstå hvis kjølingen er ujevn eller for rask.
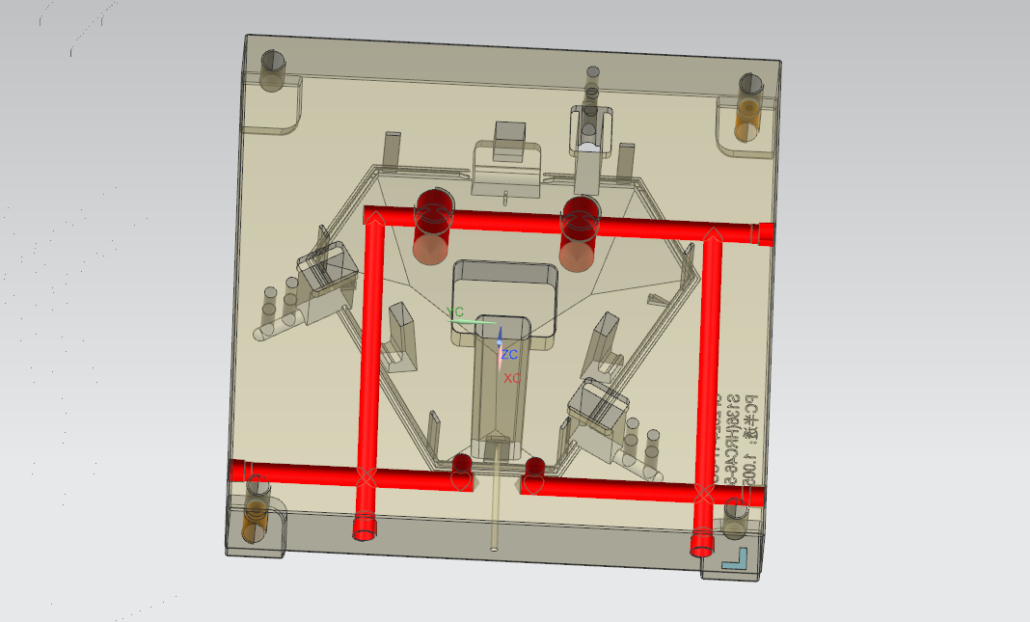
Typer kjølekanaler i sprøytestøpeformer
- Konform kjøling: Denne avanserte teknikken innebærer at kjølekanalene følger konturen til emnet i støpeformen. Konform kjøling gir jevn kjøling over hele emnets overflate, noe som reduserer syklustiden og forbedrer emnets kvalitet. Konform kjøling oppnås vanligvis ved hjelp av 3D-utskrift og andre avanserte produksjonsmetoder, og er ideell for komplekse former der tradisjonelle kanaler ville vært ineffektive.
- Rette kjølekanaler: Disse kanalene er enkle, rette baner som bores inn i formplatene. Selv om de er enkle og kostnadseffektive, er de mindre effektive enn konform kjøling i komplekse formgeometrier. Rette kanaler brukes ofte i standardformer der jevn kjøling er mer oppnåelig.
- Baffelkjøling: Baffler er flate innsatser som omdirigerer kjølevæskestrømmen i formen, spesielt på trange steder der rette kanaler ikke når frem. Baffelkjøling er effektivt for å styre temperaturen i mindre former eller spesifikke områder, men gir kanskje ikke den jevne kjølingen som er nødvendig for svært komplekse konstruksjoner.
- Bubbler kjøling: Bubblere er rør som sirkulerer kjølevæske i små, avgrensede områder av formen, noe som er spesielt gunstig for tykke deler av en del som krever raskere kjøling. Bubblere er et vanlig valg når tradisjonelle kanaler ikke kan gi tilstrekkelig kjøling for tette områder.
- Kjølestifter: Kjølepinner settes inn i formkjernen for å hjelpe til med å kjøle ned tykkere deler. Disse pinnene er ideelle for lokal kjøling i større støpeformer eller spesifikke områder som er utsatt for overoppheting. De brukes også ofte i former med flere hulrom, der det er utfordrende å opprettholde konsistente temperaturer.
Effekten av kjølekanalens utforming på syklustid og kvalitet
Utformingen av kjølekanalene påvirker både effektiviteten og kvaliteten på sprøytestøpeprosessen:
- Reduksjon av syklustid: Effektive kjølekanaler bidrar til å forkorte syklustiden, ettersom delene avkjøles og stivner raskere. Kortere syklustider betyr høyere produksjonskapasitet og lavere produksjonskostnader.
- Dimensjonell nøyaktighet: Konsekvent avkjøling over hele formen bidrar til å forhindre vridning eller krymping, noe som sikrer at delene beholder sin tiltenkte form og dimensjoner.
- Overflatebehandling: Kjøling kan påvirke overflatekvaliteten på støpte deler. Jevn kjøling minimerer spenninger som ellers kan ødelegge overflaten, noe som resulterer i en bedre finish.
Riktig utforming av kjølekanalen er en viktig faktor i designfasen av støpeformen, ettersom den er avgjørende for formens effektivitet og kvaliteten på de støpte delene.
Defekter og problemer med sprøytestøping
Til tross for presisjonen ved sprøytestøping kan det oppstå flere vanlige feil. Det er viktig å forstå disse problemene og hvordan man kan redusere dem for å opprettholde kvaliteten og minimere sløsing.
Vanlige defekter ved sprøytestøping
- Vridning: Forvrengning er en deformasjon som oppstår når ulike deler av formen avkjøles i ujevn hastighet. Denne feilen oppstår ofte i komplekse støpeformer med utilstrekkelige kjølekanaler eller utilstrekkelig kjøletid. For å forhindre vridning bør kjølekanalene utformes for å sikre jevn avkjøling, og avkjølingstiden bør overvåkes nøye.
- Vaskemerker: Synkemerker vises som fordypninger på overflaten av tykkere deler av en del, vanligvis på grunn av feil avkjøling eller utilstrekkelig holdetrykk. Bruk av optimalt trykk og tilstrekkelig kjøling, spesielt i tykke områder, kan bidra til å forhindre synkemerker.
- Flash: Flash oppstår når smeltet plast slipper ut av hulrommet ved skillelinjen på grunn av for høyt injeksjonstrykk eller feil innretting. Nøyaktig justering og riktige trykkinnstillinger er avgjørende for å forhindre flash.
- Strømningslinjer: Flytlinjer er synlige linjer på overflaten av en del som skyldes variasjoner i plastens avkjølingshastighet når den flyter gjennom formen. Justering av innsprøytningshastighet og temperatur kan bidra til å redusere flytelinjer.
- Korte skudd: Korte skudd skjer når formhulen ikke er helt fylt, ofte på grunn av lavt injeksjonstrykk eller utilstrekkelig materiale. Dette problemet kan løses ved å øke injeksjonstrykket eller sørge for tilstrekkelig tilførsel av materiale.
- Sveiselinjer: Sveiselinjer oppstår der to strømningsfronter møtes, noe som ofte skaper svake punkter i delen. Ved å justere innsprøytningshastigheten eller bruke et varmkanalsystem kan man redusere sveiselinjene.
- Skjørhet og sprekkdannelser: Disse problemene skyldes vanligvis feil kjøling eller for høyt innsprøytningstrykk, noe som fører til indre spenninger. Riktig kjøling og optimal trykkregulering bidrar til å redusere sprøhet og sprekkdannelser.
Ved å forstå og kontrollere disse faktorene - for eksempel innsprøytningshastighet, temperatur og kjøleutforming - kan produsentene redusere antall feil og forbedre den generelle kvaliteten på de støpte delene.
Produksjonsprosessen for sprøytestøpeformer
Produksjonen av en sprøytestøpeform består av flere trinn, som hver for seg er avgjørende for å sikre formens holdbarhet, presisjon og funksjonalitet. Her er en oversikt over de typiske trinnene i produksjonen av en sprøytestøpeform i plast:

- Design og prosjektering: Formdesignfasen er avgjørende, ettersom den legger grunnlaget for alle påfølgende trinn. Ved hjelp av CAD-programvare lager ingeniørene en 3D-modell av formen, med alle nødvendige detaljer, inkludert hulromsform, kjølekanaler, utstøtingssystem og skillelinje. Denne modellen gjennomgår deretter simuleringer for å forutsi problemer og optimalisere ytelsen før den fysiske produksjonen av støpeformen begynner.
- Valg av materiale: Avhengig av produksjonsvolum og krav til delene velges materialer med tanke på holdbarhet og slitestyrke. Vanlige materialer er herdet stål til støpeformer for store volumer og aluminium til mindre volumer. Stålformer foretrekkes for lange serier på grunn av deres holdbarhet, mens aluminiumsformer er enklere å bearbeide og mer kostnadseffektive for korttidsproduksjon.
- CNC-maskinering og EDM (elektrisk utladningsbearbeiding): CNC-maskinering (Computer Numerical Control) brukes til å skjære ut formens primære form med høy presisjon. EDM brukes deretter til å skape komplekse geometrier, fine detaljer og intrikate former i formhulen som CNC-maskiner ikke kan oppnå. Kombinasjonen av CNC og EDM sikrer både nøyaktigheten og kompleksiteten som kreves for formen.
- Varmebehandling og overflateherding: Stålformer varmebehandles ofte for å øke hardheten og holdbarheten. Overflatebehandlinger, som nitrering eller forkromming, brukes også for å forbedre slitestyrken, redusere korrosjon og forlenge formens levetid. Aluminiumsformer er mykere, men kan også anodiseres for å forbedre overflatehårdheten.
- Montering og polering: Etter maskinering settes formkomponentene sammen, inkludert montering av hulrom, kjerne, utkasterpinner, glidere og kjølekanaler. Deretter utføres presisjonspolering for å oppnå en overflatefinish av høy kvalitet, spesielt for deler som krever en estetisk eller glatt overflate.
- Testing og validering: Før full produksjon gjennomgår formen en prøvekjøring for å sikre at den oppfyller spesifikasjonene. Dette trinnet, kjent som T1-prøvetaking, tester formens ytelse og identifiserer potensielle problemer med kjøling, utstøting eller justering. Eventuelle justeringer gjøres for å optimalisere formens ytelse for masseproduksjon.
- Kvalitetssikring og godkjenning: Etter validering inspiseres formen for å bekrefte at den oppfyller alle kvalitetsstandarder. Det foretas målinger for å verifisere dimensjonsnøyaktigheten, og justeringer gjøres om nødvendig. Først etter bestått kvalitetskontroll godkjennes formen for full produksjon.
Hvert trinn i produksjonsprosessen er avgjørende for å sikre at den endelige formen fungerer konsekvent og effektivt i høyvolumproduksjonsmiljøer.
Velge riktig sprøytestøpeform for ditt bruksområde
Valg av riktig sprøytestøpeform er avgjørende for å optimalisere produksjonen, minimere kostnadene og sikre produktkvaliteten. Her er noen viktige faktorer du bør ta hensyn til når du velger sprøytestøpeform:
- Produksjonsvolum: Det forventede produksjonsvolumet spiller en viktig rolle ved valg av støpeform. Høyvolumproduksjon krever vanligvis holdbare former laget av herdet stål, mens aluminiumsformer er egnet for korte serier eller prototyping.
- Delkompleksitet og design: Komplekse deler med intrikate geometrier, underskjæringer eller tynne vegger kan kreve spesialiserte formfunksjoner som løftere, glidere eller konfigurasjoner med flere hulrom. Jo mer kompleks delen er, desto mer detaljert må formen være, noe som kan påvirke både kostnader og produksjonstid.
- Valg av materiale: Ulike plastmaterialer har unike egenskaper når det gjelder flyt, krymping og kjøling. Former som er konstruert for stive materialer som polykarbonat, kan kreve andre kjølekonfigurasjoner eller formmaterialer enn former som er konstruert for fleksible plastmaterialer som polyetylen.
- Krav til syklustid: Rask syklustid er avgjørende for høyvolumproduksjon. En godt utformet form med effektive kjølekanaler og et optimalt utstøtingssystem kan redusere syklustiden, øke gjennomstrømningen og redusere kostnadene.
- Kostnadsoverveielser: Støpeformer er en langsiktig investering, og kostnadene kan variere betydelig avhengig av materiale, kompleksitet og formtype. Selv om flerkavitets- eller varmkanalformer kan være dyrere i utgangspunktet, kan de gi kostnadsbesparelser på lang sikt ved å øke effektiviteten og redusere avfallet.
- Lang levetid for mugg: For høyvolum- eller kontinuerlig produksjon må formene være utformet for lang levetid med holdbare materialer og overflatebehandlinger. Funksjoner som herding og belegg bidrar til å sikre at formen tåler gjentatt bruk uten slitasje eller nedbrytning.
Ved å vurdere disse faktorene nøye kan produsentene velge riktig støpeform for å nå produksjonsmålene, opprettholde kvaliteten på delene og maksimere kostnadseffektiviteten.
Konklusjon
Sprøytestøping av plast er en hjørnestein i moderne produksjon, og gjør det mulig å produsere presise plastdeler av høy kvalitet til en lav kostnad og i høy hastighet. Å forstå de ulike aspektene ved sprøytestøpeformer - fra komponenter, typer og produksjonsprosess til kjøleutforming og potensielle problemer - gir verdifull innsikt i hvordan produksjonen kan optimaliseres.
Ved å velge riktig støpeform, implementere effektive kjølekanaler og opprettholde streng kvalitetskontroll kan effektiviteten og kvaliteten på sprøytestøping av plast forbedres betraktelig. Dette oppfyller ikke bare kravene til høyvolumproduksjon, men sikrer også at de støpte delene oppfyller de nødvendige spesifikasjonene og estetiske standardene. Med fremskritt innen materialer, formdesign og kjøleteknologi fortsetter sprøytestøping av plast å utvikle seg, noe som gir enda flere muligheter
Legg igjen et svar
Vil du delta i diskusjonen?Du er velkommen til å bidra!