I dag har Kina befestet sin posisjon som en global leder innen sprøytestøping og er blitt en verdifull produksjonsløsning for bedrifter av alle størrelser i hele verden, til konkurransedyktige priser. Takket være det store antallet sprøytestøpefirmaer har Kina spesialisert seg på produksjon av plastkomponenter til hele spekteret av bransjer, fra bilindustri, elektronikk, helsevesen og emballasje til forbruksvarer. De gjør det tunge løftet med avansert teknologi, presisjonsteknikk og automatisering som brukes til å lage støpte deler med uslåelig nøyaktighet og effektivitet. Flere viktige fordeler bygger den kinesiske sprøytestøpeindustrien som bedrifter har en tendens til å velge. En av de største drivkreftene når det gjelder kostnadseffektiv produksjon, er at arbeids- og produksjonskostnadene er billigere i Kina enn i vestlige land. Dessuten er kinesiske støpeselskaper i økende grad utstyrt med høyeffektive, toppmoderne maskiner og robotsystemer, noe som muliggjør effektiv produksjon av store volumer samtidig som kvaliteten opprettholdes. Selskapet har internasjonalt anerkjente sertifiseringer som ISO 9001, ISO 13485 (medisinsk utstyr) og IATF 16949 (bilkomponenter) for å overholde de globale bransjestandardene for kvalitet.
Kinesiske sprøytestøpeselskaper har også styrken til tilpasning og innovasjon. Produsenter i Kina har den tekniske evnen så vel som ekspertisen til å tilby tilpassede former for en kundes multikavitetsformer, overmolding, innsatsstøping og kompliserte design. For bedrifter som er ute etter hastighet og pålitelighet, er deres evne til å gi rask behandlingstid og produksjon i stor skala et foretrukket valg.
Hva er sprøytestøping?
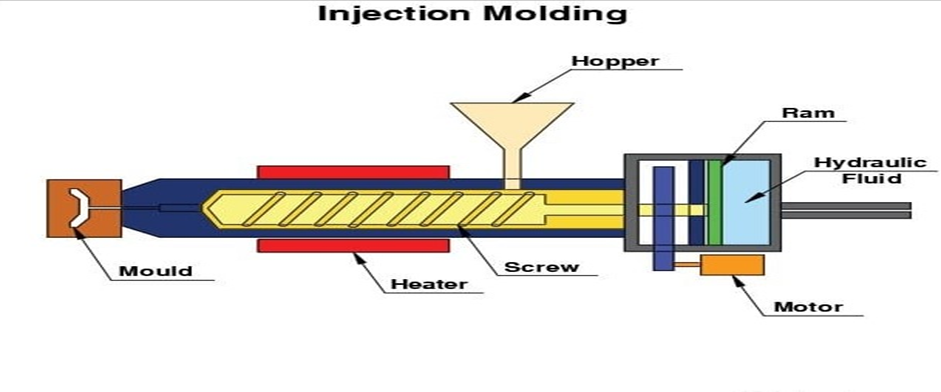
Dette er en prosess for produksjon av plastdeler ved injeksjon av smeltet materiale i en form. Det er mye brukt i for eksempel bilindustrien, medisin, elektronikk, plastemballasje og husholdningsvarer. Denne prosessen tar komplekse deler inn i masseproduksjon med høy presisjon og konsistens.
Hvorfor bruke et kinesisk sprøytestøpeselskap?
For det første har Kina blitt et viktig knutepunkt for sprøytestøping av en rekke årsaker:
1. Kostnadseffektiv produksjon
Prisene er en av de viktigste grunnene til at bedrifter velger kinesiske støpeselskaper. Fordi arbeids- og driftskostnadene i Kina er lavere enn i vestlige land, er det mulig å produsere støpte komponenter av høy kvalitet til en brøkdel av kostnaden.
2. Avansert produksjonsteknologi
I moderne kinesiske sprøytestøpefirmaer investeres det tungt i automatisering og toppmoderne maskiner. Mange bedrifter bruker robotsystemer, datastøttet design (CAD) og systemer for kvalitetskontroll i sanntid for å sikre presisjon og høyest mulig produktivitet.
3. Standarder av høy kvalitet
De fleste anerkjente kinesiske støpefirmaer følger internasjonale kvalitetsstandarder som ISO 9001, ISO 13485 (for medisinsk utstyr) og IATF 16949 (bildeler). Disse sertifiseringene garanterer at produktet oppfyller kravene til høy kvalitet.
4. Tilpasning og innovasjon
Tilpassede løsninger som passer til forskjellige forretningsbehov, tilbys av mange kinesiske støpeselskaper. Kinesiske produsenter har et svar på alle kundens behov, fra overstøping og innsatsstøping til kundens behov for komplekse modeller med flere hulrom.
5. Rask behandlingstid
Kinesiske støpeselskaper kan produsere i store volumer mer effektivt og raskere enn de fleste konkurrenter på grunn av effektive forsyningskjeder og strømlinjeformede produksjonsprosesser. Virksomheter som er avhengige av å få produktene raskt ut på markedet, vil trenge støtte fra denne hurtigheten.
6. Erfaring og ekspertise
Det finnes tusenvis av spesialiserte selskaper i Kinas sprøytestøpeindustri som har lang erfaring på alle disse områdene. De regnes som det foretrukne valget for globale virksomheter innen formdesign og materialvalg samt presisjonsteknikk.
Bransjer som drar nytte av kinesiske sprøytestøpeselskaper

Bruken av sprøytestøping er ganske bred og sprer seg i forskjellige bransjer, hver av dem har sine egne standarder og teknologier.
1. Bilindustrien
Kinesiske støpeselskaper produserer deler som dashbord, støtfangere, interiørpaneler og belysningskomponenter til bilindustrien, som er svært avhengig av disse selskapene. En viktig fordel er evnen til å lage lette, men holdbare plastdeler.
2. Elektronikk og forbruksvarer
Kinesiske sprøytestøpefirmaer har spesialisert seg på å produsere deler med høy presisjon til elektronikk- og forbruksvareindustrien og en rekke andre produkter. Det er behov for stadig flere estetisk tiltalende, holdbare og funksjonelle plastkomponenter.
3. Medisin og helsevesen
Enheter som kirurgiske instrumenter, sprøyter og IV-kontakter bruker alle sprøytestøpte deler av høy kvalitet, og den medisinske industrien kan ikke klare seg uten dem. Avhengig av den medisinske produsenten har mange kinesiske støpefirmaer renromsfasiliteter for strenge hygiene- og sikkerhetsstandarder i henhold til medisinsk produksjon.
4. Emballasje- og næringsmiddelindustrien
Sprøytestøping brukes også til et annet viktig bruksområde, nemlig plastemballasje, som omfatter beholdere, lokk og flasker. På den ene siden produserer kinesiske produsenter holdbare emballasjeløsninger av høy kvalitet, mens de på den andre siden er miljøvennlige.
Nøkkelaktører i den kinesiske sprøytestøpeindustrien
Sprøytestøping har utviklet seg til å bli ledende i Kina i bransjer som bilindustrien, helsevesenet, elektronikk og forbruksvarer med høy kvalitet og kostnadseffektivitet. Kinesisk sprøytestøpefirmaer fortsette å lede det globale markedet ved hjelp av avanserte produksjonskapasiteter, toppmoderne utstyr og gjennomføring av internasjonale kvalitetsstandarder. Det er noen få av de kjente kinesiske produksjonsbedriftene for støpeformfremstilling av plastdeler i Kina.
Sincere Tech: En ledende leverandør av løsninger for sprøytestøping av plast
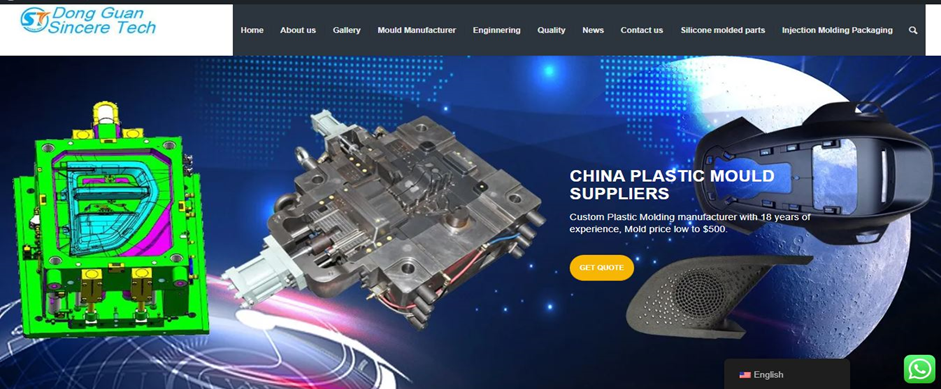
Sincere Tech, grunnlagt i 2005 og ligger i byen Dongguan-provinsen, Kina, er kjent for mer enn 10 år med å tilby forretningsstøpte plastsprøytestøpeformforsyningstjenester. Selskapet har utvidet sine evner til å inkludere ting som Eddie-støpeformer, silikon gummistøping, CNC-maskinering og komplett produktmontering og deltar i et bredt utvalg av bransjer over hele verden.
Mangfoldig utvalg av tjenester
Sincere Tech tilbyr totale produksjonsløsninger for kunder med følgende typer produkter:
- Selskapet tilbyr produkter som spesialtilpassede plastsprøytestøpeformer med mulighet til å designe og produsere høypresisjonsformer for masseproduksjon av holdbare og nøyaktige plastkomponenter.
- Presisjonsbearbeiding - CNC-maskinering, fresing, boring, dreining og sliping utført av Sincere Tech er med fullstendig ekspertise, noe som sikrer at hver del som produseres er med presisjon og høy kvalitet.
- For å øke produksjonsprosessen oppnår støpeformproduksjonsfirmaet suksess ved å produsere støpeformer av høy kvalitet og høy ytelse og sette dem sammen for å produsere holdbare metallkomponenter som oppfyller spesifikasjonene til de strenge bransjekravene.
- Vi tilbyr sprøytestøpingstjenester ved hjelp av avanserte plastsprøytestøpemaskiner for å produsere komponenter laget av følgende materialer som PP, ABS, PPS, PEEK, PA66+GF30.
- Produktmonteringstjenester - Selskapet monterer effektivt underenheter, enkle sammenstillinger og ferdig monterte produkter i henhold til strenge kvalitetsstandarder.
- Sincere Tech tilbyr silikonstøpeløsninger for spesifikke prosjekter i ulike bransjer.
Engasjement for kvalitet og teknologisk utvikling
Men oppriktig tech opprettholder den høyeste kvalitetsstandarden ved å overholde internasjonale standarder som ISO 9001:2015 og QS 9000:2015. For å produsere støpeformer og deler av beste kvalitet bruker selskapet avanserte maskiner, inkludert CMM-maskiner, 5-aksede CNC-maskiner og FANUC-maskiner. Sincere Tech matcher også kunder med NDA-er (Non-Disclosure Agreements) for å beskytte kundenes immaterielle rettigheter og proprietære design for konfidensialitetsformål.
Betjener globale bransjer
Sincere Tech er et internasjonalt sterkt selskap som leverer plast- og metallkomponenter til ulike bransjer (bilindustri, medisin, elektronikk, hvitevarer, hagearbeid, kosmetikk, matvareemballasje og elektriske kontakter). Selskapet har svært godt salg på eksportmarkedet, og produktene sendes til ulike globale markeder, inkludert Finland, ettersom de kan oppfylle de ulike bransjespesifikke standardene og kravene.
Kundefokusert tilnærming
Sincere Tech setter pris på konkurransedyktige priser, høy kvalitet i produksjonen og god service. På den annen side er selskapet en pålitelig partner for internasjonale virksomheter, med gode ferdigheter i prosjektledelse, tydelig kommunikasjon på teknisk engelsk og høy kundetilfredshet.
Seasky Medical
Seasky Medical er et kinesisk sprøytestøpeselskap som produserer plast til medisinsk bruk. Selskapet har hatt hovedkontor i Shenzhen, Guangdong, siden 1999, og tilbyr de beste sprøytestøpeløsningene. De tilbyr formdesign, materialvalg og sprøytestøping, i tillegg til å ta seg av produktutvikling, slik at medisinske komponenter oppfyller de høyeste kvalitets- og sikkerhetsstandarder.
ISO 8-sertifisert drift hos Seasky Medical sikrer produksjon av medisinsk utstyr som sprøyter, IV-komponenter og kirurgiske instrumenter i et forurensningsfritt miljø. Som et selskap med over ti års erfaring er de kjent for å levere pålitelig og nøyaktig medisinsk sprøytestøping der de betjener globale leverandører av helsetjenester.
Shenzhen Silver Basis Technology Co, Ltd
Shenzhen Silver Basis Technology er et profesjonelt kinesisk støpeselskap, dedikert til bil- og industriell moldproduksjon. Selskapet ble dannet i 1993 og er en av de mest pålitelige leverandørene for verdens berømte merkevarer som Peugeot og ZTE, og leverer modeller for forskjellige bruksområder.
Silver Basis tilbyr et omfattende utvalg av tjenester for metallstempling, pressstøping, støpeformproduksjon og produkttesting. Takket være deres ekspertise innen sprøytestøping for bilindustrien kan de produsere innvendige og utvendige bildeler som er holdbare og presise. Siden selskapet fokuserer på kvalitet, har det blitt tildelt ISO 9001- og ISO 14001-sertifikater, og på grunn av dette er det et selskap som er valgt av internasjonale bil- og elektronikkprodusenter.
JMT Automotive Mold Co, Ltd
JMT Automotive Mold Co, Ltd er et velrenommert kinesisk sprøytestøpeselskap som driver med design og produksjon av støpeformer til bilindustrien. Siden grunnleggelsen i 2005 og med base i Taizhou, Zhejiang, har selskapet bygget opp et solid produksjonssystem for å tilfredsstille de økende behovene i bilindustrien.
JMT Automotive Mold har en driftserfaring i et produksjonsanlegg på 23 000 kvadratmeter og er en av produsentene som spesialiserer seg på SMC mold, husholdningsapparater mold samt industriell mold. De har høyhastighets CNC-maskiner, presisjonstestutstyr og toppmoderne sprøytestøpemaskiner som fører til en høy produksjonsstandard. JMT Automotive opprettholder driften av teknologisk innovasjon og presisjonsteknikk, og vi tilbyr fortsatt pålitelig moldfabrikasjon for innenlandske og utenlandske kunder.
TK Mold Ltd
TK Mold Ltd ble grunnlagt i 1978 og er et velkjent kinesisk støpeselskap med mer enn 40 års erfaring innen produksjon av plastformer. Selskapet ble grunnlagt i 1983 og spesialiserer seg på utvikling av høypresisjonsformer for medisinske apparater, forbrukerelektronikk, smarthusapparater og bilkomponenter.
TK Mold tilbyr avanserte sprøytestøpeløsninger til sin globale kundegruppe fra sine fem produksjonsanlegg, inkludert ett i Tyskland. Selskapet er en pioner innen bruk av banebrytende teknologi, automatisering og presisjonsproduksjon, og er høyt verdsatt av bransjer som krever høytytende plastkomponenter. Alle produktene fra TK Mold er sertifisert i henhold til ISO 9001, ISO 13485 og ISO 14001 for å sikre at de faller innenfor de internasjonale kvalitets- og sikkerhetsstandardene.
Guangdong Yizumi Precision Machinery Co, Ltd
Guangdong Yizumi er et ledende kinesisk sprøytestøpeselskap som produserer høyytelses sprøytestøpemaskiner samt plastkomponenter. Yizumi ble grunnlagt i 2002, og hovedkontoret ligger i Foshan, Guangdong. Med over 600 000 kvadratmeter produksjonsbase og nesten 3000 ansatte har Yizumi utviklet seg til et verdensmerke.
Yizumi har vunnet en rekke bransjepriser for sine innovasjoner innen sprøytestøpingsteknologi og er kjent for sine innovative, formstøpte løsninger. I 2015 ble selskapet det første kinesiske sprøytestøpeselskapet som ble notert på Shenzhen-børsen. Yizumi fokuserer på bilindustrien, forbrukerelektronikk og industrielle bruksområder, og er i ferd med å bli ledende i bransjen med sine toppmoderne maskiner og støping med høy presisjon.
Utfordringer og hensyn ved valg av kinesisk støperi
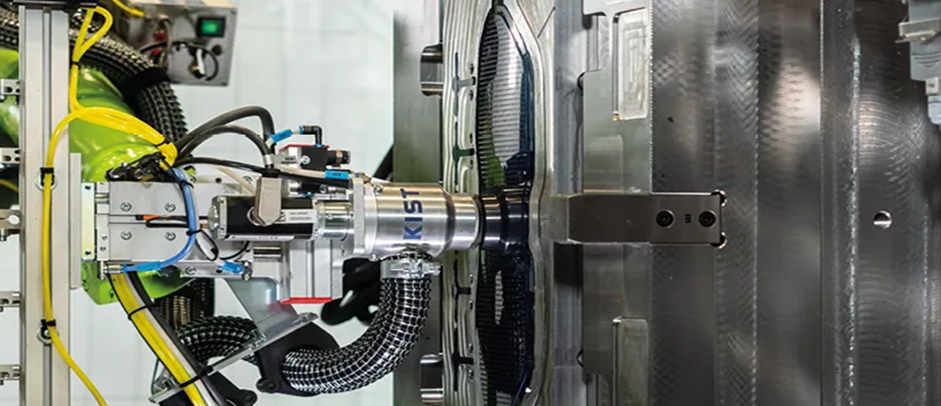
Kinesiske gruveselskaper har mange fordeler, men før man velger en produsent, bør man være klar over noen få aspekter.
1. Kvalitetskontroll og samsvar
Ikke alle produsentene følger de samme kvalitetsstandardene. Før du velger en leverandør, bør du verifisere sertifiseringer og teste en prøve først.
2. Beskyttelse av immaterielle rettigheter
Produksjon i Kina kan være et problem når det gjelder beskyttelse av immaterielle rettigheter (IP). For å unngå å miste design og beskytte dem, bør bedrifter samarbeide med pålitelige partnere og inngå juridiske avtaler.
3. Kommunikasjon og språkbarrierer
Selv om flere kinesiske produsenter har engelsktalende salgsteam, er kommunikasjonen ikke alltid like enkel. Dokumentasjon og avtale er utarbeidet for å forhindre misforståelser.
4. Logistikk og frakt
Det kan imidlertid være komplisert og kostbart å håndtere store ordrer internasjonalt. Kinesiske støpeselskaper bør være innforstått med virksomhetens tilpassede regler, ledetider og fraktkostnader.
Fremtidige trender innen kinesisk sprøytestøping
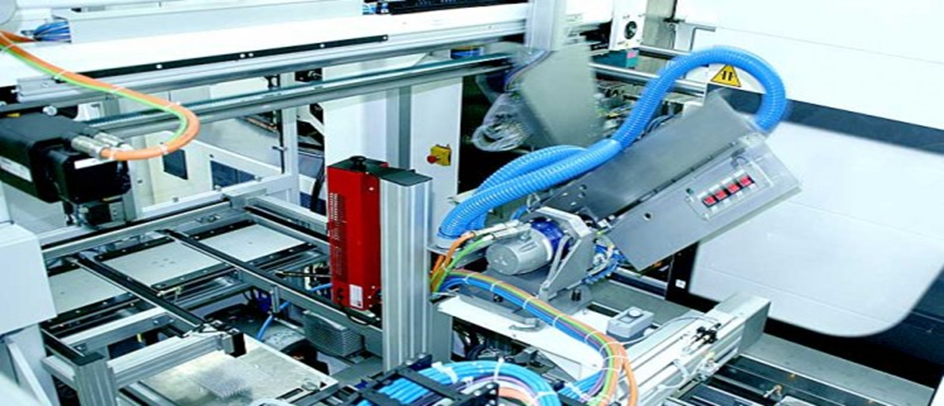
Med ny teknologi følger utviklingen av den kinesiske støpeindustrien for å møte de nye markedskravene. Viktige trender inkluderer:
1. Bærekraftige og miljøvennlige materialer
Etter hvert som bekymringene for plastavfall har økt i Kina, har mange støperier blitt mer opptatt av miljøbestemmelser og utvikler nå både biologisk nedbrytbare og resirkulerte plastmaterialer.
2. Smart produksjon og Industri 4.0
Automatiseringen og den AI-drevne kvalitetskontrollen, den fullstendige overgangen fra en menneskesentrert prosess til en IoT-aktivert smart fabrikk, har forvandlet sprøytestøpeprosessen fullstendig, og det gjør produksjonen mer effektiv og gir mindre svinn.
3. Økt tilpasning og produksjon på bestilling
Bedriftene fokuserer i økende grad på on-demand-produksjon i små serier for nisjemarkeder og rask produktutvikling.
Konklusjon
Kinesiske sprøytestøpeselskaper er en integrert del av den globale produksjonsindustrien, ettersom disse selskapene leverer kostnadseffektive og innovative løsninger av høy kvalitet til kundene. Noen av disse produsentene bearbeider plastdeler til bilkomponenter, medisinsk utstyr og andre relaterte bransjer. Når du velger et kinesisk støpeselskap, bør forretningsenheter nøye undersøke kvalitetsstandarder, kommunikasjonsmuligheter og logistikk for å sikre et vellykket partnerskap. På grunn av den kontinuerlige trenden med teknologiske fremskritt og bærekraftig praksis, vil kinesiske støpeselskaper fortsette å lede an innen sprøytestøping i mange år fremover. Med tanke på de mange fordelene bør bedrifter imidlertid ta hensyn til kvalitetskontroll, beskyttelse av immaterielle rettigheter, kommunikasjonsutfordringer og logistikk før de velger en kinesisk støpepartner. Men hvis man har gjort grundige undersøkelser og samarbeider med produsenter som produserer med kvalitet og er sertifisert for arbeidet, kan bedriftene høste fordelene av Kinas ekspertise innen sprøytestøping. I fremtiden vil sprøytestøping i Kina være preget av bærekraftige materialer, smart produksjon, høyhastighetsproduksjon og produksjonsdrevet automatisering kombinert med biologisk nedbrytbar plast og Industri 4.0-teknologi, og Kina vil fortsatt ha de største fremskrittene innen global sprøytestøping. Etter hvert som de kinesiske sprøytestøpeselskapene kontinuerlig utvikler seg og gjør sitt beste for å endre den kinesiske produksjonens ansikt utad, vil de fortsette å drive moderne produksjon fremover.
Ofte stilte spørsmål (FAQ)
1. Hvorfor er sprøytestøpingsproduksjon fra Kina populær?
Å velge Kina for sprøytestøping gir fordelen av kostnadseffektiv produksjon, moderne teknologi, godt utdannet arbeidsstyrke og godt organisert forsyningskjede. Det er mange produsenter som følger internasjonale kvalitetsstandarder, og de tilbyr tilpassede løsninger med svært rask behandlingstid.
2. Hvordan kommer kinesiske sprøytestøpeselskaper industrien til gode?
Alle disse bransjene har vært avhengige av kinesisk sprøytestøping, inkludert bilindustrien, elektronikk, medisinsk utstyr, emballasje og forbruksvarer. Kinesiske produsenter kan effektivt og billigere produsere plastkomponenter med høy presisjon som trengs for disse industriene.
3. Hvordan garanterer kinesiske sprøytestøpeselskaper produktkvalitet?
Kina støping pålitelige selskaper kontrollerer strengt kvaliteten fra råvarer til ferdige produkter og oppnår følgende sertifikater: ISO 9001, ISO 13485 (medisinsk) og IATF 16949 (bildeler). Testprosessene og de automatiserte inspeksjonssystemene deres holder høy standard.
4. Et utvalg av kinesiske støpeprodusenter er hva?
Kvalitetssertifiseringer, erfaring, produksjonskapasitet, beskyttelse av immaterielle rettigheter og evnen til å kommunisere og tilby logistikkstøtte bør tas i betraktning av bedriftene. Prøvetesting og sikring av selskapets leveringsdyktighet bør gjennomføres for å bane vei for et godt partnerskap.
5. Hva er utsiktene for den kinesiske sprøytestøpeindustrien?
Tiden vi lever i, krever at industrien finner nye trender for å løse problemet, blant annet bærekraftig og biologisk nedbrytbar plast, AI-drevet automatisering, smarte fabrikker og produksjon på forespørsel. Disse fremskrittene vil gjøre produksjonen mer effektiv, redusere avfallsmengden og dekke den stadig økende etterspørselen etter miljøvennlige produksjonsløsninger.