Nowadays, China has solidified its position as a global leader in injection molding companies and has become a valuable manufacturing solution for businesses of all sizes in the world, at competitive prices. Thanks to its large number of injection molding companies China has become a specializing area in producing plastic components for the whole spectrum of industries, from automotive, electronics, healthcare, and packaging to consumer goods. They do the heavy lifting of advanced technology, precision engineering, and automation are used for making molded parts with unbeatable accuracy and efficiency. Several key advantages build the Chinese injection molding industry which businesses tend to opt for. One of the biggest drawing forces regarding cost-effectiveness production is that labor and production costs are cheaper in China than in Western countries. Moreover, Chinese molding companies are increasingly equipped with high-efficiency, state-of-the-art machinery and robotics systems, enabling efficient and high-volume production at the same time as maintaining quality. The company has internationally recognized certifications such as ISO 9001, ISO 13485 (medical devices), and IATF 16949 (automotive components) to comply with the global industry standards of quality.
Chinese injection molding companies also have the strength of customization and innovation. Manufacturers in China have the technical capability as well as the expertise to provide customized molds for a client’s multi-cavity molds, overmolding, insert molding, and complicated designs. For businesses looking for speed and reliability, their capability to provide fast turnaround time and huge-scale production is a preferred choice.
What is Injection Molding?
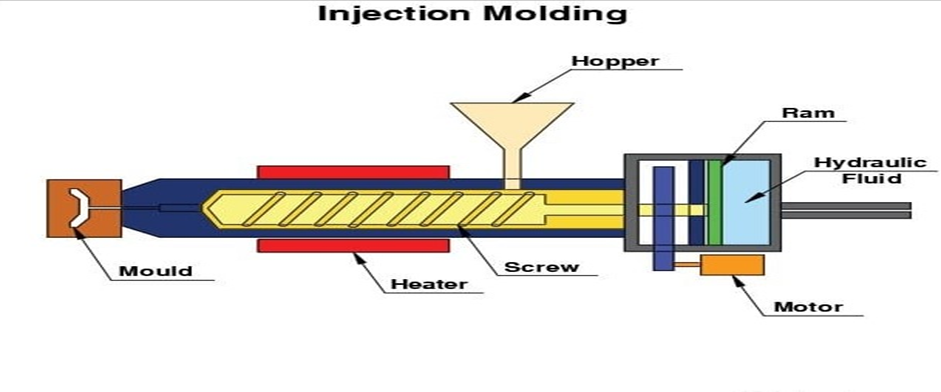
This is a process of manufacturing plastic parts by injection of molten material into a mold. Such as automotive, medical, electronics, plastic packaging and household goods, it is widely used. This process takes complex part into mass production with high precision and consistency.
Why Use an Injection Molding Company of Chinese?
Firstly, China has become a major injection molding hub for a variety of reasons:
1. Cost-Effective Production
Pricing is one of the key reasons why businesses choose Chinese molding companies. Because labor and operation costs in China are lower than in Western countries, it is possible to produce high-quality molded components at a fraction of the cost.
2. Advanced Manufacturing Technology
In modern Chinese injection molding companies heavy investments are made toward automation and state of the art machinery. Precision and the highest productivity is ensured by many firms using robotic systems, computer aided design (CAD) and real time quality control systems.
3. High-Quality Standards
Most respectable Chinese molding companies abide by international quality standards such as ISO 9001, ISO 13485 (for medical devices), and IATF 16949 (automotive parts). These certifications guarantee that the product qualifies for high-quality requirements.
4. Customization and Innovation
Customized solutions appropriate to different business needs are provided by many Chinese molding companies. Chinese manufacturers have an answer for every client’s need from over-molding and insert molding, and want to a client’s need for complex multi-cavity models.
5. Fast Turnaround Times
Chinese molding companies can produce in large volumes more efficiently and quickly than most competitors because of efficient supply chains and streamlined production processes. Businesses that depend on speed to bring products to market will need the support of this speed.
6. Experience and Expertise
There are thousands of specialized companies in China’s injection molding industry that have deep experience in all these areas. They are considered the preferred choice for global businesses in their domain of mold design and material selection as well as precision engineering.
Industries Benefiting from Chinese Injection Molding Companies

The use of injection molding is quite wide and spreads out in different industries, each of them have their own standards and technologies.
1. Automotive Industry
Chinese molding companies produce parts such as dashboards, bumpers, interior panels, and lighting components in the automotive sector, which relies heavily on these companies. One key advantage is the capability to make lightweight but durable plastic parts.
2. Electronics and Consumer Goods
For the electronics and consumer goods industry and various other products, Chinese injection molding companies specialize in producing high-precision parts. More and more aesthetically pleasing, durable, and functional plastic components are needed.
3. Medical and Healthcare
Devices such as surgical instruments, syringes, and IV connectors all use high-quality injection-milled parts, and the medical industry can’t do without them. Depending on the medical manufacturer, many Chinese molding companies have clean room facilities for strict hygiene and safety standards as per the medical manufacturing.
4. Packaging and Food Industry
Injection molding is also used for another major application, that is, plastic packaging, which includes containers, caps, and bottles. On the one hand, Chinese manufacturers produce high-quality durable packaging solutions while on the other hand, they are environmentally friendly.
Key Players in the Chinese Injection Molding Industry
Injection molding has emerged as a China leader for industries ranging from automotive, healthcare, and electronics, to consumer goods with high quality and cost-effectiveness. Chinese injection molding companies keep on leading the global market by way of advanced manufacturing capabilities, state-of-the-art equipment, and conducting following international quality standards. There are a few of those well-known Chinese molding mold fabrication china molds plastic part manufacturing companies.
Sincere Tech: A Leading Provider of Plastic Injection Molding Solutions
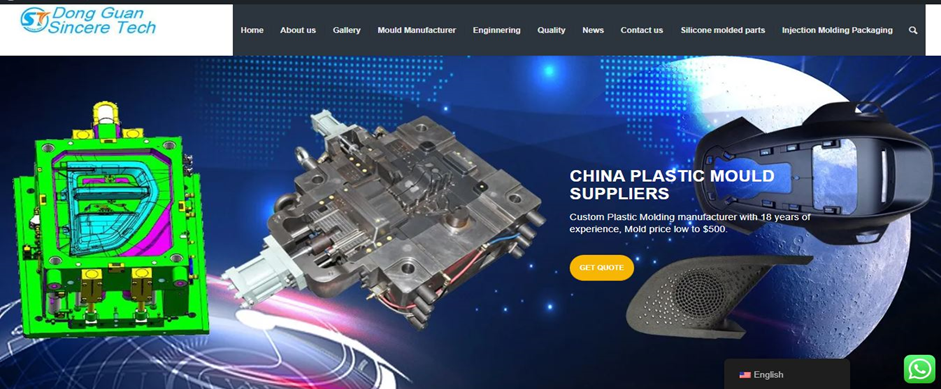
Sincere Tech, founded in 2005 and located in the city of Dongguan Province, China, is known for more than 10 years of providing business molded plastic injection mold supply service. The company has expanded its capabilities to include things like Eddie-casting molds, silicone rubber molding, CNC machining, and complete product assembly and participates in a wide variety of industries all around the world.
Diverse Range of Services
Sincere Tech provides total manufacturing solutions for those customers with the following kinds:
- The company provides products such as custom plastic injection molds with the ability to design and manufacture high-precision molds for mass manufacturing of durable and accurate plastic components.
- Precision Machining – The CNC machining, milling, drilling, turning and grinding done by Sincere Tech is with complete expertise, ensuring that every part manufactured is with precision and high quality.
- To heighten the manufacturing process, the die-casting mold manufacturing company achieves success by manufacturing high-quality and high-performance die-casting molds and assembling them to produce durable metal components that meet the specifications of the strict industry requirements.
- We provide Injection Molding Services by utilizing advanced plastic injection molding machines to produce components made of the following materials such as PP, ABS, PPS, PEEK, PA66+GF30.
- Product Assembly Services – The company efficiently assembles sub-assemblies, simple assemblies and products fully assembled, following rigorous quality standards.
- Sincere Tech provides silicone molding solutions for specific projects in various industries.
Commitment to Quality and Technological Advancement
However, sincerely tech maintains the highest standard of quality by complying with international standards such as ISO 9001:2015 and QS 9000:2015. To manufacture the best quality molds and parts, the company makes use of advanced machinery including CMM machines, 5-axis CNC machines, and FANUC machinery. Sincere Tech also matches clients with NDAs (Non-Disclosure Agreements) for the protection of clients’ intellectual property and proprietary designs for confidentiality purposes.
Serving Global Industries
An internationally strong company, Sincere Tech supplies plastic and metal components to various industries (automotive, medical, electronics, home appliances, gardening, cosmetics, food packages, and electric connectors). The company has very good sales in the export market whose product is shipped to different global markets including Finland as he can meet the different industry-specific standards and requirements.
Customer-Focused Approach
Sincere Tech values competitive pricing, high quality manufacturing and good quality service. On the other hand, as a reliable partner for international businesses, the company’s project management skills are strong, communication in technical English is clear, and customer satisfaction is high.
Seasky Medical
A Chinese injection molding company, Seasky Medical manufactures plastics for medical use. The company has been headquartered in Shenzhen, Guangdong, since 1999 and it provides the best injection molding solutions. They offer fine mold design, material selection and injection molding as well as take care of product development, so medical components are up to the highest quality and safety standards.
ISO 8 certified operation at Seasky Medical ensures production of medical devises such as syringes, IV components, surgical instruments in a contamination free environment. As a company with over a decade of experience, they are known for delivering reliable and accurate medical injection molding in which they serve global healthcare providers.
Shenzhen Silver Basis Technology Co., Ltd
Shenzhen Silver Basis Technology is a professional Chinese molding company, dedicated to automotive and industrial mold manufacturing. Formed in 1993, the company is one of the most reliable suppliers for the world’s famous brand like Peugeot and ZTE, supplying models for diverse uses.
Silver Basis offers a comprehensive range of services for metal stamping, die casting, mold fabrication, and product testing. Due to their automotive injection molding expertise, they can manufacture interior and exterior vehicle parts that are durable and precise. Since the company is focused on quality, the company has been awarded ISO 9001 and ISO 14001 certificates, and because of that, it is a company chosen by international automotive and electronics manufacturers.
JMT Automotive Mold Co., Ltd
JMT Automotive Mold Co., Ltd is a reputable Chinese injection molding company that deals in automotive mold design and manufacturing. Since its founding in 2005 and based in Taizhou, Zhejiang, the company has built up a solid manufacturing system to satisfy the increasing needs of the automotive industry.
JMT Automotive Mold has an operating experience in a production site of 23,000 square meters and is one of the manufacturers specializing in SMC mold, home appliance mold as well as industrial mold. They have high-speed CNC machinery, precision testing equipment, and state-of-the-art injection molding machinery that lead to a high standard of production. JMT Automotive maintains the operation of technological innovation and precision engineering, and we still offer reliable mold fabrication for domestic and abroad clients.
TK Mold Ltd
Founded in 1978, TK Mold Ltd is a well-known Chinese molding company with more than 40 years in plastic mold fabrication. The company was founded in 1983 and specializes in the development of high-precision molds for medical appliances, consumer electronics, smart house appliances, and automotive components.
TK Mold offers advanced injection molding solutions for its global group of customers from its base of 5 production plants, including one in Germany. Being a pioneer in the adoption of cutting-edge technology, automation, and precision manufacturing, the company is highly appreciated by industries demanding high-performing plastic components. All the produces of TK Mold are certified under ISO 9001, ISO 13485, and ISO 14001 to assure that it falls within the international Quality and safety standards.
Guangdong Yizumi Precision Machinery Co., Ltd
Guangdong Yizumi is a leading Chinese injection molding company producing high performance injection molding machine as well as plastic components. Yizumi was founded in 2002 and its headquarter is located in Foshan, Guangdong. With over 600,000 square meter production base and nearly 3,000 staff, Yizumi has developed into a world brand.
Yizumi has won numerous industry awards for its innovations in injection molding technology and is known for its innovative, molding solutions. In 2015, the company became the first Chinese molding company to be listed on the Shenzhen Stock Exchange. Yizumi is focusing on automotive, consumer electronics, and industrial applications and becoming a leader in the industry with its state-of-the-art machinery and molding with high precision.
Challenges and Considerations When Choosing a Chinese Molding Company
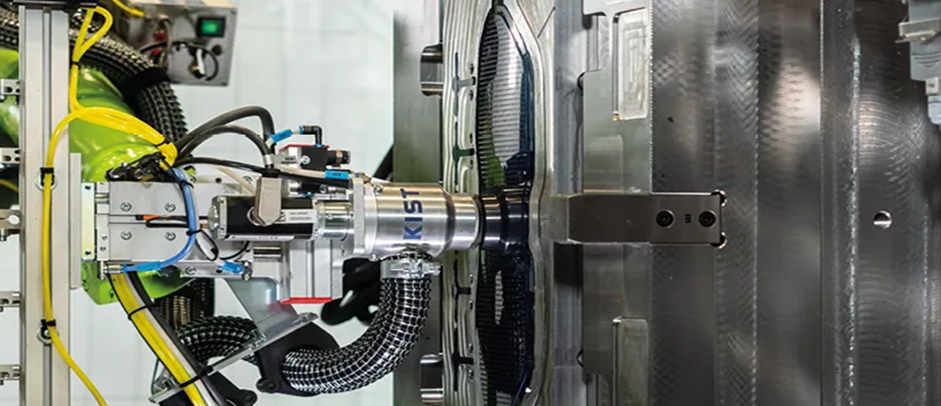
Chinese mining companies do present many advantages, however, before committing to a manufacturer, businesses should be aware of a few aspects.
1. Quality Control and Compliance
All of the manufacturers do not follow the same quality standards. Before choosing a supplier, you should verify certifications and test a sample first.
2. Intellectual Property Protection
Manufacturing in China may be an issue for outsourcing intellectual property (IP) protection. To avoid losing their designs and keep them safe, businesses should work with trusted partners and legal agreements.
3. Communication and Language Barriers
While several Chinese manufacturers will have English-speaking sales teams, communication isn’t always straightforward. Documentation and agreement are prepared to prevent misunderstanding.
4. Logistics and Shipping
However, dealing with large orders internationally can be complex and costly. Chinese molding companies should be understood within the businesses’ custom regulations, lead times, and freight costs.
Future Trends in Chinese Injection Molding
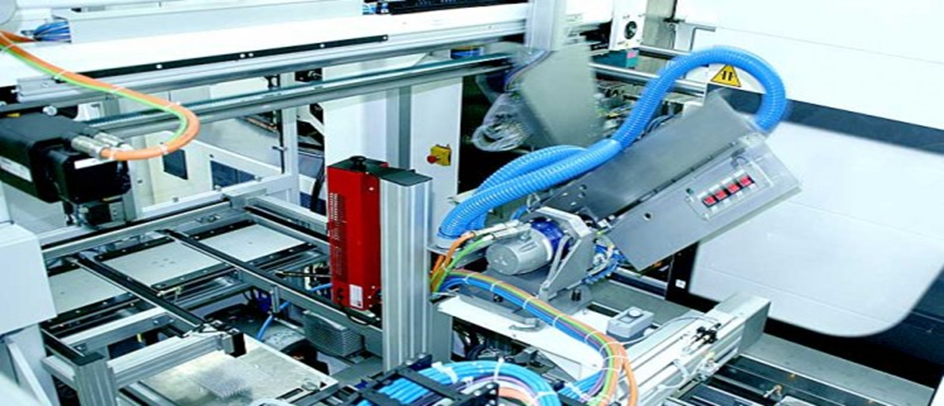
With new technologies, there comes the development of the Chinese molding industry to meet the new market demands. Key trends include:
1. Sustainable and Eco-Friendly Materials
As plastic waste concerns have grown in China, many molding companies have become more concerned about environmental regulations and are now developing biodegradable, as well as recycled, plastic materials.
2. Smart Manufacturing and Industry 4.0
The automation and AI-driven quality control, the complete changeover from a human-centric process to an IoT-enabled smart factory has completely transformed the Injection Molding process and it makes the production more efficient and less wastage.
3. Increased Customization and On-Demand Production
The focus of companies is moving to on-demand, small-batch production for niche markets and fast product development.
Conclusion
Chinese injection molding companies are an integral part of the global manufacturing industry as these companies provide cost-effective, high quality and innovative solutions for customers. Some of these manufacturers machine plastic parts for automotive components, medical devices, and other related industries. When choosing a Chinese molding company, business entities should rigorously examine quality standards, the convenience of communication, and logistics to secure a successful partnership. Due to the continual trend of technological advancements and sustainable practices, Chinese molding companies will continue to lead the way through injection molding for many more years. If given the many advantages, businesses should however weigh in quality control, intellectual property protection, communication challenges, and logistics before choosing a Chinese molding partner. However, if research has been conducted thoroughly and collaboration with manufacturers who produce with quality and are certified for the work, the businesses can reap the benefits of China’s expertise in injection molding. In the future, injection molding in China will be characterized by sustainable materials, smart manufacturing, high-speed production, and production-driven automation coupled with biodegradable plastics and Industry 4.0 technologies, China will still have the greatest strides in global injection molding. As the Chinese molding companies continuously advance and do their best to alter the face of Chinese manufacturing, they will continue to propel modern manufacturing.
Frequently Asked Questions (FAQs)
1. Why is injection molding manufacturing from China popular?
Choosing China for injection molding offers the advantage of cost effective production, modern technology, well trained workforce, and well organized supply chain. There are many manufacturers that follow international quality standards and they offer customized solutions with very quicker turnaround time.
2. How do Chinese injection molding companies benefit the industries?
All of these industries have been dependent on Chinese injection molding including automotive, electronics, medical devices, packaging, and consumer goods. Chinese manufacturers can effectively and cheaper produce the high precision plastic component needed for these industries.
3. How do Chinese injection molding companies guarantee product quality?
China molding reliable companies strictly control the quality from raw materials to finished products and obtain the following certificates: ISO 9001, ISO 13485 (medical), and IATF 16949 (automotive parts). Their level of testing processes and automated inspection systems hold them up to high standards.
4. A Chinese molding manufacturer selection is what?
Quality certifications, experience, production capabilities, intellectual property protection and the ability to communicate and provide logistics support should be taken into consideration by businesses. Sample testing and ensuring the capability of the company to deliver should be conducted to pave the way for a good partnership.
5. What is the prospect of the Chinese injection molding industry?
The times we are living in require industry to find new trends to resolve it, including sustainable and biodegradable plastics, AI powered automation, smart factories and on demand production. These advances will make manufacturing more efficient, waste less, and supply for the continually growing demand for eco friendly manufacturing answers.