En el vertiginoso mundo de la atención sanitaria, la precisión, la limpieza y el cumplimiento van más allá de las palabras de moda y son un requisito innegociable. Una de las tecnologías subyacentes que permite fabricar dispositivos médicos seguros, eficaces y escalables es el moldeo por inyección de plásticos médicos. Al dar forma a jeringuillas y catéteres, instrumentos quirúrgicos y carcasas de diagnóstico, el moldeo por inyección de plásticos es importante para impulsar la medicina moderna mediante la creación de las piezas constituyentes.
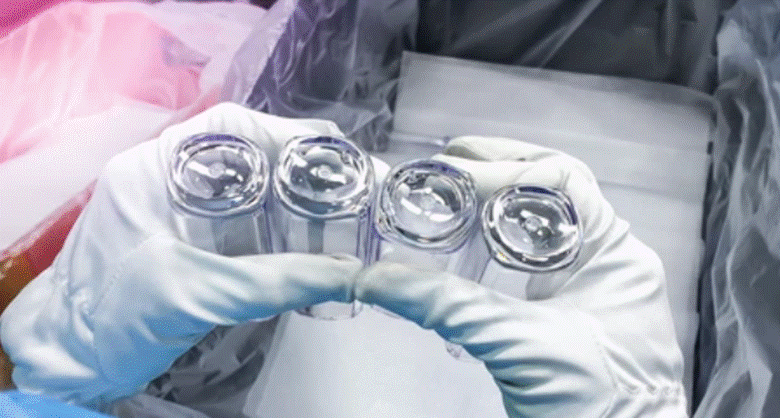
Merece la pena mencionar el factor de seleccionar un fabricante de moldes de inyección médica de confianza. El proveedor adecuado garantiza que su producto se ajuste a las estrictas normas del sector, funcione con la máxima precisión y siga siendo económico en tiradas de producción a gran escala. Un fallo de este tipo puede tener importantes repercusiones negativas, como la retirada de productos o el incumplimiento de la normativa, o poner en peligro la seguridad del paciente.
Este artículo ofrece una lista de los 10 principales empresas de moldeo por inyección de plásticos médicos de diversas partes del mundo. Los criterios de consideración de las empresas de la lista son muy estrictos, empezando por las certificaciones, la innovación, su presencia mundial y sus resultados anteriores. A pesar de que la naturaleza global de la industria implica a actores de muchas regiones, hemos restringido la elección a sólo dos empresas chinas, siendo Sincere Tech una de ellas, y el resto están distribuidas en EE.UU., Europa e Israel.
¿Qué es el moldeo por inyección de plásticos médicos?
Se trata de un proceso de fabricación especializado que se utiliza para producir componentes médicos y sanitarios de plástico de gran precisión y calidad. Consiste en inyectar plástico fundido en un molde mecanizado especialmente y enfriarlo hasta que se solidifica y adquiere su forma final.
Características principales:
- Precisión y limpieza: El moldeo médico debe ajustarse a tolerancias estrictas y se lleva a entornos de sala blanca para evitar la contaminación.
- Materiales biocompatibles: Utilice plásticos de calidad médica, como policarbonato, polipropileno y PEEK, que son seguros para su uso en o con el cuerpo humano.
- Cumplimiento de la normativa: Los fabricantes deben cumplir normas como la ISO 13485, la FDA y la CE para garantizar la seguridad y la eficacia.
- Gran volumen y repetibilidad: Perfecta para fabricar grandes tiradas de piezas uniformes y estériles, como jeringuillas, juegos intravenosos, carcasas de diagnóstico, artroscopios, instrumentos quirúrgicos y dispositivos dispensadores de fármacos.
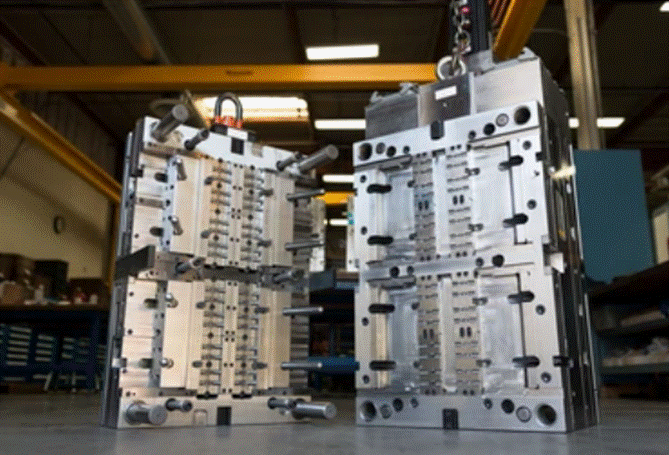
Criterios de selección
Los siguientes criterios ayudaron a decidir qué empresa era la mejor en moldeo por inyección médica,
1. Certificación ISO 13485 y cumplimiento de la normativa
La norma internacionalmente aceptada para los sistemas de gestión de calidad de la industria de productos sanitarios es la ISO 13485. Además, las empresas tienen que cumplir la normativa de la FDA y la CE cuando pretenden vender sus productos.
2. Tecnología avanzada y salas blancas
Las empresas deben ser capaces de operar en entornos de sala blanca (ISO Clase 7 o superior) y hacer uso de la última tecnología de moldeo por inyección (micromoldeo y moldeo por inyección multidisparo) para cumplir las normas de higiene, contaminación, etc.
3. Enfoque médico y trayectoria en el sector
La fiabilidad y la experiencia en la fabricación de componentes médicos tienen una larga historia. Las empresas que llevan mucho tiempo en el sector sanitario también entienden mejor la normativa y las exigencias de rendimiento.
4. Amplia base de clientes del sector sanitario y alcance mundial
Las empresas mundiales dispondrán de sólidas infraestructuras de control de calidad, logística y reglamentación para atender mejor a los fabricantes de equipos médicos multinacionales.
5. Capacidades de I+D y personalización
No sólo ofrecen fabricación, sino también asistencia en ingeniería, diseño para fabricación (DFM), así como colaboración en innovación para dar vida a nuevos productos de forma rápida y eficaz.
Las 10 principales empresas de moldeo por inyección de plásticos médicos.
Se trata de algunos de los líderes mundiales del sector del moldeo por inyección de plásticos médicos. Elegidos en función de criterios estrictos, como certificaciones de calidad, avances tecnológicos, presencia mundial y compromiso con la innovación, estos fabricantes cuentan con la confianza de las principales marcas de dispositivos médicos de todo el mundo. Aquí están los 10 primeros:
1. Sincere Tech (China)
Sincere Tech es uno de los principales fabricantes chinos dedicados al moldeo por inyección de plásticos médicos para clientes de todo el mundo. Abarcando el moldeo en sala blanca, la creación rápida de prototipos y la producción en serie, Sincere Tech es una fuente fiable de piezas médicas de alta precisión. Su compromiso con la calidad se basa en las normas ISO 13485, herramientas avanzadas y rigurosos procesos de validación. Además, los fabricantes de equipos médicos pueden subcontratar todo el proceso, incluido el diseño del molde, la fabricación e incluso el montaje, lo que lo convierte en un servicio completo con varias empresas.
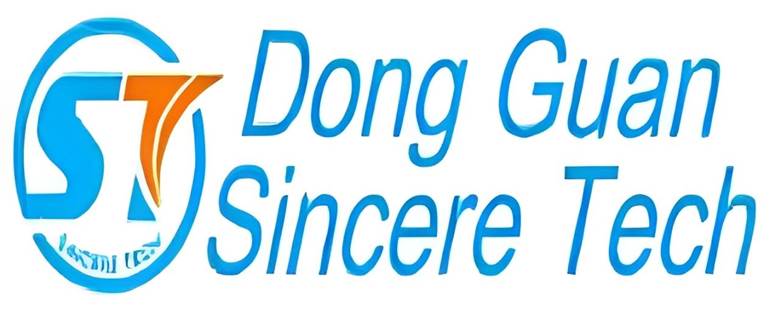
Página web: https://www.plasticmold.net/
Perfil de la empresa:
Durante más de 15 años, Sincere Tech se ha especializado tanto en la fabricación de moldes como en la elaboración de piezas de plástico precisas en China. Gracias a su cualificación ISO 13485 y a sus salas blancas de alta calidad, la empresa ofrece piezas importantes para fabricantes mundiales de equipos médicos originales que buscan tolerancias estrictas. Esta empresa abarca el diseño de moldes, se encarga del utillaje y lleva a cabo el procesamiento secundario, todo ello desde la misma ubicación. Dado que pueden gestionar el desarrollo de productos desde los primeros pasos hasta la producción en serie, son muy valiosos para la fabricación de productos sanitarios.
Industrias atendidas:
Dispositivos médicos, automoción, electrónica y envasado.
¿Por qué elegir Sincere Tech?
- Nuestra fábrica de moldeo de precisión de grado médico cumple la estricta norma ISO 13485.
- Ofrece todos los servicios, desde el diseño y la creación de prototipos hasta la producción.
- Capacidad para moldear piezas en salas blancas para productos no contaminantes.
- Se necesita una buena garantía de calidad y validación.
- Ofrecemos precios competitivos tanto a pequeños como a grandes clientes internacionales.
2. Phillips-Medisize (EE.UU.)
Phillips Medisize es una empresa de Molex y un titán de la industria en el campo de la administración integrada de fármacos, los dispositivos de diagnóstico y la electrónica médica. Se trata de una empresa de servicios integrales de moldeo por inyección de productos médicos, con presencia en todo el mundo y gran experiencia en montajes complejos. Cuentan con instalaciones de sala blanca de última generación, que ofrecen servicios de diseño y creación de prototipos, así como servicios automatizados de fabricación de grandes volúmenes en caso de que los necesite. La empresa es líder en innovación de soluciones para conectar la salud digital y de seguimiento avanzado de productos.
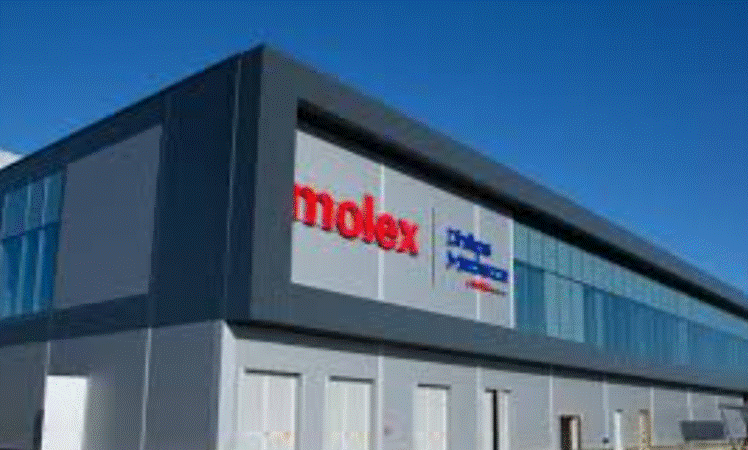
Perfil de la empresa:
Phillips-Medisize, que opera como división de Molex, se centra en la fabricación de dispositivos de administración de fármacos, diagnóstico y salud conectada en todo el mundo. Con presencia internacional en EE. UU., Europa y Asia, la empresa dispone de salas blancas desde la clase ISO 7 hasta la clase 8. Prestan servicios en cada etapa, ocupándose del diseño, el desarrollo, las pruebas y la producción completa. Entre sus clientes se encuentran algunas de las principales empresas farmacéuticas y de dispositivos médicos del mundo.
Industrias atendidas:
Administración de fármacos, diagnóstico y electrónica médica.
¿Por qué elegir Phillips-Medisize?
- Funcionamiento internacional potenciado por la automatización y mantenido en entornos de sala blanca.
- Conocimientos sobre salud conectada y uso de tecnología digital.
- Un historial de cooperación fructífera con las principales empresas de tecnología médica.
- Todas nuestras operaciones en todo el mundo cumplen las normas ISO 13485 y FDA.
- Experiencia en la gestión de las necesidades de grandes proyectos de fabricación.
3. Tessy Plastics (EE.UU.)
Tessy Plastics lleva décadas dedicándose al moldeo por inyección de plásticos de alta precisión en el sector médico y es famosa por su certificación ISO 13485. Disponen de todos los productos en la propia empresa, desde el utillaje hasta todo, desde la automatización hasta la validación. Completamente volcados en el campo médico, producen una amplia gama de dispositivos médicos quirúrgicos, de diagnóstico y wearables que trabajan en estrecha colaboración con clientes y socios para garantizar una mayor fiabilidad, facilidad de escalabilidad y cumplimiento de la normativa mundial. También poseen las capacidades de micromoldeo y moldeo por inserción para componentes delicados.
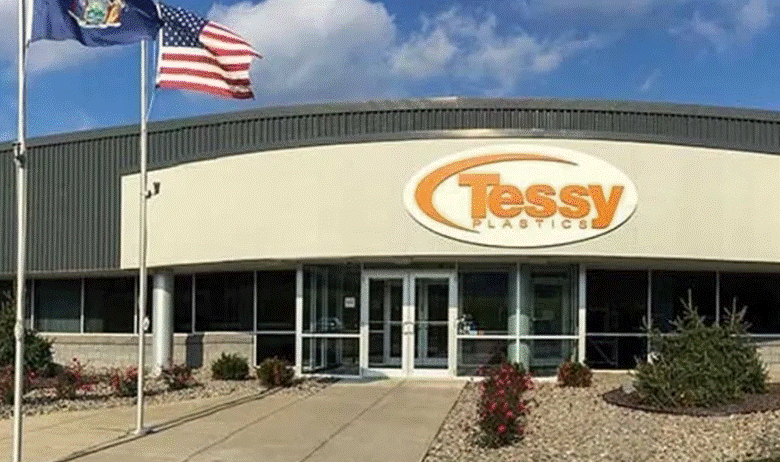
Perfil de la empresa:
Desde 1976, Tessy Plastics opera en Nueva York (EE.UU.) como empresa familiar en el campo del moldeo por inyección de precisión. La vertiente médica de Bosch hace hincapié en los dispositivos quirúrgicos, de diagnóstico y para llevar puestos, todos ellos fabricados con estrictas normas de calidad. Tessy combina en su trabajo automatización, utillaje avanzado y procesos de montaje. El personal de ingeniería de la empresa colabora con los clientes para resolver problemas de diseño, normativa y lanzamiento rápido.
Industrias atendidas:
Medicina, electrónica y bienes de consumo.
¿Por qué elegir Tessy?
- Todos los pasos, desde el diseño hasta la venta, están bajo una misma autoridad.
- Sus puntos fuertes son el micromoldeo y el moldeo por inserción.
- Más de 40 años fabricando productos sanitarios.
- La empresa dispone de salas blancas ISO Clase 7.
- La empresa cuenta con la certificación ISO 13485 y su objetivo es cumplir todos los requisitos de los productos sanitarios.
4. Gerresheimer (Alemania)
Gerresheimer es un líder mundial en envases médicos y farmacéuticos con una importante división de moldeo por inyección de plásticos capaz de fabricar sistemas de administración de fármacos, dispositivos de diagnóstico moldeados por inyección y jeringuillas precargadas. Mantiene múltiples instalaciones de fabricación en sala blanca y opera con arreglo a las normas reglamentarias más estrictas. Gracias a su integración vertical del diseño del producto a la fabricación del molde y, por último, al montaje final, es el socio preferido de las empresas farmacéuticas de todo el mundo.
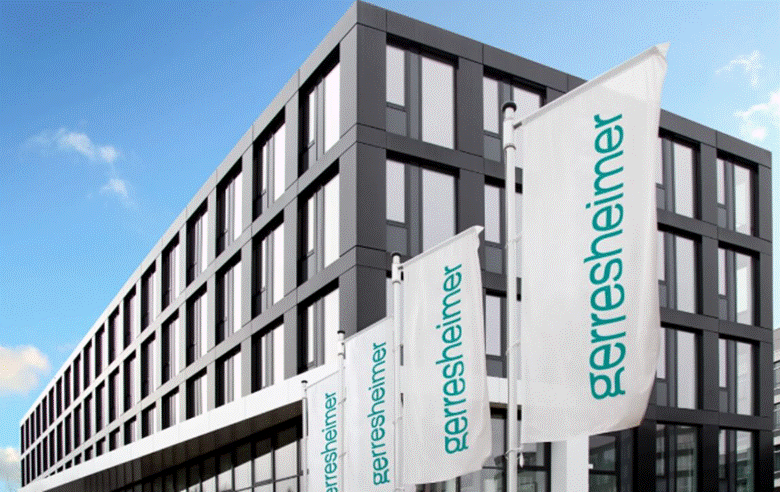
Perfil de la empresa:
Las empresas de envases médicos y farmacéuticos reconocen ampliamente a Gerresheimer y su larga trayectoria en moldeo por inyección. Las operaciones mundiales de la empresa incluyen más de 30 centros, que ofrecen a los clientes productos que van desde plumas de insulina hasta inhaladores y kits de diagnóstico. La empresa es fuerte porque cubre toda la gama de servicios, desde el diseño hasta la creación del envase final. Gracias a su avanzada infraestructura, pueden fabricar dispositivos médicos de gran tamaño que cumplen muchas normativas.
Industrias atendidas:
Productos farmacéuticos, atención sanitaria y diagnósticos.
¿Por qué elegir Gerresheimer?
- Soluciones de fabricación que incluyen un sistema completo.
- Existen instalaciones con certificación de sala blanca en distintos lugares del mundo.
- Nuevos avances tanto en envases como en dispositivos.
- Muchas organizaciones farmacéuticas líderes confían en nosotros.
- Cumplimiento de todas las normativas médicas de la UE y EE.UU.
5. Nypro Healthcare (Jabil - EE.UU.)
Nypro Healthcare forma parte de Jabil y ofrece soluciones de moldeo por inyección de plásticos médicos de gran volumen para mercados de alta complejidad y muy regulados. Gracias a sus capacidades de automatización y soporte de ingeniería, Nypro cuenta con instalaciones de fabricación en todo el mundo. Se concentran en aplicaciones médicas sofisticadas como la administración de fármacos inyectables, sistemas de diagnóstico y herramientas quirúrgicas mínimamente invasivas. Nypro trabaja con sus clientes en un modelo de asociación, asegurándose de proporcionar I+D, creación de prototipos y fabricación.
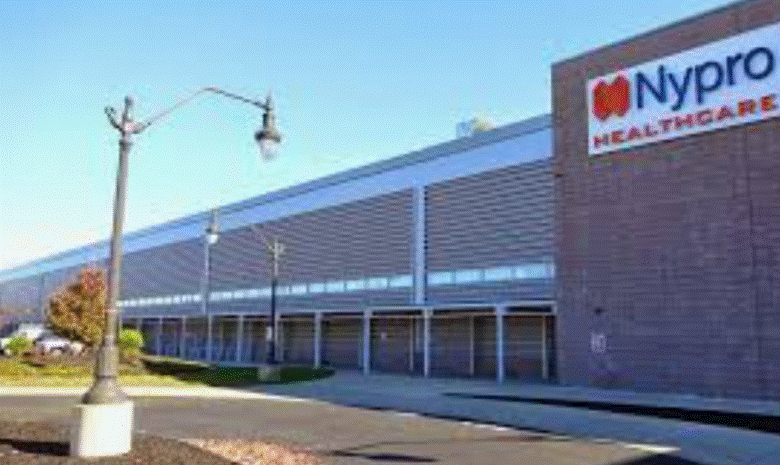
Perfil de la empresa:
Nypro, que pertenece a Jabil Healthcare, ofrece servicios completos de CDMO y moldeo por inyección para dispositivos médicos. En cinco regiones del mundo, Nypro produce grandes volúmenes para los campos de la cirugía, el diagnóstico y la administración de fármacos. Gracias a su destreza en automatización, cumplimiento de normativas y reducción de tamaño, los clientes pueden superar a la competencia. También trabajan en ingeniería desde el principio, eligen materiales importantes y construyen prototipos.
Industrias atendidas:
Sistemas de administración de fármacos, diagnóstico y cirugía.
¿Por qué elegir Nypro?
- Instalaciones de fabricación en varios países con capacidad para aumentar la producción.
- Tener un conocimiento detallado de las normas de los mercados regulados.
- La mejora de la automatización y el ensamblaje aporta ventajas a los fabricantes de automóviles.
- Trabajo en equipo temprano entre I+D y diseño temprano.
- Proveedor líder en la fabricación de productos sanitarios de alto riesgo.
6. Röchling Medical (Alemania)
Röchling Medical, que forma parte del Grupo Röchling, ofrece soluciones integrales de moldeo por inyección para clientes de los sectores farmacéutico, de diagnóstico y de dispositivos médicos. Está presente en Europa, EE.UU. y China. Las competencias de Röchling incluyen ingeniería y cumplimiento normativo, moldeo en sala blanca. Su cartera abarca desde componentes lab-on-chip hasta carcasas personalizadas para dispositivos quirúrgicos, a menudo producidos en entornos de clase 7 totalmente validados.
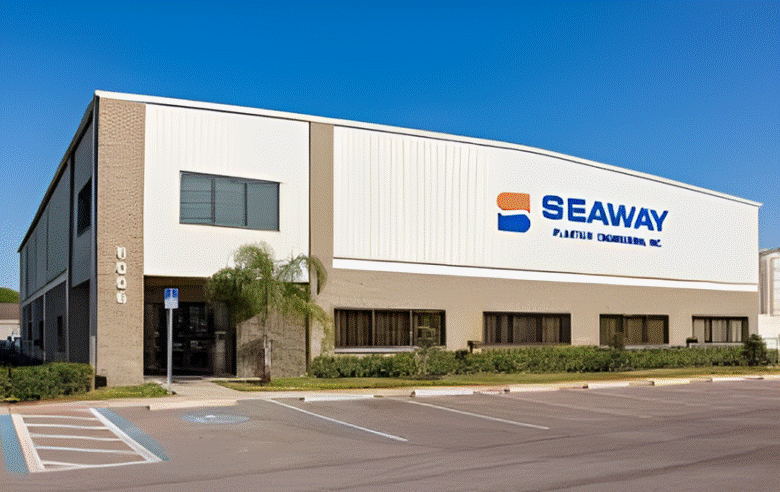
Perfil de la empresa:
Röchling Medical forma parte del Grupo Röchling y ayuda a las industrias farmacéutica, de diagnóstico y de tecnología médica de todo el mundo. Moldeo en sala blanca, lab-on-chip y carcasas de dispositivos son áreas en las que se especializan con fabricación en Alemania, EE.UU. y China. Röchling dispone de asistencia técnica, funciones reguladoras y soporte completo para la gestión de productos de principio a fin. Los sistemas de fabricación de estas instalaciones admiten tanto series limitadas como grandes producciones.
Industrias atendidas:
Diagnóstico, farmacia e instrumental quirúrgico.
¿Por qué elegir?
- Las empresas operan en varios países de Europa, China y Estados Unidos.
- Disponemos de amplios servicios de fabricación en sala blanca.
- Haber trabajado en entornos de moldeo de Clase 7 y Clase 8.
- Prestación de ayuda de ingeniería para las siguientes normativas.
- Disponemos de los conocimientos necesarios para desarrollar componentes a medida para uso médico.
7. Seaway Plastics Engineering (EE.UU.)
Seaway Plastics, especializada en la producción de volúmenes bajos y medios, es un socio creíble para los fabricantes de equipos originales médicos que requieren plazos de entrega rápidos y un apoyo flexible. Sus servicios son el moldeo por inyección en sala blanca, el utillaje interno y los servicios de montaje. Seaway tiene especial fama en el segmento de dispositivos ortopédicos y quirúrgicos. La empresa también proporciona protocolos de validación IQ/OQ/PQ, dejando claro que sus productos están muy regulados.
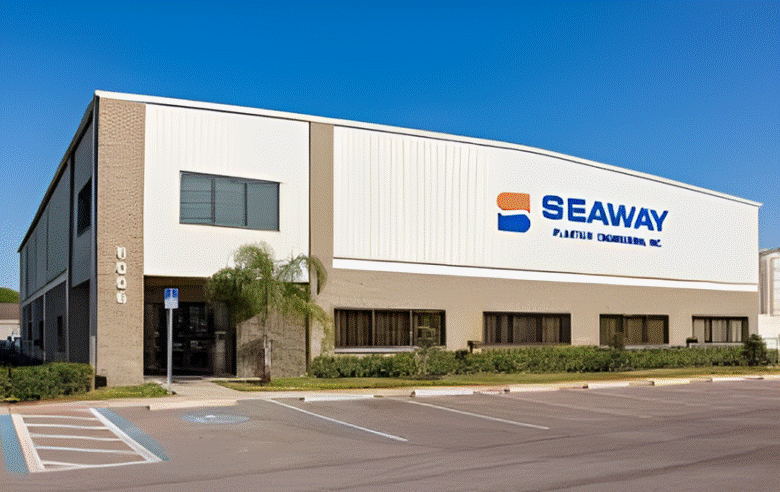
Perfil de la empresa:
Seaway Plastics ofrece principalmente moldeo por inyección de volumen bajo a medio a empresas de dispositivos médicos. Las instalaciones en salas blancas ISO Clase 7 permiten la fabricación de moldes, así como la validación y el montaje de productos finales. Seaway deja su impronta principalmente con instrumentación ortopédica y quirúrgica. Debido a sus rápidos plazos de producción, se acude a estas empresas tanto para muestras como para proyectos a pequeña escala.
Industrias atendidas:
Ortopedia, instrumental quirúrgico y diagnóstico.
¿Por qué elegir?
- Se ofrecen prototipos rápidos y un número reducido de muestras.
- Ofrecemos el desarrollo y soporte de nuestras propias herramientas de prueba y automatizadas.
- Puede confiar en que nuestras instalaciones cuentan con la certificación ISO 13485 y están reguladas por la FDA.
- El moldeo especial para componentes sensibles es posible en salas limpias.
- Ofrece total flexibilidad al cliente.
8. MedPlast (ahora Viant - EE.UU.)
Esta empresa se conoce ahora como Viant y es una potencia en la fabricación de dispositivos médicos. Realizan actividades de fabricación por contrato, como moldeo por inyección de plástico, extrusión, montaje, envasado y esterilización. Sus competencias en moldeo van más allá de los dispositivos implantables, los kits de diagnóstico y los sistemas de administración de fármacos. El énfasis de Viant en el diseño para la fabricabilidad (DFM) y el intenso control de calidad les convierte en un proveedor ideal para aplicaciones médicas de alto riesgo.
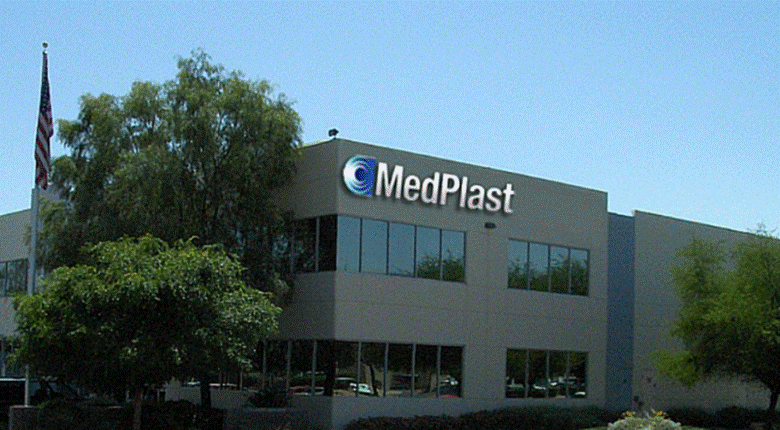
Perfil de la empresa:
La empresa opera bajo la marca Viant y ofrece diversos procesos de fabricación de dispositivos médicos, por ejemplo, moldeo por inyección y esterilización. Sus actividades se extienden a los mercados de ortopedia, diagnóstico y dispositivos de un solo uso. Gracias a las competencias de Viant en DFM y a sus recursos internos en materia de reglamentación, las soluciones se crean para que sean seguras y escalables. Vifor Pharma cuenta con más de 25 instalaciones repartidas por todo el mundo en las que aplica sus conocimientos en materia de reglamentación.
Industrias atendidas:
Dispositivos implantables, diagnósticos y sistemas quirúrgicos.
¿Por qué elegirlo?
- Ofrece servicios de diseño para fabricación, moldeo y esterilización.
- Experiencia demostrada en la atención de problemas médicos difíciles de tratar.
- Diseñado para el mundo, producido para el mundo.
- Puede modificar su pedido cuando lo necesite y se controla la calidad de todos los productos.
- Todas nuestras instalaciones cuentan con las certificaciones ISO 13485 y FDA.
9. Technoplast (Israel)
Technoplast es una empresa emergente en el sector del moldeo de plásticos médicos de precisión, con sede en Israel. Entre los productos que ofrece se encuentran el diseño de productos, la creación rápida de prototipos y la producción en serie, con especial atención a los componentes médicos personalizados. Entre sus clientes figuran fabricantes multinacionales de dispositivos médicos, y son conocidos por su rapidez de comercialización, ya que sus operaciones son muy ágiles y cuentan con un sólido departamento de I+D. Technoplast es excepcionalmente fuerte (cardiología, diagnóstico, dispositivos desechables).
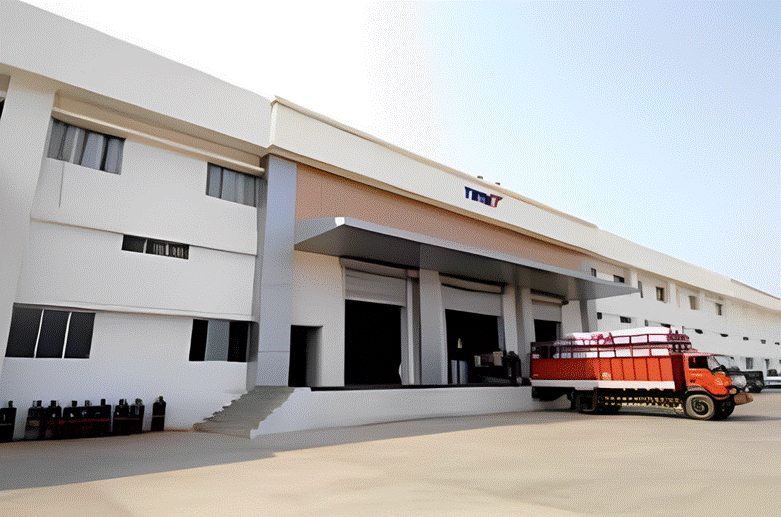
Perfil de la empresa:
Technoplast es una empresa israelí que suministra moldes de plástico avanzados para su uso en dispositivos médicos. La empresa ofrece ayuda para diseñar productos, crear prototipos, fabricar moldes y producir artículos a gran escala. Technoplast es reconocida por ser flexible, realizar una I+D eficaz y tener experiencia en la fabricación de productos para cardiología, diagnóstico y desechables de un solo uso. La rapidez de entrega y los bajos costes de fabricación son las principales prioridades de la empresa.
Industrias atendidas:
Cardiología, diagnóstico y dispositivos desechables.
¿Por qué elegir Technoplast?
- Mejora de los resultados mediante acciones ágiles y creación rápida de prototipos.
- Fabricación de moldes de alta precisión para piezas médicas detalladas.
- Hacer I+D innovadora para uso médico.
- Altas tasas de introducción de productos en el mercado.
- A la certificación ISO 13485 se suman productos conformes con las normas CE y FDA.
10. TK Mold (China)
TK Mold, la segunda y última empresa china de esta lista, es conocida por sus herramientas de alta precisión y sus servicios de moldeo por inyección. Se dedican a moldes y componentes de grado médico, y exportan productos a Norteamérica, Europa y otros mercados asiáticos. Sus puntos fuertes son el diseño de ingeniería y su capacidad para dar vida a estas ideas mediante la fabricación de moldes y la producción de volúmenes pequeños y medianos. TK Mold posee un documento ISO certificado y se adhiere a las normas médicas internacionales. Por lo tanto, es una buena empresa para subcontratar la producción.
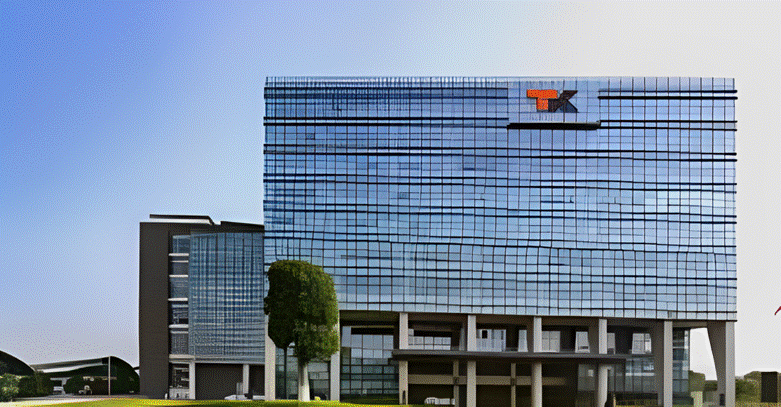
Perfil de la empresa
TK Mold es muy conocida en China por sus moldes de inyección y piezas de dispositivos médicos de alta calidad. Sus clientes de Norteamérica, Europa y Asia reciben moldes de sala blanca para aplicaciones de clase 7. TK Mold recibe asistencia durante todo el proceso, desde el diseño original hasta la fabricación de lotes medianos y los pasos posteriores a la producción. Gracias a que cuentan con la certificación ISO 13485 y cumplen las normas internacionales, se han ganado la confianza como socio en el extranjero.
Industrias atendidas
Medicina, electrónica y automoción.
¿Por qué elegir?
- Sólo se utiliza para la producción un pequeño número de moldes diseñados por profesionales.
- Prestar especial atención a la innovación en ingeniería.
- Con certificación ISO y según directrices médicas.
- Proporcionar conocimientos especializados a la UE, Estados Unidos y Asia.
- Métodos asequibles para trabajar con fabricantes de equipos originales.
Perspectivas de futuro para las empresas de moldeo por inyección de plásticos médicos.
Con el desarrollo de la industria sanitaria, se espera que las empresas de moldeo por inyección médica se desarrollen en varios aspectos esenciales. He aquí lo que nos depara el futuro:
1. Adopción de materiales inteligentes
- Las empresas están invirtiendo en materiales como polímeros antimicrobianos, biodegradables o biorreabsorbibles que proporcionan una funcionalidad mejorada.
- Estos suministros permiten utilizar productos sanitarios de un solo uso más seguros y sostenibles.
2. Expansión hacia la microfluídica y la miniaturización
- Cada vez más empresas de procesamiento se ven obligadas a crear piezas ultrapequeñas e intrincadas para lab-on-a-chip, sensores portátiles y dispositivos de diagnóstico.
- La capacidad de micromoldeo será necesaria para seguir siendo competitivos.
3. Automatización e integración de la Industria 4.0
- Sin embargo, la automatización avanzada y el análisis de datos en tiempo real permitirán a las empresas mejorar la eficacia de sus procesos, la trazabilidad y el control de calidad.
- Las fábricas inteligentes con sistemas conectados reducirán al mínimo los errores humanos y aumentará la productividad.
4. Personalización y fabricación bajo demanda
- La demanda de productos sanitarios personalizados es cada vez mayor, por lo que las empresas están adoptando un modo de producción flexible por lotes.
- La creación rápida de prototipos y la fabricación aditiva pueden mejorar los procesos de moldeo tradicionales.
5. Sostenibilidad y cumplimiento de la normativa medioambiental
- Los decretos mundiales obligan a las empresas a reciclar, reducir los residuos y el consumo de energía y disminuir el uso de plásticos no reciclables.
- Los fabricantes están adoptando las iniciativas y prácticas ecológicas de la economía circular.
6. Mayor control reglamentario
- Con la llegada de materiales y tecnologías nuevos e innovadores, las empresas pueden esperar protocolos de validación, trazabilidad y conformidad más rigurosos.
- Será necesario invertir en la pericia burocrática en aras de un acceso continuado al mercado.
7. Asociaciones estratégicas con empresas de tecnología médica
- Las empresas están estableciendo colaboraciones más estrechas con los fabricantes de equipos médicos para co-innovar las soluciones innovadoras sensibles a la propiedad intelectual.
- Se convertirá en una ventaja competitiva participar en las primeras fases del diseño.
Conclusión
Es importante seleccionar al mejor fabricante de moldeo por inyección de plásticos médicos para garantizar el éxito de su dispositivo médico en términos de seguridad, producción a escala y cumplimiento de todas las normativas. Esta lista es la élite mundial de las empresas, no sólo en términos de seguimiento de los requisitos técnicos y reglamentarios de la industria médica, sino que también aportan soluciones innovadoras y orientadas al cliente.
Desde los gigantes mundiales, como Phillips-Medisize y Gerresheimer, hasta las empresas especializadas, como Sincere Tech y Technoplast, todas y cada una de ellas cuentan con cierta experiencia y capacidades demostradas en el ámbito sanitario. Tanto si está desarrollando una nueva herramienta de diagnóstico como ampliando la producción de una pieza de maquinaria ya establecida, la colaboración con cualquiera de estos fiables proveedores de moldeo por inyección médica le sitúa a la vanguardia de las especificaciones de calidad y de la carrera competitiva.
Los proveedores de moldeo por inyección médica de renombre garantizan que se mantendrán a la cabeza en términos de referencias de calidad y juego competitivo en el mercado.
Preguntas frecuentes
1. ¿Qué es el moldeo por inyección de plásticos médicos?
Se trata de un proceso de fabricación que elabora piezas de plástico de alta precisión para el entorno de las aplicaciones médicas con equipos y materiales especiales dentro de unas estrictas normas reglamentarias.
2. ¿Por qué es importante la certificación ISO 13485 para las empresas de moldes médicos?
Garantiza que la empresa cumple las normas internacionalmente aceptadas de los sistemas de gestión de calidad de la industria de productos sanitarios, que es la clave para el cumplimiento de la normativa y la seguridad de los productos.
3. ¿Qué materiales se suelen emplear en el moldeo por inyección para uso médico?
Los materiales comunes incluyen policarbonato de grado médico, polipropileno, polietileno y elastómeros termoplásticos deben ser materiales biocompatibles y esterilizables.
4. ¿Cuál es el efecto de las salas blancas en el moldeo por inyección médica?
Las salas blancas son un entorno libre de contaminación, vital en la producción de componentes médicos estériles/sensibles al minimizar las posibilidades de contaminación por partículas.
5. ¿Pueden las pequeñas empresas igualar la producción de los grandes fabricantes?
Sí. Numerosas pequeñas empresas ofrecen servicios especializados, de desarrollo ágil y de creación rápida de prototipos que, de hecho, son buenos socios para trabajos especializados o personalizados.