Sprøytestøping av klar plast er en spesialisert produksjonsprosess som også brukes til produksjon av klare plastkomponenter av høy kvalitet for flere bransjer. Denne teknikken skiller seg fra standard plaststøping ved at materialer, formdesign og alle variabler må kontrolleres nøyaktig for at denne teknikken skal gi eksepsjonell optisk klarhet og holdbarhet. Klare plastdeler dukker opp i medisinske instrumenter og billinser, forbrukerelektronikk og arkitektonisk belysning overalt, og alle andre steder også. Sprøytestøping av klar plast er avhengig av valg av riktig materiale som akryl, polykarbonat og optisk silikongummi med sine spesifikke egenskaper som slagfasthet, UV-stabilitet og lysoverføring.
Selve prosessen krever delikat klargjøring av støpeformen, tørking av materialet, kontrollert innsprøyting og langsom avkjøling for å unngå defekter som bobler, striper og dis. Etterbehandlingsteknikker og avanserte belegg forbedrer dessuten den optiske ytelsen til de optisk klare plastkomponentene ytterligere. Til tross for alle disse fordelene står støping av klar plast overfor utfordringer som perfekt gjennomsiktighet, unngåelse av overflatedefekter og materialfølsomhet. Likevel øker fremgangen innen støping, og aktørene i bransjen drar nytte av innovasjoner som AI-drevet optimalisering av støping, 3D-printing av tilpassede støpeformer og selvhelbredende plast for å forbedre effektiviteten og produktene som produseres.
I denne artikkelen beskrives prosessen med sprøytestøping av klar plast, de viktigste materialene som brukes, utfordringer, bruksområder og fremtidige fremskritt. Hvis du jobber i medisin-, bil-, elektronikk- eller belysningsbransjen og trenger å vite hvordan man lager verktøy i gjennomsiktig plast, kan denne kunnskapen hjelpe deg med å velge en plastkomponent med høy ytelse og visuelt tiltalende utseende.
Hva er sprøytestøping av klar plast?

Sprøytestøping av klar plast er en type produksjon der gjennomsiktig eller halvgjennomsiktig plastmateriale smeltes og sprøytes inn i en form for å skape bestemte former. I motsetning til vanlig sprøytestøping er denne prosessen svært følsom for materialvalg (inkludert valg av flytetyper), formdesign og kjøleteknikker for å unngå defekter som uklarhet, bobler og forvrengninger.
Det er mye brukt til produksjon av produkter som skal ha utmerkede optiske egenskaper, for eksempel medisinske instrumenter, bilbelysning og elektroniske skjermer.
Sprøytestøpingsprosess for klar plast

Det er en svært presis prosess for å oppnå klare plastkomponenter. Her er en oversikt over noen av de viktigste trinnene i dette nettkurset.
1. Utforming og klargjøring av støpeformen
Sprøytestøping av klar plast krever en form som er godt designet. Formen må ha:
- Polert til svært høye nivåer for å forhindre merker eller forvrengninger av lyden.
- Den kan ventileres for å fjerne luftbobler og unngå innestengte gasser.
- Mekanismer for å kontrollere temperaturen for å regulere kjølehastigheten
2. Tørking av materiale
Plastharpikser med for høyt fuktighetsinnhold er kjent for å forårsake uklarheter, bobler eller svake punkter. Polykarbonat- og akrylmaterialer må tørkes ved kontrollerte temperaturer før injeksjon for å fjerne fuktighet.
3. Smelting og injeksjon
Formhulen fylles under høyt trykk med den tørkede harpiksen som varmes opp til smeltepunktet. Viktige hensyn inkluderer:
- Forhindrer strømningsmerker og spenningsbrudd ved hjelp av injeksjonshastighet og -trykk
- Høyere temperatur bidrar til å opprettholde optisk klarhet
- Jevn avkjøling og forhindrer krymping: Jevn fylling
4. Avkjøling og størkning
Nedkjølingen må være langsom og jevn for å unngå at materialet vrir seg eller forvrenges. Gjennomsiktig plast krever ofte:
- Gradvis avkjøling for å opprettholde klarheten
- Avanserte kjølekanaler i støpeformen kan brukes.
- I noen tilfeller kan ettergløding redusere indre spenninger.
5. Utstøting og etterbehandling
Delen skyves forsiktig ut når den har størknet for å unngå riper eller merker. Etterbehandlingsteknikker som f.eks:
Polering
- UV-belegg for beskyttelse
- Laserskjæring for presisjon
- Dette kan også forbedre produktets utseende og holdbarhet.
Klar sprøytestøping Bruker nøkkelmaterialer.
Klar sprøytestøpt plast krever valg av materiale, noe som er viktig for å gi høy styrke og høy klarhet. De mest brukte materialene er gitt nedenfor:
Akryl (PMMA)

Polymetylmetakrylat (PMMA), eller akryl som det også kalles på fagspråket, er et av de mest brukte materialene for sprøytestøping av klar plast på grunn av sin utmerkede optiske klarhet. Med en lysgjennomgang på ca. 92% er det designet for bruksområder som krever høy gjennomsiktighet, for eksempel belysningsarmaturer, utstillingsvinduer og bilkomponenter.
I tillegg til overlegen UV-bestandighet, som gjør at det ikke gulner over tid, og høy ripebestandighet, er akryl også giftfritt i en rekke bruksområder. Akryl er imidlertid svært sprøtt og har en tendens til å sprekke eller slå sprekker ved støt. Dessuten er det svært følsomt for fuktighet og krever fortørking for å kunne brukes i støping uten defekter.
Polyetylen med høy tetthet (HDPE)

Polyetylen med høy tetthet, eller HDPE, er et relativt billig og allsidig materiale med en gjennomskinnelig klarhet som gjør det egnet for produkter som ikke krever full gjennomsiktighet. På grunn av sin UV-bestandighet er det et godt valg for utendørs bruk, siden det tåler lang soleksponering uten å forringes.
HDPE har større slagfasthet sammenlignet med akryl, så det er mindre sannsynlig at det går i stykker. Den brukes mest til produksjon av flasker, rør og emballasjebeholdere på grunn av de lave produksjonskostnadene og den fantastiske holdbarheten. På den annen side er HDPE ikke stiv nok som annen gjennomsiktig plast, noe som gjør den uegnet til bruksområder som krever høy strukturell styrke.
Polykarbonat (PC)

Polykarbonat (PC) er en gjennomsiktig plast med høy ytelse, god optikk og svært høy mekanisk styrke. Det er mye brukt i applikasjoner som krever gjennomsiktighet og holdbarhet, f.eks. sikkerhetsbriller, billykter og skuddsikre vinduer.
I motsetning til akryl, er polykarbonat ekstremt slagfast og vil ikke knuses under alvorlige krefter. Dessuten er dette en god UV-bestandig, tilstanden vil ikke gulne i lang tid. En ulempe er imidlertid at overflaten av polykarbonat er utsatt for overflateriper og vanligvis trenger et nytt strøk med noe for å gjøre den holdbar. PC krever også forhåndsdoping før sprøytestøping for å forhindre fuktrelaterte defekter (som akryl).
Polyeterimid (PEI)

Polyeterimid (PEI) er en høytytende teknisk plast som motstår UV-stråling, varme og kjemikalier. Legeringen brukes først og fremst i bransjer som krever høy mekanisk styrke og høy termisk stabilitet, for eksempel innen romfart, bilindustri og produksjon av medisinsk utstyr.
PEI har derfor utmerket varmebestandighet for alt som skal utsettes for ekstreme temperaturer. Selv om det er dyrere og vanskeligere å støpe på overflaten av et produkt, brukes det av og til i forbrukerprodukter. I mange tilfeller krever PEI-sprøytestøping bruk av stålformer for å kunne være presis og opprettholde holdbarheten.
Polypropylen (PP)

Polypropylen (PP) er en mye brukt termoplast som er fleksibel, kjemisk motstandsdyktig og elektrisk ledende. På grunn av sin holdbarhet og allsidighet brukes det mye i emballasjematerialer, tekstiler og bilkomponenter.
PPs største fordel er at det kan lukkes og åpnes flere ganger uten å gå i stykker. Det er derfor spesielt godt egnet til bruksområder som flaskelokk og levende hengsler. Polypropylen er likevel ikke like gjennomsiktig som akryl eller polykarbonat - det egner seg bedre som gjennomskinnelig enn klart. I tillegg er det ikke stivt nok til å brukes som en strukturell eller bærende komponent.
Flytende silikongummi (LSR)

Flytende silikongummi (LSR) er en elastomer med høy ytelse som er kjent for å være ekstremt biokompatibel, ha utmerket termisk stabilitet og kjemisk resistens. Mekanisk sett er det ganske sterkt og fleksibelt, og det brukes mye i medisinske, biltekniske og elektroniske applikasjoner.
Den enestående fordelen med LSR er at det opprettholder sin form og sine egenskaper under ekstreme termiske forhold, eller når det utsettes for kjemikalier, løsemidler eller varme. LSR har en elastisitet og holdbarhet som gjør det egnet til tetninger, pakninger og medisinske slanger. Takket være sin motstand mot varme og kjemikalier kan LSR også brukes i krevende miljøer.
Optisk silikongummi (OSLR)

Denne optiske silikongummien (OSLR) er spesielt utviklet for høy lysgjennomgang og høy optisk klarhet. I optiske linser, LED-belysning, medisinsk avbildningsutstyr og andre felt der det er nødvendig med høy lystransmisjon og ekstremt lav forvrengning, for eksempel i en CCTV.
OSLR har enestående motstandskraft mot ugunstige værforhold og gulner ikke i løpet av den forventede levetiden. Det er et godt valg for utendørs belysningsarmaturer og optiske komponenter med høy presisjon på grunn av sin evne til å holde den optiske stabiliteten over tid.
Polyetylen (PE)

Polyetylen (PE) er en termoplast som fremstilles av petroleumsbaserte materialer gjennom varme- og trykkbehandling. På grunn av sin kostnadseffektivitet og formbarhet brukes det ofte i flasker, rør, emballasje og forbruksvarer.
Det er UV-bestandig og egner seg derfor godt til utendørs bruk. Selv om det ikke kommer i nærheten av den optiske klarheten til akryl eller polykarbonat, er det bedre for gjennomskinnelige applikasjoner enn helt gjennomsiktige.
Elastomere harpikser (TPR)

Termoplastisk gummi (TPR) er et fleksibelt materiale som inneholder egenskapene til plast og gummi. Det brukes ofte i medisinske, industrielle og forbrukerrelaterte bruksområder som krever kjemikalieresistens og elastisitet.
TPR brukes i vanlige bruksområder som væskedispensere, medisinske katetre og fleksible slanger. Det er et ideelt materiale for produkter som krever motstand mot syrer og sterke kjemikalier, fordi det tåler tøffe forhold.
Termoplastisk polyuretan (TPU)

Termoplastisk polyuretan (TPU) er en elastomer med høy styrke som ofte brukes i sportsutstyr, bildeler og ergonomiske håndtak. Materialet er kjent for sin myke tekstur, overlegne elastisitet og utmerkede rivestyrke.
TPU gir en gummifølelse og brukes derfor mye i håndtak og fleksible deler. Selv om denne plasttypen er dyrere enn standardplast, er den slitesterk og støtsikker, noe som gjør den til et godt valg for bruksområder med høy ytelse.
Lysgjennomgang og dens egenskaper og beste bruk
Denne tabellen hjelper deg med å sammenligne hvordan ulike gjennomsiktige og gjennomskinnelige materialer fungerer når det gjelder lysgjennomtrengelighet, egenskaper og beste bruksområde.
Materiale | Lysoverføring (%) | Viktige funksjoner | Vanlige bruksområder |
Akryl (PMMA) | ~92% | Det er en klar, UV-bestandig og ripebestandig sprø | Belysningsarmaturer, skjermer, optiske linser |
Polykarbonat (PC) | 88-90% | Høy slagfasthet, UV-bestandighet, noe lavere klarhet enn PMMA | Vernebriller, billykter, skuddsikre vinduer |
Optisk silikongummi (OSLR) | ~90-94% | Glasslignende klarhet, fleksibel, motstandsdyktig mot høye temperaturer | LED-belysning, optiske linser, medisinsk avbildningsutstyr |
Flytende silikongummi (LSR) | ~85-90% | Fleksibel, biokompatibel, varme- og kjemikaliebestandig | Medisinsk utstyr, elektronikk, spesialbelysning |
Polypropylen (PP) | ~80-85% | Gjennomsiktig, kjemikaliebestandig, fleksibel, lav pris | Frostede lokk, beholdere og emballasjeløsninger |
Polyetylen med høy tetthet (HDPE) | ~75-85% | Gjennomsiktig, slitesterk, kostnadseffektiv, støtsikker | Flasker, rør, emballasje, forbruksvarer |
Utfordringer i klar sprøytestøping

Selv om gjennomsiktig plast har flere fordeler, har den også sine ulemper:
1. Oppnå høy optisk klarhet
Gjennomsiktigheten kan reduseres på grunn av ujevnheter i formen eller avkjølingen. Formen må være glatt og blankpolert, og behandlingen må utføres ved nøyaktige temperaturer.
2. Unngå bobler og strømningslinjer
Bobler eller luftstrømmer som har blitt fanget under injeksjonsprosessen, kan bli synlige i sluttproduktet. For å forhindre dette:
Det er nødvendig med riktig utlufting i formen. Det bidrar til å opprettholde jevn flyt ved hjelp av sakte, kontrollerte injeksjonshastigheter.
3. Materialfølsomhet
Polykarbonat og akryl er klare plastmaterialer som er svært følsomme for fuktighet, varme og UV-eksponering. Hvis tørking og lagring gjøres på riktig måte, blir resultatet av høy kvalitet.
4. Riper og overflatedefekter
Det er fordi ujevnheter vises tydelig i gjennomsiktig plast, så produsentene må bruke:
- Antiripe-belegg
- Beskyttende emballasje under transport
Vanlige defekter i gjennomsiktige plastdeler og løsninger på dem
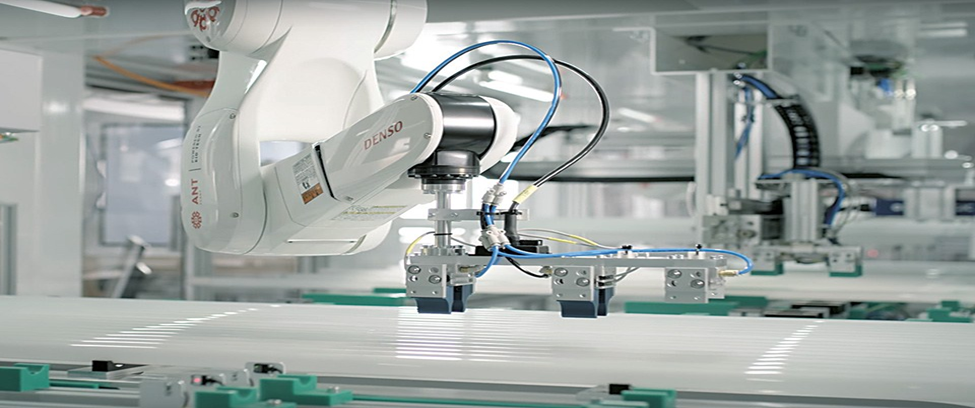
Ved produksjon av klare plastdeler kreves det perfekt gjennomsiktighet og glatthet. Det finnes imidlertid mange feil som kan påvirke sluttproduktets klarhet og generelle kvalitet. Her er noen vanlige problemer ved sprøytestøping av klar plast, og hvordan du kan løse dem.
1. Bobler
Årsak
Årsaken til bobler er vanligvis innestengt luft eller gass som ikke kan slippe ut under støpeprosessen. Dette kan skje på grunn av:
- Ufullstendig fylling av formen.
- Rask avkjøling ved kondensasjonsoverflaten.
- Harpiks med fuktighet som forårsaker dampdannelse.
Løsning
- Sørg for at formen er ordentlig ventilert slik at gasser slipper ut.
- Øk injeksjonstrykket for å forbedre materialflyten.
- Overflødig fuktighet bør fjernes fra plastharpiksen før støping.
2. Silver Streaks
Årsak
Variasjoner i indre spenninger under materialflyten forårsaker sølvstriper. Ved å legge press på harpiksen, skyves harpiksen i ulike retninger, noe som skaper en rekke ujevn brytningsindeks og resulterer i en stripete eller silkelignende effekt. Hvis dette stresset får lov til å bygge seg opp, vil det til slutt føre til sprekkdannelser.
Løsning
- For å fremme jevn avkjøling bør temperaturen i formen optimaliseres.
- Øk injeksjonshastigheten og trykket for å minimere spenningsoppbygging.
- Unngå retningsbestemt materialjustering under støping med støpeteknikker med lav belastning.
3. Seismiske mønstre
Årsak
Denne feilen kjennetegnes av rillede eller bølgete mønstre på overflaten som skyldes høy smelteviskositet. Hvis harpiksen ikke flyter jevnt og kondenserer for tidlig i hulrommet, ødelegger det materialets homogenitet.
Løsning
- Øk smeltetemperaturen for å øke materialflyten.
- Viskositeten reduseres ved å justere plastiseringsforholdene.
- Endre utformingen av granen og løperen for å få bedre materialfordeling.
4. Dårlig overflateglans
Årsak
Årsaken til en matt eller ujevn overflatefinish er vanligvis ru formoverflater, eller at harpiksen stivner for tidlig før den er helt tilpasset formen.
Løsning
- For å oppnå en jevnere finish kan du polere formhulen.
- Øk temperaturen i formen for å forbedre materialflyten.
- Det bør brukes harpiks av høy kvalitet med bedre flyteegenskaper.
5. Hvit røyk / svarte flekker
Årsak
Harpiksnedbrytningen inne i sprøytestøpefatet på grunn av overdreven varme er årsaken til at disse feilene oppstår. Svarte flekker kan oppstå når overopphetet materiale kan brenne, og hvit røyk kan oppstå når gass slippes ut fra degradert harpiks.
Løsning
- Forhindre overoppheting av fatet ved å senke temperaturen.
- Finpussere skal rengjøre og vedlikeholde injeksjonsmaskinen regelmessig for å unngå opphopning av harpiks.
- Garanterer konsistente syklustider slik at materialet ikke brytes ned.
6. Whitening / Haze
Årsak
Når fuktighet eller støvpartikler forurenser plastmaterialet, oppstår det dis eller uklarhet. Lysdiffraksjon på grunn av feil tørking eller luftbårne urenheter vil redusere gjennomsiktigheten.
Løsning
- Bearbeid råmaterialer etter grundig tørking.
- Kontaminering kan unngås ved å oppbevare lagret materiale i et rent og kontrollert miljø.
- Hold støvet borte fra luften ved hjelp av filtre og luftrensere i produksjonsområdet.
Fordeler med sprøytestøping av klar plast
Det er imidlertid mange fordeler med sprøytestøping av klar plast til tross for ulempene.
1. Utmerket optisk gjennomsiktighet
Høy lystransmisjon egner seg godt til klar sprøytestøpt plast som brukes i for eksempel linser, medisinsk utstyr og skjermer.
2. Presisjon og konsistens
Sprøytestøping er svært nøyaktig og repeterbar, noe som resulterer i identiske deler med svært få feil i hver.
3. Kostnadseffektiv masseproduksjon
Når formen først er laget, synker produksjonskostnadene betydelig sammenlignet med de påfølgende, og er dermed en effektiv måte når det gjelder produksjon i bulk.
4. Lett og slitesterk
Fordi klare plastdeler er lettere enn de fleste glassdeler, splintresikre og mer slagfaste, egner de seg utmerket til bruk i sikkerhetsapplikasjoner.
Bruksområder for klar sprøytestøpt plast
Plast med klare sprøytestøpeformer brukes ofte i industrien fordi de har optisk klarhet, holdbarhet, kjemisk motstand og lavere vekt. Plast som kan skape gjennomsiktige komponenter med høy presisjon som øker funksjonaliteten og estetikken, er disse. Noen av de viktigste bransjene som klar plastsprøytestøping gjelder, er angitt nedenfor.
1. Medisinsk industri

Det medisinske markedet krever klare plastkomponenter der sterilitet og presisjon er avgjørende, i tillegg til behovet for synlighet. Vanlige bruksområder inkluderer:
- Omfatter gjennomsiktige sprøyter og IV-slanger, eller kirurgiske instrumenter som gjør det mulig for personalet å overvåke eller kontrollere væskestrømmen og forhindre overdosering.
- Stivhet av klart beskyttelsesskjold over ansiktsmasken eller de medisinske vernebrillene for å beskytte uten å gå på bekostning av utsikten.
- Hus til diagnostisk utstyr for røntgen-, MR- og ultralydskannere der klarhet er så viktig.
2. Bilindustrien

Sprøytestøpt plast kan gjøre kjøretøy mer funksjonelle og designvennlige. De brukes i:
- Linser med høy optisk gjennomsiktighet og holdbarhet for front- og baklykter som tåler tøffe værforhold.
- Gjennomsiktige toppdeksler på dashbordet og speedometerpaneler for å gjøre kontroller og displayer synlige.
- I enkelte lettvektsbiler som krever soltak og sidevinduer, brukes det slagfast, gjennomsiktig plast.
3. Forbrukerelektronikk

Klart støpt plast brukes i elektronikkindustrien til produksjon av lette, holdbare og estetisk tiltalende deler.
- For beskyttende og kostnadssensitive berøringsapplikasjoner på smarttelefonskjermer og skjermdeksler.
- Inkluderer også gjennomsiktige TV- og laptop-skjermer med ripebestandighet og høy klarhet.
- Skjermkomponenter i bærbar teknologi som smartklokker og treningsarmbånd er også fleksible og slagfaste.
4. Emballasjeindustrien

Klar plast brukes ofte i emballasje fordi den er vaskbar, lett og estetisk tiltalende. Noen viktige bruksområder inkluderer:
- Et utvalg av gjennomsiktige beholdere og flasker i matvarekvalitet som holder maten frisk og gjør det lettere å se innholdet.
- Typen gjennomsiktig kosmetisk og farmasøytisk emballasje, slik at kundene kan se produktet trygt mens de oppbevarer det.
- Manipulasjonssikker og lufttett gjennomsiktig emballasje, som brukes til medisiner, kosttilskudd eller mer eksklusive matprodukter.
5. Belysningsbransjen
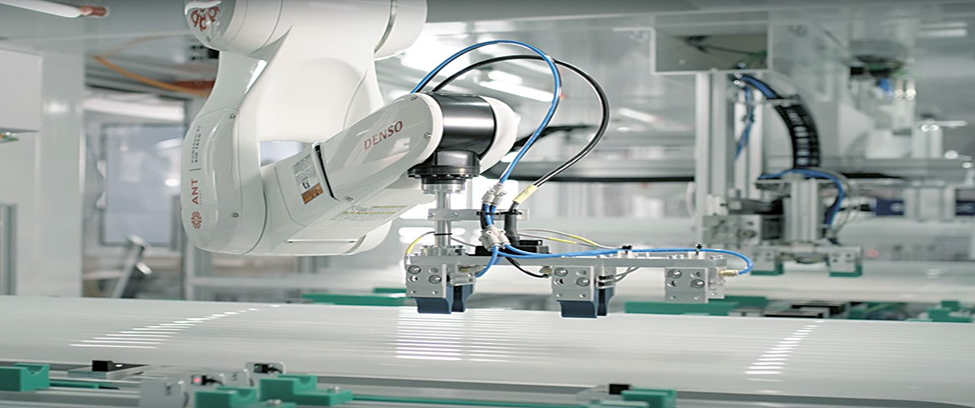
Plast som oftest brukes som elektrisk isolerende materiale, såkalt klar plast eller plast, er avgjørende for moderne belysningsapplikasjoner, noe som gir økt effektivitet og funksjonalitet. De brukes i:
- LED-deksler og lampediffusorer for jevn lysfordeling, i tillegg til å beskytte LED-komponenter.
- Transparente paneler for arkitektonisk belysning, for eksempel transparente paneler, kan brukes som skreddersydde belysningsløsninger for interiør- og eksteriørdesign.
- Optiske linser med høy ytelse brukes i gatelys, stadionbelysning og billykter for å gi fleksibilitet i lysretning og fokus.
6. Luft- og romfart og forsvar
I tillegg kreves det lette, slagfaste, klare materialer til mange bruksområder i luftfarts- og forsvarsindustrien, som f.eks:
- Høy optisk klarhet med motstand mot trykkforandringer som kreves for flyvinduer og cockpitpaneler.
- Transparente visirer til hjelmer, som beskytter så mye som øynene kan se.
- Optiske linser til forsvarsutstyr, for eksempel nattsynsbriller og avstandsmålere.
7. Optisk og vitenskapelig utstyr
Klar plast er nødvendig for optiske bruksområder med høy presisjon for nøyaktig lysoverføring uten forvrengning. Eksempler inkluderer:
- Linsene deres har blitt brukt i mikroskoper og teleskoper, noe som har gitt opphav til høy klarsynsforstørrelse.
- Optiske sensorer og laserkomponenter brukes i vitenskapelig forskning innen industriell automatisering.
- Forebyggende skjermer for laboratorieinstrumenter for å sikre håndtering av farlige materialer.
På grunn av sin allsidighet og sine avanserte egenskaper er klar sprøytestøpt plast uerstattelig for mange bransjer, for eksempel innen medisin, bilindustri, elektronikk, emballasje, belysning, romfart og vitenskap, der innovasjon fremmes av at denne plasten er tilgjengelig.
Fremtidige trender innen sprøytestøping av klar plast
Sprøytestøpeindustrien for klar plast vil oppleve store fremskritt i takt med den teknologiske utviklingen. I løpet av de kommende årene vil det være nødvendig å forbedre materialenes holdbarhet, deres bærekraft og produksjon samt produktets ytelse. Bransjen vil bli definert av noen få nøkkeltrender som er listet opp nedenfor.
1. Forbedrede materialinnovasjoner
Utviklingen av gjennomsiktig plast går raskt fremover for å utvikle mer holdbar, bærekraftig og funksjonell plast. Viktige innovasjoner inkluderer:
- Automatiske reparasjoner av mindre riper i selvhelbredende, gjennomsiktig plast forlenger levetiden til produkter som billinser og smarttelefonskjermer.
- Høyfaste, lette kompositter som er svært gjennomsiktige og har en kombinasjon av god slagfasthet og gjør det mulig å motstå støt når termoplastiske materialer er umulige eller vanskelige å bruke.
2. Avanserte støpeteknologier
Sprøytestøping av klar plast gjennomgår ulike nye produksjonsteknikker som muliggjør større effektivitet og presisjon:
- Integrasjon med 3D-printing for å tilpasse formen for rask prototyping og billig masseproduksjon av komplekse deler som den gjennomsiktige.
- Sanntidsoptimalisering av støping med kunstig intelligens, som kan tilpasse seg dynamisk for å forårsake færre feil, produsere mer konsistente produkter og kortere syklustid.
- Brukt til nanoteknologiforbedret sprøytestøping for å skape plast som var bedre i stand til å påvirke optisk klarhet, ripebestandighet og varmetoleranse.
3. UV-bestandig og antidugg-belegg
For å produsere fremtidens klare plast med bedre funksjonalitet i ulike bruksområder, vil plasten bli utstyrt med spesialbelegg.
- Forbedret UV-beskyttelse, slik at den ikke gulner eller ødelegger materialer som utsettes for sollys, som billykter eller paneler for utendørsbelysning.
- Gir antidugg-egenskaper som forbedrer sikten på bilruter, medisinske apparater og optiske enheter.
- Ripebestandige belegg for å øke holdbarheten til smarttelefonskjermer, briller, industrielt verneutstyr osv.
4. Smart og funksjonell gjennomsiktig plast
Etter hvert som gjennomsiktig plast blir mer etterspurt som multifunksjonelt materiale, vil smarte teknologier som mesh bli integrert i det.
- Også innebygde sensorer i gjennomsiktig plast for industrielle og medisinske bruksområder for overvåking av temperatur, trykk og kjemisk eksponering i sanntid.
- Skjæringer som gjør det mulig å forme ledende, klar plast til gjennomsiktige elektroniske skjermer og berøringsfølsomme overflater i neste generasjons enheter.
- Og selvrensende belegg som krever mindre vedlikehold i medisinske, optiske og biltekniske produkter.
Hvis disse fremskrittene blir oppfylt, vil vi garantert få klarere plastsprøytestøping som garantert vil oppfylle de økende kravene fra dagens industrier på en enda smartere og mer bærekraftig måte, blant andre funksjoner.
Konklusjon
Sprøytestøping av klar plast er en viktig funksjon som har forandret produksjonsindustrier som krever høy gjennomsiktighet og nøyaktighet. Avanserte materialer som polykarbonat, akryl og optisk silikongummi gjør det mulig for produsenten å designe komponenter som er lette, holdbare og optisk klare, samtidig som de erstatter de eldre glassløsningene. Alt dette har ført til en økende etterspørsel etter gjennomsiktig plast på grunn av bruken i medisinsk utstyr, bilbelysning, elektronikk og emballasje. Til tross for problemer som fuktfølsomhet, defekter på overflaten av objektet og strenge prosesseringskrav, har støpeteknologien gjort store fremskritt når det gjelder å øke effektiviteten og forbedre produktkvaliteten. AI, 3D-printing og nanoteknologi fortsetter å utvikle teknologien, slik at prosessen blir billigere og mer presis, og UV-bestandige belegg og selvhelbredende plast har økt holdbarheten til de klarstøpte produktene ytterligere.
Fremtiden for sprøytestøping av gjennomsiktig plast er rettet mot bærekraft, smarte materialer og økt funksjonalitet. Biologisk nedbrytbar og resirkulerbar gjennomsiktig plast vil i økende grad bli etterspurt av bransjer som er på jakt etter miljøvennlige alternativer til sine vanlige produkter. Dessuten kan smarte plastmaterialer med innebygde sensorer og ledende egenskaper få anvendelse innen medisin og elektronikk. Alt i alt er sprøytestøping av gjennomsiktig plast fortsatt en svært viktig teknologi som stadig utvikles og gir kreative løsninger til bransjer som krever gjennomsiktighet, styrke og estetisk appell.
Vanlige spørsmål
1. Hva er de mest brukte materialene i sprøytestøping av klar plast?
PMMA er et materiale med høy optisk klarhet og brukes oftest, PC for høy slagfasthet, OSLR for høyest mulig lystransmisjon og PP for gjennomskinnelige og rimeligere bruksområder. Valget av materiale gjøres ut fra materialets egenskaper og det industrielle behovet.
2. Hva er de største vanskelighetene med sprøytestøping av klar plast?
Hovedutfordringene er å sørge for at materialet har høy optisk klarhet, ingen defekter som bobler eller striper, at det er fuktfølsomt og at det har ripebestandige overflater. For å overvinne disse utfordringene kreves det presise støpeforhold, god tørking og svært gode støpeformer.
3. Hvilke bransjer bruker sprøytestøping av klar plast mest?
Sprøytestøping av klar plast er en av de viktigste delene i produksjonsindustrien, for eksempel i medisinske applikasjoner (sprøyter, IV-slanger, diagnostisk utstyr) og bilindustrien (frontlyktglass, dashborddeksler), forbrukerelektronikk (smarttelefonskjermer, displaypaneler), emballasje (matvarebeholdere, kosmetikkflasker) og belysning (LED-deksler, lampediffusorer).
4. Hvilken rolle spiller teknologien i sprøytestøping av klar plast?
AI-styrking av prosesser, 3D-printing for tilpasning av støpeformer, selvhelbredende plast og forbedrede UV-bestandige belegg gjør produksjonen mer effektiv og produktene mer holdbare. Disse reduksjonene muliggjør mer pålitelige prosesser, bedre materialytelse og mer bærekraftige prosesser.
5. Er gjennomsiktige plastmaterialer naturvennlige?
Tradisjonell gjennomsiktig plast fra petroleum ser ut til å ha blitt bedre når det gjelder bærekraft, selv om biologisk nedbrytbar og resirkulert gjennomsiktig plast har utviklet seg de siste årene. Produsentene utforsker også biobaserte alternativer og miljøvennlige produksjonsteknikker for å redusere miljøpåvirkningen.